Benefits of Using Polymer Blends in Injection Molding
Polymer blends are becoming increasingly popular in the injection molding world due to their many benefits. In this article, we will explore the advantages of using polymer blends in injection molding and how they can enhance the manufacturing process.
1.Improved Mechanical Properties
One of the main advantages of using polymer blends in injection molding is their ability to improve the final mechanical properties. By combining different polymers, manufacturers can also create blends with desired properties, such as higher strength, flexibility, or impact resistance. This versatility makes it possible to produce a variety of products that meet specific requirements.
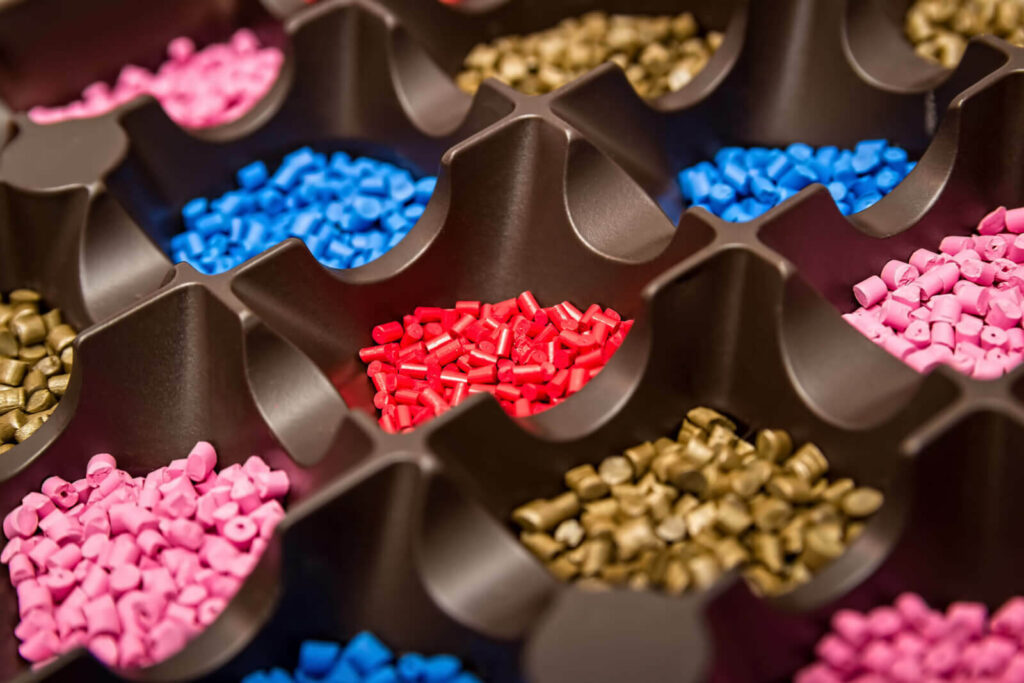
2.Cost Effectiveness
Blending different polymers can often result in a cheaper material than using a single polymer. This is particularly beneficial for large-scale production, as significant cost savings can be achieved. Additionally, polymer blends can also reduce the need for additives or fillers, further reducing costs.
3.Improved Processability
The blending of polymers can enhance the flow of the material, making it easier to mold and reducing the likelihood of defects. This improvement in processing properties can increase production efficiency and reduce cycle times, ultimately increasing productivity.
4.Enhanced Aesthetics
In addition, polymer blends can enhance the aesthetics of the final product. By combining different polymers, manufacturers can create blends with unique colors, textures, or finishes. This allows for increased design flexibility and the ability to create visually appealing products that stand out in the market.
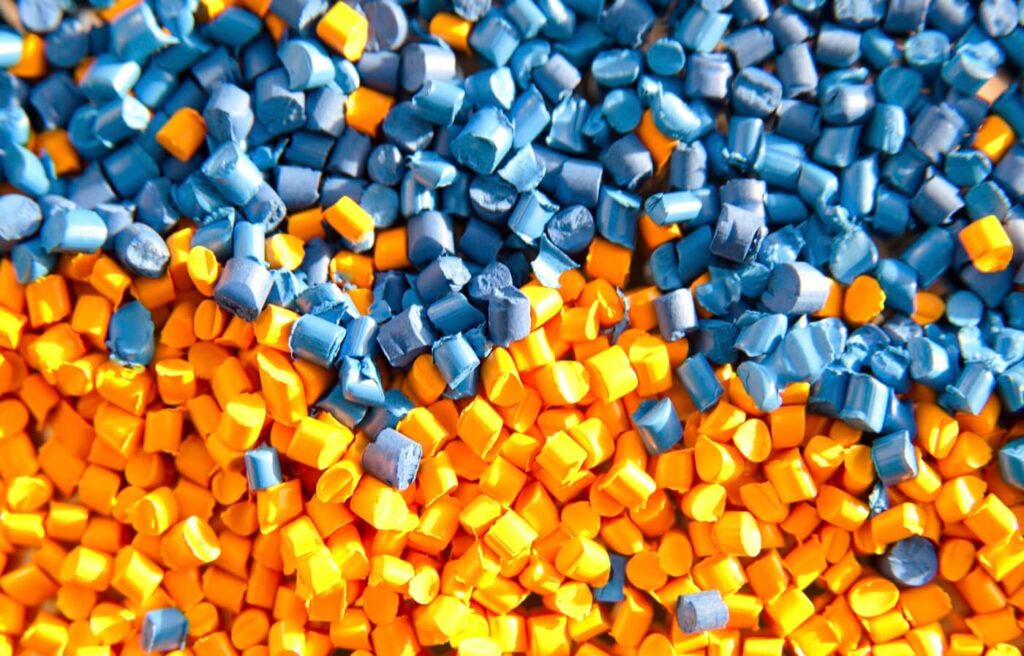
5.Better Chemical Resistance
By combining different polymers with different chemistries, manufacturers can create blends that are resistant to specific chemicals or environmental conditions. This is particularly important for industries where products may be exposed to harsh chemicals or extreme temperatures.
6.Sustainability
By using recycled or bio-based polymers in blends, manufacturers can reduce their reliance on virgin materials and minimize their environmental impact. This is particularly important in today’s society, as sustainability is a growing concern.
7.Better Dimensional Stability
By combining polymers with different shrinkage rates, manufacturers can create blends that have minimal dimensional changes during cooling and solidification. This is critical for industries that require precise dimensions, such as automotive or aerospace.
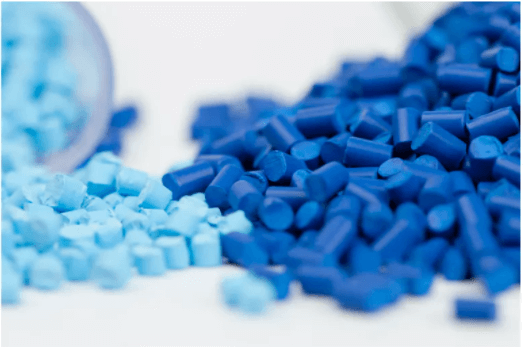
In summary, there are numerous benefits to using polymer blends in injection molding. From improved mechanical properties and cost savings to enhanced processing and aesthetics, polymer blends have revolutionized the manufacturing process.
Additionally, their improved chemical resistance, sustainability, and dimensional stability make them a top choice across industries. The use of polymer blends in injection molding is likely to continue to grow as technology continues to advance, further enhancing the production of high-quality, cost-effective and sustainable products.