How Hard Anodizing Works and Its Applications
Hard anodizing is a surface treatment process used to improve the robustness, corrosion resistance, and wear resistance of metal parts. Hard anodizing is an electrochemical process that forms a thick oxide layer on the outer layer of metal, which provides various benefits to different industries. This article will delve into the details of hard anodizing, including its process, applications, advantages, and considerations.
1.What is hard anodizing?
1) Process Overview
Hard anodizing, or Type III anodizing, is an electrochemical cycle that involves immersing a metal part (usually aluminum) in an electrolytic cell and applying an electric current to the cell and the part (similar to an electroplating unit). The anodizing process actually involves cleaning the part, removing the naturally occurring oxide layer, and electrochemically depositing a new, more uniform oxide layer. This more uniform and stronger oxide layer is made up of aluminum oxide. The hard anodized layer is also harder and more wear-resistant than the naturally occurring aluminum oxide layer.
2) Key Characteristics of Hard Anodizing
The following are the key characteristics of hard anodized coatings:
① Coverage Thickness
Hard anodizing typically produces an oxide layer with a thickness of 0.0005”, and the coating thickness can reach 0.004”. Hard anodizing thickness is much greater than the naturally occurring anodizing process (0.00000018”).
② Surface Hardness
The subsequent oxide layer hardness can be as high as Rockwell C 60-70, with significant wear resistance.
③ Corrosion Resistance
The main function is to protect the component from corrosion, making it suitable for use in harsh conditions.
④ Electrical Properties
Hard anodized surfaces are not good electrical conductors, so they are valuable in applications where electrical insulation is required.
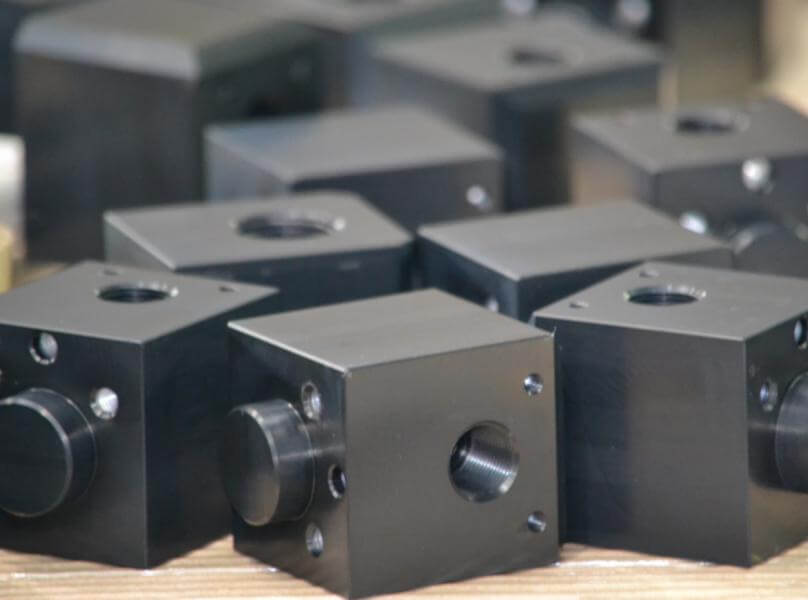
2.Applications of Hard Anodizing
1) Aerospace
Hard anodizing is widely used in aerospace applications because it improves the robustness and corrosion resistance of essential components such as landing gear, hydraulic drive systems and aircraft main components.
2) Automotive
Hard anodizing is used in the automotive industry to improve wear resistance and resist material degradation of cylinders, chamber liners and engine parts.
3) Medical devices
Clinical instruments are often hard anodized to guarantee their service life, corrosion resistance and biocompatibility.
4) Consumer parts and hardware subjected to severe wear and repeated contact
Components such as pressure drive chambers and pinions can benefit from hard anodizing.
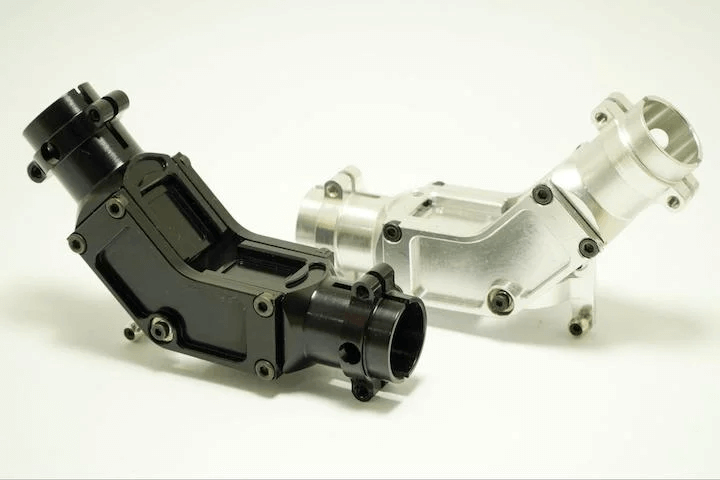
3.Advantages of Hard Anodizing
1) Further developed wear-resistant hard
Anodizing improves the wear resistance of parts, making them suitable for applications with high wear levels and repeated contact.
2) Improved corrosion protection
The anodized layer prevents corrosion and extends the service life of treated parts, especially under harsh conditions. In this context, corrosion means performance degradation or surface corrosion.
3) Electrical Protection
Hard anodizing provides electrical protection, making it particularly useful in electronic and electrical applications.
4) Delamination Robustness
The interaction does not fundamentally change the elements of the treated component. It can maintain tight tolerances with little effect, especially suitable for complex assemblies.
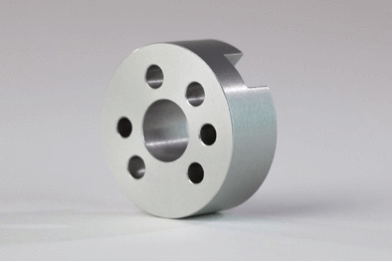
4.Hard Anodizing Considerations
While hard coat anodizing offers a variety of advantages, there are still some things to consider before specifying hard coat anodizing for your next project.
1) Material Selection
Hard anodizing is mainly used on aluminum substrates because they produce the best results.
2) What metals can be hard anodized?
Aluminum, magnesium, titanium, and stainless steel can all be hard anodized. All of these metals have a natural oxide layer and all have a strong affinity for oxygen.
3) Surface Finish
The nature of the underlying surface finish will affect the final result. A smoother surface will produce a more uniform coverage.
4) Cost and Time
Hard anodizing can be more expensive and time-consuming than other surface treatments. Regardless, its advantages often offset the cost, especially in demanding applications.
5.Conclusion
Hard anodizing is a very effective surface treatment process that works primarily on the toughness, wear resistance and corrosion resistance of metal parts. Its applications range from aviation to medical instruments, playing an important role in improving the wear resistance and service life of critical components in different industries. When considering surface treatment for parts that are subject to harsh conditions, hard anodizing is a proven and reliable choice.