The Advantages of Hard Milling on CNC Machines
Hard milling is a machining process that uses CNC (computer numerical control) machines to cut and shape hard materials. The process is particularly suitable for machining materials such as hardened steel, tool steel and cast iron, which are known for their high hardness and toughness. Examples include projection on a rotating machine part, screw-machined mechanical parts for heavy-duty vehicles and screw-machined parts to automotive industry standards.
CNC machine hard milling has a variety of advantages over traditional milling methods, making it a popular choice in many industries. For example, projection on a rotating machine part, screw-machined mechanical parts for heavy-duty vehicles and screw-machined parts to automotive industry standards.
Key benefits of hard milling on CNC machines
One of the main advantages of hard milling on CNC machines is the ability to achieve high precision and accuracy. CNC machines are equipped with advanced technology and computer-controlled systems that allow for precise control of the cutting tools. This level of control ensures that the desired dimensions and tolerances are consistently met, resulting in parts that fit together perfectly and perform their intended functions flawlessly.

In addition to precision, hard milling on CNC machines also offers increased productivity. The use of CNC machines eliminates the need for manual labor because the entire process is automated. It also means multiple parts can be machined simultaneously, reducing overall production time. In addition, CNC machine tools can run continuously 24 hours a day without breaks, resulting in higher productivity and faster turnaround times.
Another advantage of hard milling on CNC machines is the ability to achieve complex geometries and intricate designs. CNC machines are capable of executing a wide range of cutting paths and tool movements, allowing for the creation of intricate shapes and contours. This versatility opens up new possibilities for designers and engineers, enabling them to create parts with complex features that would be difficult or impossible to achieve using traditional milling methods.
Furthermore, hard milling on CNC machines offers improved surface finish and quality. CNC machines are equipped with high-speed spindles and cutting tools that can achieve smooth and precise cuts. This results in parts with superior surface finishes, reducing the need for additional finishing operations such as grinding or polishing. The improved surface finish not only enhances the aesthetic appeal of the parts but also improves their functionality and performance.
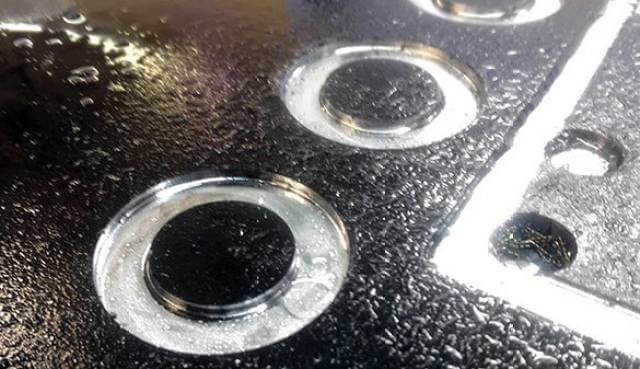
Additionally, hard milling on CNC machines offers cost savings. While the initial investment in CNC machines may be higher compared to traditional milling machines, the long-term cost savings are significant. CNC machines require minimal operator intervention, reducing labor costs. They also have a longer tool life, as the cutting tools are subjected to less wear and tear due to the precise control and reduced cutting forces. This means fewer tool replacements and lower tooling costs in the long run.
In conclusion, hard milling on CNC machines offers numerous advantages over traditional milling methods. The precision, productivity, ability to achieve complex geometries, improved surface finish, and cost savings make it an attractive option for many industries. As technology continues to advance, CNC machines are becoming even more capable and efficient, further enhancing the advantages of hard milling. Whether it’s in the automotive, aerospace, or medical industry, hard milling on CNC machines is revolutionizing the way hard materials are machined, leading to improved quality, efficiency, and profitability.