The Importance of High Precision Machining in Modern Engineering
Due to innovative technologies and an expanding global market, OEM engineer leaders face new challenges every day. They are looking for ways to increase profit margins, satisfy consumers, and attract consumers with uniqueness. High precision machining may be an effective way to maintain a competitive advantage.
In this blog post, we will give you a detailed introduction to high precision machining, its benefits, and why it is important.
1.What is high precision machining?
It is a process that uses the raw materials of an object to create a smaller-sized finished product. This process involves many cutting machines, ergonomic techniques, and software applications.
It is an extensive process that requires extreme caution and full concentration. Companies that require third-party organizations to produce machine parts also rely on other companies for precision machining work.
There are many reasons for outsourcing work, either the company is overwhelmed or the company is small and cannot afford CNC machines. There is no harm in outsourcing, however, it is important to consider all options before hiring a third party.
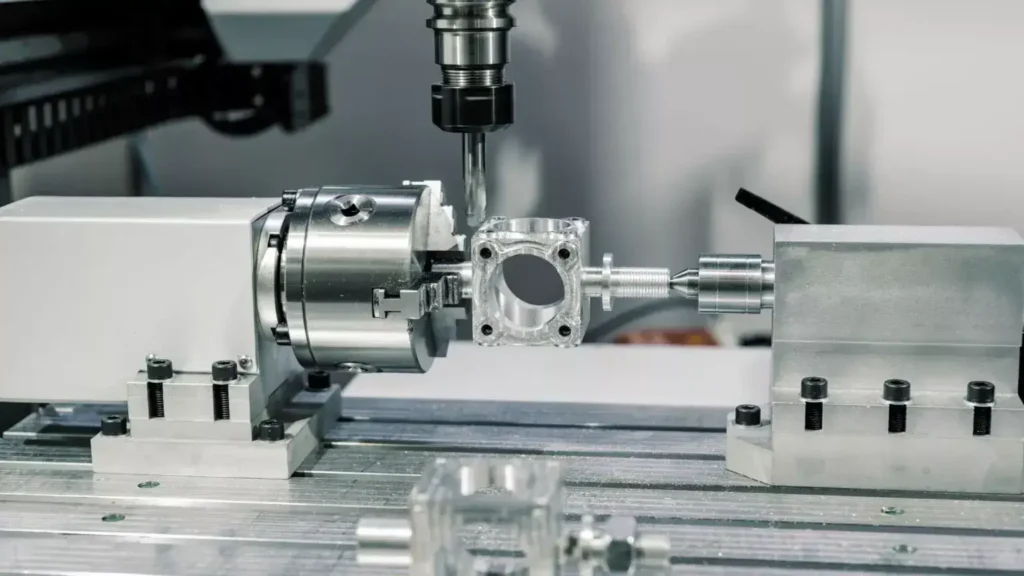
2.CNC machining technology
Modern and established manufacturers prefer products and parts to meet precise given dimensions. Therefore, today’s manufacturers rely on computer numerical control machines. For example, some manufacturers have built their own multi-axis CNC milling machines. They have turned these machines into their own workshops.
3.Advantages of High Precision Machining
Below, we have listed the advantages of outsourcing and using high precision machining.
1) Low Errors
When using high precision machining, the possibility of error is eliminated. All you have to do is make sure to enter the correct specifications. Once entered, the automated precision machining method will take over.
Compared with manual machining, the chance of error is very low. Outsourcing this work can eliminate your need for highly skilled and experienced employees required to operate the machine.
2) Reduced Material Waste
Since the main purpose of precision machining is to reduce volume, it goes without saying that material waste is greatly reduced. After all, especially in the case of manual machining, the possibility of material waste is high.
However, using precision machining can reduce material costs. Hiring a professional high precision machining company can save additional material costs.
How? These companies purchase materials in bulk. This way, their costs are reduced and they will pass on the savings to you.
3) high precision machining Provides Consistency
With high precision machining, consistency is achieved from beginning to end. Each product or part will have the same quality and excellence. Even if you produce in multiple batches, the quality of the product or part will remain consistent.
This consistent premium quality will increase customer satisfaction and increase customer leads. It will also enhance customer confidence in your brand.
4) Improved Workflow
Companies that allow engineers to work on product development instead of making minor design changes are always able to manage opportunity costs. So when you contact a professional high precision machining service provider, they will make minor modifications during the prototyping process.
This is to ensure that the product meets the requirements as well as industry standards. Since the company will do the tedious and meticulous work, the engineers will have ample time for product development.
5) Reduced Turnaround Time
With high precision machining, it is undeniable that the turnaround time is greatly reduced. After all, machines are able to work more effectively and efficiently than humans. Therefore, even if you have an in-house high precision machining system or intend to hire a third party, you will see a reduction in turnaround time.
However, contacting an experienced company will further reduce the turnaround time. Since they have a business running, all the equipment and labor are in place, and they are experienced. A third-party precision machining company will produce more effective and efficient results.
6) Production Cycle
With high precision machining, you can launch products at a much faster pace. This will give you an edge and flexibility in competing with companies that still rely on traditional methods to build your own products.
More importantly, you will be able to seamlessly update and upgrade your products in line with changing customer requirements and industry standards.
7) Prototype Testing
With precision machining, it is now possible to explore smaller markets with higher return potential. When identifying niche market opportunities, you can take advantage of the flexible product development phase of precision machines. If your product has market scope, you can move to full production mode without any difficulty.
Unlike concept prototypes, precision machined prototypes provide functionality. They will give you a clear picture of how your product will feel, look, and work in a real environment.
In addition, functional prototypes can better attract the attention of investors than prototypes that are only concepts.
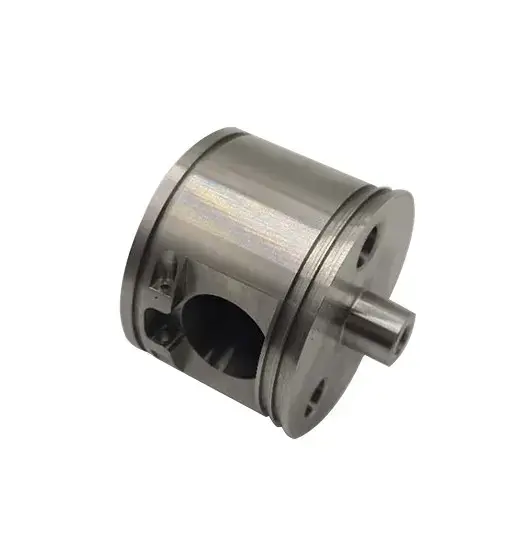
4.Importance of High Precision Machining
High precision CNC machining has evolved into an essential part of the manufacturing cycle. It provides efficiency, accuracy, and effectiveness. Precision machining has become a necessity in all walks of life.
Here are some industries that use high-precision machining extensively.
1) Medical Device Industry
Orthopedic and cardiovascular devices rely heavily on EDM and 5-axis milling. In addition, other implants and surgical instruments also use this precision machining to produce consistently high quality parts.
- Medical CNC Machining
Several factors directly affect the outcome of a medical procedure. The same rules apply to medical CNC machining. When the equipment is able to control dust and temperature, it can guarantee high-precision results. Moreover, it needs to ensure an ideal environment for each procedure as well as tight tolerances.
- Surgical Scissors
These are perhaps one of the most important tools. Doctors use them in almost every medical procedure. They have a variety of uses. For example, doctors use them to enter the skin or perform sutures.
These scissors come in different sizes and shapes. Therefore, they are suitable for different surgical procedures. For example, the surgical scissors required for eye surgery are very small. These scissors require precision and consistency in terms of quality.
Therefore, surgical manufacturers choose reliable, professional, and experienced CNC machine shops.
- Cannulas
Intravenous cannulas are a popular medical product as they are in demand in almost all medical centers around the world. Like many surgical instruments, these products come in a variety of sizes and shapes. They come in a variety of sizes and shapes, just like the gauges of a needle.
To make high-precision housings, manufacturers need to use wire cutting or multi-axis milling. Because both are state-of-the-art CNC.
- Saws used in orthopedic surgery
Because orthopedic surgeons need high-precision equipment. The reason is, they have to use saws to cut human bones. An accurate and precise saw will help you cut as quickly as possible without cutting too deep.
To ensure the precision and quality of each saw, it is important to rely on professional high precision processing manufacturers.
2) Aircraft
Modern advanced aircraft no longer rely on canvas biplanes and wooden lines. Their growing demand for precision and complexity requires something stronger and more robust.
Today’s aircraft require consistency, durability, and sturdiness. The complexity of today’s aircraft cannot be overstated. They have aircraft turbines, decorative systems, sophisticated avionics, advanced engines, and hydraulic surfaces.
All of these parts require advanced, high quality components to function properly. When it comes to building air travel, aircraft must have the best components to operate safely, reliably, and efficiently.
There is no denying the importance of precision machining in military aviation and civil aviation components. In some cases, precision machining engineers redesign the overall application level to enhance its functionality.
5-axis CNC machine tools are an excellent way to ensure part accuracy and quality. It is used in aircraft components. It also has a good service life.
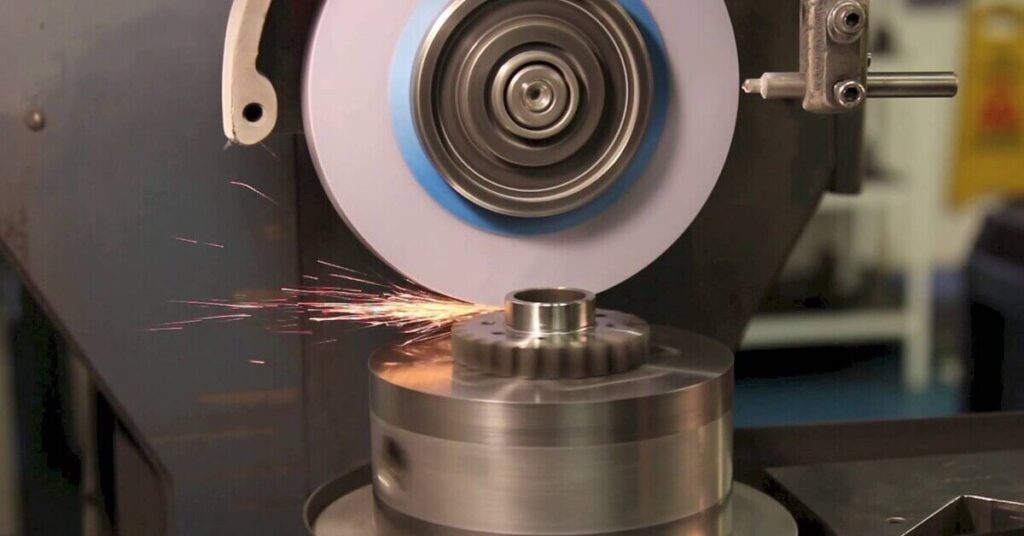
5.High precision machining jobs
In terms of work, CNC machining is very important. Manufacturers are always looking for people with experience in business management, team leadership, and the following areas.
1) Specialists or tool workers
For those who are proficient in CNC machining tools, the prospects are bright. They are engaged in jobs such as turning dies, tool group production, basic programming knowledge, fixture development, fixture design, etc.
2) Machinists
This includes multiple roles from floor managers to operators.
6.Summary
Precision CNC machining is a new way to produce high quality, precision parts and guarantee the accuracy of batch after batch of parts. However, in order to ensure the smooth progress of the entire project, you need to choose a professional high precision manufacturer.