A complete analysis of the structure, application and manufacturing process of high pressure check valves
High pressure check valves are a key valve widely used in high-pressure fluid systems. Their main function is to prevent the backflow of media and ensure the stable operation of the system. In industries such as petroleum, natural gas, chemical industry, nuclear energy and hydraulic equipment, high pressure check valves play a vital role.
Since the fluid under high-pressure environment has a large impact force and pressure change, the design and manufacture of high pressure check valves need to consider their pressure resistance, sealing performance and fatigue resistance.
This article will conduct a detailed analysis of the structure and working principle, application field, selection points and manufacturing process of high pressure check valves to help readers have a deeper understanding of the characteristics and practical applications of this type of valve.
1.Structure and working principle of high pressure check valves
(1) Basic working principle
High pressure check valves are a type of fluid control valve that automatically opens and closes based on the flow pressure of the medium itself to prevent fluid backflow. When the fluid flows forward, the valve disc opens under pressure and the medium flows unimpeded; when the fluid flows backward, the valve disc closes quickly under the action of spring force or back pressure to prevent the fluid from flowing in the opposite direction.
In a high-pressure environment, the opening and closing of the check valve needs to overcome greater pressure fluctuations. Therefore, its design needs to consider high-pressure resistant materials, fluid dynamics optimization, and sealing performance to reduce energy loss and system impact.
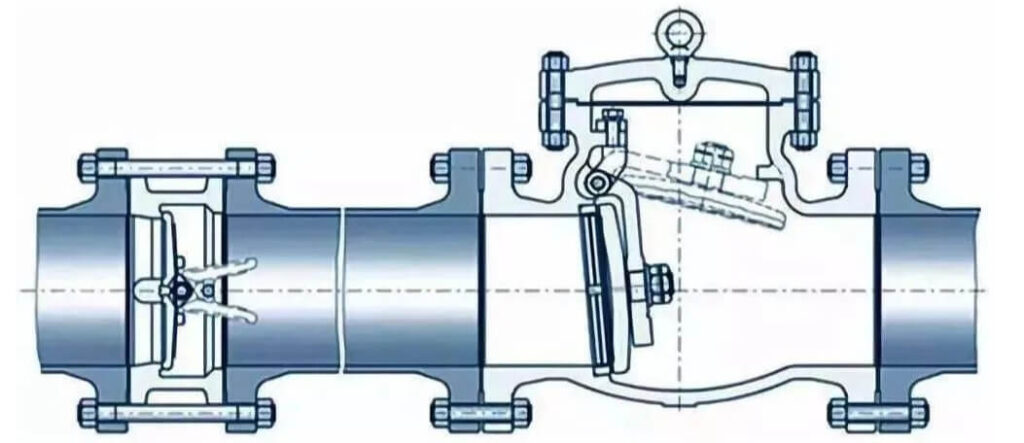
(2) Main structural components
1) Valve body material:
High-pressure environments require the valve body to have extremely high strength, corrosion resistance, and high temperature resistance. Common materials include alloy steel, stainless steel, titanium alloy, etc.
2) Seals:
The sealing performance determines the reliability of the check valve. Common sealing methods include hard seals (such as metal to metal) and soft seals (such as rubber, PTFE, etc.).
3) Internal components:
Mainly includes valve discs, valve seats, springs, flow guide chambers, etc. A reasonably designed internal structure can effectively reduce flow resistance and improve opening and closing efficiency.
2.Different types of high pressure check valves
According to application requirements and structural characteristics, high pressure check valves are mainly divided into the following types:
(1) Piston check valve:
Applicable to liquid and gas high-pressure systems, stable opening and closing, and excellent sealing performance.
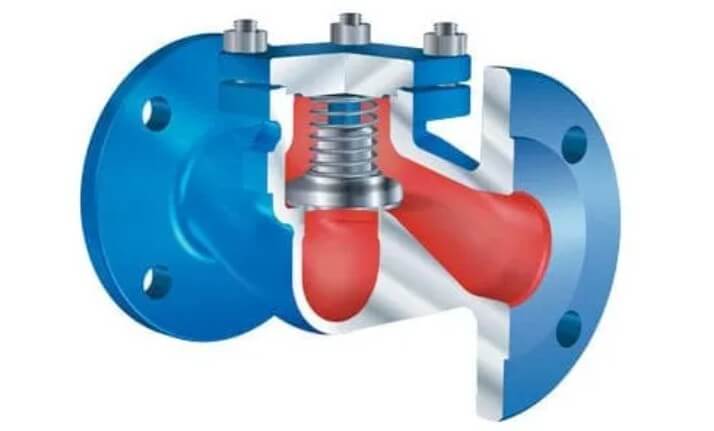
(2) Swing check valve:
Applicable to large flow pipelines, can reduce fluid resistance and improve flow capacity.
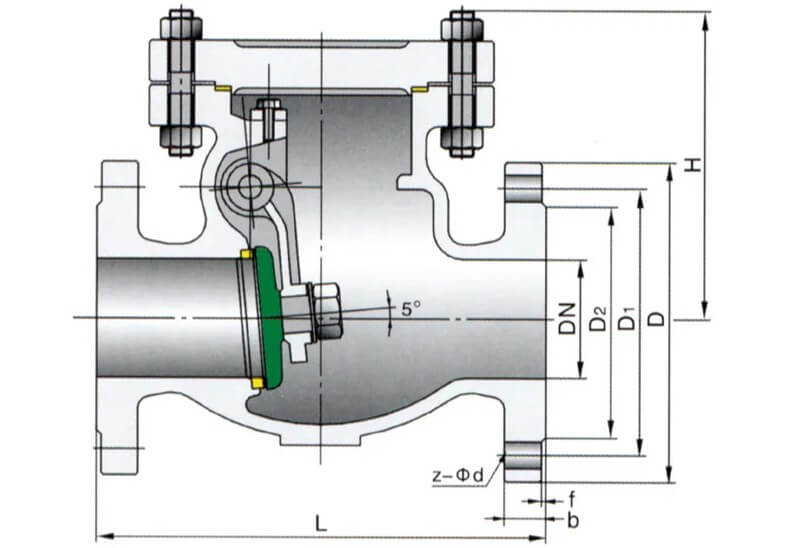
(3) Double-flap check valve:
The double-flap structure reduces the water hammer effect and is suitable for working conditions with large fluid impact in high-pressure systems.
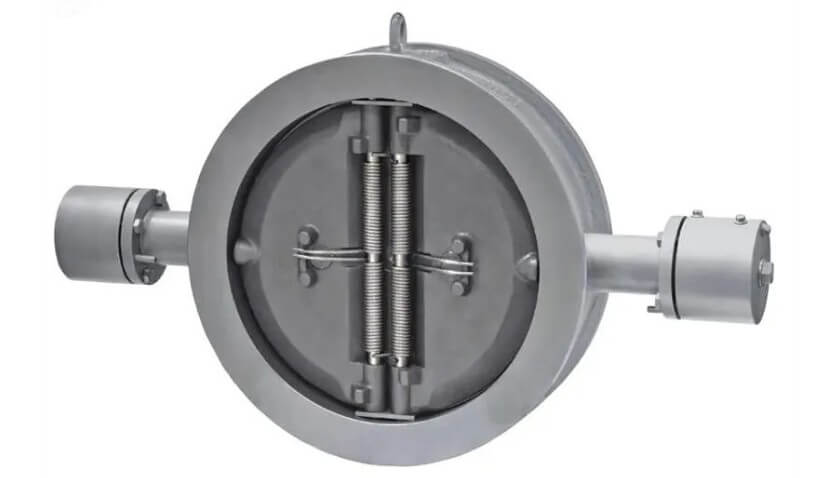
3.Application areas of high pressure check valves
(1) Oil and gas industry
1) Transportation pipelines:
During the oil and gas transportation process, high pressure check valves are used to prevent gas or liquid backflow and avoid system damage caused by sudden pressure changes.
In addition, it can also reduce pressure fluctuations in the transportation pipeline, improve transportation efficiency, and reduce energy loss.
2) Wellhead equipment:
In oil drilling and wellhead control equipment, high pressure check valves can ensure the unidirectional flow of drilling fluid and prevent dangerous situations such as blowouts.
3) Compressor system:
In natural gas processing and compressor systems, check valves can effectively prevent high-pressure gas backflow, prevent equipment damage, and improve system stability.
(2) High-pressure hydraulic system
1) Hydraulic pump protection:
Hydraulic equipment (such as hydraulic pumps and hydraulic cylinders) usually operate under high-pressure environments. High pressure check valves can ensure unidirectional flow of hydraulic oil and improve system stability. It can also prevent hydraulic backflow from damaging the pump and extend the life of the equipment.
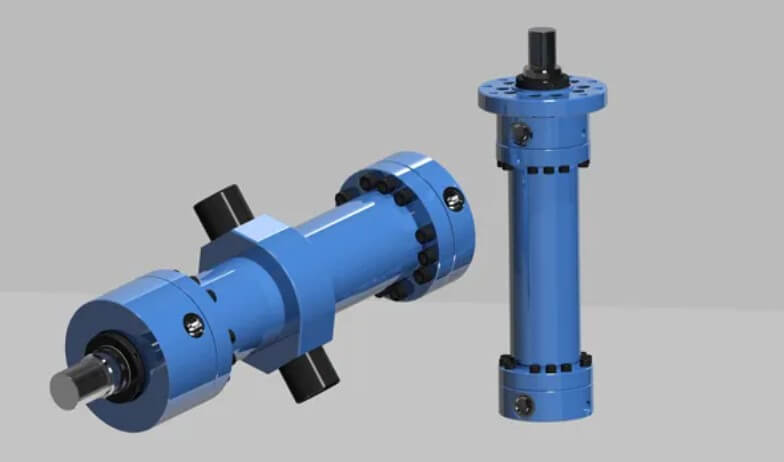
(High pressure check valve included)
2) Industrial machinery:
Such as CNC machine tools, automated production lines, hydraulic lifting equipment, etc., high pressure check valves can control the flow direction of the hydraulic system to ensure the normal operation of the system.
3) Ships and heavy machinery:
High-pressure hydraulic systems are widely used in ship propulsion, lifting equipment and other occasions. High pressure check valves ensure stable operation of the oil circuit and avoid damage to the equipment caused by hydraulic shock.
(3) High-temperature and high-pressure steam system
1) Thermal power plant:
In steam boilers and high-pressure steam pipelines, high pressure check valves can prevent steam backflow, protect equipment safety and improve energy efficiency.
2) Chemical plant:
The high-temperature and high-pressure medium used in chemical production needs to be controlled by a check valve to ensure process stability.
3) Pharmaceutical and food processing:
During high-pressure steam sterilization and heat treatment, high pressure check valves help maintain system pressure and safe operation.
4.Key points for selecting high pressure check valves
(1) Working pressure and fluid characteristics
1) Pressure level:
According to different working conditions, select check valves that are suitable for high-pressure environments, such as ultra-high pressure (>100MPa) or medium-high pressure (10MPa-100MPa) valves.
2) Fluid characteristics:
Consider the viscosity, temperature, and corrosiveness of the medium and select appropriate sealing materials and structures.
(2) Material selection
1) High-temperature resistant materials:
Such as nickel-based alloys and titanium alloys, suitable for extreme temperature environments.
2) Corrosion-resistant materials:
Such as Hastelloy and 316L stainless steel, suitable for strong acid and strong alkali media.
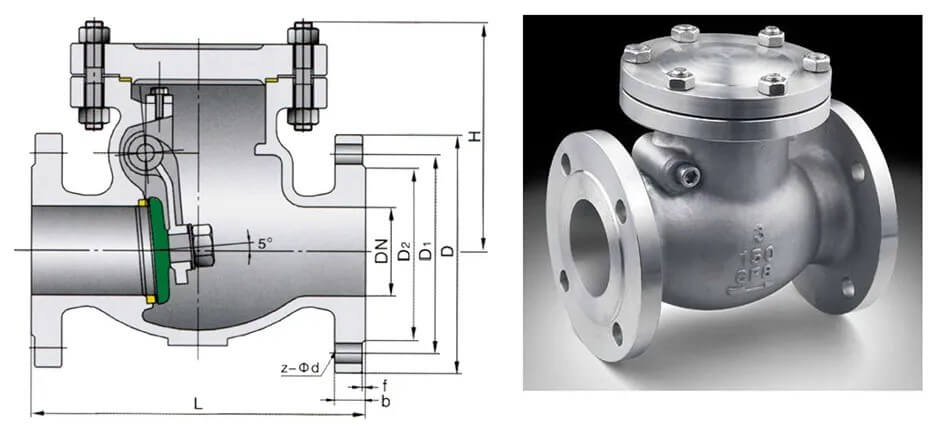
(3) Sealing performance requirements
1) Zero leakage requirements:
For high-risk environments (such as the nuclear industry), advanced sealing technology is required to ensure zero leakage.
2) Wear-resistant seals:
Such as ceramic sealing surfaces, suitable for high-pressure flushing environments.
5.Manufacturing process of high pressure check valves
(1) Selection of manufacturing materials
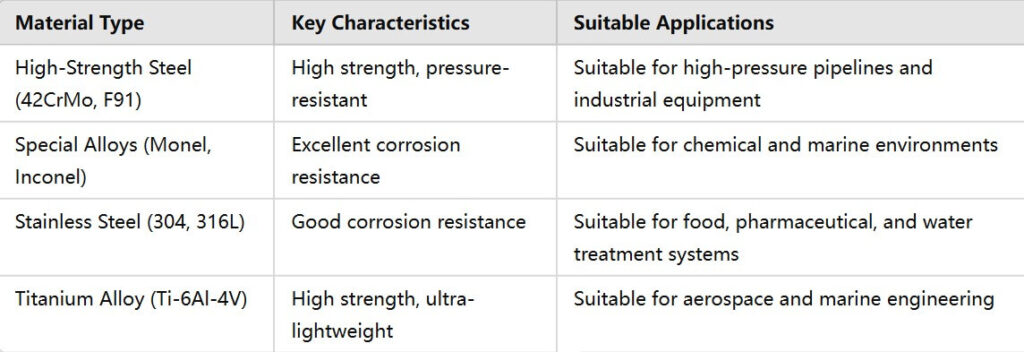
(2) Key production processes
1) Valve body processing
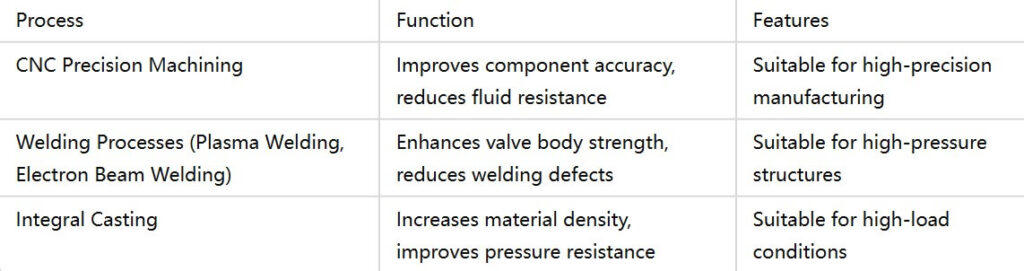
2) Sealing surface treatment
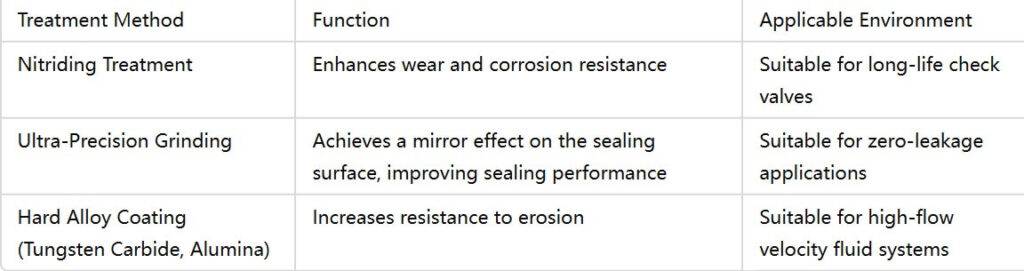
3) Spring and internal component manufacturing
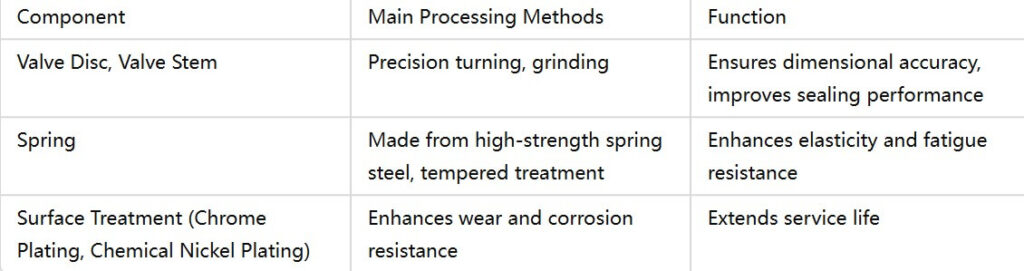
(3) Comparison of processing difficulty of different valve types
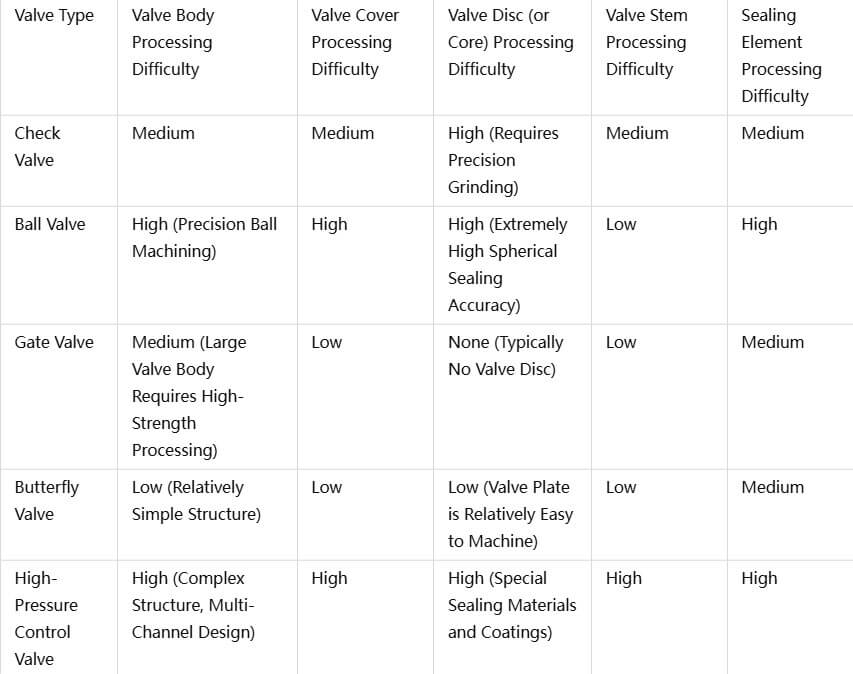
6.Summary
The correct selection, high-quality manufacturing and reasonable application of high pressure check valves can improve the safety and reliability of the system. By adopting advanced materials, precision processing and optimized sealing technology, high pressure check valves can play a key role in high-pressure fluid systems and ensure long-term stable operation.