Advantages of Anodizing
Seeing rust on an iron or steel surface can be alarming. Needless to say, if your car parts start to turn a noticeable reddish-brown color—what happens to iron during the oxidation process—you may need to visit a repair shop or car dealer.
But not all oxidation is bad. In fact, one of the reasons aluminum is so useful and versatile is precisely because it oxidizes immediately upon contact with oxygen. While this oxidation is chemically similar to iron rusting, it actually protects the underlying structure of the aluminum by forming a durable outer surface that prevents further oxidation from spreading. With rusting iron, on the other hand, the oxidized surface eventually flakes off, causing more of the underlying iron structure to oxidize and eventually degrade.
In the early 20th century, chemical engineers developed a process based on aluminum’s natural self-protective oxidation process that essentially thickens the protective oxide layer on the metal’s surface by passing an electric current through the metal in an electrolytic acid bath. The process is now called anodizing and can be used on aluminum, titanium, and other metals.
1.Improve Your Electronics with Anodizing
While anodizing is used for a variety of different purposes across many industries, it has become an essential tool for electronics manufacturers. This article will explain how it can help you create superior electronic devices using Xavier’s trusted anodizing process.
① Vivid colors
Anodizing is often seen as an excellent method for adding color to aluminum and titanium items. This is because the oxide layer produced by the process is porous, allowing dye to flow neatly into the crevices. When the anodizing layer is sealed after the dye is applied, the color is more durable than paint, which can easily flake off because it is not embedded in the “pores” of the surface.
A wide range of colors and tones can be achieved using this process. Even light tones can be achieved with a very thin anodizing layer, while darker, more saturated tones can be achieved with thicker anodizing layers.
Most modern Apple devices have this finish, giving them a durable finish and a high-end look in a variety of colors.
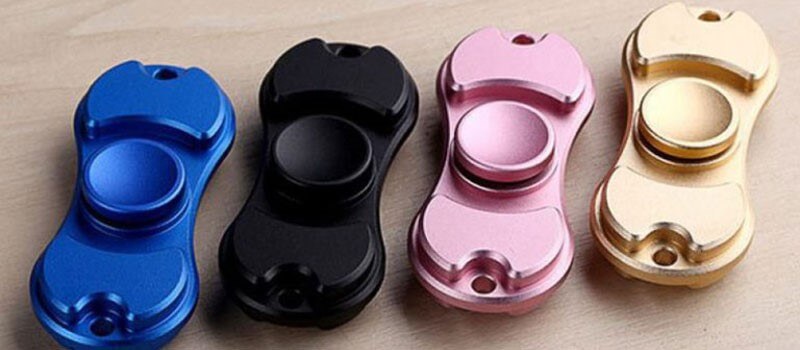
② Electrical and thermal insulation
One of the more practical benefits of anodizing, especially sulfuric acid anodizing (Type II or Type III), is improved electrical and thermal insulation, because aluminum oxide is a better insulator than aluminum. This means that anodized electronics, whose surfaces do not conduct electrical current, have a safety advantage over products that have been treated with other surfaces or not treated at all. This is obviously a huge attraction for consumer electronics manufacturers: anodized surfaces not only look great, but also keep electrical current where it should be. At the same time, the heat insulation provided by the anodized surface is also beneficial for electronic products whose internal components generate heat.
③Corrosion resistance and wear resistance
In addition to improving the appearance and safety of electronic products, anodizing can also improve the wear resistance and corrosion resistance of products. Although anodized surfaces are more prone to cracking at extremely high temperatures, the oxidized outer layer of anodized products will have better corrosion resistance relative to the thickness of the anodized layer. For example, compared with untreated products, the corrosion resistance of an MP3 player with a thin anodized coating is slightly improved, while the corrosion resistance of another MP3 player with a thick anodized coating will be significantly improved.
Anodized surfaces can also effectively improve the wear resistance and scratch resistance of products, thereby extending the shelf life of products and maintaining a better appearance.
2.What Xavier can provide
Xavier has many years of experience in surface treatment, providing processes such as polishing, painting, coloring and powder coating. It also offers comprehensive anodizing solutions, including four different processes:
① Anodizing Type I
Uses chromic acid to produce a thin and ductile anodized layer
② Anodizing Type II
Uses sulfuric acid to produce a medium-thick anodized layer suitable for coloring
③ Anodizing Type III
Uses sulfuric acid to produce a thick anodized layer suitable for coloring
④ Chemical film/aluminum anodized film
Applies an aluminum anodized film to the surface of the part to produce an anodizing-like effect.