How to Achieve the Perfect CNC Surface Finish
CNC machining has revolutionized the manufacturing industry, making the production of complex parts precise and efficient. However, achieving a perfect surface finish on CNC machined parts can be a daunting task.
In this article, we will explore the basics of CNC surface finishing and provide some tips on how to achieve the desired results.
1.Basics of Surface Finish
First, it is important to understand that it refers to the quality and smoothness of the surface of the machined part. A good surface finish is not only visually appealing, but it is also essential for functional purposes.
It affects the performance, durability and even life of the part. Therefore, achieving a perfect surface finish is essential to ensure the overall quality of the product.
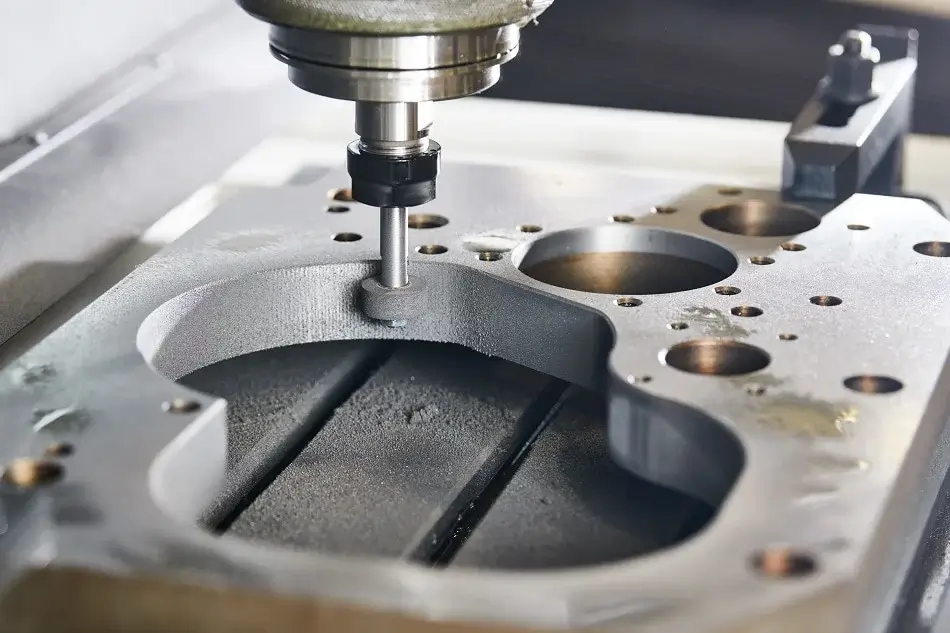
2.Factors Affecting Surface Finish
1) Cutting Tools
Different types of cutting tools such as end mills, drills, and reamers can produce different surface effects. Factors such as tool geometry, materials, and coatings can all affect it. It is important to select the right cutting tool based on the desired surface finish and the material being machined.
2) Cutting Parameters
These include cutting speed, feed rate, and depth of cut. Adjusting these parameters can significantly affect it. For example, increasing the cutting speed can make the surface smoother, while reducing the feed rate can help reduce tool marks. It is crucial to find the right balance between these parameters to achieve the desired surface finish.
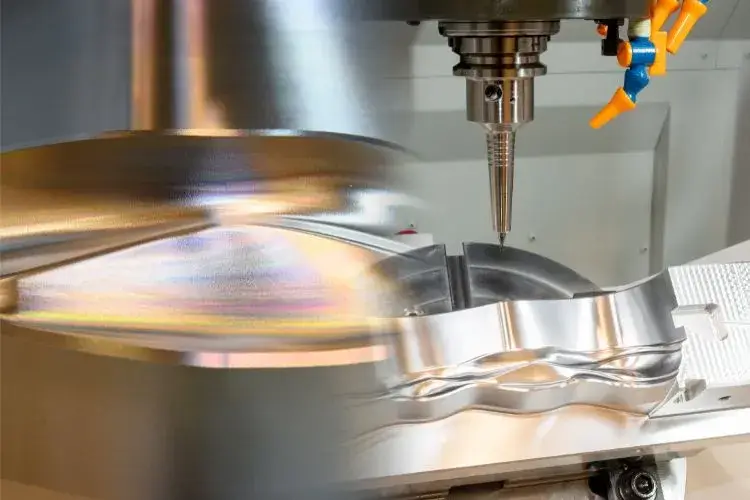
3) Machining strategy
In addition to tool selection and cutting parameters, the choice of machining strategy also affects it. There are a variety of strategies to choose from, such as conventional milling, climb milling, and high-speed machining.
Each strategy has its advantages and disadvantages in various aspects. It is important to understand the characteristics of each strategy and choose the one that best suits a specific application.
4) Processed material
In addition, the material being processed also plays an important role for it. Because different materials have different characteristics and require different machining techniques. For example, machining aluminum requires different cutting parameters compared to machining steel.
Therefore, it is important to understand the material characteristics and choose the appropriate machining technology to achieve the desired surface finish.
5) Post-processing technology
These technologies include deburring, polishing, and coating. Deburring can remove any sharp edges or burrs left after machining, while polishing can enhance the smoothness and glossiness of the surface. Coatings such as anodizing or electroplating can provide additional protection and improve the aesthetics of the part.
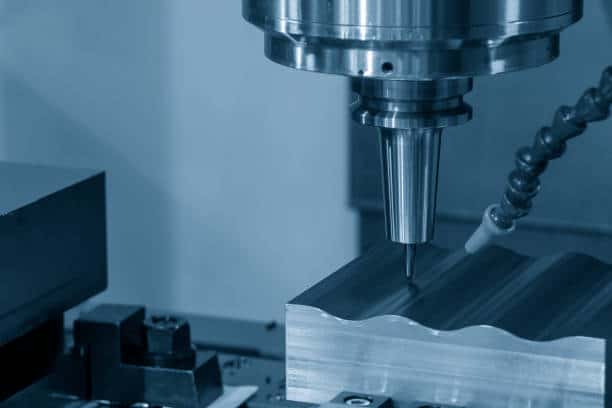
In summary, achieving the perfect surface finish on a CNC machined part requires a combination of factors. This includes selecting the right cutting tool, adjusting cutting parameters, choosing the appropriate machining strategy, understanding material properties, and employing post-processing techniques.
By focusing on these factors and continually improving the process, manufacturers can achieve the desired surface finish and ensure the overall quality of their products.