How to cut 80/20 aluminum profiles efficiently and accurately
In order to achieve efficient and accurate cutting of 80/20 aluminum profiles, it is crucial to choose the right tool and master the correct operating points. Different cutting tools and techniques can have a significant impact on the quality of the final product and productivity. This article will introduce the importance and challenges of cut 80/20 aluminum profiles, several commonly used tools for cut 80/20 aluminum profiles, their techniques and operating procedures, to help improve cutting accuracy and efficiency.
1.80/20 aluminum profile related introduction
(1) Characteristics of aluminum and its applications
Aluminum is widely used in many fields such as aviation, automobiles, construction and electronic products due to its light weight, high strength, good electrical conductivity and corrosion resistance. These characteristics of aluminum make it indispensable in modern industry. Especially in application scenarios that require weight reduction and improved weather resistance, aluminum is one of the preferred materials.
(2) Overview of 80/20 aluminum profiles
80/20 aluminum profile is a highly modular, standardized industrial aluminum system, named for its cross-sectional size, usually 80mm x 20mm. This profile can be quickly assembled into various frames, machine parts and workbenches through specific connectors and accessories, and is widely used in fields such as automation equipment, factory workshops and laboratory furniture. The design of the 80/20 aluminum profile allows users to customize it according to specific needs, providing a flexible and efficient solution.
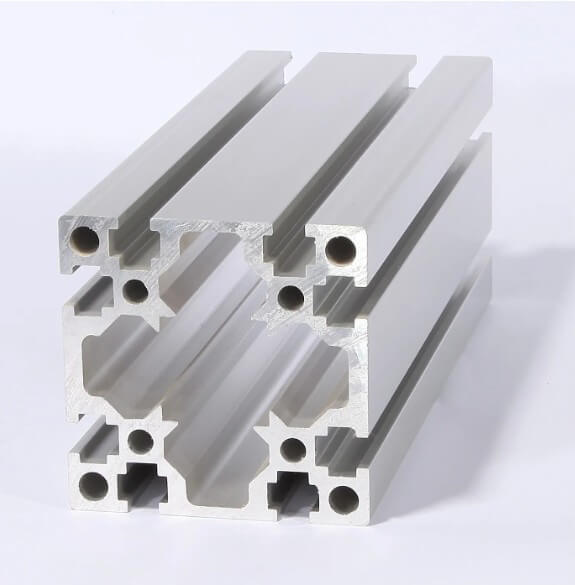
2.Importance and challenges of cut 80/20 aluminum
(1) Importance
1) Accuracy requirements
In many applications, the cutting accuracy of cut 80/20 aluminum profiles directly affects the quality and performance of the final product. For example, in the construction of automated production lines, the dimensional accuracy of aluminum profiles will directly affect the stability and reliability of the entire system. High-precision cutting not only ensures the precise docking of individual components, but also improves the safety and service life of the entire structure.
2) Surface quality requirements
The finish of the cut surface when cutting 80/20 aluminum is critical for subsequent processing and assembly. The smooth and burr-free cutting surface not only reduces friction and wear during assembly, but also improves the appearance quality and service life of the entire structure. Therefore, during the cutting process, special attention needs to be paid to the selection of cutting tools and the setting of cutting parameters to ensure the high quality of the cutting surface.
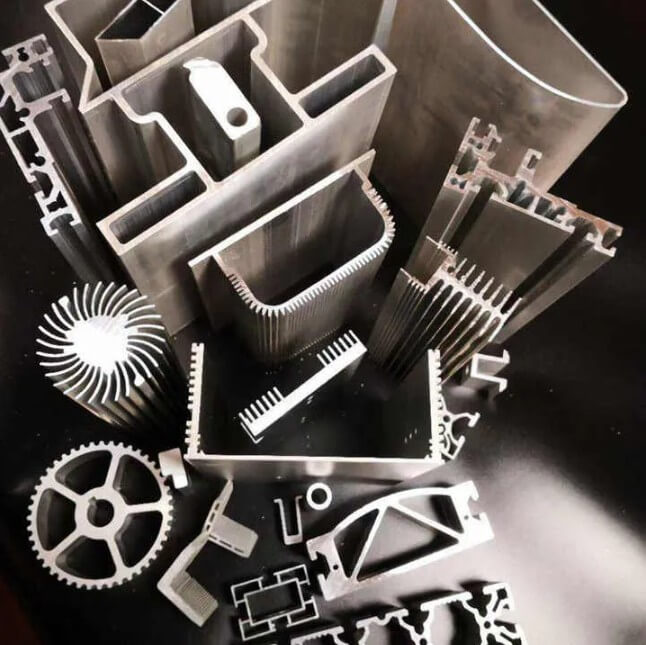
(2) Common problems during the cutting process
1) The incision is uneven
Using improper cutting tools or techniques can result in uneven cuts, affecting the aesthetics and functionality of the assembly. Uneven cuts will not only affect subsequent processing and assembly, but may also lead to a reduction in structural strength, thereby affecting the quality and safety of the entire product.
2) Material deformation
The heat and pressure generated during the cutting process can cause the aluminum to deform, especially when cutting thin-walled or large aluminum. Material deformation will not only affect cutting accuracy, but may also lead to material scrap, thereby increasing production costs and material waste.
3) Low cutting efficiency
Choosing inappropriate cutting equipment or improper parameter settings may lead to low cutting efficiency and affect production efficiency. Low cutting efficiency will not only increase production costs, but may also lead to an extension of the production cycle, thus affecting the company’s competitiveness and market response speed.
3.Selection and use of tools for cut 80/20 aluminum
(1) Introduction to common cutting tools
1) Metal cutting machine:
Metal cutting machines are commonly used tools for cut 80/20 aluminum profiles and are suitable for metal materials of various thicknesses and hardness. It can complete cutting tasks quickly and accurately, and the cutting surface is flat and smooth. However, metal cutting machines are usually more expensive and require certain skills and safety measures to operate.
2) Aluminum cutting saw:
This is a saw blade specially used for cutting aluminum. The design takes into account the characteristics of aluminum and can effectively reduce burrs and deformation during cutting. Aluminum cutting saws are suitable for manual operation and are low-cost, but the cutting efficiency is relatively low.
3) Laser cutting machine:
The laser cutting machine cut 80/20 aluminum through a high-energy-density laser beam, with extremely high cutting accuracy and surface quality. It can handle various complex shapes, but the equipment cost is high.
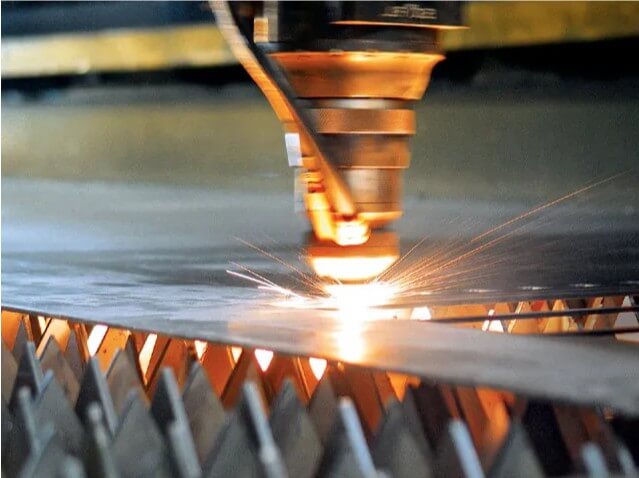
4) Sawing machine:
The sawing machine is a high-precision metal cutting equipment suitable for mass production or aluminum profile cutting with high-precision requirements. The sawing machine can ensure the verticality and dimensional accuracy of the cutting surface when cut 80/20 aluminum, but the equipment cost is high and it occupies a large area.
5) High-speed CNC cutting machine:
High-speed CNC cutting machine is a precision tool for cut 80/20 aluminum, suitable for complex shape cutting and high-precision processing. It cuts with a high-speed rotating tool and has the advantages of high efficiency, high precision, and smooth surface, and is widely used in industrial production.
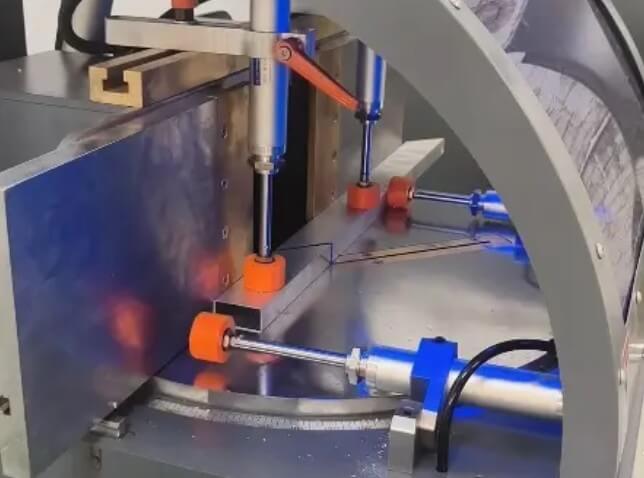
6) Plasma cutting machine:
Plasma cutting machines use high-temperature plasma arcs to cut, and are suitable for thicker aluminum profiles. Its cutting speed is fast, but the cutting surface may have a heat-affected zone, which affects the material properties.
(2) Principles for selecting cutting tools
1) Select according to material thickness and hardness
For thicker 80/20 aluminum profiles, you should choose a cutting tool with more power and tougher blades. For example, using a carbide saw blade can effectively cut thicker aluminum while keeping the cut surface smooth. Carbide saw blades have high hardness, high wear resistance and high thermal stability, which can maintain the sharpness and stability of the blade when cut 80/20 aluminum profiles at high speeds.
2) Select according to cutting accuracy and efficiency requirements
The task of cut 80/20 aluminum with high precision often requires the selection of power tools equipped with high-precision guidance systems, such as CNC cutting machines. CNC cutting machines can achieve high-precision cutting by precisely controlling cutting paths and parameters, and are suitable for complex shapes and large-scale production tasks.
4.Tips and operating procedures for cut 80/20 aluminum
(1) Preparation before cutting
1) Inspection of materials and equipment
Before cutting, make sure the surface of the aluminum profile is clean and free of impurities, the equipment is running normally, and the cutting tools are sharp. The stability of the cutting equipment and the sharpness of the blade directly affect the cutting quality and efficiency. Therefore, a comprehensive inspection and maintenance of the equipment is required before cutting to ensure that it is in optimal working condition.
2) Calibration of cutting line
Use a ruler or marker to accurately mark the cutting line to ensure precise cuts. Accurate cutting line calibration not only improves cutting accuracy, but also reduces material waste and cutting errors.
(2) Operating skills in the process of cut 80/20 aluminum profiles
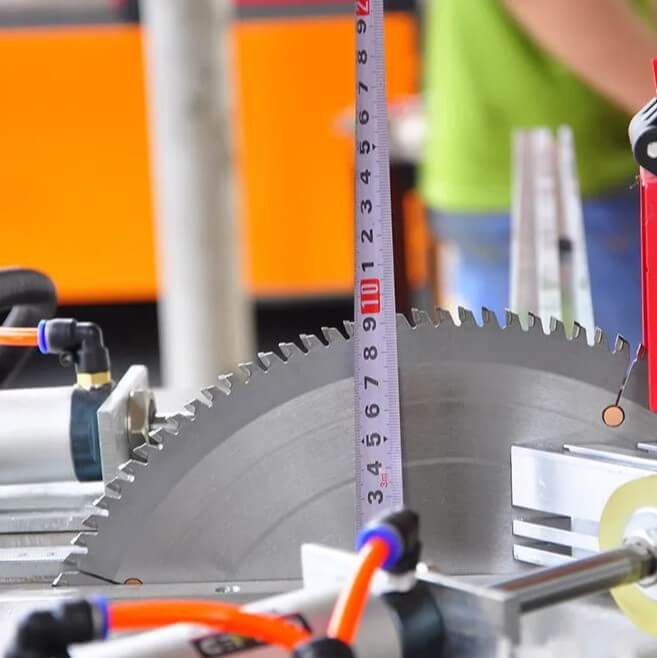
1) Stable holding and feeding speed
When cut 80/20 aluminum, maintain tool stability and uniform feed speed to avoid uneven cutting caused by uneven speed. Stable holding and uniform feed speed are the keys to ensuring cutting quality. During the cutting process, attention needs to be paid to keeping the cutting tool stable and avoiding shaking and vibration to ensure the flatness and accuracy of the cutting surface.
2) Reasonable use of coolant
Proper use of coolant can reduce friction and heat during cutting, preventing material overheating and tool wear. The use of coolant can not only reduce the cutting temperature, but also reduce friction and wear during the cutting process, improving cutting quality and the service life of the tool. When using coolant, you need to pay attention to selecting the appropriate type and amount of coolant to ensure cutting results and equipment safety.
(3) Processing after cutting
1) Cleaning and trimming of incisions
After completing the task of cutting the 80/20 aluminum profile, use a file or sandpaper to clean the edges of the cut to remove burrs and ensure a smooth surface. Cleaning and trimming the incisions are important steps to ensure cutting quality. By cleaning and trimming the cuts, burrs and impurities generated during the cutting process can be removed, ensuring the smoothness and flatness of the cutting surface, and improving the quality and efficiency of subsequent processing and assembly.
2) Safety precautions
Appropriate protective equipment, such as protective glasses, gloves, etc., should be worn when cutting to ensure the safety of the operator. During the cutting process, you need to pay attention to comply with the safe operating procedures. Safe operation is an important part of the cutting process.
5.Methods to improve efficiency and quality when cut 80/20 aluminum
(1) Maintenance and maintenance of equipment
1) Check and replace blades regularly
Carry out regular maintenance on cutting equipment, regularly check the wear of blades, and replace and adjust them in time to ensure that the blades are sharp and reduce wear. The sharpness and stability of the blade directly affect cutting quality and efficiency.
2) Clean and lubricate equipment
During use, the equipment needs to be cleaned and lubricated regularly to ensure that it is in optimal working condition and to improve cutting efficiency and quality. Cleaning and lubrication of equipment are important measures to ensure normal operation of equipment and extend its service life.
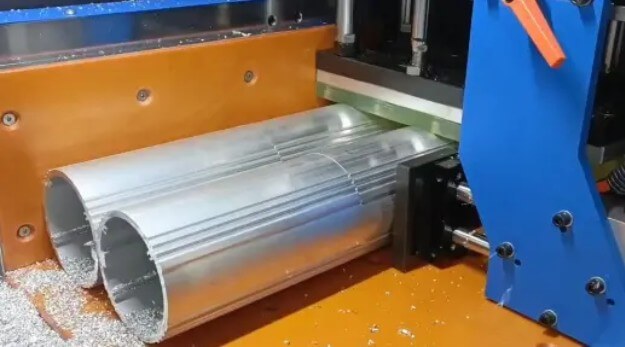
(2) Optimization of cutting parameters
1) Adjustment of feed speed and cutting depth
In the process of cut 80/20 aluminum, the feed speed and cutting depth need to be reasonably adjusted according to the characteristics of the material and cutting requirements to ensure the smoothness of the cutting surface and cutting efficiency. Optimization of cutting parameters is the key to improving cutting efficiency and quality.
2) Reasonable selection of tool angle and type
Choosing the right knife angle and type can significantly improve cutting efficiency and quality. In the process of cut 80/20 aluminum, it is necessary to select the appropriate tool angle and type based on the characteristics of the material and cutting requirements.
6.Summary
By choosing the appropriate cutting tools and mastering the correct operating points, the quality of cut 80/20 aluminum can be significantly improved to meet various precision processing needs.