How to Make Custom Aluminum Parts
Aluminum is a versatile and widely used material in various industries, thanks to its lightweight, corrosion-resistant, and durable properties. Many businesses and individuals often require custom aluminum parts for their specific needs. Whether it’s for automotive, aerospace, or even DIY projects, knowing how to make custom aluminum parts can be a valuable skill.
In this article, we will provide an introduction to custom aluminum parts manufacturing, guiding you through the process and highlighting key considerations. By the end, you’ll have a better understanding of the steps involved and the tools required to create your own custom aluminum parts.
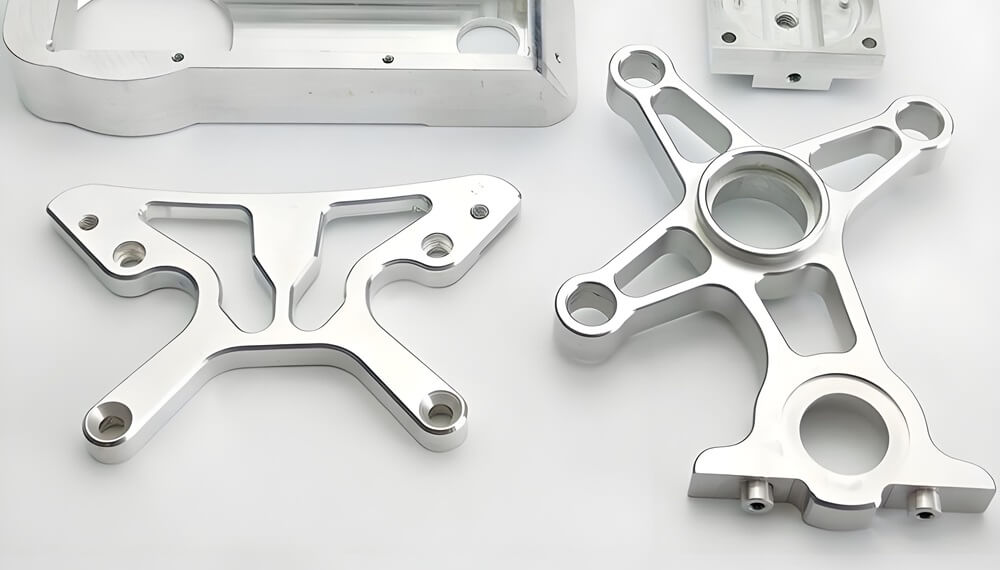
The first step in making custom aluminum parts is to have a clear understanding of the design requirements. This involves determining the dimensions, shape, and specific features of the part. It’s crucial to have accurate measurements and a detailed blueprint to ensure the final product meets your expectations.
Once you have the design specifications, the next step is to choose the appropriate manufacturing method. There are several techniques available for custom aluminum parts manufacturing, including casting, machining, and 3D printing. Each method has its advantages and limitations, so it’s essential to select the most suitable one for your project.
Casting is a common method used for manufacturing custom aluminum parts. It involves pouring molten aluminum into a mold and allowing it to solidify. This process is ideal for producing complex shapes and large quantities of parts. However, it may require additional post-processing steps, such as sanding or polishing, to achieve the desired finish.
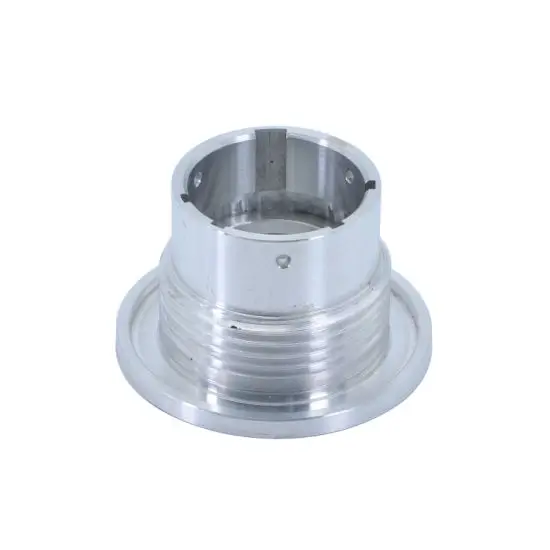
Machining is another popular method for creating custom aluminum parts. It involves removing material from a solid block of aluminum using cutting tools, such as drills, lathes, or mills. Machining offers precise control over the final dimensions and surface finish of the part. However, it can be time-consuming and may require advanced skills and equipment.
In recent years, 3D printing has emerged as a viable option for custom aluminum parts manufacturing. This additive manufacturing technique builds the part layer by layer using a computer-controlled process. 3D printing offers design flexibility and the ability to create complex geometries that may be challenging with traditional methods. However, it may not be suitable for large-scale production due to its relatively slow speed.
No matter which manufacturing method you choose, having the right tools and equipment is crucial. For casting, a furnace is needed to melt the aluminum, molds and various tools for post-processing. Machining requires cutting tools such as end mills or drills, as well as CNC machines or manual equipment. What 3D printing requires is a 3D printer that can handle aluminum materials.
Safety is also an important consideration when working with aluminum. Because aluminum dust and fumes can be hazardous to health, appropriate protective equipment such as gloves, goggles, and respirators must be worn for safety. It is also important to ensure that the workplace is well ventilated to minimize exposure to harmful substances.
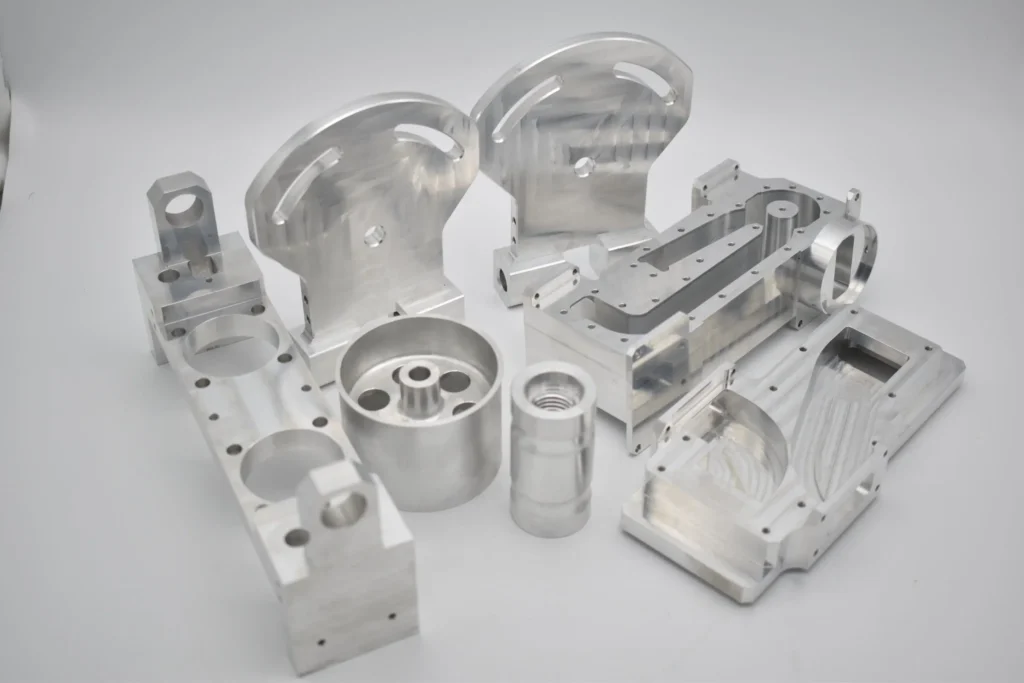
In conclusion, custom aluminum parts manufacturing is a valuable skill that can be useful in various industries and projects. By understanding the design requirements, selecting the appropriate manufacturing method, and having the right tools and safety precautions, you can create high-quality custom aluminum parts that meet your specific needs. Whether you choose casting, machining, or 3D printing, the possibilities for custom aluminum parts are endless.