How to Simplify CNC Machined Part Design
CNC machining, short for computer numerical control machining, is a highly advanced manufacturing process that uses computer-controlled machines to create precise and intricate parts. It has revolutionized the manufacturing industry by making parts production more efficient and cost-effective. Including but not limited to whirlpool washing machine replacement parts, bosch washing machines parts, bosch washing machines spare parts, breville one-touch coffee machine parts uk and brother sewing machines parts.
In CNC machining, factory tools and machinery are controlled by pre-programmed computer software, allowing for three-dimensional cutting tasks to be done with exceptional accuracy. This automated process eliminates the limitations of manual control and ensures consistent production of parts such as whirlpool washing machine replacement parts, bosch washing machines parts, bosch washing machines spare parts, breville one-touch coffee machine parts uk and brother sewing machines parts。
CNC machining plays a significant role in the manufacturing sector, especially in metal and plastic production. Its ability to create highly detailed and accurate products across various materials has made it essential for industries ranging from aerospace to automotive.
In this article, we will explore how to simplify CNC machined part design to enhance efficiency and cost-effectiveness. By embracing design simplicity, involving the manufacturing team from the start, and leveraging standardization opportunities, you can optimize your CNC machining projects for better outcomes.
CNC machining is a highly advanced manufacturing process that utilizes computer-controlled machines to produce precise and complex parts. To ensure successful CNC machining processes, it is crucial to consider the principles of Design for Manufacturability (DFM). DFM involves designing parts that are optimized for efficient and cost-effective production.
When it comes to CNC machining design, there are several key considerations to keep in mind:
- Material Selection: Choosing the right material is essential for achieving the desired functionality and performance of the machined part. Different materials have varying properties, such as strength, heat resistance, and machinability. Understanding these characteristics helps in selecting the most suitable material for the specific application.
- Optimizing Tolerances: Tolerances define the allowable variation in dimensions during the manufacturing process. It is important to optimize tolerances based on the requirements of the part to avoid unnecessary costs or compromises in functionality. Tighter tolerances may result in higher manufacturing costs, while looser tolerances may affect the overall quality of the part.
- Surface Finishes: The surface finish of a CNC machined part affects its appearance, durability, and functionality. Different surface finishes can be achieved through various machining techniques like milling, turning, or grinding. Factors such as roughness, smoothness, and texture should be considered based on the intended application of the part.
By understanding these considerations and incorporating them into the design process, you can improve the efficiency and cost-effectiveness of CNC machined part production. Next, we will explore how to simplify CNC machined part design by embracing design simplicity and involving the manufacturing team from the start.
When it comes to simplifying CNC machined part design, embracing design simplicity is a fundamental principle that can significantly impact the efficiency and cost-effectiveness of the manufacturing process. By keeping designs simple and minimizing unnecessary complexities, you can streamline production and reduce the likelihood of errors or complications. Here are key points to consider in embracing design simplicity:
1. Minimizing Complex Geometries
Simplifying the design by reducing intricate or convoluted geometries can lead to smoother machining processes and improved part quality. For instance, avoiding unnecessary undercuts or sharp internal corners can make the machining process more straightforward.
2. Using Standard Components and Off-the-Shelf Parts
Incorporating standard components and readily available off-the-shelf parts into your designs can simplify manufacturing processes. By utilizing standardized elements, you can leverage pre-existing specifications and reduce the need for custom fabrication, ultimately streamlining the CNC machining workflow.
3. Collaborating with Machinists and Manufacturing Engineers
Engaging with machinists and manufacturing engineers during the design phase can provide valuable insights into simplifying part geometries and optimizing manufacturability. Their expertise can guide you in making design choices that align with efficient machining practices.
Design simplicity not only enhances manufacturability but also contributes to overall cost reduction by minimizing material waste and machining time. By prioritizing simplicity in CNC machined part design, you pave the way for smoother production processes and improved outcomes.
Involving the manufacturing team from the beginning is another important aspect of streamlining the design of CNC machined parts, as it promotes collaboration between design and manufacturing disciplines. Then, by establishing clear lines of communication between designers, engineers and machinists early in the development process, potential manufacturability challenges can also be proactively identified and addressed.
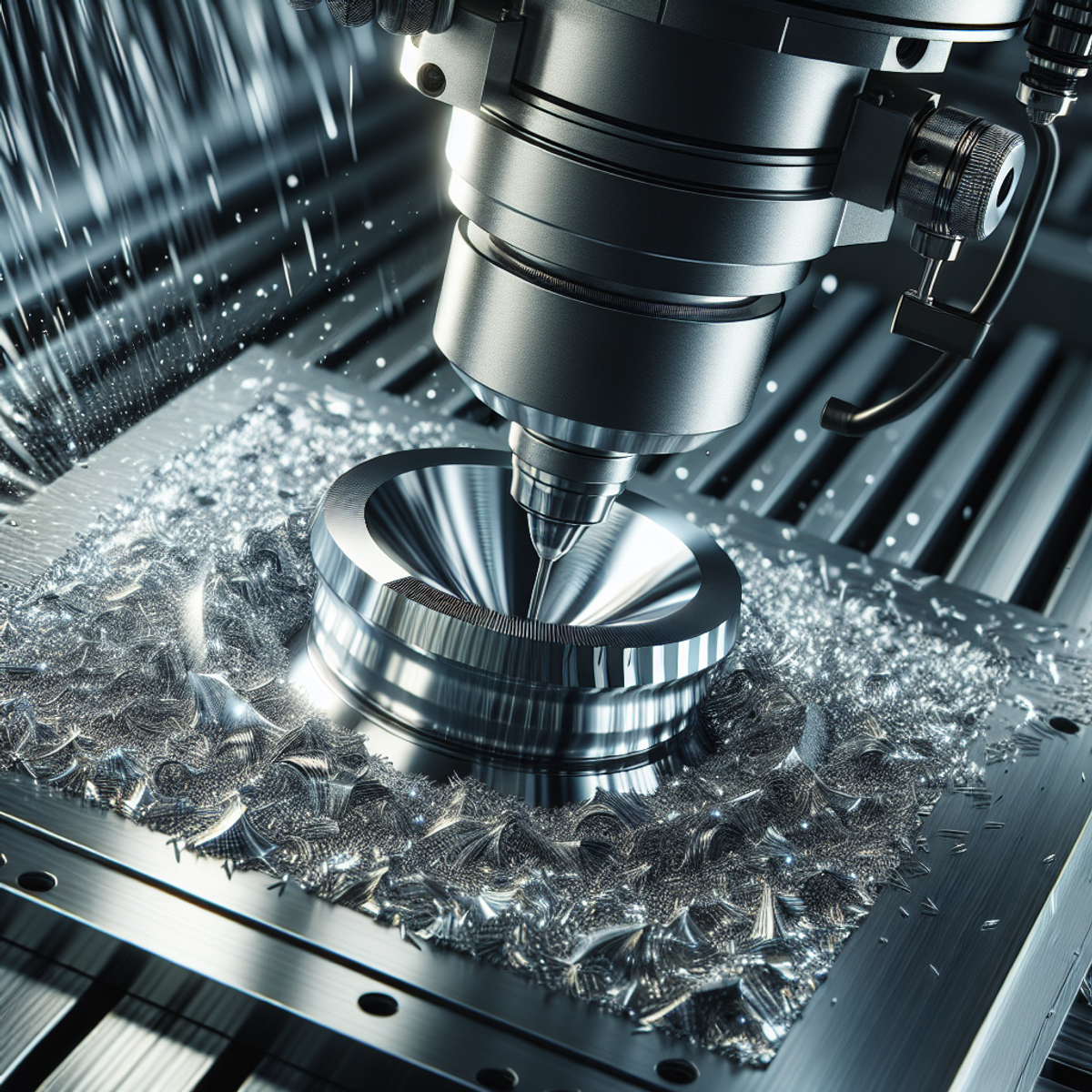
4. Involving the Manufacturing Team from the Start
Exploring strategies for simplifying CNC machined part design through the use of standard components and leveraging the expertise of machinists and manufacturing engineers.
1. Early Involvement
Involving the manufacturing team at the beginning stages of part design can significantly contribute to streamlining the overall process. By collaborating with machinists and manufacturing engineers early on, potential complexities and challenges in production can be identified and addressed proactively.
2. Collaborative Design Approach
Adopting a collaborative approach where designers, engineers, and machinists work together can lead to more efficient designs. This ensures that all perspectives are considered, leading to designs that are not only easier to manufacture but also more cost-effective.
3. Leveraging Expertise
The knowledge and experience of the manufacturing team can provide valuable insights into optimizing designs for CNC machining. Their input can help in selecting standard components or off-the-shelf parts that simplify the manufacturing process while maintaining the required functionality.
By involving the manufacturing team from the start, designers can benefit from their expertise, leading to more streamlined and effective CNC machined part designs.
4. Leveraging Standardization Opportunities
Designing CNC machined parts can be complex, but you can make it easier by taking advantage of standardization opportunities. This not only simplifies the design process but also makes production more efficient. Here’s how you can leverage standardization opportunities in CNC machined part design:
- Standard Components: Using off-the-shelf parts like screws, bolts, nuts, and bearings can greatly simplify manufacturing. These standard components are readily available in various sizes and materials, saving you time and money compared to custom-made parts.
- Design Libraries: Many CAD software packages offer libraries of pre-designed parts that you can easily incorporate into your own design. These libraries include commonly used features such as fasteners, brackets, and connectors. By using these pre-designed parts, you can speed up the design process and ensure compatibility with existing manufacturing methods.
- Expertise of Machinists and Manufacturing Engineers: Getting input from machinists and manufacturing engineers early on can be invaluable. They have specialized knowledge about industry best practices and can provide recommendations for simplifying your design. By involving them from the beginning, you’ll be able to identify opportunities for standardization and optimization.
By leveraging these standardization opportunities, you’ll be able to simplify the production process and achieve better results in your CNC machining projects. Remember to keep things simple, involve the manufacturing team from the start, and make use of existing resources like standard components and design libraries.
Apply the strategies and principles discussed to simplify your own CNC machined part designs and achieve better outcomes.
Partner with a reliable CNC machining service provider that offers a wide range of capabilities, such as cnc milling services, aluminum parts machining, and aerospace cnc machining, to support diverse manufacturing needs.