The Importance of Tighter CNC Machining Part Tolerances in Design and Production
In the manufacturing industry, precision is key. The ability to manufacture parts to tight tolerances is essential to ensure the quality and functionality of the final product. This is where Computer Numerical Control (CNC) machining comes into play. CNC machining is a process that uses computer-controlled machines to manufacture parts with a high degree of precision and accuracy.
As technology has advanced, tighter tolerances can now be achieved with CNC machining. But how will this affect design and production?
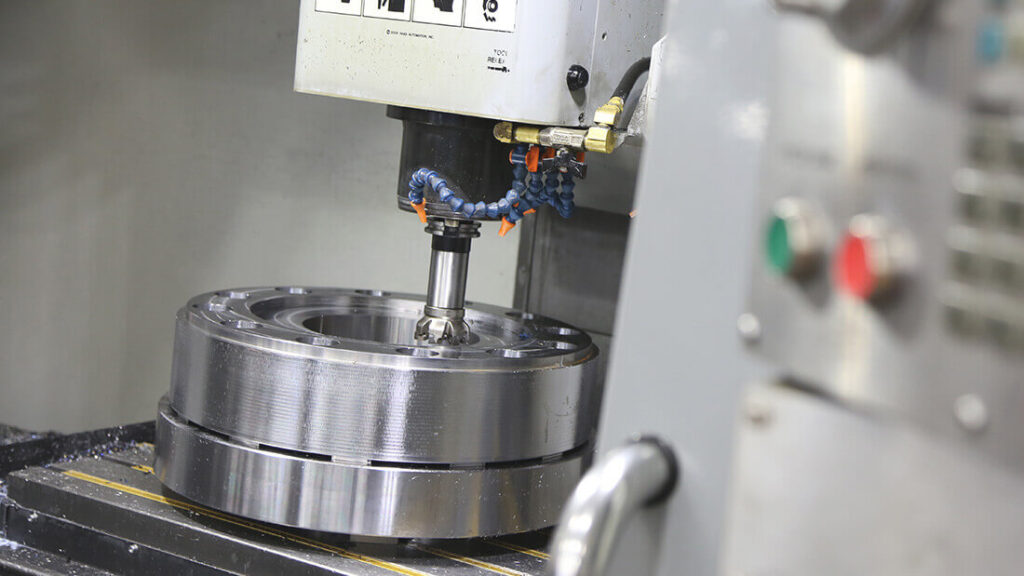
1.Benefits of Tight CNC Machining Part Tolerances
Tighter CNC machining part tolerances offer a number of benefits to design and production.
1) Greater Design Flexibility
Designers can now create more complex parts knowing that the CNC machine can accurately replicate their designs. This opens up a whole new world of possibilities for product design because designers are no longer limited by the capabilities of the manufacturing process.
2) Improved Product Performance
Because parts manufactured to tighter tolerances not only fit together more accurately, they also provide smoother operation and less wear. This is especially important in industries such as aerospace and automotive, where even the smallest deviations can have serious consequences.
At the same time, by ensuring that parts are manufactured to tight tolerances, manufacturers can also guarantee the reliability and longevity of their products.
3) Improved Production Efficiency
When parts are manufactured to tight tolerances, there is less need for manual adjustments and rework. This reduces the time and resources required for production, saving costs for manufacturers. In addition, tighter tolerances can also reduce the likelihood of errors and defects, further improving production efficiency.
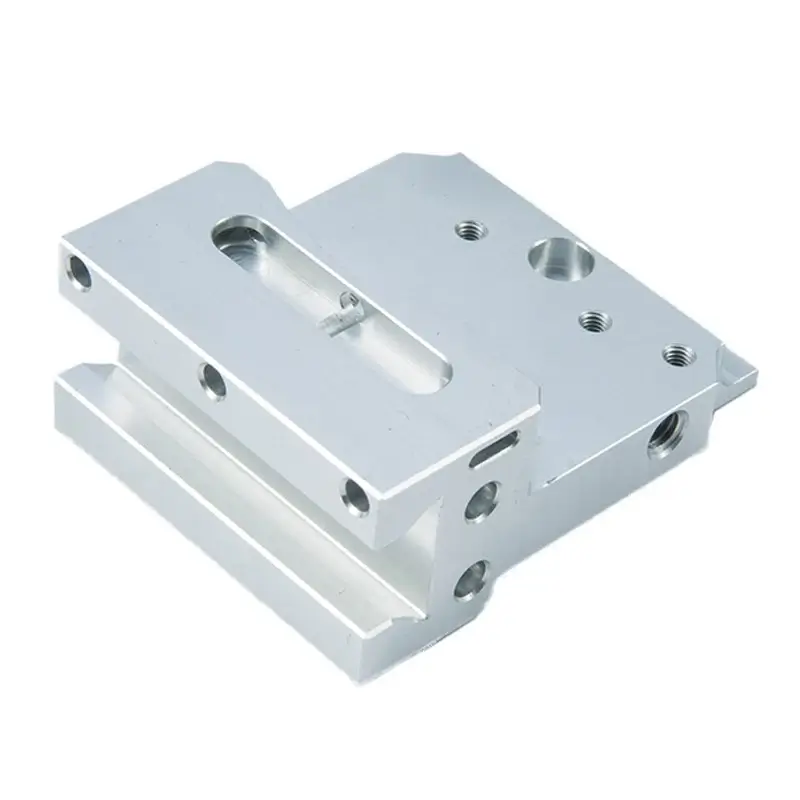
2.Challenges of Achieving Tighter CNC Machining Part Tolerances
Achieving tighter CNC machining part tolerances is not without challenges.
1) Increased Complexity of the Machining Process
Tighter tolerances require more precise control of CNC machines, which may require additional programming and setup time. Manufacturers need to invest in advanced CNC machines and skilled operators to ensure that tighter tolerances can be consistently achieved.
2) Increased Risk of Scrap and Rework
Even the smallest deviation from the specified tolerance can render the part unusable. Manufacturers need to implement strict quality control measures to ensure that all parts meet the required tolerances. This may involve additional inspection and testing processes, increasing overall production time and cost.
Despite these challenges, the advantages of tighter CNC machining part tolerances outweigh the disadvantages. Being able to manufacture parts with high precision and accuracy opens up new possibilities for design and improves product performance. In addition, increased production efficiency and reduced potential for errors saves manufacturers money.
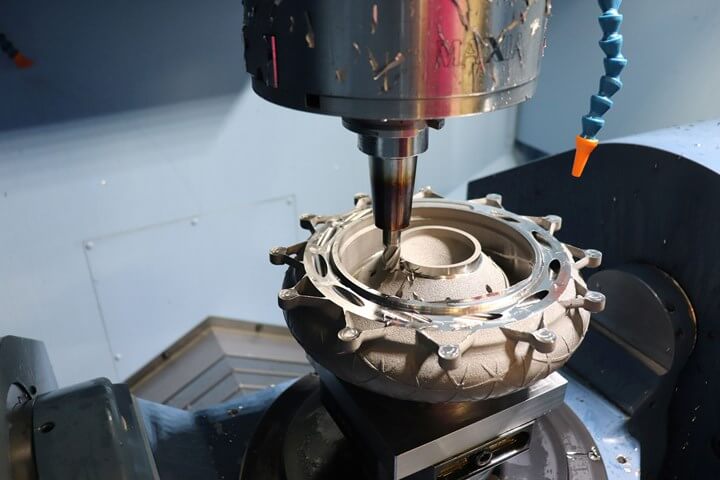
In summary, tighter CNC machining part tolerances have a significant impact on design and production. They provide greater design flexibility, improved product performance, and greater production efficiency.
However, achieving tighter tolerances requires investment in advanced CNC machines and skilled operators, as well as strict quality control measures. Despite the challenges, the benefits of tighter CNC machining part tolerances make it a worthwhile endeavor for manufacturers.