Composition of hydraulic valve components and its manufacturing process
As a key component in the hydraulic system, the performance and reliability of the hydraulic valve directly affect the operation effect of the entire hydraulic system. The composition and manufacturing process of the hydraulic valve components are important factors that determine its performance. This article will introduce the composition and manufacturing process of the hydraulic valve components in detail.
1.Composition of hydraulic valve components
Its basic structure mainly includes the following parts:
(1) Valve body:
The valve body is the core component of the hydraulic valve. It not only serves as a carrier for other components, but also constitutes a channel for oil circuit connection. The valve body is usually made of high-strength materials such as aluminum, forgeable cast iron or forged steel, and is distributed with mounting holes, oil holes, screw holes, positioning pin holes, etc. The design of the valve body needs to ensure that the internal oil channel is clear and concise to reduce the pressure loss when the oil flows.
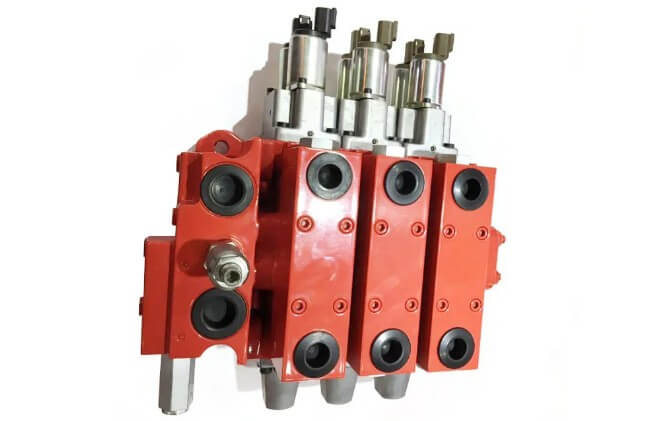
(2) Valve core:
The valve core is a key component in the hydraulic valve to realize the control function. According to different control requirements, the valve core can be in various forms, such as sliding valve, cone valve and ball valve. The valve core changes the flow direction, pressure and flow rate of the oil by relative movement in the valve body.
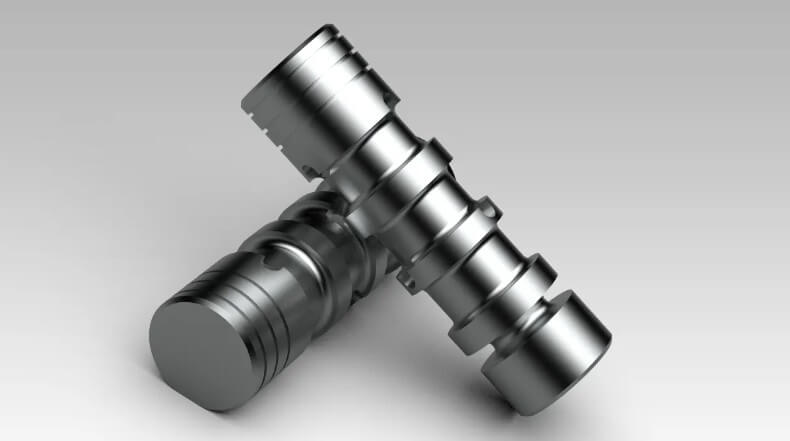
(3) Driving device:
The driving device is used to drive the valve core to make relative movement in the valve body. Common driving methods include manual adjustment mechanism, spring, electromagnet and hydraulic pressure drive. The design of the driving device needs to ensure sensitive action, reliable use, and small impact and vibration during operation.
(4) Sealing element:
The sealing element is used to ensure that the hydraulic valve does not leak during operation. Common sealing elements include O-rings, oil circuit sealing rings, etc. These sealing elements are usually made of materials such as oil-resistant rubber and have good sealing performance and durability.
(5) Pipe fittings and accessories:
Pipe fittings are used to connect the hydraulic valve to the external pipeline to achieve the circulation of oil. Accessories include pipeline connection flanges, process hole plugs, etc. The design and manufacture of these components need to ensure a firm connection and reliable sealing.
2.Manufacturing process of hydraulic valve parts
The manufacturing process of hydraulic valve parts is complex and involves multiple processing technologies. The following is an introduction to the manufacturing process of the main components:
(1) Valve body manufacturing process:
1) Material selection:
The selection of valve body materials is crucial. Commonly used materials include aluminum, malleable cast iron and forged steel. Aluminum is light in weight and has good thermal conductivity, and is suitable for low-pressure applications; malleable cast iron has good casting and mechanical properties, and is suitable for medium-pressure applications; forged steel has high strength and good wear resistance, and is suitable for high-pressure applications.
2) Casting or forging:
For aluminum and malleable cast iron, casting is usually used to produce blanks. Casting processes include sand casting, precision casting, etc. For forged steel, forging is usually used to produce blanks. Forging can improve the mechanical properties of the material and make it more durable.
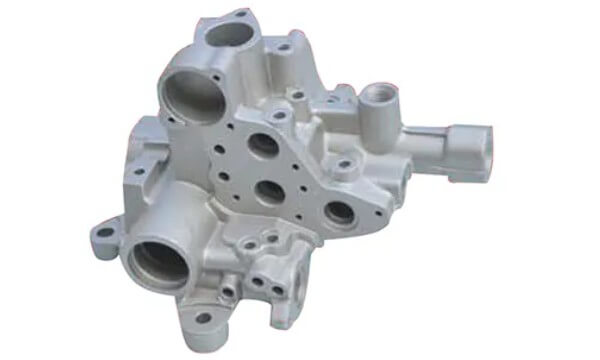
3) Machining:
The blank after casting or forging needs to be machined to achieve the size and shape required by the design. Machining includes turning, milling, drilling, tapping and other processes. During the machining process, the accuracy and surface roughness need to be strictly controlled to ensure that the internal oil passage of the valve body is unobstructed.
4) Heat treatment:
For some high-strength materials, such as forged steel, heat treatment is required after processing to improve its hardness and wear resistance. Heat treatment processes include quenching and tempering.
(2) Valve core manufacturing process:
1) Material selection:
Valve core materials are usually made of high-strength and wear-resistant metal materials, such as stainless steel and alloy steel.
2) Machining:
The machining accuracy of the valve core is relatively high, and it is usually processed by CNC machine tools. During the machining process, the dimensional accuracy and surface roughness need to be strictly controlled to ensure the matching accuracy between the valve core and the valve body.
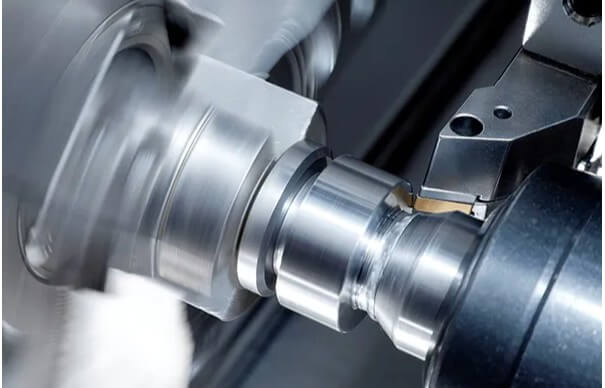
3) Heat treatment:
The processed valve core needs to be heat treated to improve its hardness and wear resistance. Heat treatment processes include quenching and tempering.
4) Surface treatment:
In order to improve the wear resistance and corrosion resistance of the valve core, the valve core is usually surface treated, such as chrome plating, nitriding, etc.
(3) Manufacturing process of drive device:
1) Electromagnet manufacturing:
Electromagnet is one of the commonly used drive devices in hydraulic valves. Its manufacturing process includes coil winding, core processing, assembly, etc. Coil winding requires strict control of wire diameter, number of turns and insulation performance; core processing needs to ensure dimensional accuracy and surface roughness.
2) Spring manufacturing:
Spring is another commonly used drive device in hydraulic valves. Its manufacturing process includes material selection, winding, heat treatment, etc. Material selection needs to consider the strength, elasticity and fatigue life of the spring; winding needs to ensure that the number of turns and diameter of the spring meet the design requirements; heat treatment can improve the hardness and elasticity of the spring.
(4) Sealing element manufacturing process:
1) Material selection:
Sealing element materials are usually selected from oil-resistant rubber, polyurethane and other materials.
2) Mold manufacturing:
The production of sealing elements usually adopts mold molding process. The design and manufacture of the mold need to ensure dimensional accuracy and surface roughness.
3) Molding process:
Molding process includes injection molding, vulcanization, etc. Injection molding is suitable for thermoplastic materials, and vulcanization is suitable for thermosetting materials. Parameters such as temperature, pressure and time need to be strictly controlled during the molding process to ensure the dimensional accuracy and performance of the sealing components.
(5) Manufacturing process of pipe fittings and accessories:
1) Material selection:
Pipe fittings and accessories are usually made of stainless steel, copper and other materials.
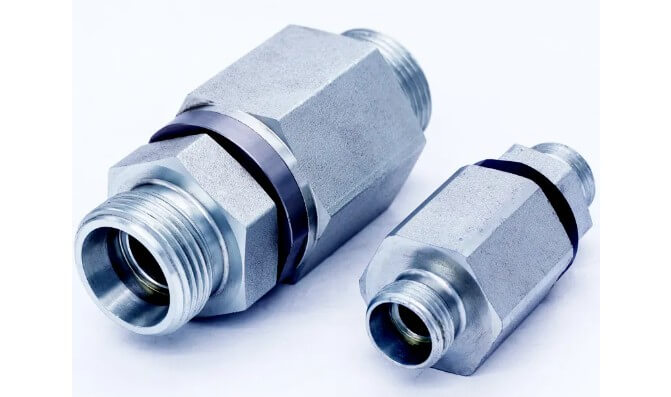
2) Machining:
The processing of pipe fittings and accessories needs to ensure dimensional accuracy and surface roughness. Turning, milling, drilling and other processes are usually used during the processing.
3) Surface treatment:
In order to improve the corrosion resistance of pipe fittings and accessories, they are usually surface treated, such as nickel plating, chrome plating, etc.
3.CNC machining skills and machining accuracy control of hydraulic valve parts
The CNC machining skills and precision control of hydraulic valve parts are crucial links in the manufacturing industry. The following are the relevant points:
(1) CNC machining skills
1) Reasonable selection of tools:
Select appropriate tools according to the material of hydraulic valve parts, such as high-speed steel tools, carbide tools, etc., to ensure machining efficiency and surface quality.
2) Optimize the processing program:
Use advanced CAM software for programming, reasonably plan the processing path, reduce idle stroke, and improve processing efficiency.
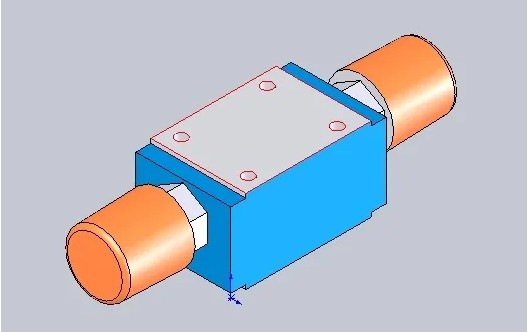
3) Control cutting parameters:
Reasonably select cutting speed, feed rate and cutting depth to reduce cutting force and cutting heat and ensure processing accuracy.
4) Adopt cooling and lubrication measures:
Use appropriate cooling lubricant to reduce cutting temperature, reduce tool wear and improve surface quality.
(2) Processing accuracy control
1) Machine tool accuracy assurance:
Use high-precision CNC machine tools, and regularly inspect and maintain the geometric accuracy, motion accuracy and positioning accuracy of machine tools.
2) Fixture and positioning accuracy:
Design and manufacture high-precision special fixtures to ensure the positioning accuracy of parts during the processing process.
3) Inspection and feedback:
Use high-precision inspection equipment to inspect the processed parts, feedback the inspection results to the processing process, and adjust the processing parameters in time to ensure processing accuracy.
4) Processing accuracy range:
Under normal circumstances, the CNC processing accuracy of hydraulic valve parts can be controlled between ±0.005mm and ±0.01mm. The specific accuracy depends on factors such as machine tool performance, processing technology and detection methods.
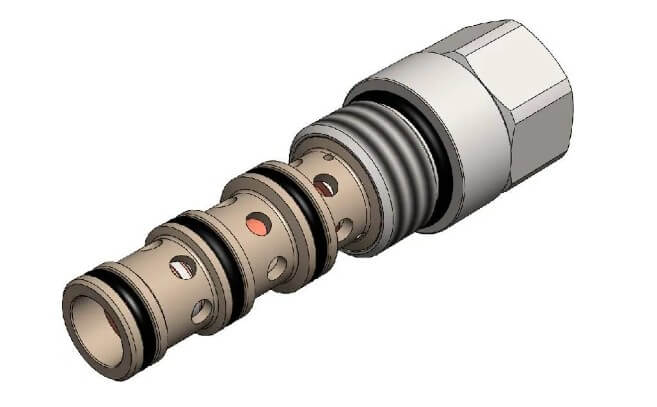
4.Application fields of hydraulic valves
As a key control component, it is widely used in many industries. The following are its main application fields:
(1) Manufacturing industry:
In various mechanical manufacturing processes, it is used to control the hydraulic systems of machine tools, presses and other heavy equipment to achieve precise pressure and flow control.
(2) Automobile industry:
Hydraulic valves are used in power steering systems, suspension systems and braking systems in automobile manufacturing to help improve controllability and safety.
(3) Aerospace:
Hydraulic valves are widely used in landing gear, flight control systems and door control systems of aircraft and spacecraft due to their high reliability and precise control.
(4) Energy industry:
It plays an important role in the turbine control systems of oil and gas extraction equipment and power stations, helping to achieve smooth operation and efficient control of the system.
(5) Construction Engineering:
It is used in construction machinery such as excavators and cranes to control their hydraulic arms and drive systems to complete various complex construction tasks.
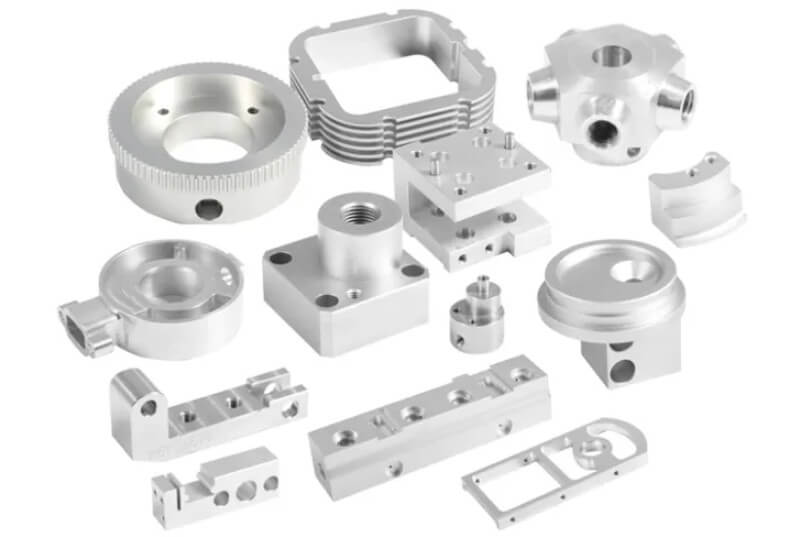
(6) Shipbuilding Industry:
In the ship’s steering system, anchor system and crane system, it is used to control the flow of liquid to ensure the accuracy and stability of ship operations.
(7) Metallurgical Industry:
Hydraulic valves are used in metallurgical equipment to control metal processing processes under high temperature and high pressure environments to ensure production efficiency and safety.
5.Summary
In summary, the components and manufacturing process of hydraulic valves is a complex and systematic process. The manufacturing of each component requires strict process control and quality inspection to ensure the performance and reliability of the final product.