Key Manufacturing Technologies for Implantes Dentales: Metal Processing Technology and Surface Treatment Technology
In the field of modern dental restoration, implantes dentales are a vital component that plays an important role in supporting dentures and ensuring close integration with alveolar bone. A small dental implant may seem simple, but it actually contains a complex and sophisticated manufacturing process.
Among them, metal processing technology and surface treatment technology are crucial and directly affect the performance, lifespan of the implant and the overall oral health of the patient. Therefore, this article will focus on these two important technologies.
Implantes dentales are usually made of metals with good biocompatibility, high strength and corrosion resistance, such as pure titanium or titanium alloys. The first step in metal processing is the selection and inspection of raw materials to ensure that their purity and impurity levels meet medical grade standards.
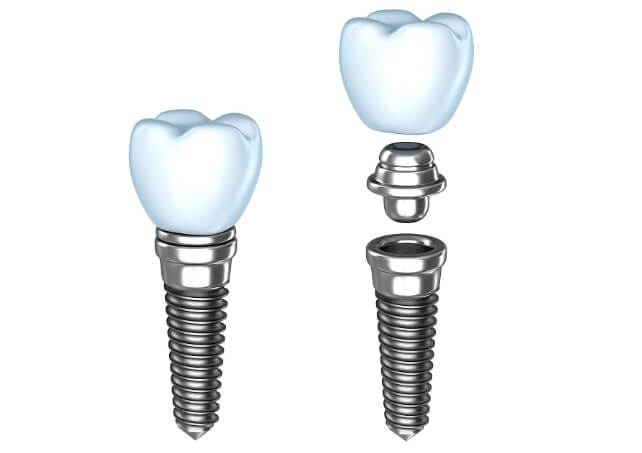
1.Metal processing technology for implantes dentales
(1) Cutting and forming
Starting from a metal rod or sheet, use precision cutting equipment to cut the raw material into the appropriate size and shape according to the design specifications.
1) Laser cutting technology:
Laser cutting is one of the commonly used cutting technologies in dental implant manufacturing. Its advantages are high precision, fast cutting speed and small heat-affected zone. Laser cutting can accurately cut raw materials into the required shape and size, reducing material waste. In addition, the laser cutting process generates less heat, which can effectively avoid material deformation and ensure the geometric accuracy of the implant.
2) Electrospark cutting technology:
Electrospark cutting technology is suitable for processing high-hardness and high-toughness materials such as titanium alloys. Through the action of electric spark discharge, the material can be accurately removed. This technology performs well in the processing of complex shapes of implantes dentales and can meet the needs of personalized customization of implants.
3) Cold forging and stamping technology
Then, cold forging, stamping and other processes are used to shape the cut material into the basic shape of the dental implant. Cold forging enhances the strength and hardness of the metal without changing the metal crystal structure, so that the implant exhibits excellent mechanical properties and can withstand complex forces such as chewing in the oral environment.
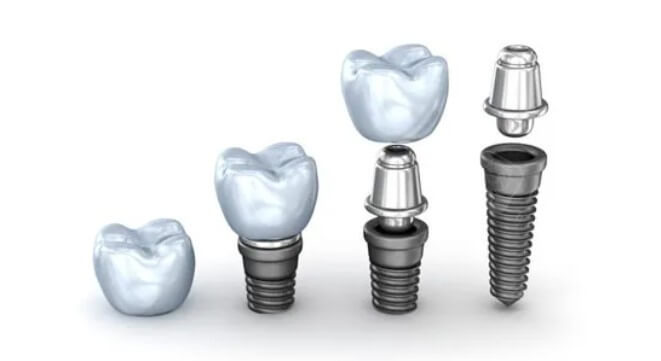
(2) Precision machining
1) Turning:
Turning is one of the basic processes in the manufacture of implantes dentales. Through high-precision CNC lathes, the cylindrical part of the implant can be efficiently processed to ensure that its diameter and surface roughness meet the design requirements. Advanced turning technology can also process specific texture structures on the surface of implants to promote bone integration.
2) Milling:
Milling plays an important role in the processing of complex structures of implantes dentales. Using a five-axis CNC milling machine, the head, neck and other parts of the implant can be processed with high precision to achieve precise molding of complex curved surfaces. The implant structure processed by milling is more in line with the anatomical characteristics of the human body and improves the success rate of implantation.
3) Drilling:
Drilling operations are also essential. Through holes are usually required inside the implant to install fixing screws or connect other components. The use of high-precision CNC drilling technology can ensure the accuracy of hole positioning, diameter and verticality, thereby preventing deviations from adversely affecting the overall performance of the implant.
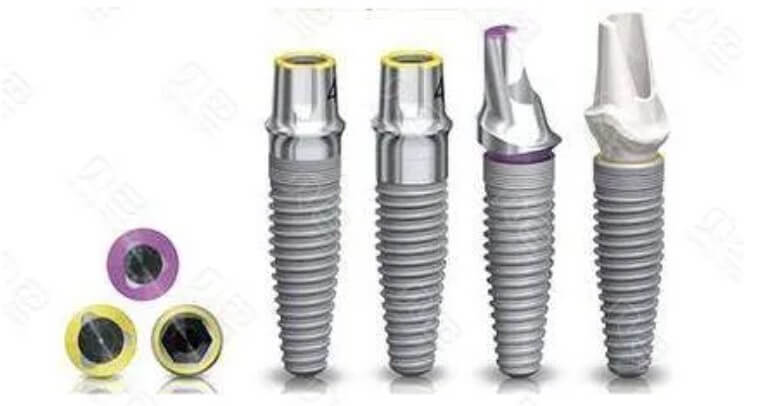
(3) Thread processing
The thread is one of the important parts of the implant because it not only facilitates the connection with the prosthetic components, but also affects the combination of the implant and bone tissue to a certain extent.
1) Thread cutting technology:
Thread cutting is an important link in the manufacturing of implantes dentales. Although the traditional thread cutting method can meet certain precision requirements, it has the problem of low efficiency. Modern CNC thread cutting technology can complete thread processing efficiently and with high quality through high-speed rotating tools and precise feed control.
2) Thread rolling technology:
Thread rolling technology is a method of forming threads on the surface of a material by rolling tools. This technology can not only improve the strength and wear resistance of the thread, but also reduce the deformation and stress concentration of the material. In the manufacture of implantes dentales, thread rolling technology is widely used to improve the connection strength and stability of the implant.
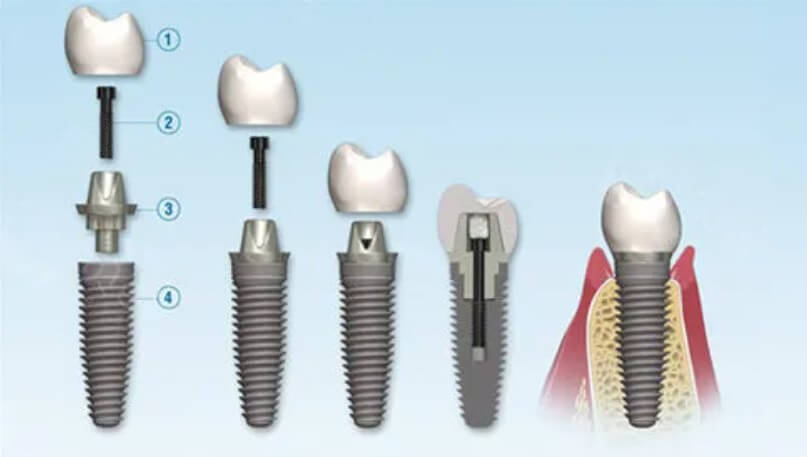
2.Surface treatment technology of implantes dentales
After metal processing, the implant blank needs to be carefully designed with surface treatment technology to further optimize its performance and make it better adapt to the complex and changing environment of the oral cavity.
(1) Sandblasting and acid etching
Sandblasting and acid etching technology is a widely used method in implant surface treatment. This technology first uses high-pressure airflow to impact large particles such as corundum particles on the implant surface at high speed to form a microscopic rough structure. Subsequently, the implant is placed in a mixture of high-temperature hydrochloric acid and sulfuric acid for acid etching to further increase the multi-dimensional structure of the surface.
This dual treatment method significantly improves the roughness of the implant surface and increases the contact area of the bone interface, thereby enhancing the implant’s anti-torque ability and facilitating the attachment and bone integration of osteoblasts.
(2) Plasma spraying
Plasma spraying technology is to heat powder materials such as titanium and hydroxyapatite to a molten or semi-molten state, and then spray them onto the implant surface at high speed to form a uniform, rough and biocompatible coating.
The titanium coating enhances the corrosion resistance and wear resistance of the implant, while the hydroxyapatite coating, due to its similar composition to human bone tissue, can form a direct chemical bond with the surrounding bone tissue, fundamentally increasing the strength of bone integration, accelerating the growth and repair of bone tissue around the implant, and reducing the occurrence of surrounding inflammatory reactions.
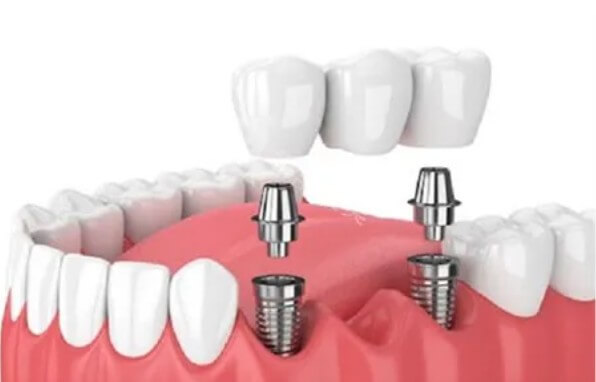
(3) Hydrophilic treatment
Making the implant surface hydrophilic is an important breakthrough in recent years. Through special chemical or physical treatment methods, such as plasma treatment or surfactant modification, the implant surface can quickly absorb water and biological molecules such as proteins in the oral environment to form a stable biofilm.
This biofilm promotes cell adhesion, proliferation and differentiation, thereby promoting rapid healing between the implant and the surrounding tissue, allowing patients to adapt faster after implantation, and improving the success rate of implantes dentales.
(4) Anodizing
Anodizing technology is an electrochemical treatment method that uses an implant as an anode to place it in an electrolyte and use electrochemical reactions to form a thicker titanium oxide layer on the implant surface. This oxide layer not only improves the surface hardness and wear resistance of the implant, but also adjusts the surface roughness and chemical composition, improving its biocompatibility and bone integration performance.
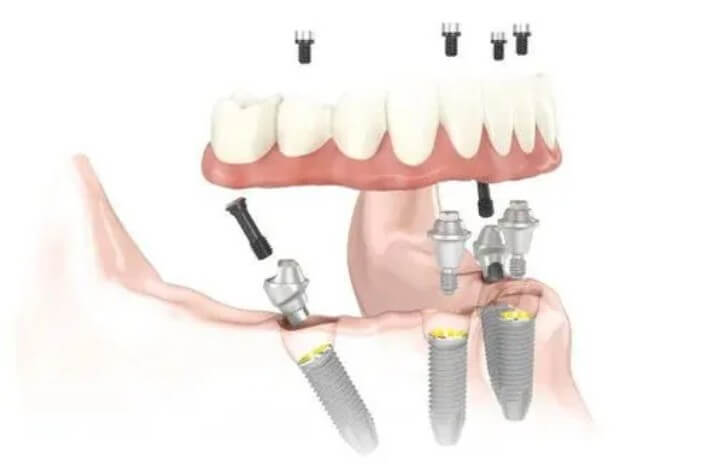
By controlling the parameters of the anodizing process, such as voltage, current density and duration, titanium oxide layers of different thicknesses, roughness and chemical properties can be obtained to meet the specific oral conditions and clinical needs of different patients.
3.Future development trends of implantes dentales
(1) Personalized customization
With the development of digital technology, personalized customization of implantes dentales will become a future development trend. Through the patient’s CT data, additive manufacturing technology can be used to customize implants that fully match the patient’s anatomical structure, improving the success rate of implantation and patient comfort.
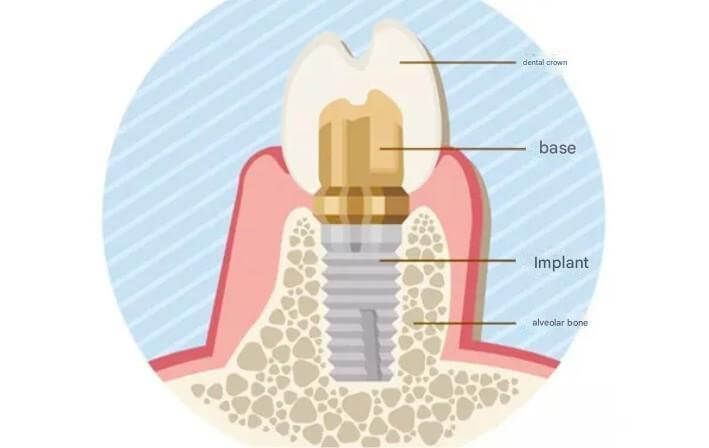
(2) Multifunctional surface treatment technology
In the future, the surface treatment technology of implantes dentales will develop in a multifunctional direction. For example, multiple technologies such as sandblasting, acid etching, and anodizing can be combined to form a composite surface structure with multiple functions. In addition, bioactive factors, drugs, etc. can be introduced on the surface of the implant to further improve the biocompatibility and therapeutic effect of the implant.
(3) Application of new materials
In addition to traditional titanium alloy materials, more new materials with excellent performance will be developed in the future for the manufacture of implantes dentales. For example, magnesium alloys, zirconium alloys and other materials have better biocompatibility and mechanical properties, and are expected to become ideal materials for implantes dentales.
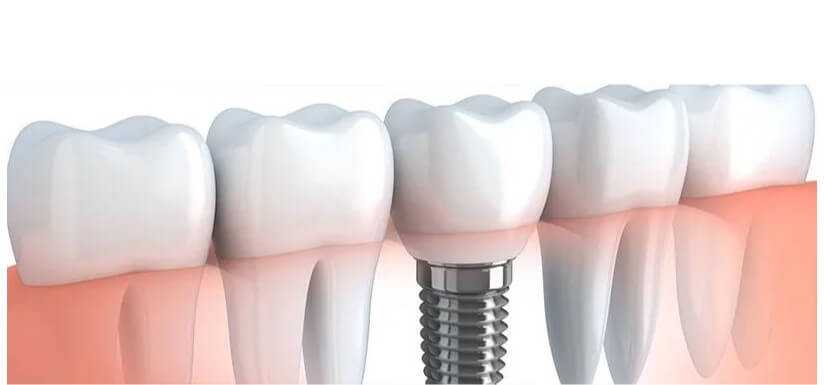
(4) Intelligent manufacturing
Intelligent manufacturing technology will play an increasingly important role in the manufacture of implantes dentales. Through technologies such as the Internet of Things and big data, intelligent monitoring and management of the implant manufacturing process can be achieved, improving production efficiency and product quality.
4.Summary
In the manufacturing process of implantes dentales, metal processing technology and surface treatment technology complement each other. Metal processing provides implants with precise shapes and solid structures, while surface treatment gives them excellent performance suitable for the human environment.
From the selection of raw materials to the final inspection of finished products, each link requires strict quality control. Negligence in any link may lead to poor quality of implantes dentales and affect the patient’s dental implant experience. With the continuous advancement of science and technology, dental implant manufacturing technology will continue to innovate, bringing more efficient and higher-quality solutions to the field of dental restoration, allowing more patients to regain a healthy and confident smile.