Importance of Titanium Anodizing
Titanium anodizing is an important technology in modern industry. It is an advanced process that can significantly change the surface properties of titanium and its alloys. Whether you are pursuing material performance improvement or product appearance optimization, an in-depth understanding of titanium anodization is crucial.
1.What is titanium anodizing?
Titanium anodizing is an electrochemical process used to change the surface properties of titanium and its alloys. In this process, titanium is placed in an electrolyte solution and connected to a power source. After power is applied, the current triggers an oxidation reaction, forming a protective oxide layer on the titanium surface. This oxide layer can not only effectively improve the wear resistance and corrosion resistance of the material, but also can achieve coloring of the oxide layer through precise adjustment of the voltage during the anodizing process, bringing more diverse appearance effects to the titanium material.
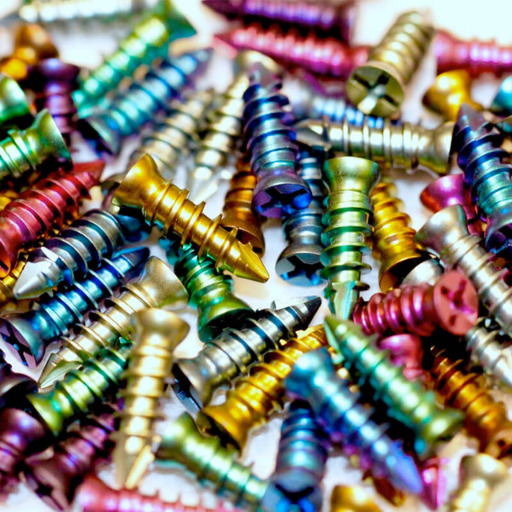
2.Types of titanium anodizing
(I) Type I: Chromic acid anodizing
This type of anodizing uses a chromic acid solution. The titanium parts are placed in the solution and then energized to form an oxide layer on the surface.
Oxide layer thickness: The oxide layer formed is usually thin, ranging from 0.1 to 2 microns.
Color rendering: It is generally dark gray, and the color selection is relatively limited.
Application areas: Due to its excellent corrosion resistance and good adhesion to paints and coatings, it is mainly used in the aerospace field.
(II) Type II: Sulfuric acid anodizing
Type II anodizing uses sulfuric acid as the electrolyte. The oxide layer is formed under the action of electricity.
Oxide layer thickness: A relatively thick oxide layer can be produced, with a thickness of up to 25 microns.
Color range: Depending on the applied voltage, a variety of colors can be presented, including blue, purple, and gold.
Application areas: Commonly used in aerospace, medical equipment, and consumer products, as these fields have high requirements for product protection and aesthetics.
(III) Type III: Hard Anodizing
Type III anodizing (hard anodizing) uses higher voltages and a specific sulfuric acid solution to form a thick and durable oxide layer.
Oxide layer thickness: It can produce significantly thicker oxide layers, up to 100 microns thick.
Durability: The tough surface formed greatly enhances wear and corrosion resistance.
Applications: Ideal for applications such as military, aerospace and heavy industry where durability is extremely important.
(IV) Type IV: Color Anodizing
The fourth type of anodizing can use a variety of electrolyte solutions, mainly sulfuric acid. This method focuses on achieving bright and rich colors through precise control of the anodizing process.
Oxide layer thickness: The oxide layer thickness produced is generally thinner, similar to Type II.
Color range: A wide range of color options are available for customized finishes.
Applications: Commonly used in consumer products such as jewelry and decorative items, where beauty and functionality are equally important.
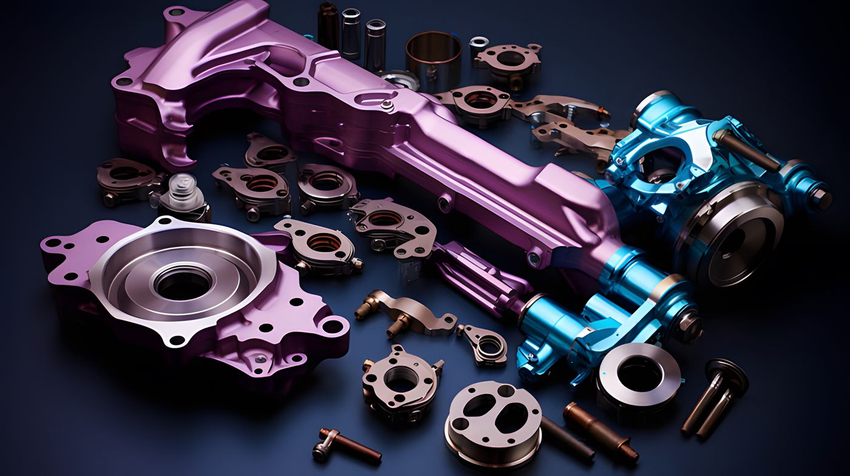
3.Operation steps of titanium anodizing
The titanium anodizing process mainly involves the following steps:
(I) Surface preparation
First, the titanium surface must be thoroughly cleaned to remove oil and other contaminants to ensure that the surface is clean and create good conditions for the subsequent anodizing process.
(II) Equipment setup
Place the titanium workpiece in an electrolyte solution, usually sulfuric acid as the electrolyte. This step provides the necessary chemical environment for the oxidation reaction to occur.
(III) Circuit connection
Connect the titanium workpiece to the positive pole (anode) of the power supply, and connect the cathode to the negative pole of the power supply to establish an electrochemical circuit to provide electrical energy for the oxidation reaction.
(IV) Voltage application
The desired oxide layer thickness and color effect are achieved by adjusting the voltage. This step requires precise control of the voltage parameters to ensure that the oxidation effect meets the requirements.
(V) Rinse and dry
After the anodizing is completed, rinse the titanium workpiece with distilled water to remove residual electrolyte and other substances on the surface, and then dry thoroughly.
(VI) Oxide layer sealing (optional)
If needed, the anodized layer can be sealed, which helps to further improve the durability of the oxide layer.
4.Materials required for titanium anodizing
The following materials are usually required for anodizing titanium:
(i) Titanium workpiece
This is the core object that needs to be anodized, that is, the object to be treated.
(ii) Electrolyte
Generally, a suitable chemical solution such as sulfuric acid or phosphoric acid is used as the medium for the anodizing reaction.
(iii) Power supply
A direct current (DC) power supply is required to provide the necessary voltage for the anodizing process to drive the oxidation reaction.
(iv) Hardness tester
Used to measure the hardness of the anodized layer in order to evaluate the oxidation effect.
(v) Distilled water
Used to rinse the titanium workpiece after the anodizing process to ensure the cleanliness of the workpiece surface.
(vi) Safety equipment
Including gloves, goggles and protective clothing, etc., to ensure the safety of operators during the entire anodizing process and prevent chemical contact and other potential safety hazards.
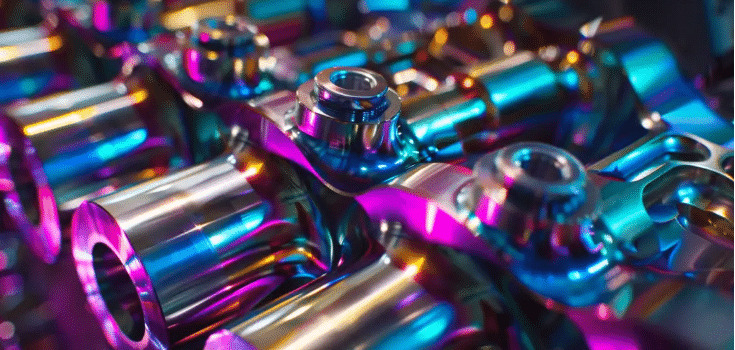
5.Titanium Anodizing Chart
The following is a simple titanium anodizing color chart showing the typical colors produced at different anodizing voltages:
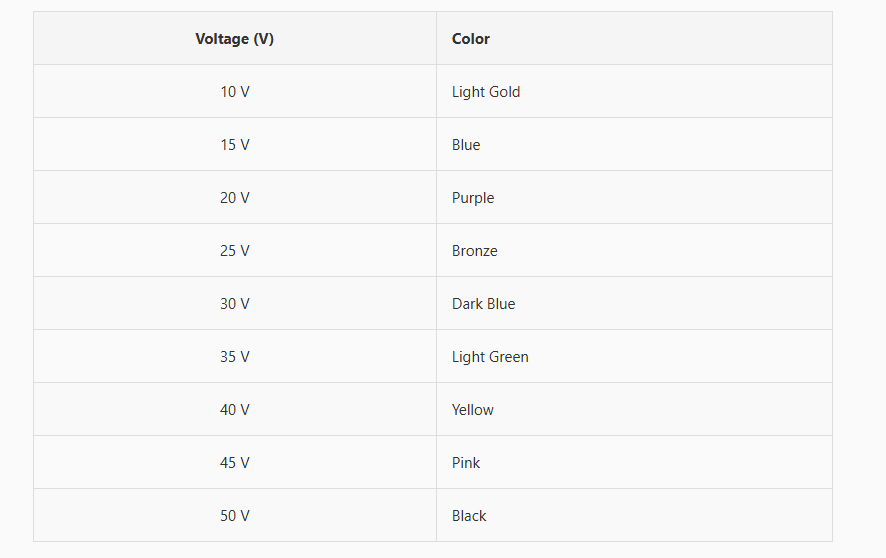
6.Application fields of titanium anodizing
(1) Aerospace field
In the aerospace industry, low weight and high corrosion resistance are key requirements for aircraft components. Anodized titanium meets these needs and is therefore widely used to manufacture such components to ensure the reliable operation of aerospace equipment in complex environments.
(2) Medical device industry
Implants and surgical instruments in medical devices place extremely high demands on the biocompatibility and durability of materials. Anodized titanium is favored for these excellent properties, providing a safe and reliable material choice for medical applications.
(3) Automobile industry
In high-performance vehicles, the use of anodized titanium parts not only enhances the functionality of the vehicle, but also improves its aesthetics, giving the vehicle a more attractive appearance while delivering high performance.
(4) Consumer goods field
Consumer products such as jewelry and watches are significantly enhanced in appearance and scratch resistance through titanium anodization, meeting consumers’ dual needs for beauty and durability.
7.Advantages of Titanium Anodizing
(1) Enhance corrosion resistance
The oxide layer formed by anodization can effectively protect the titanium material from erosion by external environmental factors, thereby significantly extending its service life, which is particularly critical in applications in various harsh environments.
(2) Enhance aesthetic appeal
Anodized titanium can present a variety of colors and surface treatments, with a strong visual impact. This not only meets the need for beautiful product design, but also makes the product more competitive in appearance.
(3) Improve durability
The formation of the oxide layer increases the hardness of the titanium material, making it more wear-resistant, reducing loss during use, and improving the quality and service life of the product.
(4) Good biocompatibility
Anodized titanium shows good biocompatibility in medical applications and can be safely used in medical devices such as human implants, effectively reducing the risk of the body rejecting the implants.
8.Limitations of titanium anodizing
(I) Cost factors
Because the anodizing process requires specific materials and equipment, the cost of the process is relatively high, which may limit its large-scale application to a certain extent.
(II) Oxide layer thickness limitation
There is a maximum thickness limit for the anodized layer, which means that for some application scenarios with special requirements for the thickness of the oxide layer, it may not be able to fully meet the needs.
(III) Color consistency problem
During the anodizing process, due to the changes in various factors, it is difficult to achieve uniform and consistent color, and different tones are prone to occur, affecting the consistency of the product appearance.
(IV) Alloy applicability issues
Not all titanium alloys can be anodized well, and some titanium alloys may have problems during the anodizing process, which limits their use in certain specific applications.
At last
Titanium anodizing is a valuable process that can significantly enhance the properties of titanium materials and broaden their range of applications, making it an ideal material choice in many fields.
If you’re looking for an experienced titanium anodizer, look no further than Xavier. The Xavier team is well-equipped to provide high-quality titanium anodizing solutions, feel free to contact us at any time.