Differences between Injection Molding and Compression Molding
This article will describe the similarities and differences between injection molding and compression molding to help you determine which process is best for your project in terms of manufacturing process, materials used, and production rates. Injection molding is a plastic manufacturing technology that is capable of extremely high production volumes. The process works by injecting liquid plastic into a mold at extremely high pressure. Compression molding, on the other hand, is better suited for medium-volume production and is often used for rubber and silicone.
Injection molding is better suited for making complex parts, while compression molding is better suited for making simple geometries and large panels. Injection molding is highly automated and does not require constant human supervision, while compression molding often requires human intervention to load the charge and remove the finished product. Compression molding also has lower tooling costs.
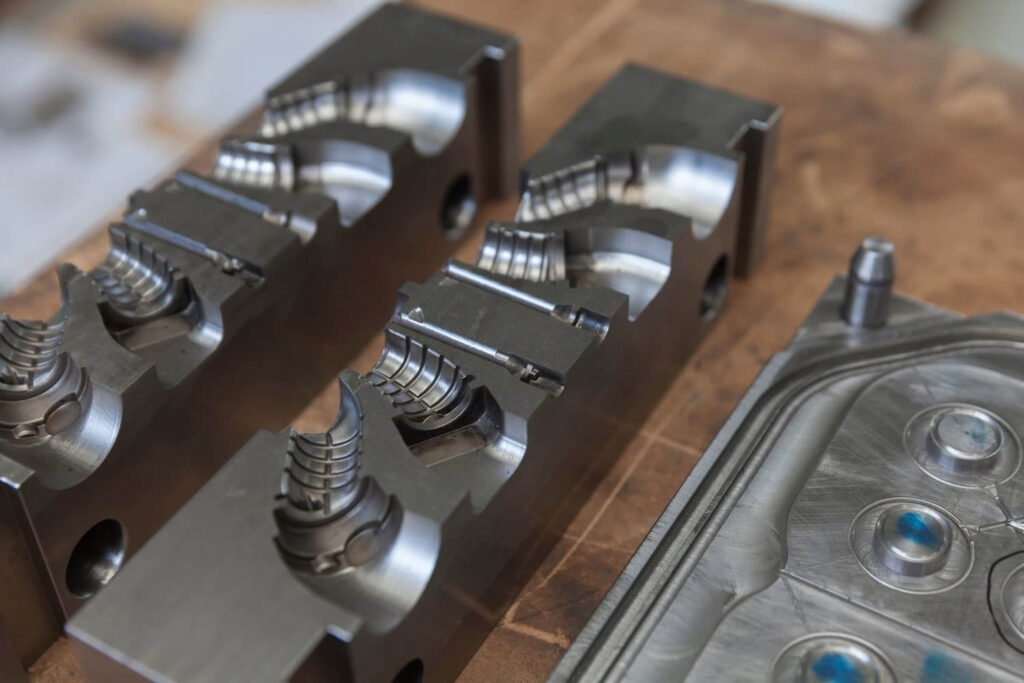
1.Injection Molding Definition and Comparison with Compression Molding
Injection molding works by injecting molten thermoplastic into a mold cavity. During the plastic injection process, plastic resin pellets are melted inside a barrel. Inside the barrel is a screw with a shaft that increases in diameter along its length. As the screw rotates, the plastic is forced to gradually become smaller. This compression is the primary mechanism for melting the plastic. The barrel is also heated to provide additional heat. Once enough plastic has melted to fill the mold, the screw retracts and is then pushed forward to press the plastic resin into the mold at very high pressure.
The mold consists of at least two parts that are held together by hydraulic cylinders so that the high-pressure plastic injected into the mold does not escape the parting line. The mold has cooling channels that cool the part sufficiently to eject it from the mold without damage. Injection molding can achieve high production volumes that are unmatched by any other plastic processing technology. Compression molding, on the other hand, is more suitable for medium-volume production.
1) Advantages of Injection Molding Compared to Compression Molding
Listed below are some of the advantages and disadvantages of injection molding compared to compression molding:
- Injection molding is a mass production method that can produce millions of parts per year per machine.
- Injection molded parts are cheaper than compression molded parts due to high automation and fast manufacturing speeds.
2) Disadvantages of Injection Molding Compared to Compression Molding
Listed below are some of the disadvantages of injection molding compared to compression molding:
- Injection molding requires very high plastic injection pressures. Therefore, the mold must be able to withstand these high pressures. This increases tooling costs.
- Injection molding is not well suited for making large, thin parts such as vehicle panels.
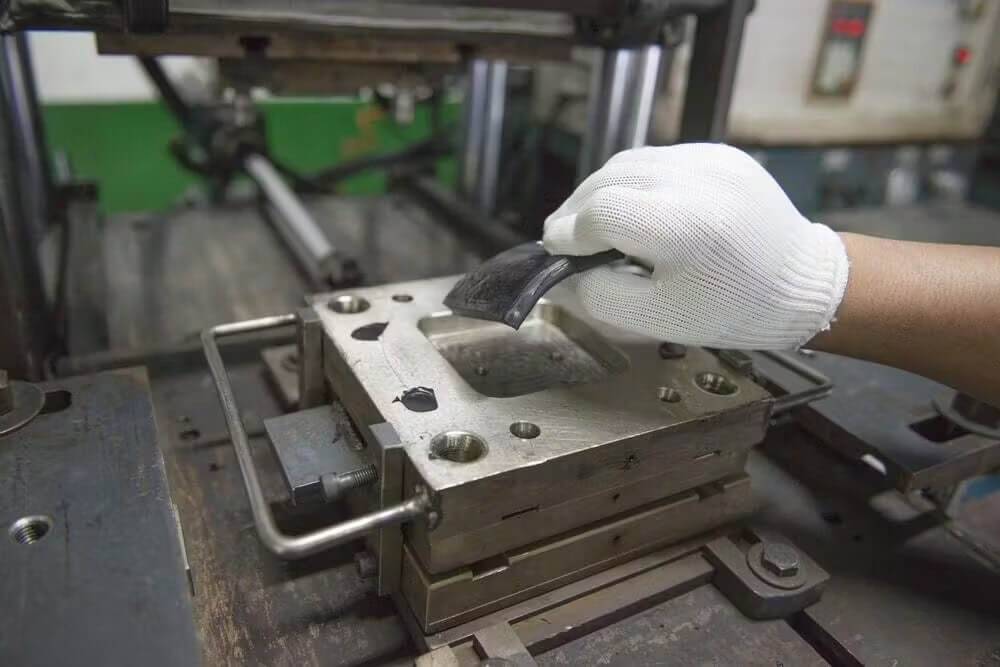
2.Compression Molding Definition and Comparison with Injection Molding
Compression molding is a process most commonly used to make parts made of flexible materials. This molding technique usually uses a two-part mold, one of which is fixed to the base of the compression molding tool, while the upper half is free to move up and down. The mold is usually heated to help solidify the final product while the charge is heated before compression. The accurately weighed charge is heated until it becomes pliable. It is then placed into the lower half of the mold.
The upper half then moves down, forcing the material to conform to the shape required by the mold. The heated mold remains closed while the material is allowed to solidify. This usually takes several minutes. Once solidified, the part is removed from the mold. Post-processing is required to cut off any flash. Flash (or excess material on the mold parting line) is a common phenomenon with compression molded parts.
Compression molding is used to make reinforced panels. The process involves laying down a fiber-filled plastic sheet in the lower half of the mold. The upper half of the mold then compresses and heats the material, forcing the plastic to run through the entire mold to form a composite part. Large plastic car bumpers are made this way.
1) Advantages of compression molding compared to injection molding
Listed below are some of the advantages of compression molding compared to injection molding:
- Compression molding can make composite panels out of SMC (sheet molding compound) and BMC (bulk molding compound). These panels do not have continuous fiber-impregnated sheets, but rather chopped fiber bundles distributed throughout the bulk material. Composite parts cannot be made with the injection molding method.
- Compression molds do not need to withstand high internal pressures like injection molds. Instead, the only load they withstand is the compressive force from above. This means that compression molds tend to be cheaper.
2) Disadvantages of compression molding compared to injection molding
Listed below are some of the disadvantages of compression molding compared to injection molding:
- Compression molding is a very manual and slow process. Even with robotic arms to add charge and remove product, the cycle time between parts is still much slower than injection molding due to the need to set up the parts before removal.
- Compression molding cannot produce plastic parts with a high degree of complexity. The materials used are usually very viscous and therefore do not flow well into small and complex parts.
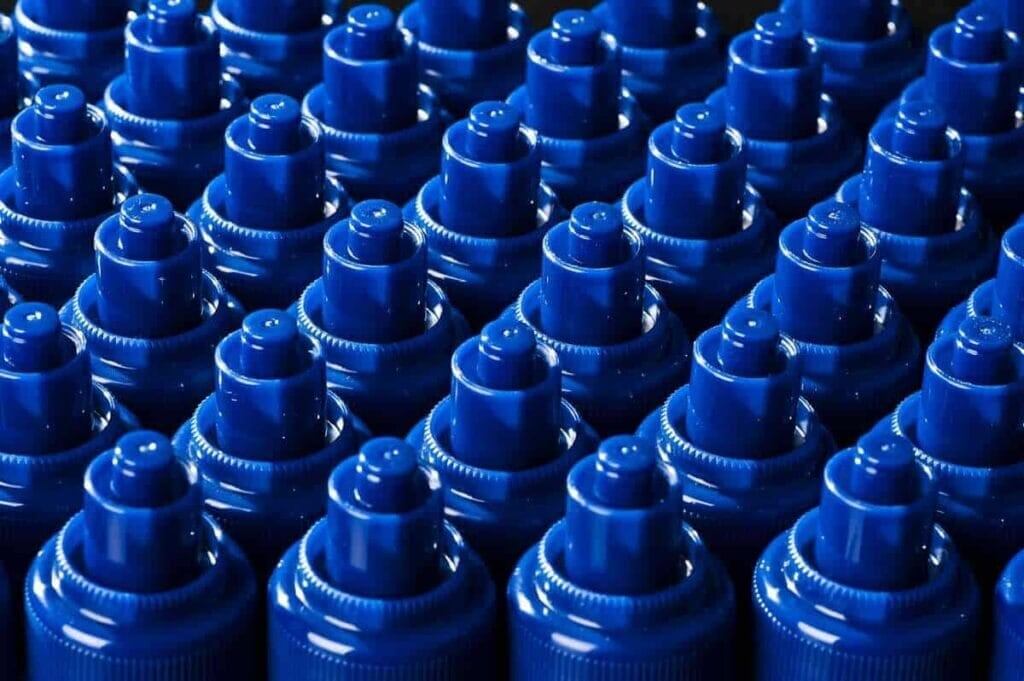
3.Injection Molding and Compression Molding Comparison Table
Injection molding is better suited for high-volume production, while compression molding is better suited for pliable, easily bendable materials. Compression molding also has lower tooling costs.
1) Injection Molding and Compression Molding: Lead Cost Comparison
Injection molding can produce complex parts at a low price in terms of the cost per part. However, this manufacturing process is cost-competitive only when production volumes are large enough to spread the high cost of injection molding tools over a sufficient number of parts. In the case of lower production volumes, compression molding is cheaper than injection molding due to lower initial tooling costs.
2) Injection Molding and Compression Molding: Speed Comparison
Injection molding is much faster than compression molding. The cycle time for an injection molded part may be only a few seconds, while the cycle time for compression molding can easily reach several minutes. This is because compression molded parts usually need to be cured through a heating process before they can be removed from the mold.
3) Injection Molding and Compression Molding: Volume Comparison
Injection molding is a high-volume production method that is unmatched by any other manufacturing technology. The injection molding process can be fully automated, while compression molding usually requires manual labor to place the raw materials into the mold, remove them, and perform post-processing.
4) Injection molding and compression molding: material comparison
Injection molding can use both hard thermoplastics and thermoplastic elastomers. Compression molding is more commonly used with flexible elastomers such as rubber and silicone, but can also produce hard composite parts using SMC and BMC.