Insert Molding Design Guide: A Detailed Guide
Insert molding is an efficient and economical manufacturing process that combines plastic injection molding with the embedding of metal or other components. The technology allows for the creation of complex and durable products by encapsulating the insert within the molded plastic part.
In this article, we will provide a comprehensive guide to insert molding, covering everything from design considerations to material selection and production techniques.
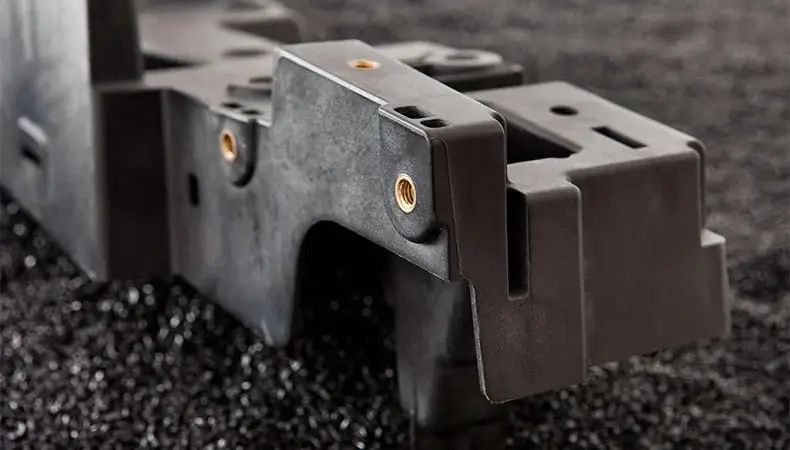
1.Considerations for Insert Molding
When designing for insert molding, several factors need to be considered to ensure a successful and efficient manufacturing process.
1) Proper Placement and Retention of Inserts
First, the design should allow for the proper placement and retention of the insert within the plastic part. This involves considering the size, shape, and orientation of the insert, as well as the type of plastic used.
2) Mechanical and Thermal Properties
In addition, it is critical to consider the mechanical and thermal properties of the insert and the plastic material. The design should also consider any potential stresses or strains that may be imposed on the insert during the molding process or in the final product. These factors include material compatibility, coefficient of thermal expansion, and mechanical strength, among others.
3) Suitable Materials
Choosing the right insert molding material is critical to ensuring the desired functionality and performance of the final product. The plastic material should have good flow properties to ensure the insert is properly encapsulated and minimize the risk of voids or defects. Common materials used in insert molding include thermoplastics such as ABS, PC, and nylon.
The insert material should be compatible with the plastic material and able to withstand the molding process without deformation or degradation. Common insert materials include metals such as brass, stainless steel, and aluminum, as well as other materials such as ceramics or electronic components.
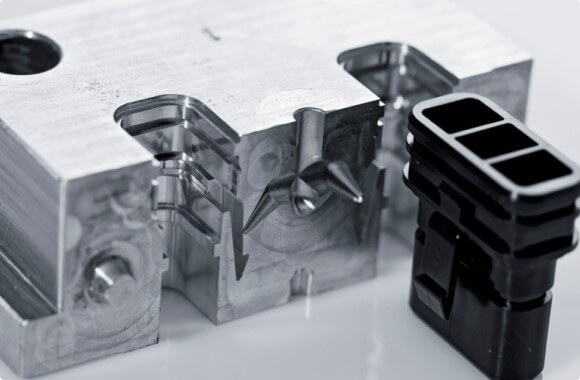
2.Insert Molding Methods
There are several production techniques for insert molding, each with its own advantages and limitations.
1) Overmolding
The most common method is overmolding, which is where an insert is placed into the mold cavity and then the plastic material is injected around it. This technique allows for precise placement and encapsulation of the insert, resulting in a strong and durable bond.
2) Preformed Inserts
Another technique is insert molding with preformed inserts, where the insert is preheated and placed into the mold cavity before the plastic material is injected. This method is often used for inserts with complex shapes or fine features that may be damaged during the molding process.
3) Ultrasonic or hot insertion technology
In some cases, ultrasonic or hot insertion technology can be used to insert components into molded parts after the molding process. This technology is particularly useful for inserts that cannot withstand the high temperatures and pressures of the molding process.
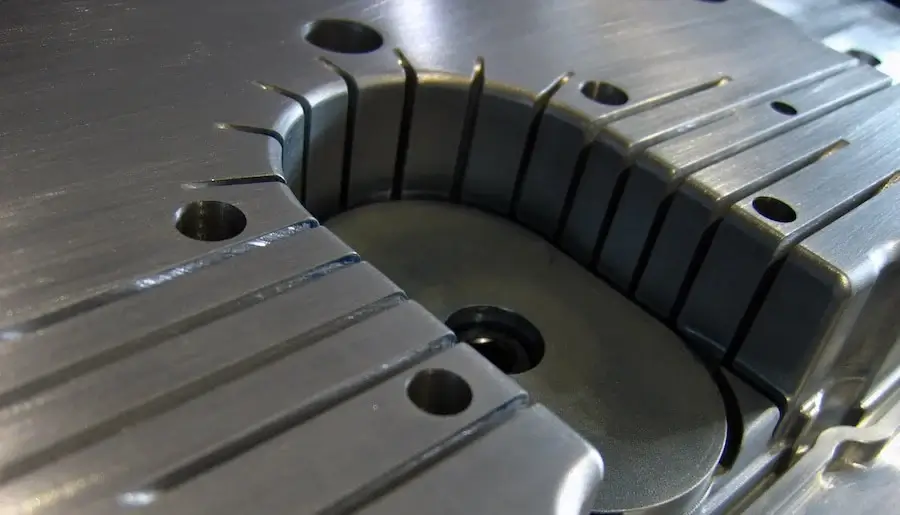
Insert molding is a versatile and efficient manufacturing process that offers many benefits, including improved product functionality, reduced assembly time, and cost savings. By taking into account design considerations, material selection, and production technology, manufacturers can optimize the insert molding process and create high-quality products.