A Basic Guide to 5 Axis CNC Machining Center
1.What is a 5 axis CNC machining center?
A 5 axis CNC machining center is a precision CNC machine that uses a variety of cutting tools to remove material from a workpiece. It cuts along five different directional axes, either by positioning the workpiece or cutting along these axes simultaneously until the desired shape is achieved.
To put it more specifically, an example of a 1 axis machine is a radial drilling machine, which has up and down motion (Z axis). By the same logic, a 3 axis CNC machine can move up and down (Z axis), left and right (X axis), and forward and backward (Y axis).
A 5 axis CNC machining center has two additional rotary axes, which opens the door to endless machining possibilities. Types of rotary axes include rotary axes A, B, and C, which rotate around the X, Y, and Z axes, respectively. Although these are three additional axes instead of two, they are still considered a total of 5 axes.
The combination of additional axes depends on the machine tool and can be any combination of AB, AC, or BC. With additional axes, the cutting tool can approach the part from all sides, allowing undercuts that are only possible on machines with fewer axes, provided the part is repositioned with integrated fixtures.
A 5 axis CNC machine avoids this time-consuming and error-prone process on machines with fewer axes.
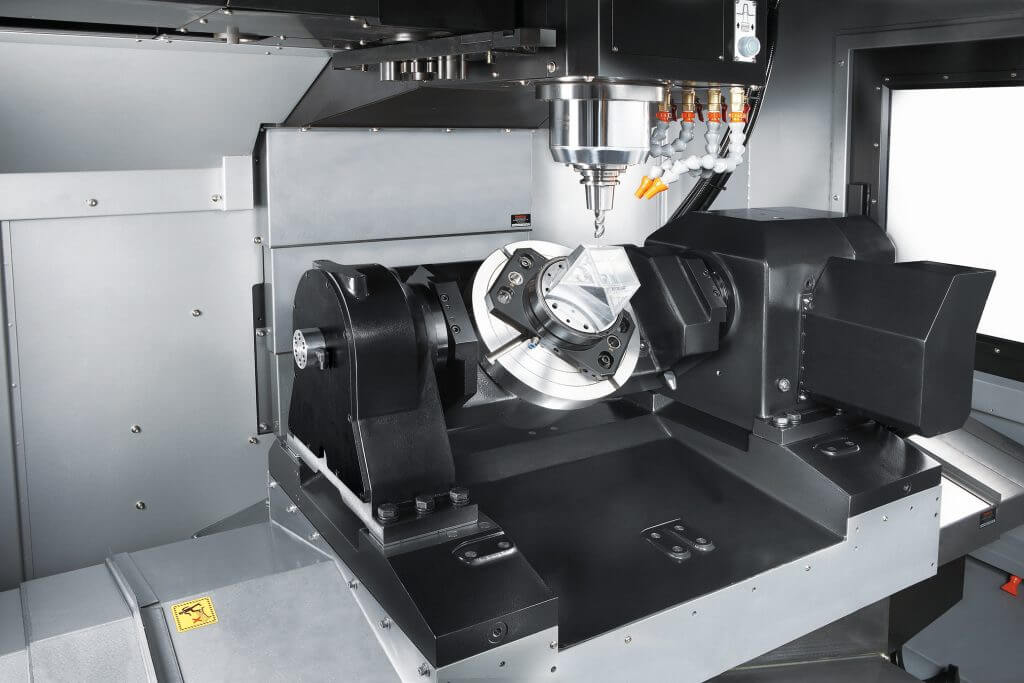
2.How does a 5 axis CNC machining center work?
The cutting tool on a 5 axis CNC machining center can approach the workpiece from any of five sides. It moves in the X, Y, and Z linear axes and rotates on the A, B, or C axis.
Here are the corresponding axes and their movements:
1. X-axis – from left to right
2. Y-axis – from front to back
3. Z-axis – up and down
4. A-axis – 180° rotation around the X-axis
5. B-axis – 180° rotation around the Y-axis
6. C-axis – 180° rotation around the Z-axis
3.Difference between 3-axis and 5 axis machining
To better support the increasingly complex needs of advanced industries such as aerospace engineering, medical, defense, robotics, and automotive manufacturing, CNC machine tool manufacturers continue to innovate and develop newer, more complex, and at the same time more powerful machines.
A major milestone in this field was the development of 5 axis machining center. The capabilities and flexibility of such machines are far superior to standard 3-axis machining centers.
The following table lists some key points:
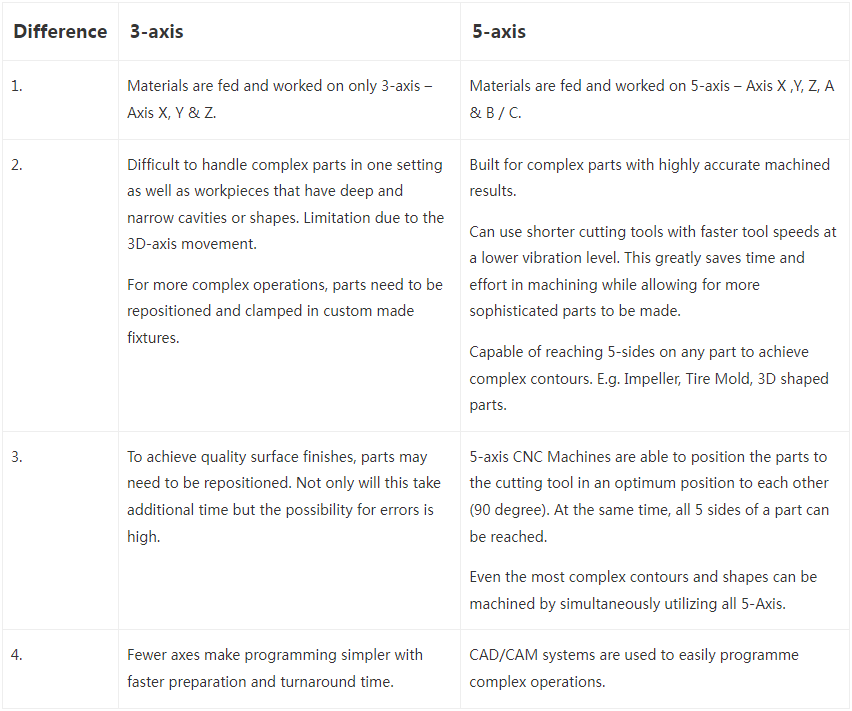
4.How to set up a 5 axis CNC machining center?
One of the advantages of a 5 axis CNC machining center is that there is no need for complex clamping systems or fixtures to fix the machined parts. Therefore, setting up the workpiece on such a machine is quite easy.
The clamping device or workpiece component is preferably mounted in the center of the machine table. The clamping device can be a zero clamp, hydraulic clamp or simply a block to which the component to be machined is securely mounted.
More importantly, the part should have free access to the cutting tool from all 5 sides and be securely fixed so that it does not move or vibrate. The cutting tool and tool holder then need to be prepared, measured and loaded into the machine’s automatic tool changer (ATC) magazine.
An important point that is often overlooked is the calibration of the entire machine before production begins. This calibration requires very special software and an automatic measuring probe (operated by infrared or radio).
By running such a calibration cycle, all axes of the machine are freshly and correctly calibrated, and there is no accumulation of tolerances between each axis. This should be done at least once a month (ideally once a week) and definitely before every production run.
Unfortunately, many 5 axis CNC machining centers are sold without this feature and the necessary equipment, primarily to save money. While this may save initial money, it comes at the expense of accuracy. Over time, these costs can add up, resulting in substandard machining quality. This is certainly not part of industry best practices.
Another important thing to note is to carefully check for any potential collision areas before pressing the cycle start button. Thereafter, let the entire program run step by step to ensure that every position is correct and every tool replaced is the correct one.
If you don’t take the time to check, collisions can occur. Not only will this take a lot of time to fix, it can also result in very expensive repairs and the need to realign all of the axes.
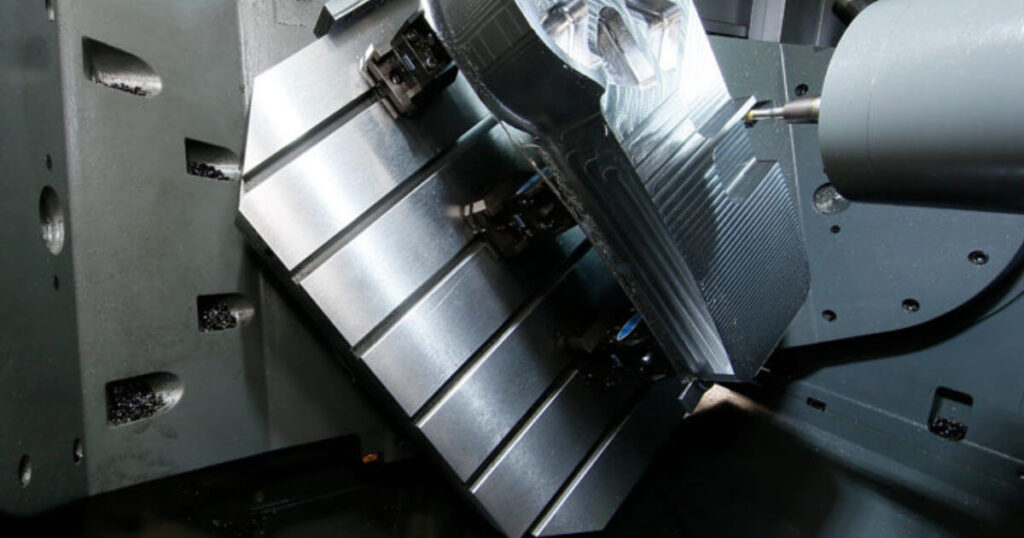
5.How to Program a 5 axis CNC Machining Center?
For part machining, CNC programs are required to position the axes and initiate drilling, tapping, and milling operations. For simple operations that are not too complex, you can do this directly on the machine with the help of the CNC control panel and various CNC macros/subroutines.
To machine more complex jobs or parts with more intricate contours, a CAD/CAM system that is appropriate for the machine tool, the CNC control, and the overall configuration of the machine is required.
Most CNC programs today are written on a secure and dedicated CAD/CAM system, most of which can also check for errors.
The CAD/CAM system requires the right post-processor from the CAD/CAM vendor – to ensure that all data is properly converted into a format that the machine’s CNC control can use.
6.What tools can be used with a 5 axis CNC machining center?
One of the advantages of 5 axis machining (or 3+2 / 4+1 machining) is that it allows for the use of shorter, more robust cutting tools than 3- and 4-axis machining. This allows for faster feeds and speeds, less tool deflection, and better cutting conditions.
These combinations allow for superior surface finish, greater accuracy, heavier cuts, and fewer setups, all of which result in shorter overall cycle times. This capability is very useful in recessed applications such as milling parts or deep cavities in molds.
Tool changes can be easily automated with modern automation solutions on 5 axis CNC machining center.
Larger ATC magazines offer significant advantages when machining very complex parts, both in terms of tools and the number of tools used. Standard magazines with 30-40 stations quickly become limiting.
Therefore, a 5 axis CNC machine with 60 tool stations is recommended. If the parts are very complex and automation is added to the machine, an ATC with 60 stations is a must, although 120 stations would be even better.
This feature not only provides a sufficient number of different tools, but also allows the integration of “sister” tools. Such tools have precise dimensions and specifications for specific operations and wear out faster than other tools. Sister tools are automatically replaced once the life of other tools with the same specifications has ended. This will avoid working with weakened or broken tools.
The main advantage of multi-axis machining centers may be that more surfaces and part sides can be machined in the same setup/clamping compared to simple machines. Multiple operations (milling, drilling, tapping, etc.) can also be performed without re-clamping the part to a secondary position (or even moving the part to another machine).
Not only can time be saved and fixture costs avoided, but errors can also be eliminated. This reduces the need for additional machines or manpower.
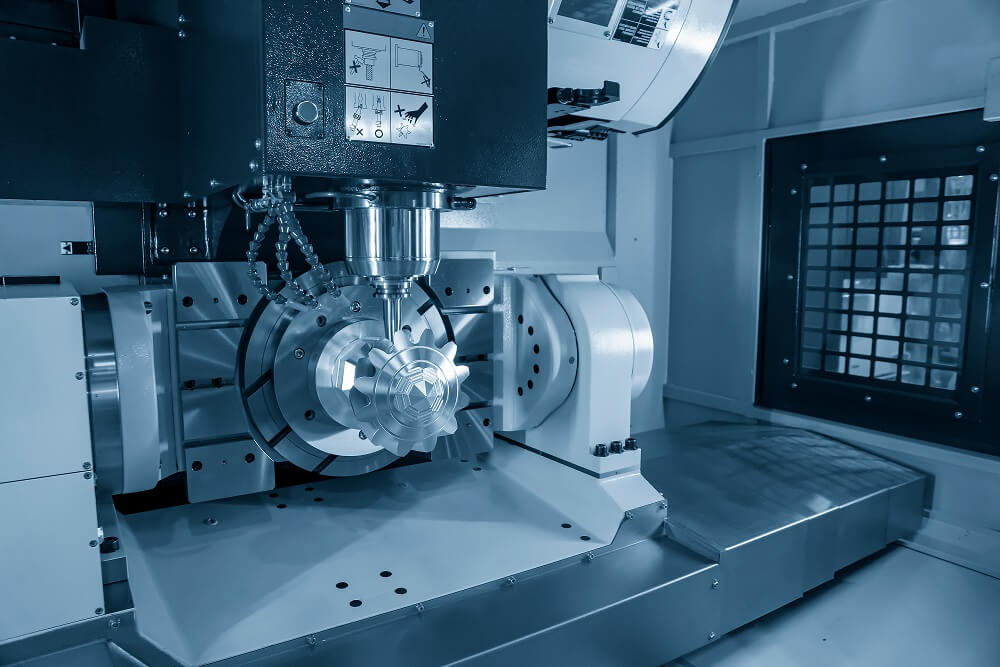
7.What are the advantages and disadvantages of 5 axis CNC machining centers?
Now that you understand how 5 axis CNC machining centers work, you may ask what are the advantages and disadvantages of this type of machine tool. Let’s take a closer look.
1) Advantages of 5 axis CNC machining centers
Main advantages of 5 axis CNC machining centers:
1. Minimized machine setup
With a single setup process (also known as “one-stop completion”), you can significantly reduce preparation time and improve manpower and machine efficiency. This can also reduce human and machine errors caused by multiple setups at each stage of machining.
Simpler clamping equipment for placing parts in the desired position in the machine can also save time and cost and reduce potential errors.
2. Machining complex shapes
With 5 axis machining, complex shapes and designs can be easily processed. This may include: hydraulic system components, water pump housings, gearbox housings, gears, injection molds, oil and gas equipment, medical or blood transfusion equipment, etc.
3. Higher machining accuracy
By reducing the number of manual setups required, 5 axis CNC machining centers can help improve the overall accuracy of produced parts.
4. Better surface finish
With a 5 axis CNC machining center, the cutting tool can not only be close to the workpiece, but also positioned at a 90° angle to the surface of the part, which allows for optimal cutting conditions at all times.
The fourth and fifth axes (rotary axes) allow the cutting tool to be shorter and vibrate less, thereby improving the surface finish. The main purpose of the additional axes is to enable the cutting tool to reach all 5 sides of the part more accurately.
5. Faster Material Removal
Designed to remove the toughest materials quickly and efficiently, 4+1 or full 5 axis CNC machines significantly reduce any manual operations. This improves machining efficiency and stability.
6. Significant Time Savings
With rising labor costs, a lack of trained manpower, and the need to increase factory productivity, it is becoming increasingly important to consider operational and labor costs.
Because such machines feature an all-in-one setup, operators do not need to re-clamp parts and move them to other machines for the next operation. Instead, they can focus on managing additional machines, which improves productivity.
7. Significant Cost Savings
Increased tool life reduces the frequency of changing to new tools. Improved accuracy reduces the risk of costly errors or scrap.
5 axis CNC machining centers further reduce floor space requirements, increase flexibility and spindle utilization, reduce the need for expensive fixtures, and reduce overall inventory investments—all of which can save costs.
8. Expanded Factory Capacity and Production Flexibility
For both part manufacturers and contract manufacturers, investing in a 5 axis CNC machining center increases production flexibility. With their multiple applications, this type of machine tool allows you to maximize the use of your machine tool to meet both large and small manufacturing orders.
These features may not be present in low-cost standard machine tools with significantly limited capabilities. 5 axis CNC machining centers are also ideal for today’s high-mix-low-volume manufacturing environment, where large-scale production is uncommon and machined parts are delivered in small batches and repeatedly when needed.
9. Reduced Competition
5 axis CNC machining centers can significantly increase your productivity and profitability. They put your manufacturing capabilities several levels above your competitors because they are able to take on a wider range of complex jobs, improve product quality, and meet upcoming production needs.
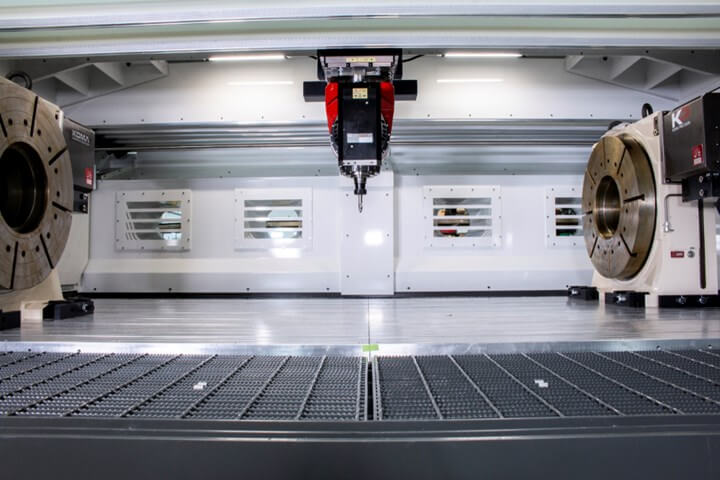
2) Disadvantages of 5 axis CNC machining centers
Of course, there are also some disadvantages to 5 axis CNC machining centers. Here are some common disadvantages:
1. Cost
5 axis CNC machining centers and the prerequisite software usually require a higher initial investment. The total investment cost is usually higher than the cost of a standard 3-axis machining center. In addition, the required maintenance is usually more complex.
2. CAD/CAM Programming
Five-axis machining involves two rotational motions in addition to three linear motions, so it is more complex than three-axis machining and requires consideration of the coordination of the motions of each axis, avoiding interference, collisions, and the appropriate amount of interpolation motion.
Complex programming can be a challenge to optimize the required machining accuracy and surface quality, which may require the services of a qualified programmer.
3. Advanced operator skills required
5 axis machining is an advanced technology in which programming, setup, and machine operation require more highly skilled technicians.
As can be seen from the above points, the advantages of using a 5 axis CNC machining center often outweigh the disadvantages. In today’s challenging production and manufacturing environment, the lack of this highly flexible machining center will put your machine shop at a significant disadvantage. However, you should still consider the range of challenges you face when purchasing a 5 axis CNC machining center. To avoid making a costly mistake, consider a comprehensive review of your machining requirements before investing in such a machine tool.
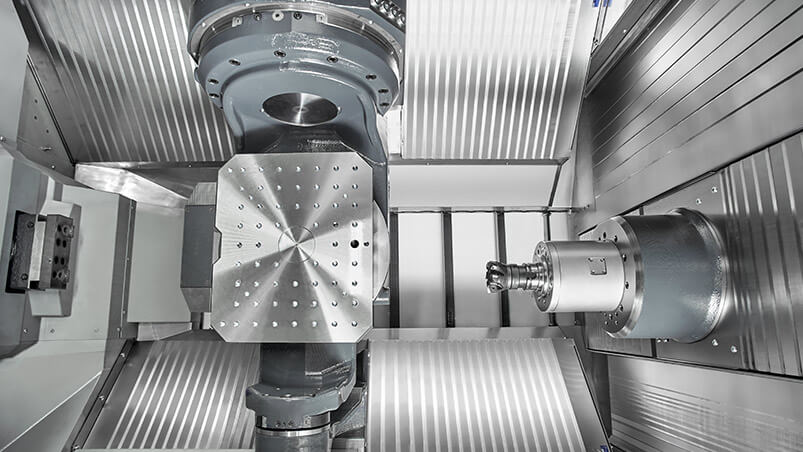
8.What is the best 5 axis CNC machining center?
In order to choose the best 5 axis CNC machining center for your shop, you need to take a close look at its various features.
Use the following as a checklist:
1) Ability to produce complex parts
The head/head rotary axis and 2 rotary axes are located in the head structure. The 5 axis consists of 3 linear axes and 2 rotary axes in the head.
2) Ability to rotate continuously
1. The table/head rotary axis has one rotary axis located on the table and another rotary axis located in the head.
2. The range of motion of the rotary axis located in the head is limited, while the range of motion of the rotary axis located in the table is not limited.
3. This configuration has certain advantages for specific applications. For example, shaft machining – long cylindrical parts that require operations around the part (milling, drilling, tapping, etc.). This is used in standard vertical machining centers (Vesta Line, Sirius Line) or long bed moving column machining centers Hi-Rex 4000/5000/6000).
3) Define the working range
1. Table/table rotary axis – 2 rotary axes combined into a trunnion table.
2. One of the rotary axes has a limited range of travel, while the other axis has unrestricted rotation.
3. This is widely used for complex precision parts or mold applications.
4. Rigidity is suitable for most application requirements.
5. The speeds of the 2 rotary axes vary, depending on the design and construction. The dynamic version is faster and more dynamic, and is mainly used for contouring. The rigid and slower movement speed is suitable for heavier and more stable cutting conditions.
6. Overall, different uses and applications will determine which configuration is most suitable. Each configuration and design has its own advantages and limitations.
4) Sufficient CNC machining capacity
1. The processing power of the CNC control must be high enough to calculate, calculate and control the number of axes used simultaneously.
2. Block processing time/rate becomes more important in 4-axis or 5 axis motion due to the sharp increase in data volume.
3. For a 3+2 configuration this is not as critical since only 3 axes will be working simultaneously at any given time.
4. For a 4+1 configuration the amount of data that needs to be processed is much higher and a faster block processing time is required.
5. For a full 5 axis version where all 5 axes can move simultaneously, block processing time is critical. If it is not fast enough and feed rates are programmed at higher rates the machine may start to jitter or slow down.
5) Match the look-ahead feature to the application
1. A standard machine with a FANUC 0i-MF CNC control has a very low 40 block look-ahead setting and a BPT (block processing time) of only 4 milliseconds.
2. For a 4+1 axis machine used for part machining with a BPT of 2 milliseconds, a minimum of 200 blocks is required.
3. For more complex 4-axis machining operations/sequences with a BPT of 1 millisecond, 400 blocks is recommended.
4. For full 5 axis simultaneous operation, of course a CNC control with faster calculation speed is required. This can be a Fanuc 31i B5 with HAI 600 block look-ahead and 0.4 ms BPT, or the optional 1000 block look-ahead function and the same 0.4 ms BPT, which can provide very high calculation speed even for the most complex operations.
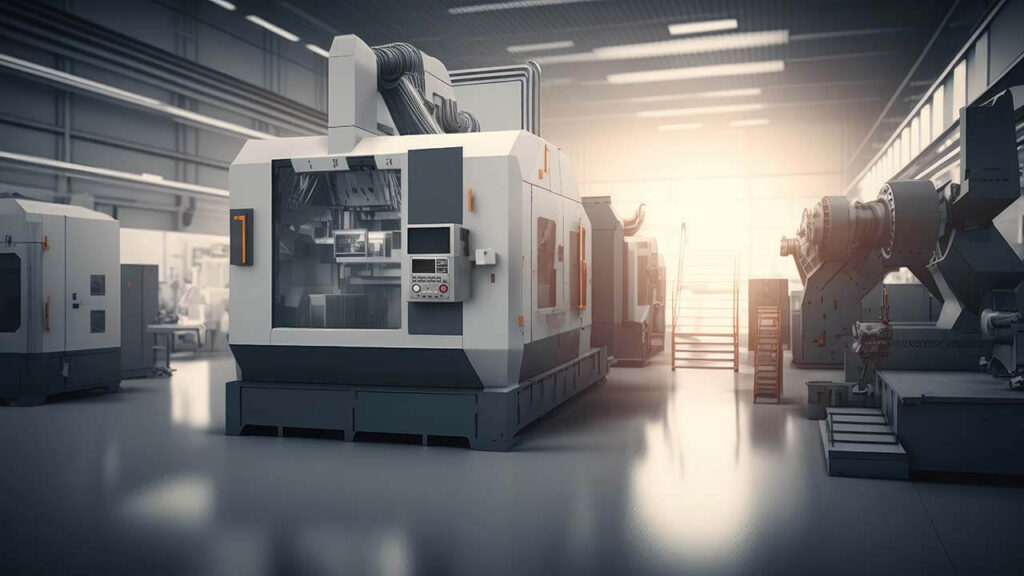
6) The machine tool spindle power and rigidity are sufficient
1. In order to ensure smooth and error-free cutting, the machine tool spindle must have sufficient power to withstand the stress and load imposed on it, and have sufficient limit reserves.
2. The maximum torque of a lower-powered spindle (11-15Kw) is less than 100Nm, which may limit the performance of the machine.
3. Although the initial machine cost may be higher, its wide range of applications and long-term savings will prove to be more cost-effective in the long run.
7) Suitable tool holder system
1. The best tool holder system is BBT or HSK to eliminate vibrations that shorten tool life, affect surface quality and eventually damage spindle bearings.
2. They provide the best connection/bonding between spindle and tool holder at any time and under any machining conditions.
3. Note: The medium-duty HSK-A63 tool holder is 2.5 times stronger and stiffer than the standard BT 50 tool holder.
8) Adaptable cutting feed speed and cutting conditions
The flexibility to maintain a constant cutting feed speed or change the cutting feed speed according to different cutting conditions is important. This allows better control of each situation to optimize the cutting feed speed.
9) High mechanical tolerance and durability
1. Consider the mechanical design and mechanical construction/structure of the machine, as well as the use of electronic systems for optimization and calibration.
2. To ensure longer service life and higher tolerances, all our machine parts are cast in Meehanite to ensure the mechanical advantages of our machines.
10) Spindle Thermal Control and Cooling Management
1. It is vital that the spindle box (including the spindle nose) is effectively cooled and all parts are in optimal condition.
2. This helps to extend the life of this important component and provide better quality and precision for the parts.
11) Horizontal or Vertical
1. Horizontal Five-axis CNC machining centers are usually equipped with automatic pallet changers (APC) and can be installed directly on the shop floor. They tend to be heavier and stronger, supporting cutting steel, titanium or Inconel materials. Designed with effective chip handling functions, large amounts of chips will naturally fall freely into the conveyor.
2. On the other hand, vertical five-axis CNC machining centers tend to be more flexible when machining smaller parts. Operators find it easier and more convenient to clamp parts vertically. Although they allow operators to have better access to parts and monitor the process more easily, such machines require careful design for effective chip removal.
12) Swivel Head or Trunnion Table
1. The non-tilted table on a swivel head machine is often used to hold large, heavy parts because this type of table offers better rigidity.
2. They are also more versatile and can be used with multiple fixtures, vises, or tombstones.
3. Swivel heads as well as trunnion-style versions can use shorter tools because the spindle can reach all accessible areas and points on the part in the shortest distance.
4. Trunnion-style table machines are also preferred in mold making because both rotary axes are contained within the trunnion table itself and the spindle head is fixed.
5. The spindle head extends out of the tilting table, providing better undercutting capabilities as well as access to the underside of the part. 6. Trunnion-style table machines tend to be more effective at clearing large amounts of chips.
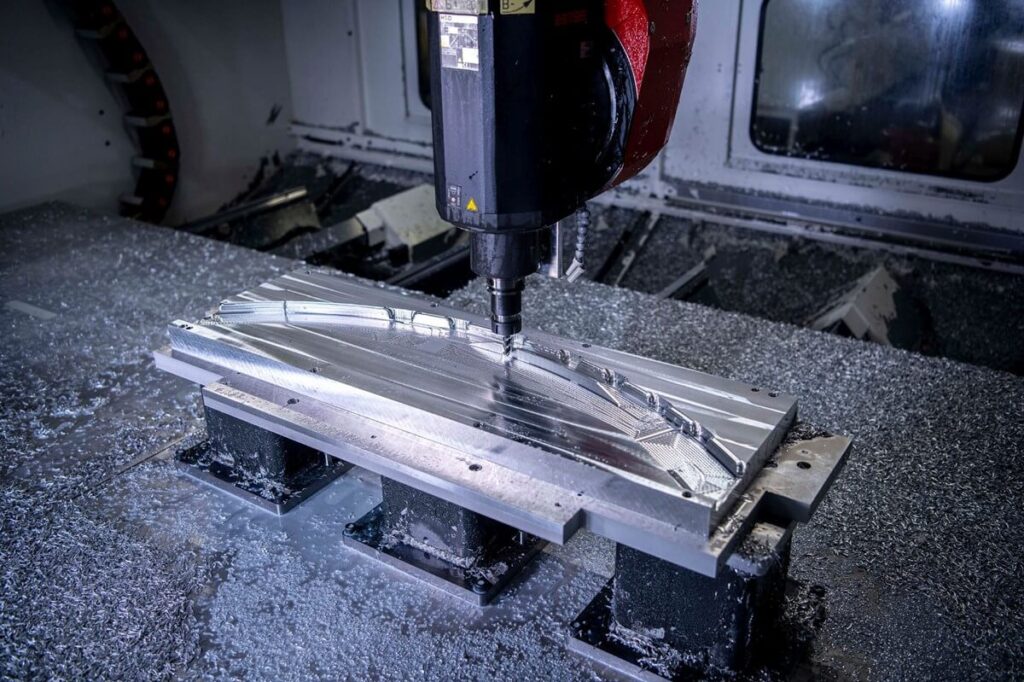
9.What influences the price of a 5 axis CNC machining center?
1) Machine size and specifications
1. Table size
2. X – Y – Z axes
3. Spindle power
4. CTS requirements (through-spindle cooling)
5. Number of tool positions required in the ATC (tool magazine)
6. Other required specifications
2) Types
1. 5 axis is divided into 3 categories, each with different prices:
2. 3+2 axes
3. 4+1 axes
4. Full 5 axes
3) Design
1. Most 5 axis CNC machines have 3 linear axes and 2 rotary axes, provided by the so-called “trunnion” table.
2. Designed and built-in 5 axis machines offer better stability and accuracy, but the investment will be higher.
3. A cheaper version is to add a 2-axis table to the table of a 3-axis machining center.
4) Processing materials
1. Aluminum
2. Standard steel
3. Stainless steel
4. Titanium
5. Inconel 6. Others