A Comprehensive Guide to CNC Precision Turned Parts
CNC precision turned parts are at the heart of precision engineering and are the building blocks of a wide range of complex applications. Often associated with the pinnacle of precision, CNC precision turned parts are an essential component of many advanced industries.
CNC precision turned parts are used in a variety of applications such as aerospace products, fluid and gas control, medical and telecommunications applications, and more.
1.High Precision CNC Turning
CNC turning is a highly automated machining process used to create cylindrical parts by removing material from a rotating workpiece. It is controlled by a computer program that guides the cutting tool to shape the workpiece to the desired specifications.
Known for its accuracy and efficiency, CNC turning is used to manufacture precision turned parts for a variety of parts in industries such as automotive, aerospace, and medical devices. CNC turning is often used to create near-axisymmetric parts.
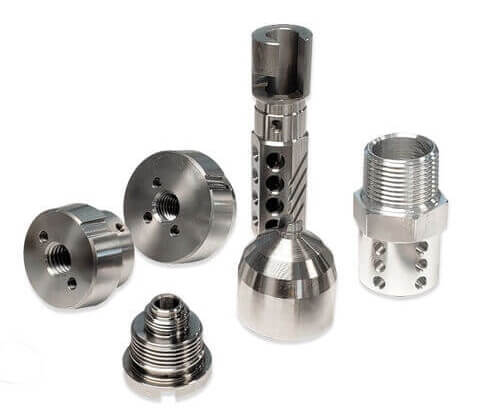
2.High Precision CNC Turning Process Overview
- CNC turning is a highly automated and computer-controlled process that plays a key role in producing high-precision turned parts. The process involves the use of computer numerically controlled (CNC) machines that are capable of complex and precise movements. These machines can operate on multiple axes, allowing for complex shapes and high precision.
- Multi-axis machining is an important feature of CNC turning, allowing parts to be machined from all angles. This versatility is essential when producing complex parts as it allows different surfaces to be cut simultaneously, thereby reducing production time and increasing precision.
The following are the different turning processes:
- Micro-turning: Micro-turning is a specialized technique within high-precision CNC turning that is used to create extremely small parts with fine details. It is commonly used in industries such as electronics, where there is a high demand for miniature, high-precision parts. Micro-turning requires precision tools, high spindle speeds, and advanced programming to achieve sub-millimeter dimensions.
- Thread cutting: Many high-precision parts require threads for assembly. CNC lathes are equipped with tools designed specifically for thread cutting. Achieving precise threads is essential as it ensures that threaded parts fit together securely, preventing any problems in various applications such as automotive and aerospace.
- Contour Turning: Unlike standard turning, where the goal is to create cylindrical shapes, contour turning involves precisely controlling tool motion to create complex, non-cylindrical features.
- Form Turning: A CNC turning process that creates specific geometries or forms on a workpiece, such as grooves, bevels, and chamfers.
- Taper Turning: This process involves gradually reducing the diameter of a workpiece along its length, creating a tapered part. Taper turning is essential for producing parts such as shafts, pins, and spindles that require one end to be wider or narrower than the other.
- Line Turning: Line turning is the most basic CNC turning process and is used to produce cylindrical shapes with consistent diameters. It is commonly used to produce parts such as shafts, pins, and rods. Line turning is characterized by a simple, straight tool path along the length of the workpiece.
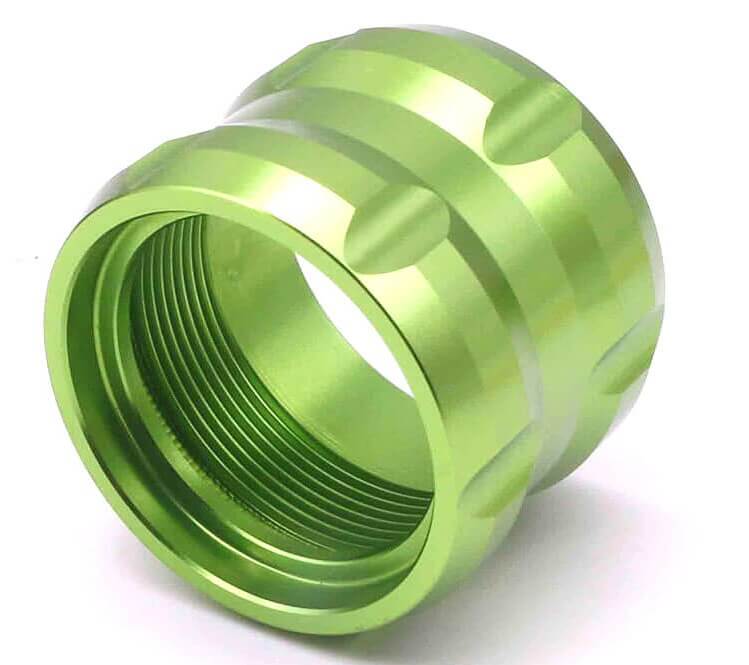
3.High-Precision CNC Turning Materials
1) Metals and Alloys
High-precision turned parts are typically made from a variety of metals and alloys, including stainless steel, aluminum, brass, titanium, and high-speed steel. These materials have excellent machinability and dimensional stability, making them ideal for precision parts.
- Stainless steel
- Aluminum
- Brass
- Titanium
- Copper
- Carbon steel
- Tool steel
- Inconel
- Super alloys
- Monel
2) Plastics
In some applications, precision turned parts can also be made of plastics such as Delrin, PTFE or nylon. These materials are valued for their light weight, corrosion resistance and versatility in applications such as medical and aerospace.
① Delrin (polyoxymethylene)
- Features: Delrin is a high-performance polyoxymethylene resin known for its excellent dimensional stability, low friction and high strength. It is moisture-resistant, chemical-resistant and wear-resistant.
- Applications: Delrin is widely used in precision parts such as gears, bushings and bearings, especially in industries such as automotive and consumer electronics that require low friction and high durability.
②PTFE (polytetrafluoroethylene)
- Characteristics: PTFE, commonly known as Teflon, has excellent chemical resistance, low friction, and excellent electrical insulation properties. It can withstand a wide temperature range.
- Applications: PTFE is often used for precision turning, involving chemical processing, electrical insulators, and low-friction parts such as seals and bearings.
③Nylon (polyamide)
- Characteristics: Nylon is valued for its high strength, excellent wear resistance, and good chemical resistance. It is lightweight and easy to process.
- Applications: Nylon is used for precision turned parts such as bushings, washers, and structural parts, where its durability and ease of processing have advantages.
④Acrylic (polymethyl methacrylate)
- Characteristics: Acrylic is a transparent thermoplastic with excellent optical clarity. It is lightweight and has good impact resistance.
- Applications: Precision turned acrylic parts can be used in optical devices, medical devices, and consumer products, where optical clarity and aesthetics are important.
⑤UHMW (Ultra-High Molecular Weight Polyethylene)
- Features: UHMW polyethylene has excellent wear resistance, chemical resistance and impact strength. It is self-lubricating and has a low coefficient of friction.
- Applications: UHMW is used for precision turning in applications that require wear-resistant parts, such as conveyor belt parts, bushings, and medical devices.
⑥Peek (Polyetheretherketone)
- Features: Peek is a high-performance thermoplastic with excellent mechanical properties, including high temperature resistance, excellent chemical resistance, and low moisture absorption.
- Applications: Peek is used for precision turning in demanding environments, including aerospace, medical, and automotive industries.
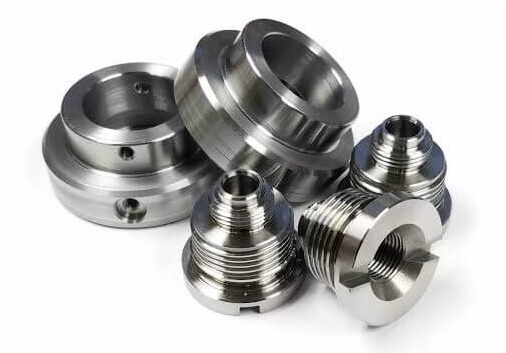
4.Applications of CNC Precision Turned Parts
CNC precision turned parts are widely used in various industries due to their precision and versatility.
1) Automotive
They are used in engine parts, transmission systems, suspension systems, and steering mechanisms. Such as shafts, bushings, and specialized fasteners. The accuracy and reliability of CNC precision turned parts are critical to the safety and performance of vehicles.
2) Aerospace
They are used in aircraft engines, landing gear, and control systems. CNC precision turned parts in aerospace applications include pins, shafts, and various accessories that ensure the integrity of critical systems.
3) Medical devices
The medical industry relies on CNC precision turned parts to manufacture surgical instruments, implants, and diagnostic equipment. These parts must meet tight tolerances and be biocompatible. CNC precision turned parts in the medical field include bone screws, dental implants, and connectors.
4) Electrical and Electronics
CNC precision turned parts are used in connectors, sockets, and switches in the electrical and electronic industries. These parts ensure secure electrical connections and are essential to maintaining the reliability of electronic equipment.
5) Hydraulic and Pneumatic Systems
CNC precision turned parts are essential parts for hydraulic and pneumatic systems, including pumps, valves, and accessories. These parts control and transmit fluids and gases, and their precision is essential to prevent leaks and ensure efficient operation.
6) Industrial Machinery
CNC precision turned parts are an integral part of industrial machinery such as textile machines, printing equipment, and packaging machines. Parts such as spindles, shafts, and couplings are essential for the efficient operation of these machines.
7) Oil and Gas
CNC precision turned parts are used in parts for drilling equipment, valves, and wellhead components in the oil and gas sector.
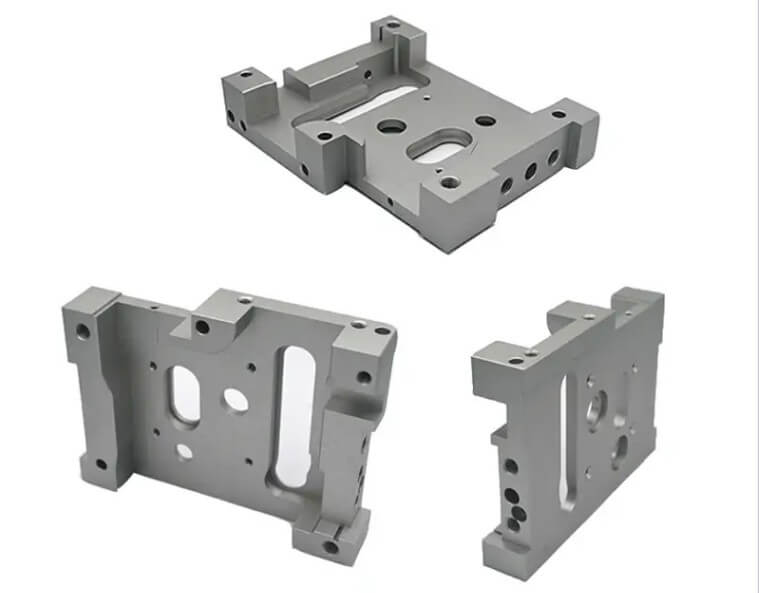
5.Industry Standards for CNC Precision Turned Parts
Industry standards for CNC precision turned parts vary by specific application, industry, and geographic location. These standards ensure the quality, consistency, and safety of CNC precision turned parts.
Here are some of the notable industry standards and organizations related to precision turned parts:
Standards | Description |
ISO 9001 | ISO 9001 is a globally recognized standard for quality management systems. |
ISO 286-2 | ISO 286-2 provides international standards for limits and fits. |
AS9100 | AS9100 is a quality management standard specifically for the aerospace industry. |
ASTM International | Develops and publishes standards for materials and components used in a wide range of industries. |
NADCAP | It sets rigorous standards for aerospace precision components. |
SAE | Develops and maintains standards related to automotive, aerospace, and commercial vehicle engineering. |
FDA | Food And Drug Administration |
6.Benefits of CNC Precision Turned Parts
1) Cost Effectiveness (Energy Savings)
CNC precision turned parts can reduce your operational energy costs by minimizing friction and waste heat, and are able to produce the same power output while running at lower speeds.
2) Improved Productivity
Deploying CNC precision turned parts in your applications can optimize your production processes and improve overall efficiency, increase accuracy, and minimize human errors.
3) Ability to produce high-quality parts using a variety of materials
Investing in CNC precision turned parts also gives you greater control over the material and dimensional configuration of your parts, allowing you to use a variety of materials including steel, titanium, aluminum, chrome, and even various thermoplastics or acrylics without compromising quality, accuracy, or delivery time.
4) Dimensional Accuracy and Reduction of Human Error
CNC machining is able to meet the tight tolerances required for any production volume, maintaining dimensional accuracy throughout the production process.
This helps reduce human error, lower costs through rational use of materials and reduced waste, thereby reducing the unit cost of CNC precision turned parts throughout the production process, and simplifying the inspection and approval process.
5) High Repeatability
CNC precision turned parts have high repeatability, which is critical for producing identical parts in consumer applications. CNC machines can continue to produce identical parts in an indefinite production run, making them ideal for mass production scenarios where multiple parts need to be machined to exacting specifications each time.
6) User-Friendly and Safe
The accuracy and repeatability of CNC precision turned parts improves their user-friendliness and safety ratings, reducing the risk of DOA components, premature mechanical failures and breakdowns, while also saving you and your end users long-term repair and maintenance costs.
7) Low Waste
CNC precision production enables manufacturers to optimize the use of their valuable raw materials and pass on the savings to their customers without compromising on quality and turnaround time for premium products.
7.Conclusion
CNC precision turned parts are essential in every industry, from automotive to aerospace, medical devices to electronics. They are the driving force behind critical systems and components, ensuring quality and performance.