Gear Machining: Types of Manufacturing Processes You Need to Know
The concept of gear machining has been around for a while as they are one of the oldest machine components still in use today. Gears offer a variety of benefits across a wide range of applications. They are used in a variety of products and industries including automotive, aerospace, industrial, and more. Ron’s Machining Service offers a full range of backend and driveline components produced by today’s top manufacturers.
Gears can also be manufactured using techniques such as casting, forging, extrusion, powder metallurgy, blanking, and gear milling. However, the machining process is critical to achieving the size, shape, and surface finish of the final gear.
1.Importance of Gears in Machinery
Gears have several importance in machinery, which include:
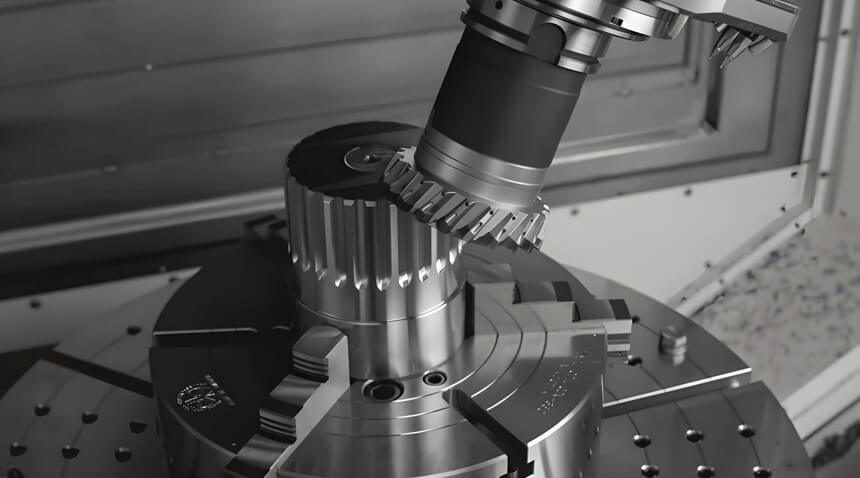
1) Setting the Speed of Rotation
The gear cutting process plays a vital role in regulating the rotational speed of a mechanical system. A prominent example of this function can be observed in the use of gears within an engine. These gears are responsible for fine-tuning the speed of the engine by adopting a specific gear ratio. Including gears with different ratios, such as a ratio of 1:2 for an electric motor running at 1400 rpm, helps in regulating the number of motor revolutions per minute. This allows for precise control of the speed.
2) Transmitting Power
The basic function of a gear lies in its ability to transmit power between interconnected parts without encountering problems associated with slippage. A common example of this capability is a lathe. In a lathe setup, the motor is not directly connected to the spindle for manipulating the chuck. Gears are cleverly used to bridge the gap between the motor and the shaft to ensure adequate power transmission. This facilitates reliable movement of the chuck.
3) Changing Torque
Torque is the rotational force of the engine and is essential for acceleration. The gear blank plays a key role in regulating torque output. The effect of gear diameter on torque production embodies this principle. The larger the gear diameter, the greater the torque, and this principle applies both ways. The choice of gear blank diameter can precisely adjust the torque characteristics of the engine, thereby affecting its acceleration capabilities.
4) Changing the Direction of Power
The gear cutting process helps to change the direction of power transmission. In addition to adjusting speed and torque, the gear blank can also affect the change in the trajectory of power. Gear cutting is used in structures such as dam gates and reservoir machinery. A notable example is the operation of doors through gears. By using gears, the manipulation of the door handle can be converted into vertical movement. This allows the door to move up and down in a controlled manner.
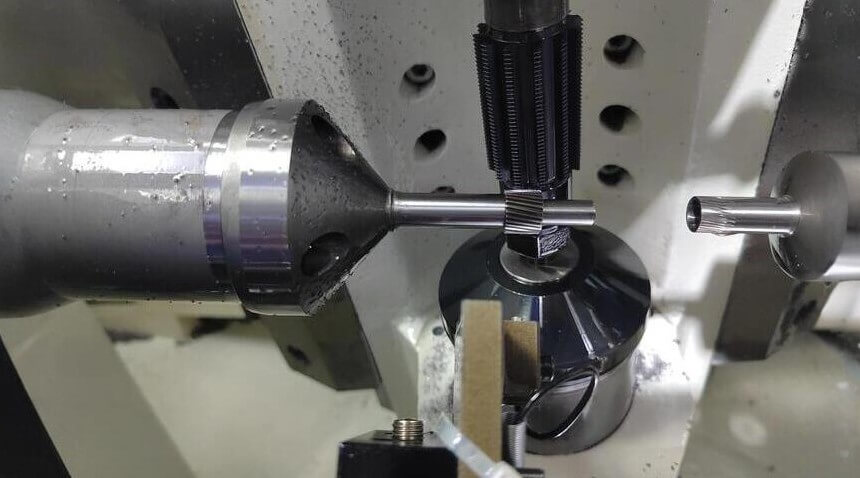
2.What is Gear Machining: Overview
Gear machining involves the precise manufacturing and shaping of gears, which are an indispensable component in machinery for transmitting torque. Gears are characterized by their rotating nature, with their teeth meshing with the teeth of another gear mechanism. This mechanism allows for seamless transmission of mechanical power.
The gear cutting process involves meticulously carving gear teeth into a spherical blank, creating a perimeter adorned with these essential features. The gear cutting specialty encompasses a variety of machining techniques, each designed to produce high-precision gears.
Gears are made using a variety of methods, including machining, powder metallurgy, casting, and stamping. Of the many techniques available, the most precise and popular are gear milling, grinding, broaching, and hobbing methods. These techniques ensure the creation of complex and well-defined gear profiles.
Gears are made from a variety of materials, including metal, plastic, and even wood. Advances in technology have led to alternative methods, where metal and plastic gears can be die-cast or injection molded. As a result, manufacturers can go beyond traditional gear manufacturing processes. However, it must be acknowledged that in some cases post-processing is required to perfect the final gear product.
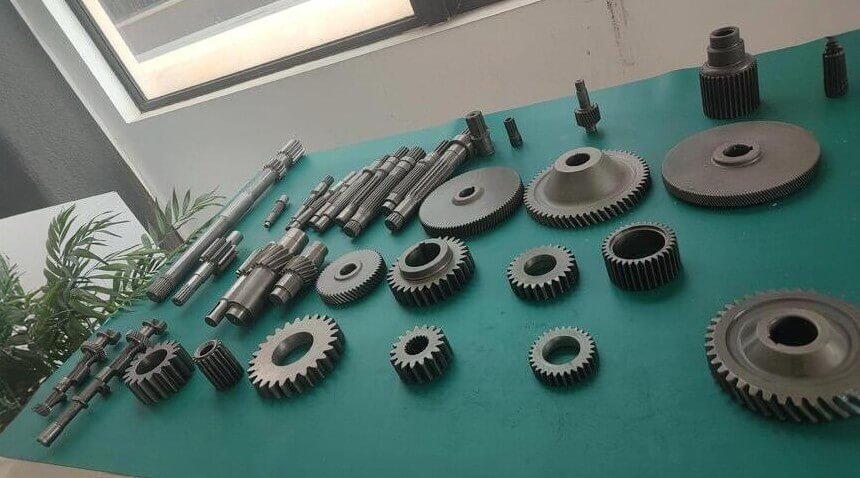
3.Types of Manufacturing Processes for Gear Machining
Let’s look at the various machining processes used for gear manufacturing and their unique applications:
1) Casting
CNC gear hobbing machines are used to produce the teeth of gears. However, casting is a simpler process that is often used to prepare blanks or cylinders for gears. It is the preferred choice for gear blanks due to its ability to be mass-produced and its relative simplicity. However, casting is the most commonly used production technology in a specific area. That is the manufacture of giant gears. Gear cutting and other hobbing techniques may be more practical in large diameter gears. Larger gears are usually spur gear structures.
The most popular casting techniques for manufacturing gears are shell casting, die casting, sand casting, and permanent mold casting. In other cases, other strategies are only partially useful. Nonetheless, the above strategies are the most common in the manufacturing industry.
2) Forging
This is an alternative production method. It can produce both blank components and prefabricated gears. The forging process has practical uses and is mainly used in cases involving relatively simple gear blank designs. In theory, forging is a very effective technology for manufacturing heavy gears. This application stems from the need for forged components to undergo a heat treatment process. This gives the final gear enhanced fatigue resistance. Nonetheless, it must be acknowledged that the enormous forces required by the forging process limit the size and thickness that can be achieved through this method.
In practice, forging performs best when producing gears with diameters of 6 to 10 feet. It is worth noting that the specific forging variant employed (e.g., precision forging) may determine whether a subsequent machining process is required to achieve the final gear specification.
3) Extrusion and Cold Drawing
This represents an alternative gear cutting process that combines versatility with simplicity. Extrusion technology exhibits favorable cost benefits by reducing tooling requirements. However, it must be noted that this factor may not be the only factor that determines the ultimate economic feasibility.
Extrusion, as the name implies, involves passing a heated metal profile through a predefined, smaller-sized shape. The process produces a solid bar with the desired geometry, characterized by a solid and impeccably smooth outer surface.
A similar process is called cold drawing, which is similar to extrusion but has specific differences. First, the extrusion process pushes the blank through a die, while the cold drawing process pulls it through a die. In addition, the contrasting aspects of the two involve temperature control. Unlike the extrusion process, the cold drawing process does not require heating of the initial blank, so the mechanical properties of the final product can be improved, but the cost will increase.
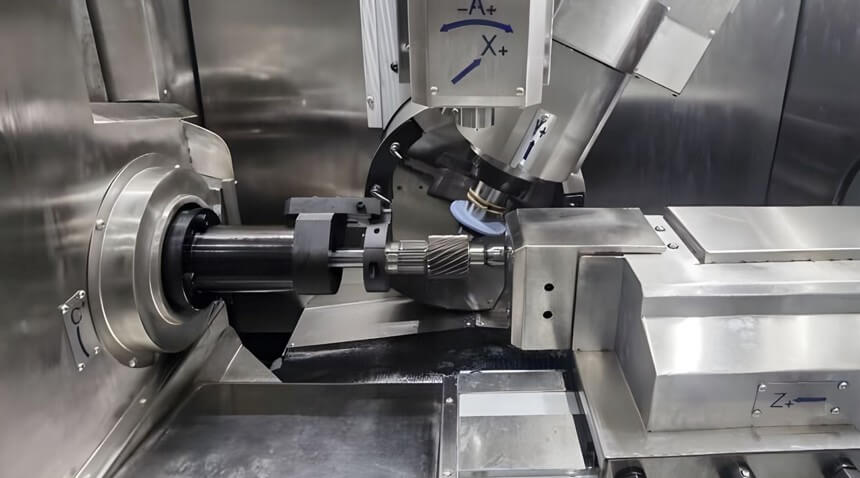
4) Powder Metallurgy
Powder metallurgy is a complex technology that has made great progress in recent years. It is now used in various gear manufacturing processes, including internal gear manufacturing. So, how does it work? From the outside, it looks very simple. However, there are many complex factors involved. Everything starts with metal powder. The first step is to shape all the powder into the desired shape. After that, the next stage ensures that the whole unit is compact, thereby achieving higher mechanical properties. After that, the whole unit is carefully heated.
It is very efficient, simple, and cost-effective when produced in large quantities. No post-processing is required, and the product can be used directly. However, the resulting internal gear has size limitations and cannot withstand excessive loads. In addition, the initial cost of any powder metallurgy system is relatively high, so it is not suitable for small-scale hobbing.
5) Blanking
Blanking technology is very similar to extrusion technology, although there are some limitations in its three-dimensional capabilities. In this gear manufacturing process, metal sheets are used with a series of dies to obtain the desired shape. Various types of gears can be manufactured through blanking, with an emphasis on achieving the best results when producing spur gears. Blanking methods of gear manufacturing can be applied in many industries, especially in environments where lightweight solutions are required. Notable industries include office equipment, hydraulic systems, small medical devices, and other situations where minimum load prerequisites are required.
4.Gear Machining Process
This is a popular gear cutting process due to its adaptability. While traditional machining methods have historically been used for gear cutting and production, computer numerical control (CNC) machining has significantly increased its popularity.