Large CNC Machining Services: Essential
It is not always feasible to produce large parts with traditional methods, but large CNC machining services makes it possible to machine these parts.K&B Machining has the capabilities to machine large-scale parts.
In addition, many industries, including mining, agriculture, construction, and oil and gas, require large machining.
Large CNC machining involves the manufacture of large-diameter products weighing up to 100 tons. CNC machines used for this process typically have many large-diameter machining equipment and parts, as well as simple and complex shapes.
In addition, large machining capabilities are always simulated before manufacturing. This helps to improve quality while reducing production costs.
So, what exactly is large CNC machining? What are the applications of parts produced through this process? What factors need to be considered when machining large parts? Read on as we answer these questions and shed more light on large CNC machining.
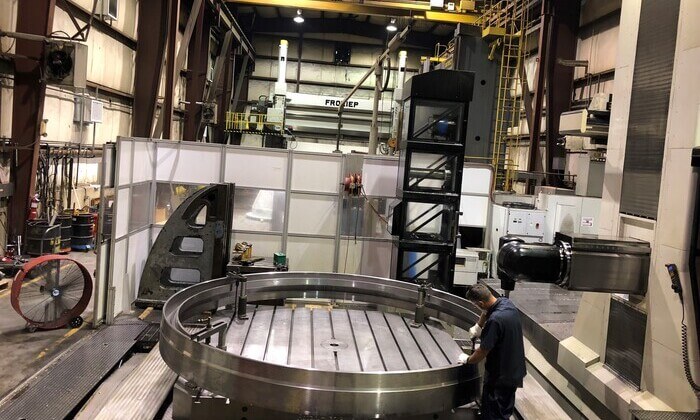
1.What is large CNC machining?
This is a CNC machining process used to manufacture large mechanical parts. It is a subtractive machining process like traditional CNC machining, but it is not as simple.
In this process, a computer directs different machine tools to remove parts from a large workpiece during the machining process.
There are four main steps in the large CNC machining process;
1) Design creation through computer-aided design (CAD) software
The first step is to create a model design of the large machine component. The model can be 2D or 3D. This process uses software and the design depends on the product requirements.
The CAD model design shows the operator the key features and other features required for effective machining, such as tolerances, threads, and construction lines.
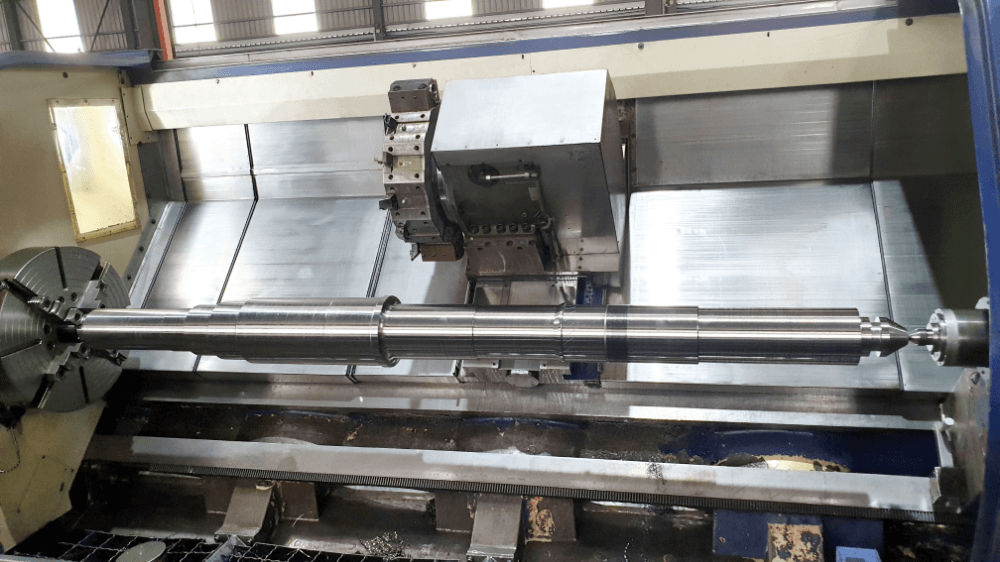
2) Converting the CAD file to digital code that the CNC equipment can read digitally
Since CNC machines cannot recognize CAD models, the model must be converted to a format that the CNC machine can effectively interpret. This conversion involves the use of CAM software.
The software converts the CAD model to a CNC compatible format and instructs the CNC machine machining parameters, such as the cutting sequence. Other instructions include rotary and linear motion, tool paths, machine speed, and workpiece.
3) Preparation and positioning of tools and workpieces
After the CAD model is converted to code, the next step in the process is to prepare for machining. Preparation includes selecting a CNC machine suitable for the process, selecting tools, and configuring operations.
The type of CNC machine and process selected depends on the complexity of the design, budget, and workpiece material.
Automated Part Generation
This is the final step in CNC machining. It involves starting the machining process. However, before starting the process, it is important to perform a final check to ensure the connection of important cutting tools.
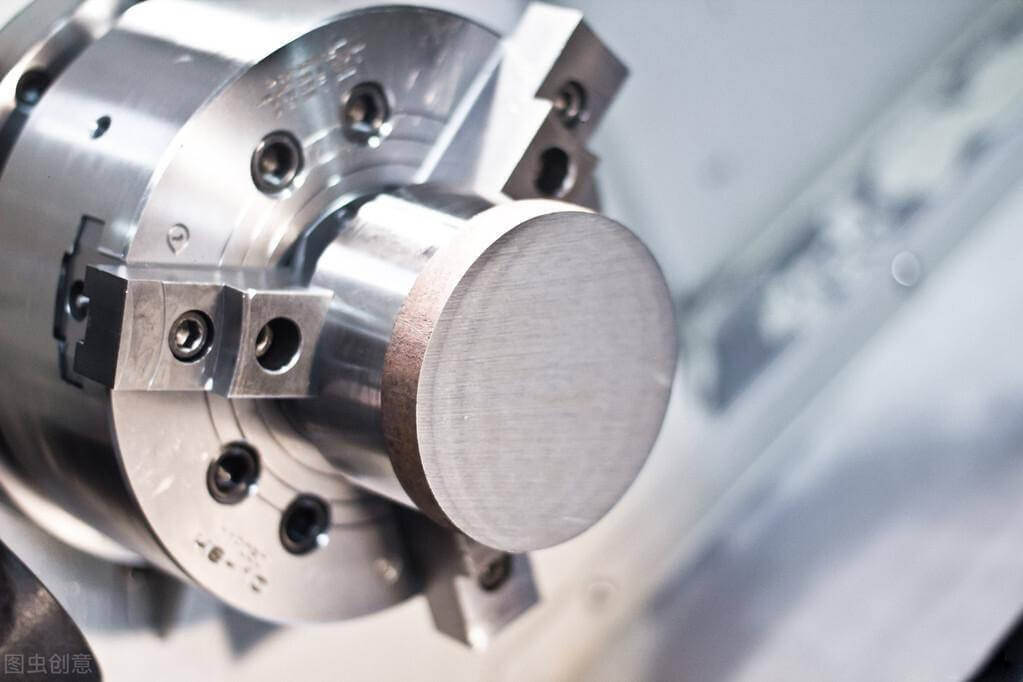
2.Applications of Large CNC Machining Parts
Many industries use large CNC machining to produce parts and large components. However, the most common industries include: automotive, aviation, energy and power generation, mining, and oil and gas.
Let’s look at these industries and their capacity and demand for large parts in more detail.
1) Automotive
Although the automotive industry uses small CNC machining to machine prototype vehicles, they prefer to use large CNC machining in real-time production. This is especially true when manufacturing automotive components such as engines, shafts, cylinder heads, and transmissions.
2) Aerospace
The aerospace industry is another industry that uses large CNC machining to produce parts. There are many reasons why this industry adopts large CNC machining. First, it has a high level of accuracy and precision. Another reason is the ease of producing replacement parts and upgrading machine parts.
3) Energy and Power Generation
Large energy generation components are needed to meet demand. Only large CNC machining has the capacity to manufacture these components. Applications of large CNC machining in the energy and power generation industry include the production of wind turbine casings and power generation engines.
4) Mining
Equipment used in the mining industry is usually large in size to achieve optimal lifting capabilities. They also have high strength to withstand the pressure of mining without breaking down. This makes large CNC machining an ideal choice for this industry.
Engineers use large CNC machining to manufacture mining industry steel parts such as rocker arms, racks, and gearboxes.
5) Oil and Gas
The oil and gas industry is another industry that uses large parts and equipment. These equipment are often located at drilling stations and include steel parts gearboxes, hydraulic fracturing pumps, and connecting rods.
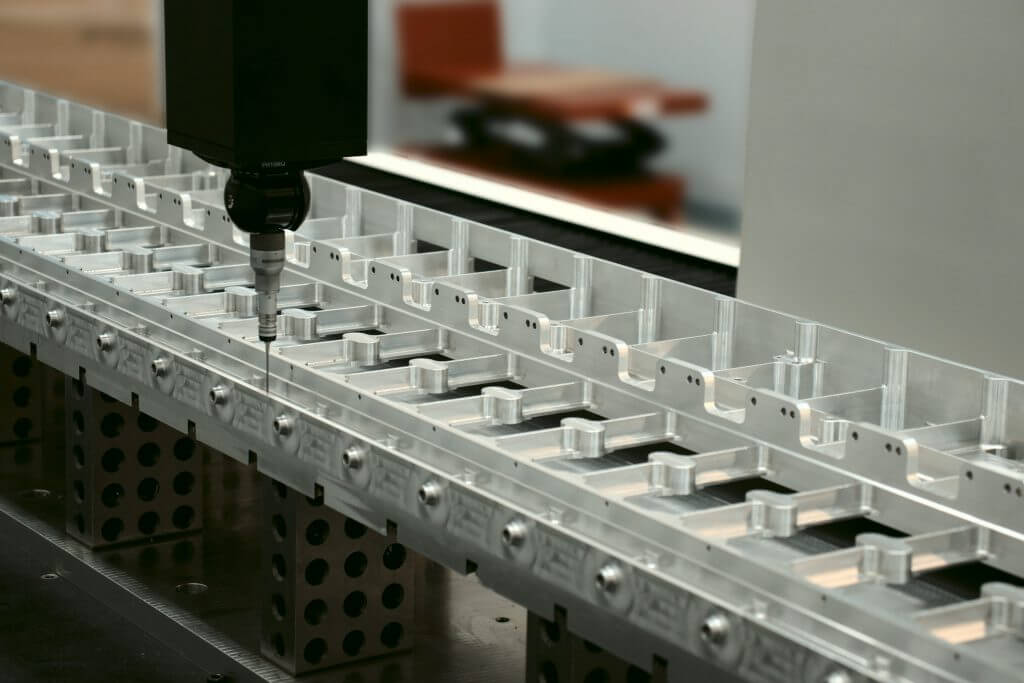
3.Precautions for large CNC machining parts
Due to the size difference, manufacturing large parts is not as easy as manufacturing small parts or materials. Therefore, many factors must be considered before machining large parts. These considerations include:
1) Design
The engineering design of a high-quality design involves many factors. Understanding these factors is the first step in making a high-quality design. Design factors that need to be considered include:
- Temperature: Temperature is an important consideration when manufacturing large parts. This is because heat is a major byproduct of CNC machining. This heat can be generated due to friction during the machining process and can change the dimensions of the workpiece.
- Work Area: CNC machinery used to machine large parts should have a work area, table, or area. This area allows for efficient machining of these parts while minimizing deformation.
- Accuracy and Speed: Professionals in the field of large part machining do not complete the entire process in one go. Instead, they make incremental changes to the design. This design, while time-consuming, can improve the accuracy of the design. It also eliminates the risk of expensive modifications and delays.
2) Planning
Large CNC machining requires preparation and planning to avoid reverse engineering at the end of manufacturing. You should also note that machining large parts requires many components and equipment.
Therefore, it is important to machine large parts at a location that has the facilities and capabilities to withstand the weight of the equipment. The following factors need to be considered when planning;
- Collisions: Due to the large size of the parts, collisions between one part and other materials may occur. Therefore, it is important to optimize the CAD file to eliminate collisions. Also, check the proportions of the inside of the housing to the design.
- Weight: The larger the part being machined, the heavier and more difficult it is to machine. Therefore, it is important to consider weight support when planning.
- Loading devices: Although these devices cannot cut large parts, they are still important. This is because they help load and unload heavy parts and parts that are difficult to move.
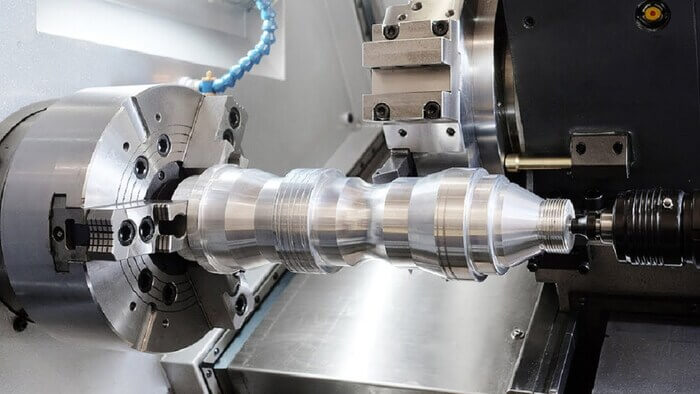
3) Tools
The tools used to machine standard diameter parts are very different from the tools used to machine large diameter parts. Although both tools work in the same way, their operating ranges are different.
Therefore, before performing large CNC machining, it is best to obtain machining tools such as cast iron and steel that are suitable for large diameter machining. These tools include: large lathes, large CNC milling machines, large drilling machines, large boring machines, etc.
4) Machining process
In addition to machining, knowing the right tools and proper settings is also one of the main considerations for machining. The reason is that successful large CNC machining processes use different equipment and techniques.
Common large CNC machining processes include:
This involves machining using machines that can move in different directions or multiple axes. These axes include: X, Y, and Z axes and A and B rotary axes.
Using multi-axis mobile machines to machine large parts is more efficient than using 3-axis or 4-axis machines. This is mainly because multi-axis machines machine large part sections from different angles and directions.
Contour drilling is a process used to finish uneven surfaces as the contouring tool is able to machine hard-to-reach sections.
Using this tool helps smooth out radii and workpiece angles, resulting in a high-quality and consistent finish across the entire surface of a large component.
This process involves rough drilling, milling, and finishing. It is a multi-step process that involves drilling metal by carefully aligning the center of the cut. The benefit of this type of drilling is that it maintains the integrity of the material by causing minimal damage to the material.
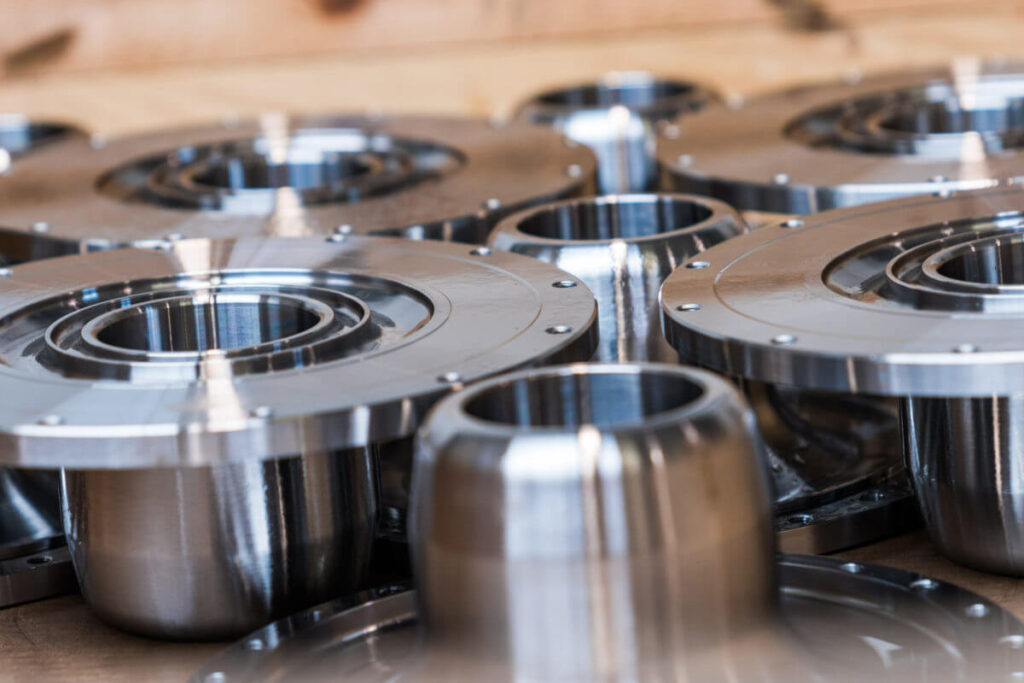
4.conclusion
Large part machining is much different from small part machining because large parts are oversized and usually require careful handling. Due to their size, they require unique machining considerations that will help reduce deformation.
If you are looking for an experienced CNC machining manufacturer, Xavier is your ideal choice. The Xavier team is well-equipped to provide high-quality CNC machining solutions. If you need more information or to discuss your machining needs with us, please feel free to contact us.