Basic Introduction to Laser Welding
In the manufacturing industry, traditional welding methods often affect product quality due to unstable welding quality and large thermal deformation. In contrast, laser welding stands out with its advantages of high precision, high speed and low heat impact, making it an ideal choice. It melts and fuses materials through a highly focused beam and can be used for a variety of materials, whether thin or thick workpieces. Want to know how laser welding is performed? Please read this guide carefully.
1.Principle of laser welding
The principle of laser welding is energy conversion. Laser is a device that converts electrical energy into light energy. Its light energy is guided into a coherent and concentrated beam during welding to heat and melt the materials being connected. The key to its efficiency lies in the interaction between light and material. The laser energy is converted into heat after being absorbed by the material, and the heat is concentrated at the weld, causing the material to melt and fuse.
The high energy density of the laser only affects a small controlled area, making it ideal for precision applications. Unlike traditional welding techniques that use flames or arcs to generate heat, laser welding can accurately control the depth and width of the weld, which is extremely valuable for industries with complex designs and high tolerance requirements.
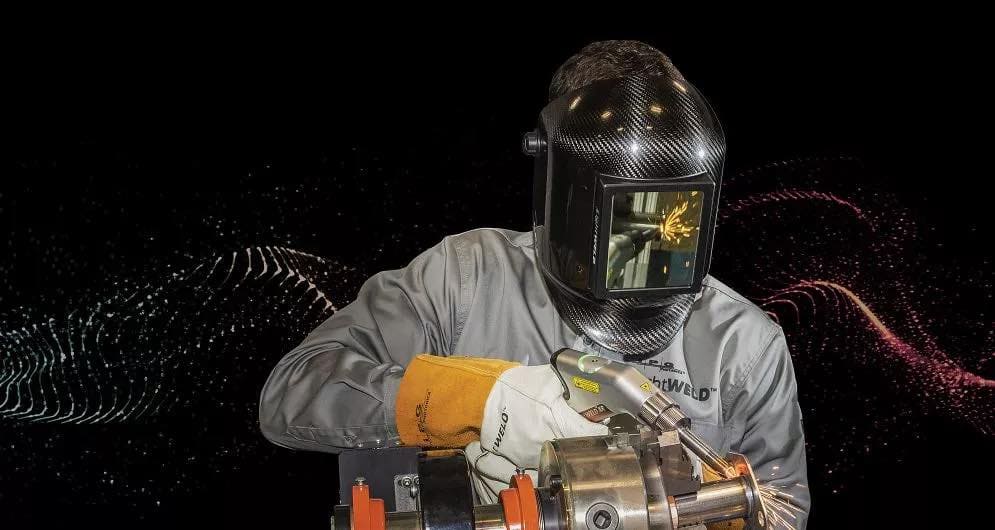
2.Laser welding process steps
(i) Material positioning
The first step in laser welding is to accurately position the materials to be joined. Correct alignment of the materials is critical because the laser needs to be focused at the weld joint. Usually, clamping or fixing devices are used to ensure that the materials are stable and motionless during the welding process.
(ii) Focusing the laser beam
The laser beam is then focused on the surface of the material. The beam is concentrated into a small and precise point, releasing a large amount of energy. The beam size, power and focus are adjusted according to the thickness of the material and the required welding depth.
(iii) Melting the material
When the laser is applied to the material, the material is heated to the melting point, forming a small molten pool at the welding point. The high precision of the laser ensures that only the target area is melted, thereby reducing the heat-affected zone and avoiding unnecessary damage to the surrounding materials.
(iv) Creating the weld
The molten material on the two surfaces merges to form a seamless joint. The laser beam moves along the joint, continuously melting and fusing the material. Depending on the material and the type of laser welding, the weld can penetrate deep into the material or remain shallow at a surface joint.
(v) Cooling and solidification
After the laser is removed, the molten material cools and solidifies rapidly, forming a strong and durable bond between the two pieces of material. Rapid cooling can minimize the risk of warping or deformation, ensuring a clean and beautiful weld.
(vi) Post-weld inspection
After welding is completed, a post-weld inspection is required to ensure the integrity of the weld. Depending on the application scenario, the inspection method includes visual inspection, non-destructive testing methods or mechanical testing.
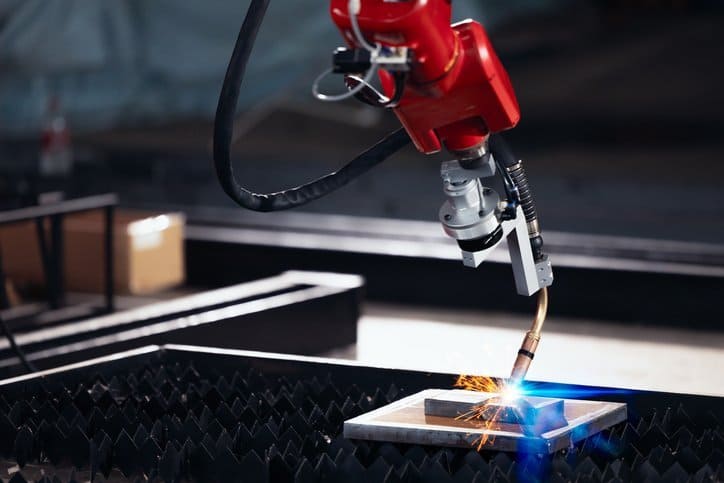
3.Types of laser welding
(i) Heat conduction welding
This method is suitable for thin materials and only melts the surface of the material without deep penetration. The laser energy is absorbed at the surface, resulting in minimal deformation, which is very suitable for applications with high aesthetic requirements, such as welding in jewelry or electronic products.
(ii) Deep penetration (keyhole) welding
This process is used for thicker materials that require deep welding. The laser beam vaporizes the material, creating a “keyhole” effect, which allows deeper penetration of the material and can produce strong welds. It is widely used in industries such as aerospace and automotive manufacturing.
4.Laser types and their selection
(i) CO2 lasers (gas lasers)
CO2 lasers are widely used in industrial welding because of their high power and high efficiency. They produce laser beams through a mixture of gases (usually CO2, nitrogen, and helium). When reliable, cost-effective laser welding of metals is required and some types of lasers are too expensive for large-scale industrial applications, CO2 lasers provide high power output at a lower cost and are suitable for a wide range of applications.
(ii) Solid-state lasers
Solid-state lasers use solid gain media (such as crystals or glasses doped with rare earth elements) to produce laser beams with good beam quality and can be used for welding and cutting applications. When a versatile laser is needed for welding and cutting, and some lasers have limited ability to handle multiple operations, solid-state lasers can provide high beam quality and flexibility.
(iii) Fiber lasers
Fiber lasers use optical fibers as gain media, have excellent beam quality, and are energy-efficient and durable. Because of their high precision, they are often used in industries that require complex welding, such as electronics and medical device manufacturing. Fiber lasers are ideal when a laser with high precision and low maintenance cost is needed, while some lasers have limited precision and require frequent maintenance.
(iv) Disk lasers
Disk lasers are similar to fiber lasers and use a disk-shaped gain medium to provide high power output and excellent precision, making them ideal for heavy industrial applications such as aerospace or automotive manufacturing. When a high-power laser is needed to complete heavy welding tasks, and some lasers cannot effectively handle heavy operations, disk lasers can meet the needs.
5.Advantages of laser welding
(i) High precision
Laser welding has extremely high precision and is suitable for complex parts and components. The laser beam can be focused on a very small area to achieve precise control of the welding process.
(ii) Fast speed
The welding speed is faster than traditional methods, which can improve production efficiency.
(iii) Small deformation
Highly concentrated heat can reduce thermal deformation, which is crucial in industries such as aerospace.
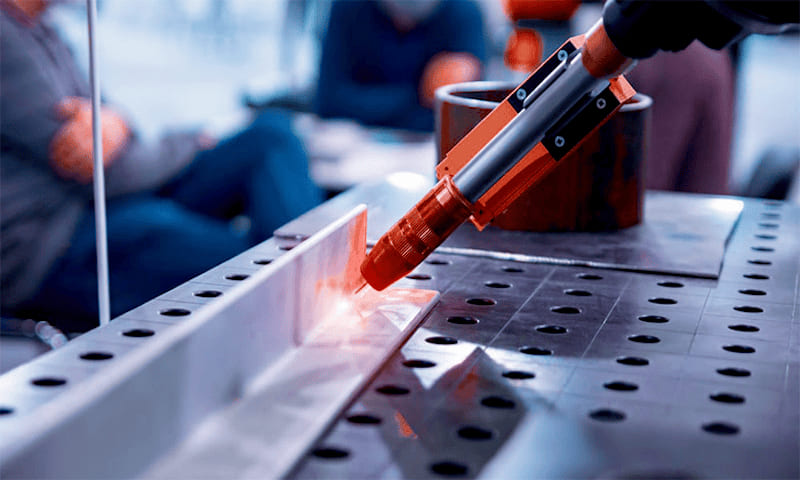
(iv) Strong flexibility
Can connect a variety of materials such as metals and plastics.
(v) Non-contact
As a non-contact process, it can eliminate the risk of contamination and tool wear, achieve cleaner welding, reduce maintenance and tool replacement frequency, and improve overall efficiency.
6.Disadvantages of Laser Welding
(I) High cost
The initial investment of laser welding equipment is large, which may not be feasible for small manufacturers.
(II) Material restrictions
Reflective materials such as copper and aluminum will reduce welding efficiency and require special treatment.
(III) Complex setup
Material alignment requires high precision, which increases setup time.
(IV) Strict joint requirements
High-precision joint preparation is required, and small errors will affect quality.
(V) Limited thickness
Suitable for thin materials, thick materials require multiple welding, which reduces efficiency.
(VI) Safety hazards
High-energy laser beams have safety hazards, and protective measures must be strictly followed.
7.Application of Laser Welding
Laser welding is widely used in various industries due to its versatility and high precision.
Automotive Industry
In the automotive industry, it is used for complex metal components such as body parts and gear parts
Aerospace
In the aerospace field, its high-strength welds and minimal deformation are crucial to aircraft manufacturing
Medical Equipment
In medical equipment manufacturing, precision welding is essential for the production of surgical instruments, pacemakers and other equipment
Electronic Products
In electronic products, it can ensure the clean joints of precision components such as circuit boards and connectors
Jewelry Industry
In the jewelry industry, its fine details and beautiful welds are suitable for gold, silver and platinum designs
Finally
Laser welding is an important technology with high precision, high speed and high flexibility. It is widely used in many industries and is an indispensable process for industries that require both strength and precision. A deep understanding of the characteristics of laser welding technology will help companies improve production quality and efficiency.