Lightweight Metals in CNC Machining
Lightweight metals play a vital role in modern manufacturing. With the increasing requirements of modern manufacturing for product performance, lightweighting has become the goal of many industries such as aerospace and automobiles. Parts made of lightweight metals show excellent characteristics such as high strength, corrosion resistance, and high temperature resistance in these fields, which is of great significance for reducing weight.
In the field of CNC processing, lightweight metals such as aluminum alloys, magnesium alloys, and titanium alloys are widely used. For example, the use rate of aluminum alloys in modern aircraft exceeds 70%. Every kilogram of aircraft weight reduction can significantly save fuel consumption and reduce operating costs. This article will explore in depth the characteristics, advantages, and application cases of common lightweight metals in CNC processing.
1.What are lightweight metals?
Lightweight metals are metals with relatively low density, which means they weigh less per volume. Their specific gravity is generally between 1.5 and 5.0 g/cm3, which is lower than common engineering materials such as steel (about 7.85 g/cm3). This property is extremely valuable in industries such as aerospace, automotive, and consumer electronics, where it helps reduce weight to improve performance and fuel efficiency.
2.Commonly used lightweight metals for CNC machining
(i)Aluminum alloy
Aluminum alloy has good corrosion resistance because a dense oxide film is formed on its surface, which can block oxygen and moisture from contacting the internal metal and slow down corrosion. In CNC machining, if the surface is properly treated, such as forming a thicker and stronger oxide film through anodizing and other methods, the corrosion resistance can be further improved and the product life can be greatly extended.
Features
The density is 2.7 g/cm3, the strength-to-weight ratio is high, the corrosion resistance is excellent, and the machinability is easy.
Advantages: Aluminum can provide important structural support without significantly increasing the weight, and is an ideal choice for applications in wet environments such as outdoor and marine environments. In addition, there are a variety of alloys (such as 2024, 6061 and 7075) to choose from for specific applications.
Application areas
Widely used in aerospace components (such as aircraft frames, wing structures), automotive parts (such as wheels, engine blocks), sports equipment (such as bicycle frames), and electronic product housings (such as laptops, mobile devices).
(ii)Titanium Alloy
Titanium is strong and stronger than many traditional metals (such as steel), but much lighter, making it an ideal material for high-strength and low-weight applications (such as the aerospace industry). In CNC machining, its high strength can produce thinner and stronger parts, reducing the overall weight, while its good toughness allows it to withstand machining stress and is not easy to break. Titanium has a strength of more than 1000MPa, which is several times that of ordinary steel. Titanium parts perform reliably under high loads, ensuring product safety.
Features
Features: Density 4.43 g/cm³, high tensile strength, excellent corrosion resistance, difficult machinability, and requires special tools.
Advantages: Titanium has a higher unit weight strength than most metals, is suitable for high-stress applications, can maintain strength at high temperatures, and its natural oxide layer has excellent corrosion resistance (especially in salt water and acidic environments).
Application Areas
Used in aerospace (such as turbine engines, structural components), medical (such as implants, prostheses), ships (such as propeller shafts, accessories), and high-performance automobiles (such as exhaust systems).
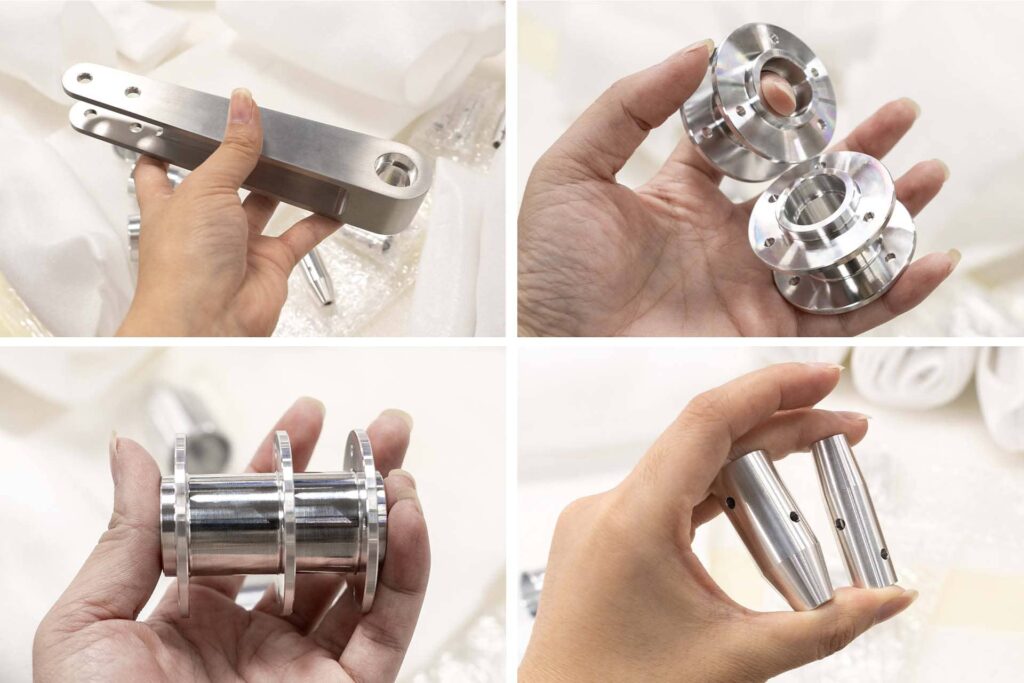
(iii)Magnesium alloy
Magnesium is the lightest structural metal currently available and is very attractive for weight-sensitive industries. However, compared with aluminum and titanium, magnesium alloys are more difficult to process and are more susceptible to corrosion if not handled properly.
Features
Features: Density 1.738 g/cm³, medium strength-to-weight ratio (lighter but weaker than aluminum), medium corrosion resistance (requires coating or alloy to improve corrosion resistance), medium machinability (caution required due to flammability).
Advantages: Magnesium has a low density and is the first choice for weight-reducing key applications. Although it is weaker than aluminum and titanium, it still has good strength in many applications and is more cost-effective than some lightweight materials.
Application areas
Applied in automobiles (such as engine blocks, gearboxes), aerospace (such as aircraft seats, brackets), and consumer electronics (such as laptop cases, mobile devices).
(iv)Beryllium
Beryllium is an advanced lightweight metal that is often used in highly specialized applications. It is more expensive and difficult to process than aluminum or titanium, but its unique properties make it extremely valuable in specific industries. Beryllium has high strength, low density and excellent thermal properties, making it the material of choice for high-performance applications.
Characteristics
Characteristics: Density 1.848 g/cm³, very high strength (stronger than many other lightweight metals), high corrosion resistance (especially at high temperatures), difficult machinability (specialized equipment and safety precautions required).
Advantages: Beryllium is stronger than other lightweight metals and stable at high temperatures. It can be used in high-performance thermal systems such as heat exchangers. Its high hardness makes it an ideal material for making precision parts.
Applications
Used in aerospace (such as satellite components, structural parts), nuclear energy (such as reactors, radiation shielding), and electronic products (such as connectors, electrical contacts).
(v) High-strength steel alloys (such as 4130, 4340)
Strength and weight characteristics
Although steel is generally heavier than other lightweight materials, some high-strength steel alloys have a good balance between strength and weight, especially for parts that are subjected to extreme pressure and wear. The high strength of steel makes it an ideal choice for heavy machinery and structural parts.
Features
Features: Density 7.85 g/cm³ (heavier than other lightweight metals), very high tensile and yield strength, moderate corrosion resistance (requires coating or treatment), moderate to difficult machinability (may require specialized tools).
Benefits: Steel alloys such as 4130 (chrome-molybdenum steel) and 4340 (nickel-chrome steel) have very high tensile strength, steel is cheaper than exotic materials such as titanium or beryllium, and is wear-resistant and can be treated to increase toughness.
Applications
Used in landing gear, structural components and fasteners, roll cages, chassis components and suspension systems, and heavy machinery and tools requiring high strength.
3.Considerations for selecting lightweight metals
Selecting lightweight metals for CNC machining requires comprehensive consideration of factors such as strength requirements, corrosion resistance, machinability, and cost.
Aluminum alloys have balanced properties and are commonly used materials; titanium alloys have excellent strength and high temperature resistance, but are expensive; magnesium alloys are suitable for weight-sensitive applications; and beryllium is suitable for highly specialized applications.
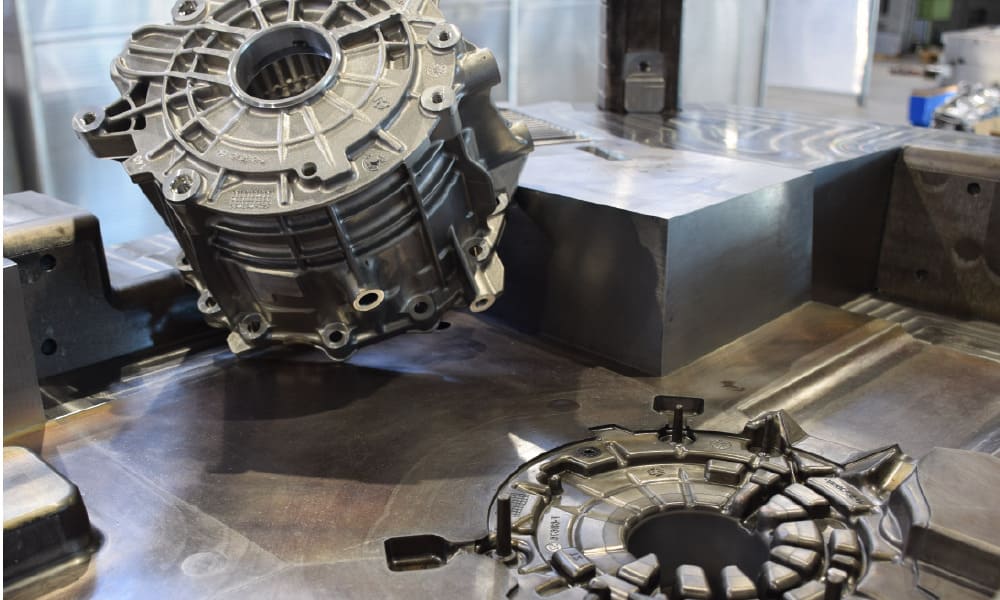
4.Reasons for choosing lightweight metals
(i) Improve fuel efficiency and performance
In industries such as aerospace, automotive and transportation, using lightweight metals to reduce product weight can directly improve fuel efficiency and performance. Lightweight metals such as aluminum, magnesium and titanium can reduce the total weight of the final product and reduce the energy required to move or operate it.
(ii) Corrosion resistance and long life
Lightweight metals such as aluminum, titanium and magnesium alloys have excellent corrosion resistance, which is essential for material applications exposed to harsh environments. Good corrosion resistance can extend the service life of the product and reduce long-term maintenance and replacement costs.
(iii) Improve machinability
Lightweight metals are often selected for machinability, that is, the ease with which the material can be processed in processes such as CNC machining, milling and turning. Many lightweight metals (such as aluminum) have relatively simple machining requirements, which can shorten production time and reduce labor costs.
(iv) Sustainability and
Sustainable development is becoming increasingly important in various industries, and lightweight metals can help improve the environmental credentials of projects. Reducing the weight of products can improve energy efficiency during use and reduce the impact of transportation and production on the environment.
(v) Versatility
Lightweight metals are widely used in a variety of industries. Whether it is durable components in high-tech industries or lightweight materials for consumer products, they can meet a variety of needs.
(vi) Specific applications
Lightweight metals can often be alloyed with other materials to enhance specific properties. For example, aluminum can be alloyed with copper, magnesium or silicon to improve strength, corrosion resistance or thermal conductivity, allowing manufacturers to choose the ideal material based on project requirements.
Lightweight Metal Comparison Table
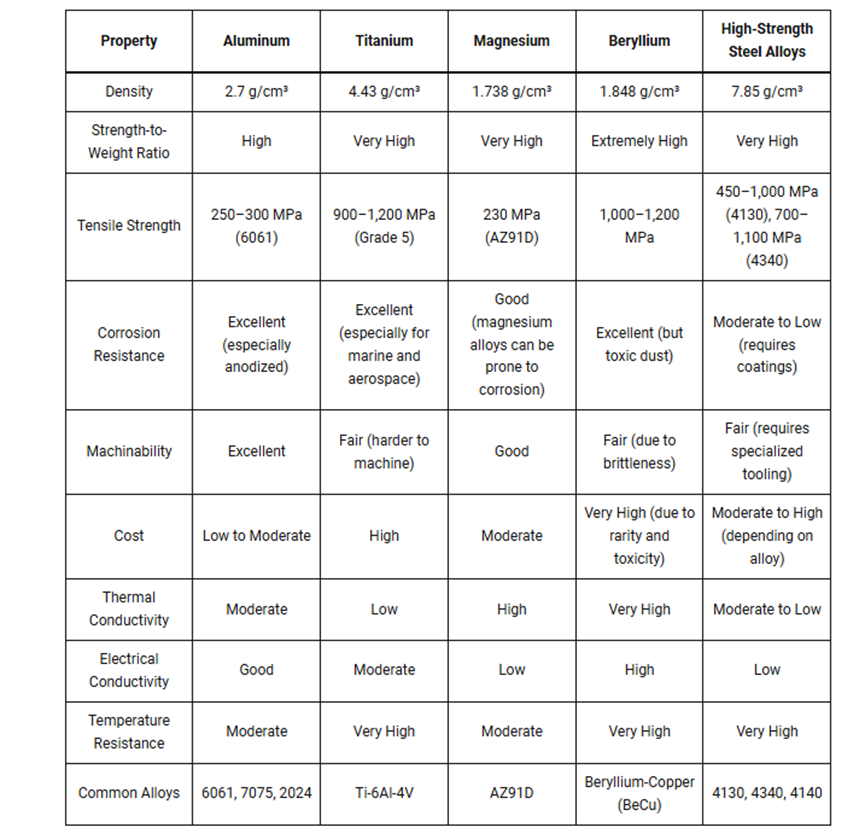
Conclusion
Choosing lightweight metals for CNC machining requires a combination of factors, including performance requirements, environmental conditions, and machinability. Metals such as aluminum, titanium, and magnesium have their own advantages in different applications, and manufacturers can carefully evaluate these factors to select the ideal material to achieve a balance of strength, weight, and cost. If in doubt, consult with Xavier CNC machining professionals to ensure that the right metal is selected for optimal performance and efficiency.