Techniques for Enhancing the Machinability of Aluminum Alloys
Aluminum is widely used in various industries due to its excellent properties such as low density, high strength-to-weight ratio, and good corrosion resistance. It is used in a variety of parts including spare parts for washing machines, tyre changing machine parts, and washing machine replacement parts. However, one challenge manufacturers face when using aluminum is its poor machinability.
Aluminum alloys can be difficult to machine, resulting in increased tool wear, poor surface finish, and reduced productivity. To overcome these challenges, a variety of techniques can be used to enhance the machinability of aluminum alloys.
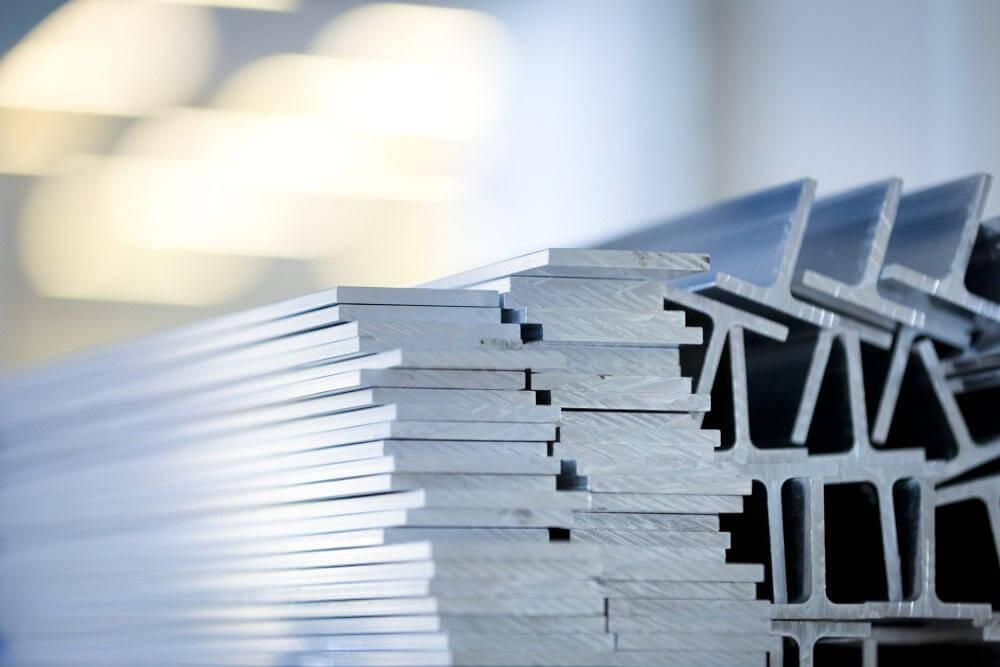
What are the technologies to improve the machinability of aluminum alloys?
One technique that can improve the machinability of aluminum is alloying. Because by adding certain elements to aluminum alloys, its machinability can be significantly enhanced. For example, adding small amounts of lead or bismuth can improve chip formation and reduce tool wear. At the same time, these elements can also act as lubricants during processing to reduce friction between the tool and the workpiece. In addition, adding sulfur can also improve machinability by forming a lubricating film on the tool surface.
Another technique for enhancing the machinability of aluminum alloys is heat treatment. Heat treatment involves heating the material to a specific temperature and then cooling it at a controlled rate. This process can improve the mechanical properties of the alloy, making it easier to machine. For example, solution heat treatment followed by aging can increase the strength and hardness of the alloy, reducing tool wear and improving surface finish during machining.
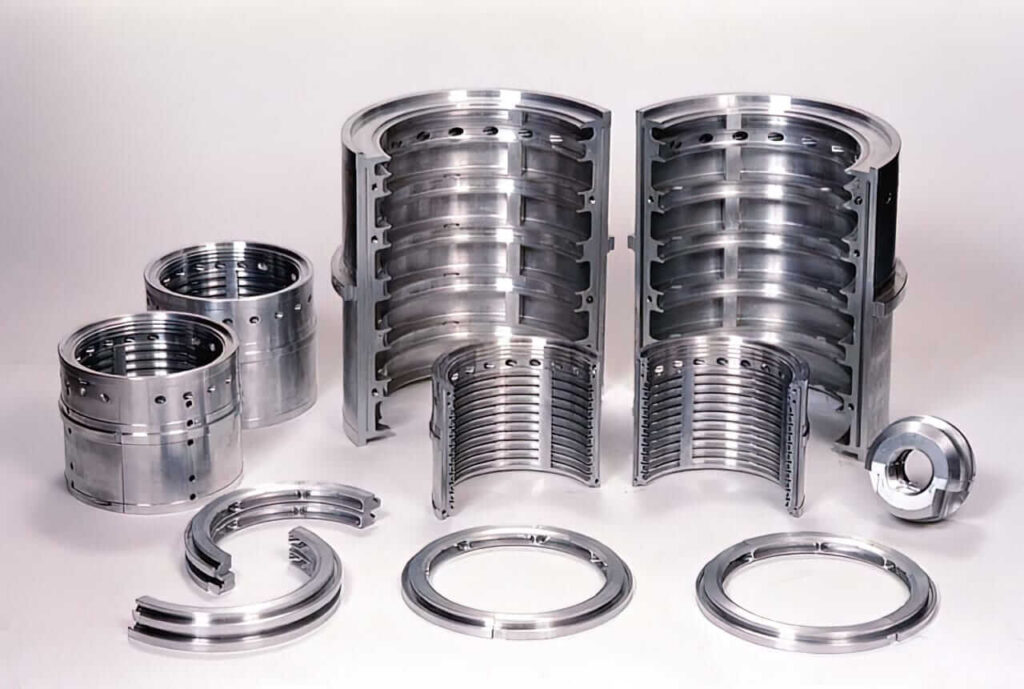
Furthermore, the use of cutting fluids can greatly improve the machinability of aluminum alloys. Cutting fluids act as coolants and lubricants, reducing heat generation and friction during machining. They also help to flush away chips and debris, preventing them from interfering with the cutting process. When selecting a cutting fluid for machining aluminum, it is important to choose one that is compatible with the alloy and provides adequate lubrication and cooling properties.
In addition to alloying, heat treatment, and cutting fluids, optimizing cutting parameters is crucial for improving the machinability of aluminum alloys. Cutting parameters such as cutting speed, feed rate, and depth of cut can greatly influence the machinability of the material. High cutting speeds and feed rates can lead to increased tool wear and poor surface finish, while low cutting speeds and feed rates can result in inefficient machining. Finding the right balance between these parameters is essential for achieving optimal machinability.
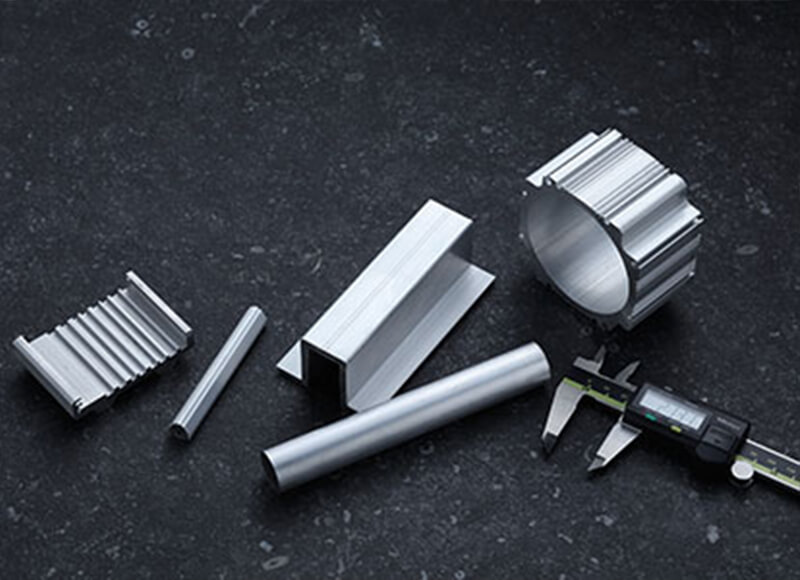
Lastly, the use of advanced cutting tools can also enhance the machinability of aluminum alloys. Carbide and ceramic cutting tools are commonly used for machining aluminum due to their high hardness and wear resistance. These tools can withstand the high cutting temperatures generated during machining and maintain their sharpness for longer periods, resulting in improved tool life and surface finish.
In conclusion, the machinability of aluminum alloys can be improved through various techniques. Alloying, heat treatment, the use of cutting fluids, optimizing cutting parameters, and using advanced cutting tools are all effective methods for enhancing the machinability of aluminum. By implementing these techniques, manufacturers can overcome the challenges associated with machining aluminum and achieve higher productivity, better surface finish, and reduced tool wear.