Factors that Influence Machining Large Parts
Large part machining is a great example. CNC machines can complete small, simple parts with minimal supervision, but require the help of an experienced machinist to handle more challenging operations. Twin-column machining centers are ideal for manufacturing large parts. K&M machining is able to produce custom large machine parts and fabrications.
When a workpiece is too large to fit in an enclosure, or requires additional support to prevent deformation, a creative machine shop can often find alternatives to get the job done in unexpected ways.
This article describes some common challenges encountered when machining large parts, as well as some potential solutions employed by resourceful machine shops.
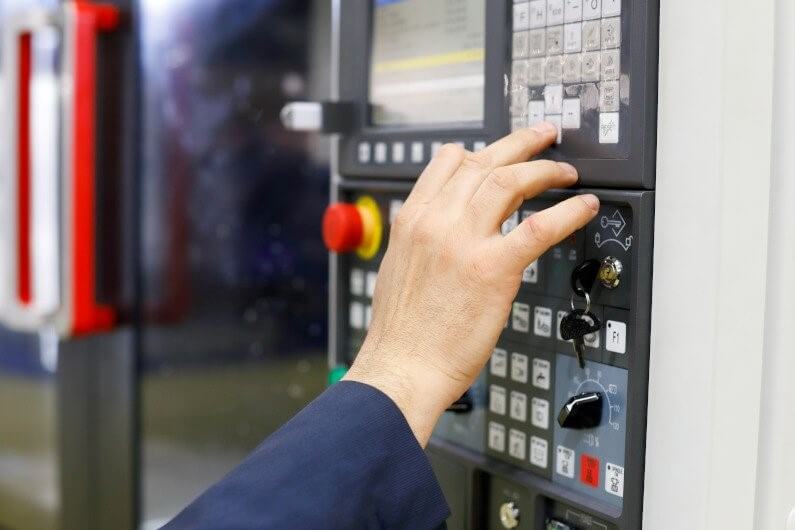
1.Common problems and solutions when machining large parts
① The working area is not large enough
The range of motion of the equipment cannot reach all the parts that need to be machined. Either the part is too large or the machine’s function is too small.
② Solution
- Work in sections
Process all parts in one area, then reposition the workpiece so that a new area can be accessed. Even custom fixtures and brackets can be used to make sliding or rotating the workpiece easier and more accurate. - Use different machinery
Machine shops have a wide variety of equipment to complete specialized operations. In some cases, it is sufficient to use different machinery with different functions to complete the job.
③ Too big for the enclosure
The workpiece is too tall, too long, too wide, or too large. It may be that there is not enough room under the processing head, or the workpiece is too long to fit within the baffle on the machine. It may also be that the heavy workpiece exceeds the weight capacity of the equipment.
④ Solution
- Decomposition
Although not possible in all cases, some parts can be broken down into smaller components. It may even be possible to complete the operation simultaneously on different machines to speed up processing time. It is best to address this issue during the design phase of the part. - Modify the machinery
Can the tooling head be replaced with a shorter one to provide more clearance? Can obstacles be removed to allow the part to extend beyond the normal limit? This approach can expand the capabilities of the equipment, but it requires additional planning to prevent damage to the equipment and parts. Consider using CAD tools to detect problems ahead of time. Extra precautions may also be required to ensure the safety of workers. - Introduce external supports
If the part is unbalanced, it will cause tolerance problems. If a part exceeds the load-bearing capacity of the equipment, it may also damage the equipment or cause safety hazards. Additional supports can reduce mechanical loads and stabilize the workpiece.
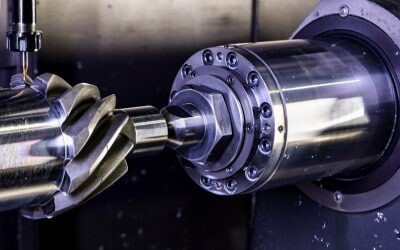
⑤ Design tolerances are not met
After machining, the part does not meet the quality requirements of precision machining. Perhaps the worker did not reposition the workpiece correctly between operations, or the individually machined parts were not aligned. Perhaps large, bulky parts are difficult to fix and move during the machining operation.
⑥Solutions
- Take your time
Spend extra time planning to prevent mistakes, and double-check to ensure that the workpiece is properly positioned and fixed. Although this will increase machining time, experienced machinists know that the labor and material costs of rework are not worth the cost of saving a few minutes.
- Use semi-finishing
Machining large parts requires extra care and patience. Especially when tolerances are tight, additional machining between roughing and finishing can help ensure precision and accuracy.
⑦Feature distortion
When exposed to extreme heat and dynamic forces, parts can deform and distort. The high thermal stress generated by machining large parts can cause the metal to expand unevenly. If it is processed as designed in the expanded state, it is likely to be out of tolerance after cooling. Additionally, for CNC lathes, long, unbalanced parts can cause wobble due to bending out of position, resulting in distorted profiles and poor surface finish.
⑧Solutions
- Plan for expansion
Implement additional supports under vulnerable areas and ensure that the workpiece is balanced to ensure accuracy. - Control heat input
Experienced machinists know that thermal expansion is a greater challenge for large parts. Machining large parts may require you not to remove too much material in each operation to reduce heat input. Also make sure to use the right coolant and ensure it has good flow in the cutting area.
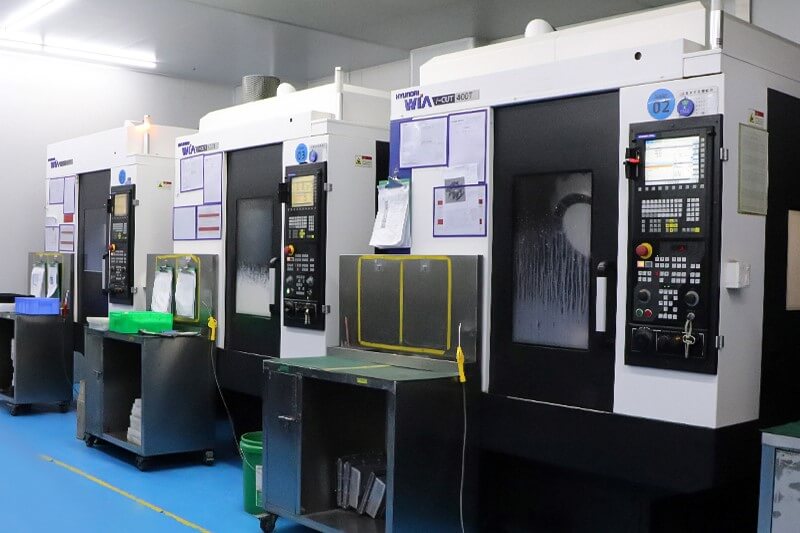
2.Meet the challenges of machining large parts
Machining large parts is undoubtedly a challenge. The impact of errors and inaccuracies is magnified, so the cost of repair is much higher than that of repairing small parts. At least for now, computers and robots alone cannot cope with the subtle challenges of oversized workpieces.
Machining large parts requires patience and careful planning, and for some machine shops, it may not be worth the risk. But it also provides a chance for top machine shops to show their expertise and resourcefulness. Xavier has the ability to handle parts of various shapes, sizes and materials.