A comprehensive guide to machining magnesium
Machining magnesium has taken off because magnesium is a versatile material that is well suited for a variety of applications across a wide range of industries. However, while you can use magnesium alloys to produce high-quality parts with excellent corrosion resistance, magnesium is extremely flammable during CNC machining operations.
Therefore, taking the necessary precautions can help you machine magnesium safely. Taking appropriate care in machining magnesium can help mitigate any safety risks.
1.Risks of machining magnesium
There are some threats that must be handled with caution when machining magnesium alloys. You should be aware of some of the risks of CNC magnesium machining.
1) Fire Hazards
The fine chips and dust produced when machining magnesium alloys are extremely flammable and can easily cause fires. Overheating or small sparks generated during machining can cause fires.
2) Tool Wear
Because magnesium alloys are relatively soft and abrasive, the tool wear rate during CNC machining will be faster than other metal materials, resulting in a significant reduction in machining efficiency and an increase in tool replacement costs.
3) Heat
Magnesium has poor thermal conductivity, and heat is concentrated in the cutting area. Excessive cutting temperatures can reduce tool life, cause workpiece deformation, and tool wear, etc.
4) Surface Finish Deformation
Magnesium alloys are often prone to burr formation and machining distortion. Therefore, it is difficult to achieve the desired high-quality surface finish without proper machining strategy and tool selection.
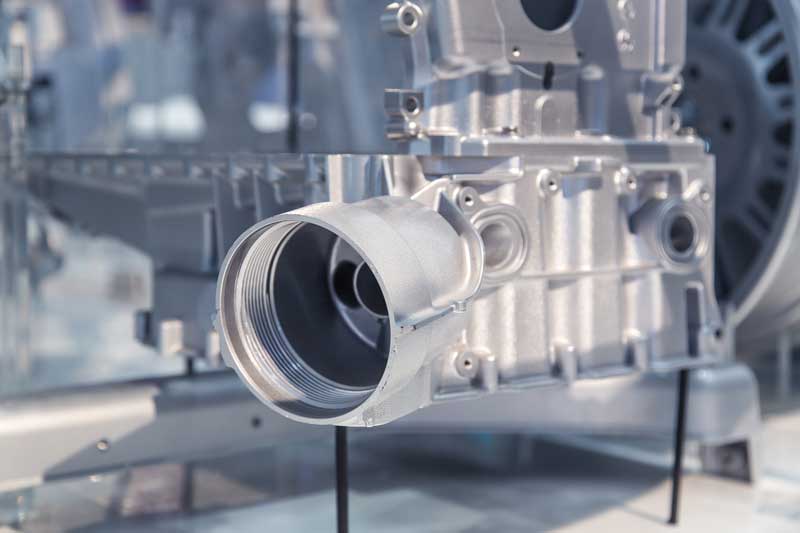
2.Top Tips for Safely Machining Magnesium Alloys
CNC precision machining is a versatile process for safely machining magnesium if necessary precautions are taken. Here are some tips for safely machining magnesium.
1) Maintain Proper Tool Condition
Using sharp cutting tools in magnesium CNC machining helps reduce the danger because dull tools can cause extreme heat. Therefore, it can ignite the chips generated by the CNC machining operation.
However, carbide tools retain their hardness and are less likely to produce sparks when machining magnesium at higher temperatures.
2) Avoid Small Clearance Angles
It is recommended to avoid using small clearance angles when machining magnesium alloys, even if you can machine at higher speeds without compromising the quality of the part. Machining with small clearance angles creates longer, full chips that can easily entangle the rotating cutting tool.
Therefore, this can lead to high heat buildup, and the flammability of magnesium alloys can cause a serious fire hazard.
3) Create discontinuous chips
Check the size and type of chips produced during magnesium CNC machining. A general rule of thumb is to program your CNC machine to produce either well-broken or discontinuous chips.
Discontinuous chips help to effectively dissipate heat from the cutting tool and workpiece surface, thereby reducing the risk of ignition.
Program your cutting tool to use a small rake angle so that good chip formation occurs. Then, use low feed rates and medium to high cutting speeds.
However, you can also achieve discontinuous chips with larger depths of cut.
4) Avoid using water-based coolants
If your project does not use a small rake angle, low feed rates, or medium cutting speeds, CNC magnesium machining may generate excessive heat. Therefore, you must use mineral oil coolants in your machining. These coolants mitigate fire and explosion risks and improve the surface quality of magnesium machined parts.
However, water-based coolants are not recommended when machining magnesium alloys. These water-based coolants may react with magnesium to produce highly flammable hydrogen gas.
5) Use explosion-proof vacuum cleaners to suck up chips
Even if the machining parameters required to create discontinuous chips are followed, discontinuous magnesium chips generated during machining can still be dangerous. Advanced CNC machining shops now use explosion-proof vacuum systems and extractors to safely remove magnesium chips and dust from CNC machines.
6) Never use water to extinguish a magnesium fire
Whenever a magnesium combustion fire accident occurs during machining, it is not recommended to extinguish it with water. This is not an ideal option because using water will only increase the severity of the fire.
Therefore, you can use a dry Class D fire extinguisher to quickly control a magnesium fire. Similarly, dry sand is also an easy alternative if you want to put out a small fire.
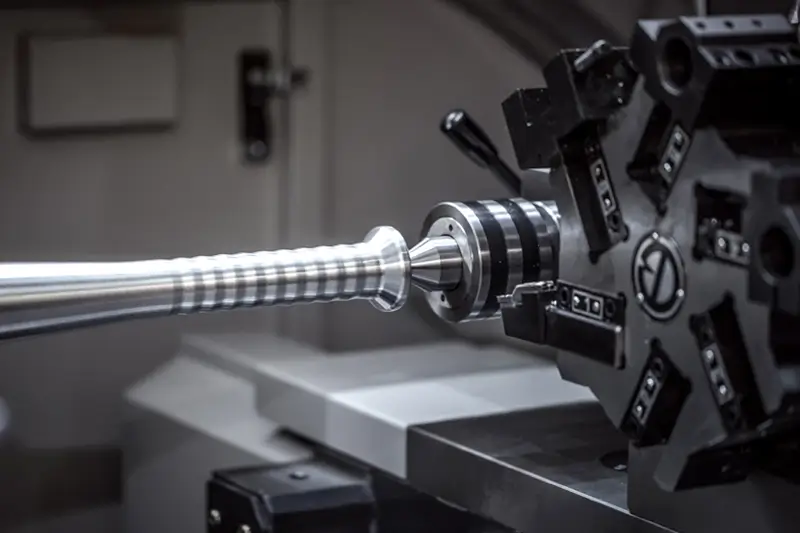
3.Why choose magnesium for CNC machining?
Given the risks of CNC magnesium machining, why use it? This is a reasonable question. However, if you follow safety guidelines, magnesium is an ideal choice for CNC machining.
Magnesium is a lightweight structural metal with excellent surface finish and machinability. There are several typical reasons to choose magnesium for CNC machining.
1) Excellent Machinability
Since magnesium alloys have excellent machinability, it is easier to cut and shape magnesium alloys using CNC machining processes. Magnesium alloys have low cutting forces, which reduces the wear rate of cutting tools.
Complex Geometries
Since magnesium alloys are highly machinable, they are ideal for machining custom parts with complex geometries. In addition, CNC magnesium machining can provide magnesium parts with precise and complex features that meet the stringent requirements of modern engineering projects.
CNC machining does not make any errors when machining according to programming instructions, allowing magnesium alloy parts to be manufactured with microscopic precision.
In addition, multi-axis CNC machine tools have machining centers with multiple axes that are able to machine magnesium alloys from different angles to meet requirements.
2) Recyclability
Magnesium materials can be recycled; magnesium alloys are environmentally friendly. Therefore, magnesium is an ideal material for sustainable manufacturing operations. Likewise, CNC machining procedures produce magnesium waste that can be recycled.
4.Tool Selection for Machining Magnesium
Choosing CNC cutting tools is a key factor to consider when machining magnesium alloys. Sharp tools must be used to avoid excessive heat generation during machining operations. The following are typical tools used when machining magnesium alloys.
1) High-speed steel tools
Made from hardened steel alloys, high-speed steel tools are ideal for machining applications with less demand and low to medium manufacturing scale. High-speed steel tools are inexpensive, readily available, and have the low cutting speeds required to cut magnesium materials.
2) Solid carbide tools
Solid carbide end mills, reamers, and drills are widely used as magnesium alloy CNC machining tools due to their excellent heat resistance and high hardness. These carbide tools have excellent wear resistance and good heat resistance, making them ideal for demanding magnesium alloy machining applications.
3) Coated carbide tools
Cutting tools with special coatings such as titanium aluminum nitride (TiAlN) or titanium nitride (TiN). The thin coating on these tools enhances their wear resistance, thereby mitigating the formation of built-up edge when machining magnesium.
In addition, these coated tools exhibit impressive thermal stability, allowing them to perform well despite the high temperatures generated during magnesium machining.
4) Polycrystalline Diamond Tools
These tools have excellent wear resistance and are ideal for machining magnesium machined parts with a high-quality surface finish. Machinists often use these tools to machine magnesium alloys because they are very effective in machining hard materials or highly abrasive magnesium alloys.
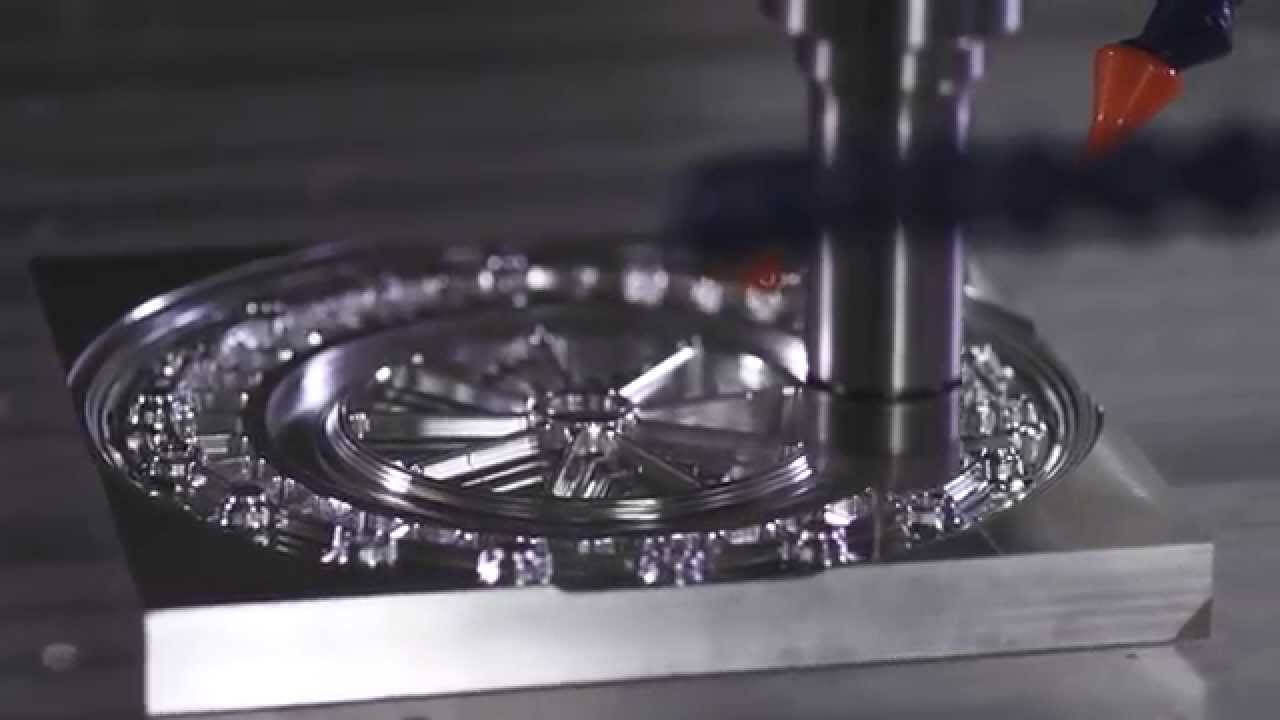
5.Various CNC Machining Methods for Magnesium Alloys
CNC machining methods can effectively cut magnesium to create a variety of parts for different applications.
1) CNC Drilling
CNC drilling is a common method of drilling holes in magnesium workpieces using a rotating tool or drill. Most applications require precise drilling, and CNC machines provide the high accuracy required to make complex hole patterns.
2) CNC Milling
CNC milling is one of the common CNC machining techniques used for magnesium materials. This method uses a rotating tool to create the preferred shape when milling magnesium. CNC milling is efficient and is ideal for machining simple and complex geometries.
3) CNC Turning
The CNC turning method involves cutting material from a rotating magnesium alloy material clamped in a chuck. This method is ideal for machining cylindrical shapes such as pins, shafts, and threaded parts.
4) Laser Cutting
This is another common method for machining magnesium. It uses a high-powered laser to make precise cuts in magnesium sheets or plates. Laser cutting is ideal for making thin and complex parts quickly and efficiently.
5) Tapping
Tapping is a tried-and-true method for machinists to create internal threads in machined magnesium alloy parts. CNC machining helps automate this method. As a result, you can achieve precise thread sizes and pitches.
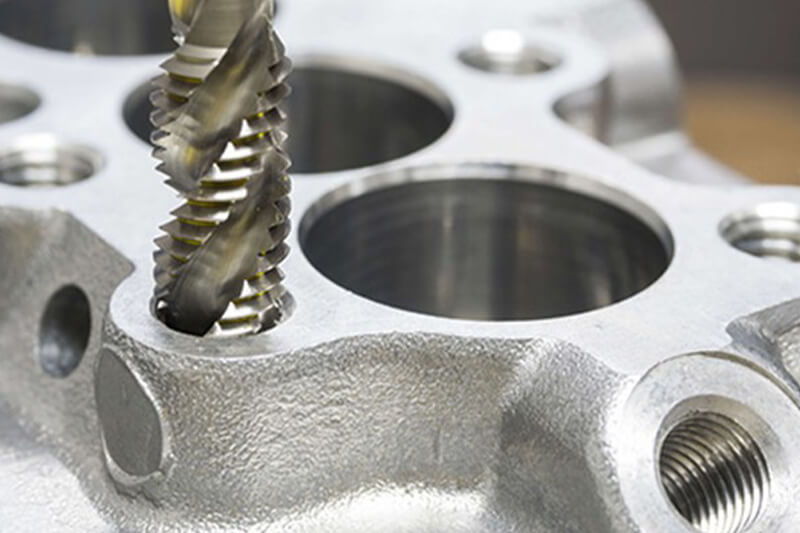
6.Conclusion
Machining magnesium alloys produces lightweight parts with high strength, high impact resistance, and good dimensional stability. However, there are a variety of magnesium alloy CNC machining processes that can be used to manufacture parts for a variety of uses.
Despite magnesium’s excellent machinability and the wide range of uses for CNC machining, machining magnesium also presents inherent dangers. Therefore, understanding how to machine magnesium alloys will help ensure safety during machining operations.