Machining Parts: The Secrets of Production
As the backbone of modern industry, parts machining can produce precise and complex parts for various fields. In this article, we will explore the concept of “part machining” in depth and discuss different machining methods, industry applications, important considerations and latest technological developments.
1.Methods and applications of machining parts
Machining is the process of removing materials with cutting tools to produce parts of desired shapes and sizes. The process can be applied to metals, plastics, composites and other materials.
Machining parts are widely used in various industries from prototyping to mass production and play an important role in many fields such as automotive, aerospace, medical, energy, etc.
Machining processes are basically divided into two categories:
- Machining: The process of removing chips by cutting materials. Operations such as turning, milling, grinding and drilling are all machining methods.
- Chipless machining: This is the process of forming without cutting materials. Water treatment processes such as laser cutting, water jet cutting and electro-erosion are all chipless machining methods.
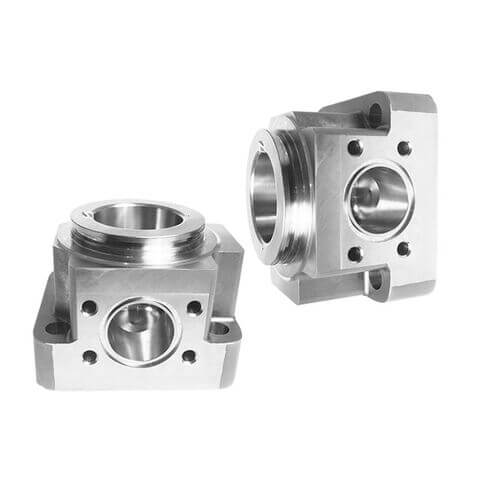
2.CNC machining: Computer-aided machining of parts production
CNC (computer numerical control) machining is controlled by computer software and is the process of machining parts using automated machine tools. The technology is characterized by high precision, repeatability and efficiency. CNC machines can produce parts with complex geometries and minimize human errors.
The advantages of CNC machining parts are:
- High precision and repeatability: CNC machines are able to manufacture parts accurately within the specified tolerances.
- Production of complex geometries: CNC machines can produce parts with complex geometries that are difficult to produce with traditional methods.
- High productivity: CNC machines operate automatically, so productivity is high.
- Flexibility: CNC machines can be easily used to produce different part designs.
3.Processing parts of different materials: metals, plastics and composites
The processing technology can be adapted to different material properties. Each material has its own machinable characteristics.
- Metals: Metals such as steel, aluminum, titanium and brass are often used in applications that require high strength and durability.
- Plastics: Plastics such as ABS, nylon, polycarbonate and PTFE are favored for their light weight and low cost.
- Composite materials: Composite materials such as carbon fiber, fiberglass and Kevlar have advantages such as high strength, light weight and corrosion resistance.
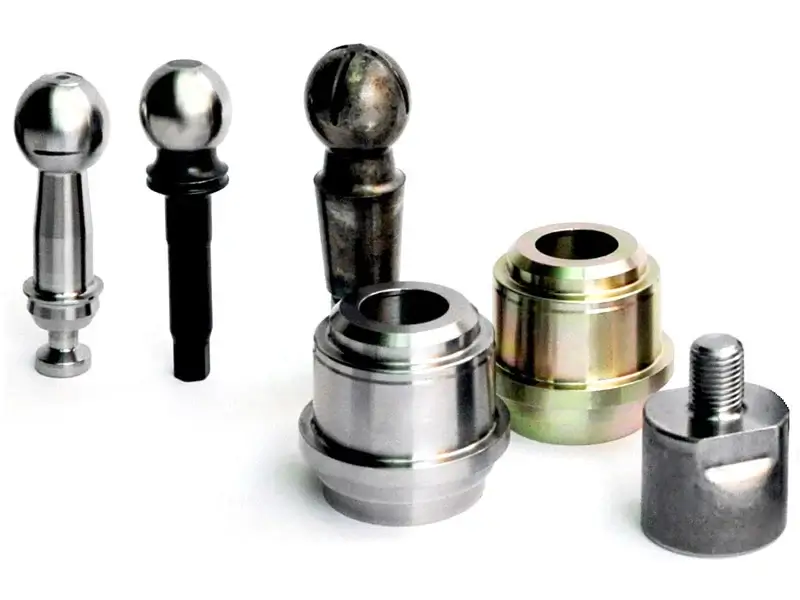
4.Machining tolerances: the importance of precision and measurement methods
During the machining process, the machining parts must be produced within a certain tolerance range. The tolerance determines the acceptable size and geometric variation of the part. Precision measuring instruments are used to check whether the part meets the tolerance.
Commonly used measuring instruments are:
- Micrometer: used to measure the outer diameter of the part.
- Caliper: used to measure the inner diameter, outer diameter, depth and length of the part.
- Profile projector: used to view and measure the profile of the part in a magnified form.
- Coordinate measuring machine (CMM): used to measure the three-dimensional measurement of the part.
5.Lathe machining: producing rotationally symmetric machining parts
Lathes are used to create cylindrical or conical shapes by cutting rotating workpieces. This process is widely used to produce shafts, bushings, gears and other rotationally symmetric machining parts.
The turning process may involve different operations, such as:
- Roughing: used to quickly remove large amounts of material from the workpiece.
- Finishing removal: used to improve surface quality and make precise dimensioning.
- Threading: used to drill threads on a workpiece.
- Drilling: used to drill holes in a workpiece.
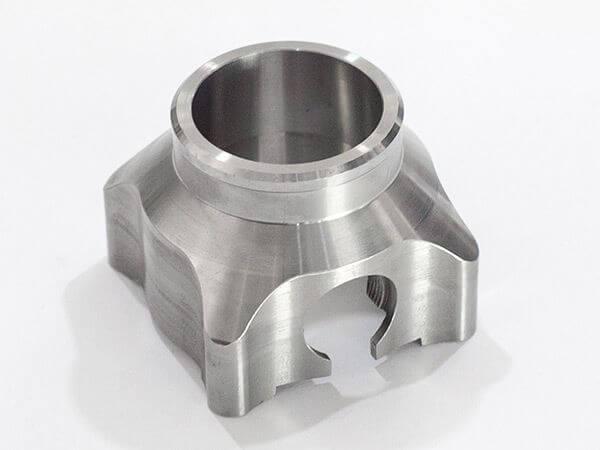
6.Milling: Creating machined parts with complex geometries
Milling machines use rotating cutting tools to create flat or curved surfaces, grooves, slots, and other complex geometries. Milling is used to produce molds, fixtures, and other special parts.
The milling process may involve different operations, such as:
- Face milling: used to create flat or curved surfaces.
- Pocket milling: used to create pockets or slots on a workpiece.
- Contour milling: used to create complex contours.
7.Grinding: Improving the surface quality and precise dimensions of machining parts
The grinding process is to use a grinding wheel to grind the material to improve the surface quality and precise dimensions of the machined parts. This process ensures the finishing accuracy of the machined parts that need grinding.
The grinding process includes the following different types:
- Surface grinding: used to grind flat or curved surfaces.
- Cylindrical grinding: used to grind cylindrical parts.
- Centerless Grinding: Used for grinding parts that are not rotationally symmetrical.
8.Drilling and Machining: Drilling and Reaming Techniques
Drilling and machining operations are the use of tools such as drills, reamers, and taps to drill and ream holes. These operations are used to create mounting holes, threaded holes, and other special holes.
Drilling and machining operations include the following different types:
- Drilling: The most common method of drilling holes.
- Reaming: Used to increase the size and surface finish of a hole.
- Tapping: Used to thread a workpiece.
9.Machining in the Aerospace Industry: High-Performance Machining Parts
The aerospace industry requires parts with properties such as high strength-to-weight ratios, corrosion resistance, and high temperature resistance. Machining is used to manufacture turbine blades, landing gear, and other critical components used in the industry.
Common materials used for machining parts in the aerospace industry include:
- Aluminum alloys: Lightweight and corrosion-resistant.
- Titanium alloys: High strength, light weight, and high temperature resistance.
- Nickel alloys: High temperature and corrosion resistance.
10.Machining in the Automotive Industry: Engine and Transmission Machining Parts
In the automotive industry, parts such as engine blocks, cylinder heads, pistons, crankshafts, and transmission gears are produced by machining. These parts require high strength, wear resistance, and precise tolerances.
Commonly used materials in the automotive industry include:
- Steel: has high strength and durability.
- Aluminum alloy: light weight and corrosion resistance.
- Cast iron: has wear resistance and shock absorption properties.
11.Machining in Medical Device Manufacturing: Precision and Sterile Machined Parts
Medical device manufacturing requires precision and sterile machined parts such as implants, prostheses, and surgical instruments. Machining can be applied to titanium, stainless steel, and other biocompatible materials used in the production of these parts.
Commonly used materials in medical device manufacturing include:
- Titanium: has biocompatibility, corrosion resistance, and high strength-to-weight ratio.
- Stainless steel: biocompatible, corrosion-resistant, and suitable for sterilization.
- Cobalt-chromium alloy: has high strength and wear resistance.
12.Machining in the Energy Sector: Turbine and Pump Machining Parts
Machining is used to produce turbine blades, pump casings, and other critical machined parts in the energy sector. These parts must be resistant to high temperatures, high pressures, and corrosion.
Commonly used materials in the energy sector are:
- Stainless steel: resistant to high temperatures and corrosion.
- Nickel alloys: resistant to high temperatures and corrosion.
- Titanium alloys: high strength, light weight, and resistant to high temperatures.

13.Factors affecting the cost of machining parts
The cost of machined parts depends on factors such as part geometry, material selection, machining time, tolerances, and quantity. Complex geometries, difficult-to-machine materials, and tight tolerances increase costs.
14.Quality control during machining
Quality control during machining is important to ensure that machined parts meet specified tolerances and specifications. Measuring instruments, visual inspection, and other test methods can be used for quality control.
Quality control methods are as follows:
- Visual inspection: used to check the surface quality and visible defects of parts.
- Dimensional measurement: used to check whether the dimensions and tolerances of parts meet the requirements.
- Material testing: Checking material properties and standards compliance to get the most out of it.
15.Latest developments in machining technology
- Multi-axis machining: Machines with five or more axes allow parts with complex geometries to be machined in a single setup.
- High-speed machining: Cutting tools operating at high speeds reduce machining time and improve surface quality.
- Laser machining: A process that uses a laser beam to cut or engrave materials. It can be used to create precise and complex geometries.
- Additive manufacturing (3D printing): A process that produces parts by adding material layer by layer. It is used for prototyping and the production of custom parts.
If you are looking for an experienced CNC machining manufacturer, Xavier is your ideal choice. The Xavier team is well-equipped to provide high-quality CNC machining solutions. If you need more information or to discuss your machining needs with us, please feel free to contact us.