Why do burrs appear during machining and how to solve them?
There are small protruding particles on the surface of the workpiece, especially at the edges, and there may be hook-shaped protrusions. Including zero turn parts, that is, zero turn mower parts, you can also think of toro zero turn mowers parts.
1.Causes of burrs during machining
Metal materials have ductility, toughness, and plasticity, properties that cause metals to deform unevenly during CNC machining. In particular, ductility will hinder cutting and cause burrs on escaped parts such as toro zero turn mowers parts.
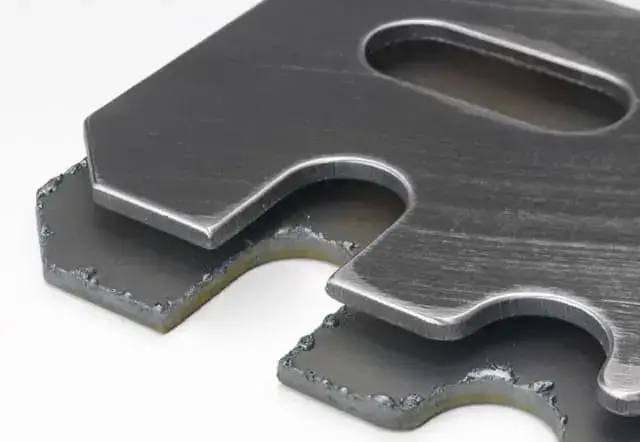
2.Solutions
1.Tool review
Check whether the tool is sharp and hard enough, and adjust the contact angle of the tool during processing to improve the cutting effect of zero turn mower parts.
2.Cutting oil
When the tool is cutting, heat will be generated due to friction, and if the heat is not dissipated in time, the cutting may not be smooth and deformed. Therefore, cutting oil is generally sprayed at present. Wet machining is less prone to burrs than dry machining, and properties such as oil amount and viscosity also affect it.
3.Load adjustment
The load of the tool will change due to the deformation of the material of the toro zero turn mowers parts and other parts, the speed of the tool and the cutting depth, and it needs to be adjusted if necessary.
4.Design
For example, rounded corners are less prone to burrs than right angles, so it is a good idea to avoid right angles if possible.
5.Deburring
If burrs cannot be avoided due to the nature of the material or processing, deburr (grinding, polishing, sandblasting, etc.) after processing parts such as zero turn mower parts. In addition, deburring programs can be added to CNC machine tools and multi-processing machines.