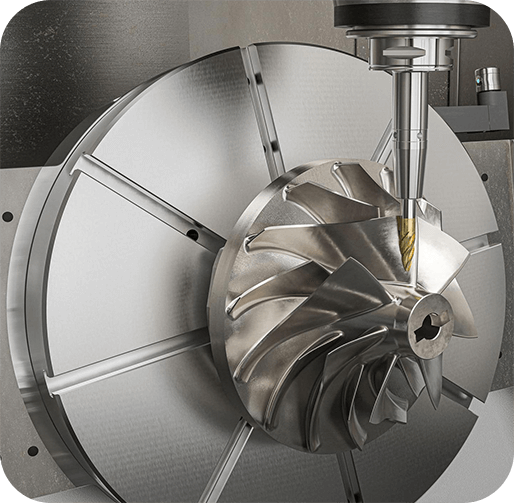
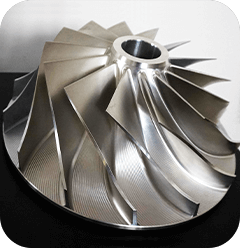
15
+
Years Experience
Trusted by many companies
About 5-Axis Machining
Ultra-Precise 5-Axis Machining Parts
5-axis milling is suitable for turbo blowers, turbochargers, valve bodies, blades, aviation structural parts, complex medical parts, strict X-detection internal quality inspection, small batch processing of raw materials, long-term demand and mass production provide cost Optimize plan.