Machining stainless steel: challenges and tips
Stainless steel is one of the metals used for CNC machining because of its incredible versatility. It can be used in a variety of industries, including automotive, consumer products, medical, and aerospace.
The versatility of stainless steel stems from its many benefits, from corrosion resistance to durability. However, not all types of stainless steel are easy to machine. There can be challenges when machining stainless steel.
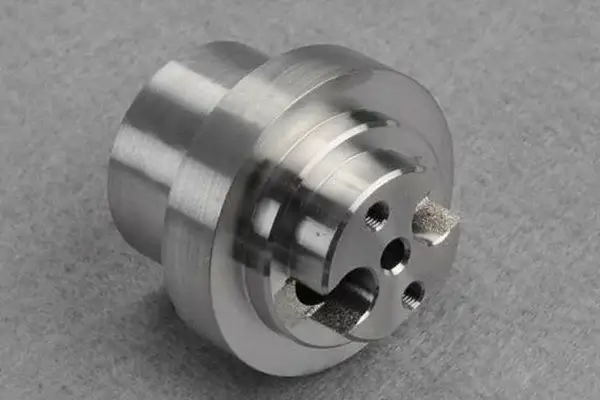
1.Why Choose Stainless Steel for CNC Machining Projects?
Stainless steel is an excellent CNC machining material choice for making strong and durable items. Here are some reasons to choose stainless steel for CNC machining projects.
1) High Tensile Strength
Stainless steel has a higher tensile strength than mild steel, brass, and different types of aluminum alloys. The tension required to stretch a material to the breaking point is called tensile strength.
This is an important quality for many products throughout their service life, especially those that experience a lot of bending and rolling.
2) Low Temperature Resistance
Some stainless steel varieties maintain their stability at certain temperatures. For example, austenitic steel exhibits excellent toughness and higher tensile strength at sub-zero temperatures.
However, it is important to note that not all stainless steel varieties have this property.
3) Corrosion Resistance
Stainless steel is highly resistant to corrosion and can resist water stains and rust. This corrosion resistance makes stainless steel ideal for a variety of outdoor and indoor applications, including extreme temperatures and pressures.
This property of stainless steel is due to the presence of chromium in the metal, which forms a thin layer to protect the steel when it comes in contact with oxygen.
4) Appearance
Stainless steel has a silvery white color and does not discolor or rust over time. Its appearance is due to the high chromium content.
In addition, stainless steel has other properties besides its high strength. This metal is used in a variety of products due to its aesthetic appearance.
Without sacrificing practicality, CNC machined stainless steel parts have a clean, modern look.
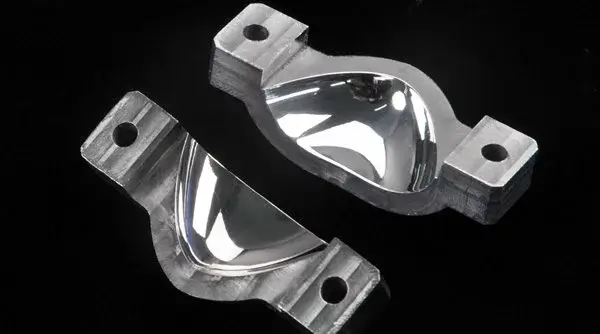
2.Challenges of Custom Stainless Steel Machining Parts
The hardness, machinability, strength, and high temperature resistance of stainless steel alloys are between titanium and aluminum. But there are some challenges. Here are some challenges faced when machining custom stainless steel parts.
1) Overheating
Unlike many other types of steel and metals, stainless steel has poor thermal conductivity. But machining stainless steel causes it to heat up quickly, which can damage the stainless steel itself as well as the tools and CNC machines used in the process.
2) Difficult Surface Finishes
Choosing the right surface finish for stainless steel CNC machined parts is difficult. The reason is that, unlike other metals, the surface finish of stainless steel affects more than just its aesthetics.
It also affects other qualities such as corrosion resistance, electrical properties, impact resistance, and weldability.
3) Technical Expertise
Machining stainless steel requires technical skills and forethought. The reason is that machining stainless steel is tricky because using the wrong cutting tool or speed can damage the material.
It is this challenge that makes machining stainless steel not only very laborious but also slow.
4) Poor Machinability
Stainless steel is much more difficult to machine than other metals. Additionally, stainless steel hardens too quickly and is difficult to work with, resulting in a low machinability rating.
Therefore, stainless steel requires specialized tools for machining.
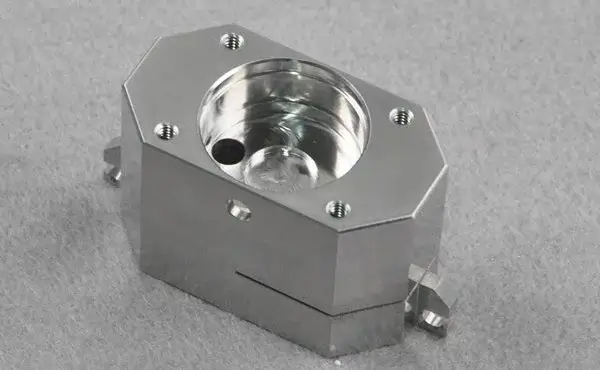
3.Quick Tips for Machining Stainless Steel
There are some challenges when machining stainless steel, but there are ways to avoid these issues and ensure smooth machining. Here are some quick tips for CNC machining this metal.
1) Choose a Specialized End Mill and Drill Bit
It is best to use tools made of high-quality materials, such as molybdenum or tungsten HSS end mills and drill bits. They can withstand the stress of the process with minimal wear when cutting stainless steel.
These tools can also improve surface finish. Avoid using tools that are prone to wear, as this may reduce the processing speed while increasing production costs.
2) Manage the Heat Generated
One of the reasons why stainless steel CNC machining fails is heat. Keeping cutting speeds low and using coolants to control heat is the best way. In addition, it is generally recommended to stop the process when the material begins to overheat.
3) Pecking and Chip Breaking Cycles
Machining with pecking and chip breaking cycles is one way to control chip formation. Doing so helps to eliminate long, thin chips.
Another way to control chip formation is to check the tool frequently, as worn cutting tools will form more chips.
4) Protect the workpiece from deformation
There are many factors that can cause workpiece deformation, including speed and feed rates as well as the cutting tool. Using a worn cutting tool will increase tool deflection, which can cause the part to exceed tolerance and deform.
That is why it is important to use the recommended speeds and feed rates when machining stainless steel.
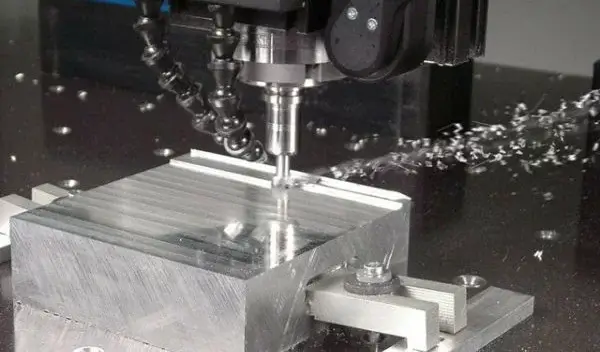
4.Stainless Steel Alloys Available for CNC Machining
Just as there are many types of titanium alloys, there are many stainless steel alloys suitable for various applications. CNC stainless steel alloys suitable for CNC machining are shown below.
1) SS 17-4 Grade (PH Stainless Steel)
This stainless steel contains up to 30% chromium. It is a precipitation hardening martensitic stainless steel.
① Advantages:
- Corrosion resistance
- High toughness
- High strength
② Disadvantages:
- Susceptible to heat damage
③ Applications:
- Oil and gas
- Aircraft turbines
- Nuclear reactions
2) SS303 (Easy to Machining Stainless Steel)
This austenitic stainless steel is highly machinable and easily accessible.
① Advantages:
- Good corrosion resistance
- Moderate price
- Excellent machinability
②Disadvantages:
- Not suitable for marine applications
- Does not harden when heat treated
③Applications:
- Nuts, bolts and screws
- Aircraft accessories
- Bushings
- Electronic hardware
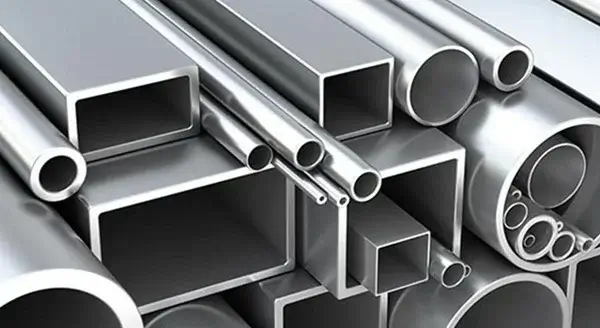
3) SS304 (stainless steel)
This stainless steel with good weldability is one of the most common stainless steel grades.
①Advantages:
- Good weldability
- Good machinability
- Cost-effective
- Good corrosion resistance
②Disadvantages:
- Extremely prone to cracking and corrosion
③Applications:
- Construction applications
- Screws
- Heat exchangers
- Food processing
- Automotive parts
4) SS416 (easy-to-process stainless steel)
This is the easiest stainless steel to process.
①Advantages:
- Moderate corrosion resistance
- Excellent machinability
- Excellent strength
②Disadvantages:
- Not suitable for marine environments
- Not suitable for chlorine-saturated environments
- Not yet popular
- Poor weldability
③Applications:
- Nuts and bolts
- Shafts and gears
- Valves
- Pumps
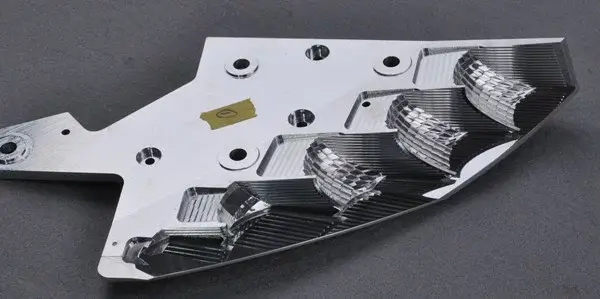
5.Surface treatment options for stainless steel machined parts
There are a variety of surface treatment options available for stainless steel machined parts. These options include polishing and etching, brushing, and sandblasting. The type of surface treatment selected for the stainless steel surface generally determines its corrosion resistance.
1) Polishing
There are many possibilities for the polished surface of stainless steel items. Most stainless steel parts have a surface finish of 3 or 4, and a mirror finish of 8.
Many manufacturers prefer the reflective look of a mirror finish. Mirror finishes are great because they reflect light and look polished and shiny.
2) Sandblasting and pickling
Common surface treatments for stainless steel products are sandblasting and pickling. To achieve this finish, the stainless steel is first mechanically cleaned by sandblasting and then chemically cleaned by dipping it into a stainless steel passivation tank.
This finish gives a matte finish and a highly modern look.
Sandblasted and pickled surfaces are great for creating an industrial look. This finish hides imperfections. It is also a top choice for marine projects and any other project subject to the elements.
3) Brushing
Similar to polished stainless steel, brushed stainless steel requires light abrasion. Brushed steel allows the underlying soft silver-grey color to be seen. Because brushed surfaces do not reflect as much light as mirror-polished surfaces, they slightly dull the color of the steel, and many designers prefer this look.
If you are looking for an experienced machining manufacturer, Xavier is your ideal choice. The Xavier team is well-equipped to provide high-quality machining solutions. If you need more information or to discuss your machining needs with us, please feel free to contact us.