Analysis of CNC machine tool manufacturing precision control and error compensation technology
As the core equipment of modern manufacturing industry, the manufacturing precision of CNC machine tools directly affects the quality and production efficiency of products. In order to ensure that CNC machine tools can meet the requirements of high-precision processing, it is necessary to deeply analyze and control their manufacturing precision and apply effective error compensation technology.
This paper will discuss in detail the three aspects of CNC machine tool processing error sources, methods to improve manufacturing precision and error compensation technology.
1.Analysis of error sources affecting CNC machine tool manufacturing precision
The processing error sources of CNC machine tools are complex and diverse, and can be mainly divided into the following categories:
(1) Machine tool body error:
Including the geometric shape, surface quality, and position error of the working surfaces of various machine tool components. The original manufacturing error of the machine tool is the main cause of the machine tool geometric error, such as spindle rotation error, guide rail error, etc.
(2) Control system error:
Including servo error, interpolation algorithm error, etc. The control system error mainly affects the dimensional accuracy and shape accuracy of the processed parts.
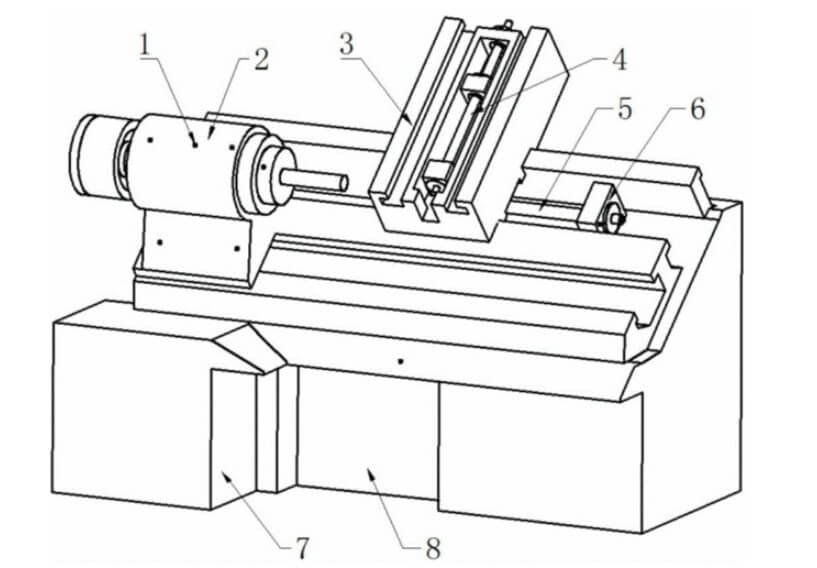
(3) Thermal deformation error:
Error caused by thermal deformation of the machine tool structure due to the internal heat source of the machine tool and the thermal disturbance of the environment. Thermal deformation has a great impact on the accuracy of the machine tool, especially during long-term continuous processing.
(4) Process system deformation error:
Includes the deformation of the machine tool, tool, workpiece and fixture under the cutting load. This error is also called “tool let-down”, which causes the shape distortion of the machined parts, especially when processing thin-walled workpieces or using slender tools. This error is more serious.
(5) Vibration error:
During cutting, due to the flexibility of the process and the variability of the process, the machine tool is more likely to fall into the unstable area, thereby exciting strong chatter, resulting in deterioration of the surface quality of the workpiece and geometric shape errors, affecting the final part manufacturing precision.
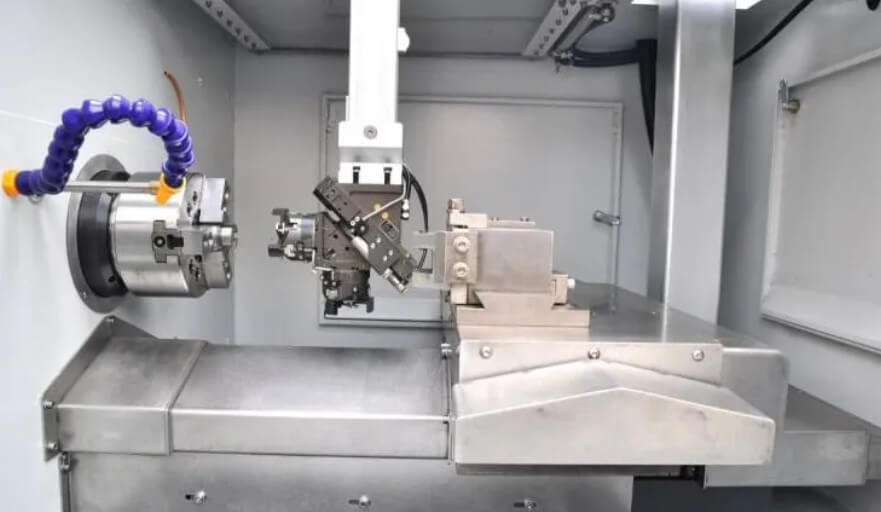
(6) Detection system error:
Includes measurement errors caused by manufacturing errors and installation errors of the measuring sensor and machine tool parts and mechanism errors.
(7) External interference error:
Random error caused by changes in the environment and operating conditions.
2.Methods to improve the manufacturing precision of CNC machine tools
In order to improve the manufacturing precision of CNC machine tools, we can start from the following aspects:
(1) Machine tool accuracy detection and compensation
1) Dual-frequency laser interferometer detection:
Dual-frequency laser interferometer is an important device for CNC machine tool accuracy detection, which can detect the reverse deviation and positioning accuracy of the machine tool. By performing accuracy detection on the machine tool, the error source of the machine tool can be identified, so as to formulate corresponding compensation measures.
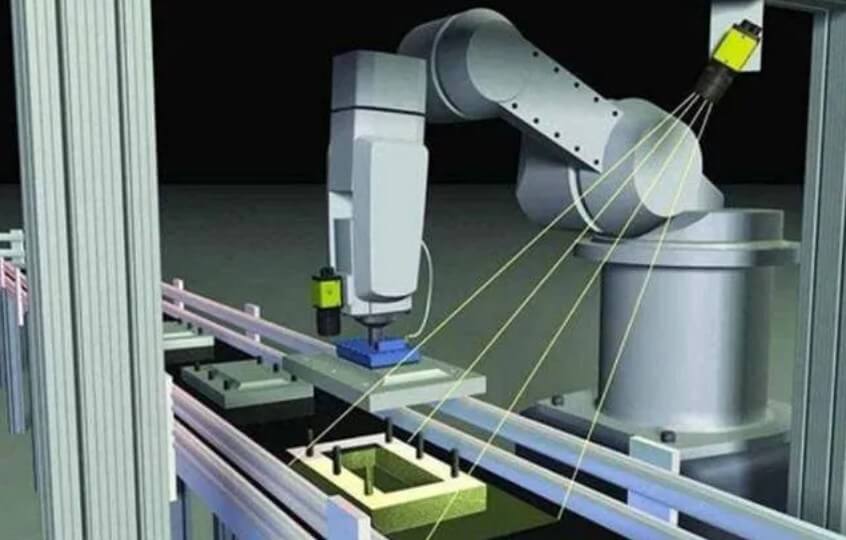
2) Error compensation technology:
Error compensation technology compensates the machine tool error by modifying the processing instructions of the machine tool to achieve the ideal motion trajectory and realize the soft upgrade of the machine tool accuracy. Common error compensation technologies include single error synthesis compensation method, error direct compensation method and relative error decomposition and synthesis compensation method.
(2) Improving the accuracy of the machine tool body
1) Optimizing the machine tool design:
Reduce the original manufacturing error of the machine tool by improving the design and manufacturing precision of each component of the machine tool. For example, improving the spindle rotation accuracy and guide rail accuracy can significantly improve the processing accuracy of the machine tool.
2) Regular maintenance and care:
Regular maintenance and care of machine tools, timely replacement of worn parts, can keep the machine tools in good condition and reduce wear errors.
(3) Control thermal deformation
1) Reduce heat sources:
By optimizing the machine tool structure design, reduce the internal heat sources of the machine tool, such as using low-heat motors, optimizing cooling systems, etc.
2) Control ambient temperature:
Maintain the stability of the machine tool working environment temperature and reduce the impact of ambient temperature changes on the thermal deformation of the machine tool. For example, install air conditioning systems, constant temperature workshops, etc.
3) Thermal compensation technology:
Apply thermal compensation technology to monitor the temperature changes of the machine tool in real time, correct the processing instructions of the machine tool, and offset the impact of thermal deformation on processing and manufacturing precision.

Accuracy changes before and after thermal error compensation
(4) Reduce process system deformation
1) Improve machine tool stiffness:
By optimizing the machine tool structure design, improve the overall stiffness of the machine tool and reduce the deformation of the machine tool under cutting load.
2) Reasonable selection of tools and fixtures:
For those small and precise parts, it is necessary to select tools and fixtures with good rigidity and high precision to reduce the deformation of tools and fixtures under cutting load.
3) Optimize processing technology:
Reasonable selection of cutting parameters to reduce the impact of cutting force on the process system. For example, the use of process parameters such as high-speed cutting, small cutting depth, and large feed can reduce cutting force and improve processing accuracy.
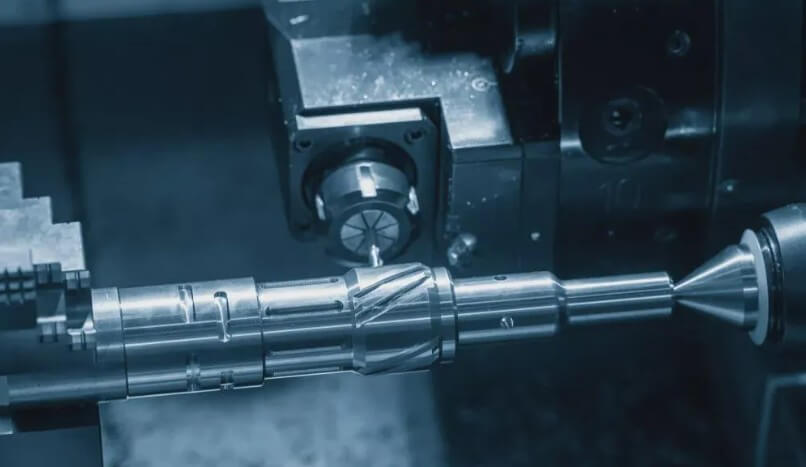
3.Analysis of error compensation technology
Error compensation technology is an important means to improve the processing accuracy of CNC machine tools. Common error compensation technologies include the following:
(1) Single error synthesis compensation method
This compensation method is based on the error synthesis formula. First, the original error values of each single item of the machine tool are measured by direct measurement. The error component of the compensation point is calculated by the error synthesis formula to achieve error compensation for the machine tool. This method is suitable for compensation of machine tool system errors and can significantly improve the accuracy of the machine tool.
(2) Direct error compensation method
This method requires accurate measurement of the machine tool space vector error. The higher the compensation accuracy requirement, the more measurement accuracy and measurement points are required. The error component of the compensation point is obtained by interpolation method, and the error correction is performed. This method requires the establishment of an absolute measurement coordinate system that is consistent with the compensation, and is suitable for high-precision processing occasions.
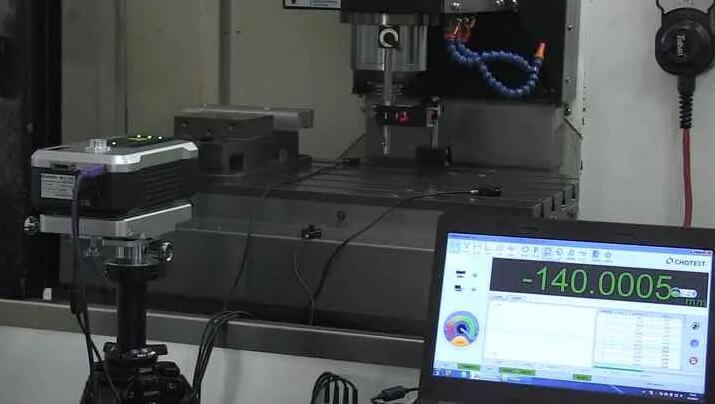
(3) Relative error decomposition and synthesis compensation method
Most error measurement methods only obtain relative comprehensive errors, based on which the single error of the machine tool can be decomposed. Further use of the error synthesis method is feasible for machine tool error compensation. This method is relatively simple to measure and is suitable for production site operations, but it requires a suitable general mathematical model for error decomposition.
(4) Thermal error compensation technology
Thermal error is an important component of CNC machine tool processing error. Thermal error compensation technology monitors the temperature change of the machine tool in real time, establishes a mathematical model between temperature and error, corrects the machine tool processing instructions, and offsets the influence of thermal deformation on processing accuracy. Thermal error compensation technology can significantly improve the manufacturing precision stability of the machine tool during long-term continuous processing.
(5) Online error compensation technology
Online error compensation technology monitors the processing status of the machine tool in real time, dynamically adjusts the machine tool processing instructions, and offsets the influence of various errors on processing and manufacturing precision. Online error compensation technology is suitable for high-precision and high-efficiency processing occasions, but it requires a complete set of high-precision measuring devices and other related equipment, which is costly.
4.Conclusion
The processing and manufacturing precision control and error compensation technology of CNC machine tools is one of the key technologies in modern manufacturing. By deeply analyzing the processing error sources of CNC machine tools and applying effective manufacturing precision control methods and error compensation technologies, the processing and manufacturing precision of CNC machine tools can be significantly improved to meet the requirements of high-precision processing.