What is a mass air flow sensor: structural classification and production and processing technology
The mass air flow sensor (MAF) is one of the key components in the electronic fuel injection system of modern automobiles. It is responsible for accurately measuring the amount of air entering the engine and converting the data into an electrical signal for the electronic control unit (ECU) to calculate and control the amount of fuel injection.
This article will discuss in detail the definition, function, type and detailed overview of the mass air flow sensor and its processing technology.
1.Definition and function of mass air flow sensor
(1) Definition
The mass air flow sensor, also known as the air flow meter, is one of the important sensors of the electronic fuel injection engine. It is located between the air filter and the engine intake manifold, responsible for measuring the air flow entering the engine, and converting this data into an electrical signal and sending it to the ECU.
The ECU uses these signals as the main basis for determining the amount of fuel injection to ensure that the mixture in the engine combustion chamber reaches the optimal concentration, thereby achieving efficient combustion and reducing emissions.
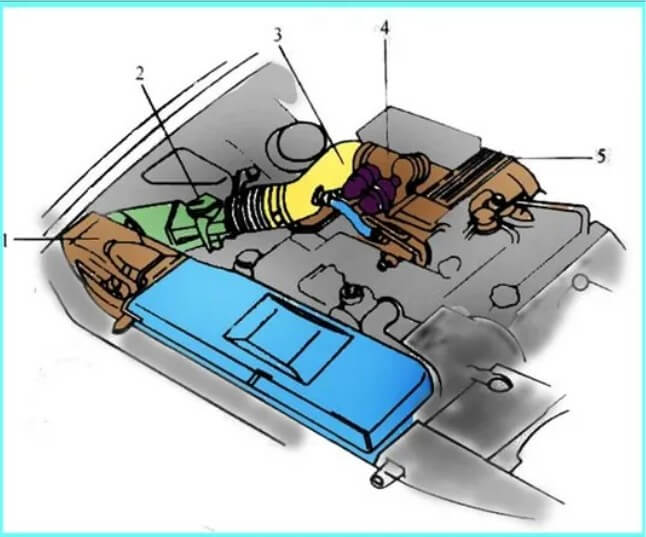
(2) Function
The importance of mass air flow sensors cannot be ignored. The ideal air-fuel ratio is 14.7:1, that is, 14.7 pounds of air corresponds to 1.0 pounds of gasoline. However, the air-fuel ratio is not fixed. When accelerating, the car needs an air-fuel ratio as high as 12:1, while when cruising, it needs to be as low as 22:1.
If the mass air flow sensor or its circuit fails, the ECU will not be able to accurately calculate the amount of fuel injection, resulting in too rich or too lean mixture, abnormal engine operation, and even a series of other problems.
2.Basic structure and classification of mass air flow sensors
There are many types of air flow sensors, and their main structural types include vane type, core type, hot wire type, hot film type, Karman vortex type, etc. Each type has different working principles and applicable scenarios, but their basic function is to measure the intake volume and convert it into an electrical signal.
(1) Vane air flow sensor:
It reflects the intake volume by measuring the opening of the vane pushed by the intake air. Its structure is simple, but the response speed is slow, and it is gradually replaced by other types.
(2) Core air flow sensor:
Uses the displacement of the core in the intake air flow to measure the intake air volume, with high accuracy, but the structure is complex and the cost is relatively high.
(3) Hot wire and hot film air flow sensors:
Uses the cooling effect of hot wire or hot film resistor in the air flow to measure the intake air volume, with fast response speed and high accuracy, and is one of the most widely used types.
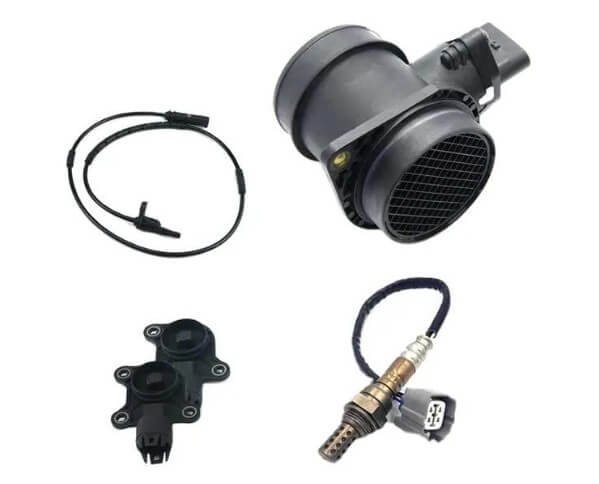
(4) Karman vortex air flow sensor:
Measures the intake air volume by detecting the vortex frequency generated when the air flow passes through a specific structure, with high accuracy and good stability.
3.How to select materials when processing mass air flow sensors?
The material selection of the mass air flow sensor is crucial and must have good high temperature resistance, corrosion resistance and mechanical properties. Commonly used materials include stainless steel, aluminum alloy, ceramics and plastics. For example, the hot wire of the hot wire air flow sensor usually uses platinum wire because of its excellent high temperature resistance and stability.
(1) Plastics:
The shells and some internal structures of many mass air flow sensors are made of engineering plastics, such as polyphenylene sulfide (PPS) and polybutylene terephthalate (PBT). These materials have good mechanical strength, high temperature resistance and molding processability, and are suitable for large-scale production.
(2) Metals:
Some key components in the sensor, such as measuring blades and springs, usually use metal materials such as stainless steel and aluminum alloy. The advantages of metal materials are high mechanical strength, high temperature resistance and good corrosion resistance, but the processing cost is relatively high.
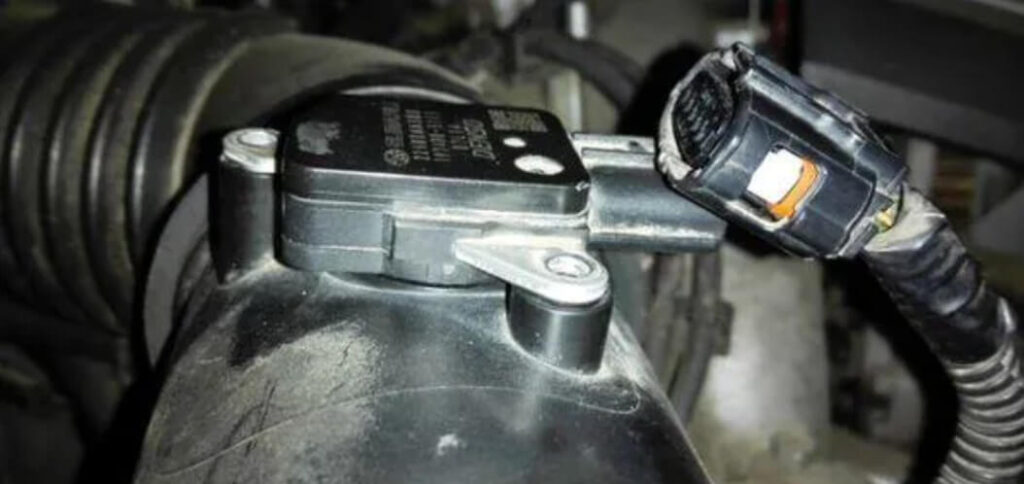
(3) Ceramics:
Ceramic materials are often used as sensitive elements in sensors due to their excellent high temperature stability and chemical corrosion resistance, such as thermistors in thermal film mass air flow sensors. Ceramic materials are complex to process and have high costs, but they have superior performance and are suitable for high-performance engines.
4.Brief description of the processing technology of mass air flow sensor parts
Component processing is the basic link in the production of mass air flow sensors, mainly including machining, injection molding, surface treatment and other processes.
(1) Machining:
For metal parts, such as measuring blades, bearings, shafts, etc., CNC machining technology is usually used for precision machining to ensure dimensional accuracy and surface quality.
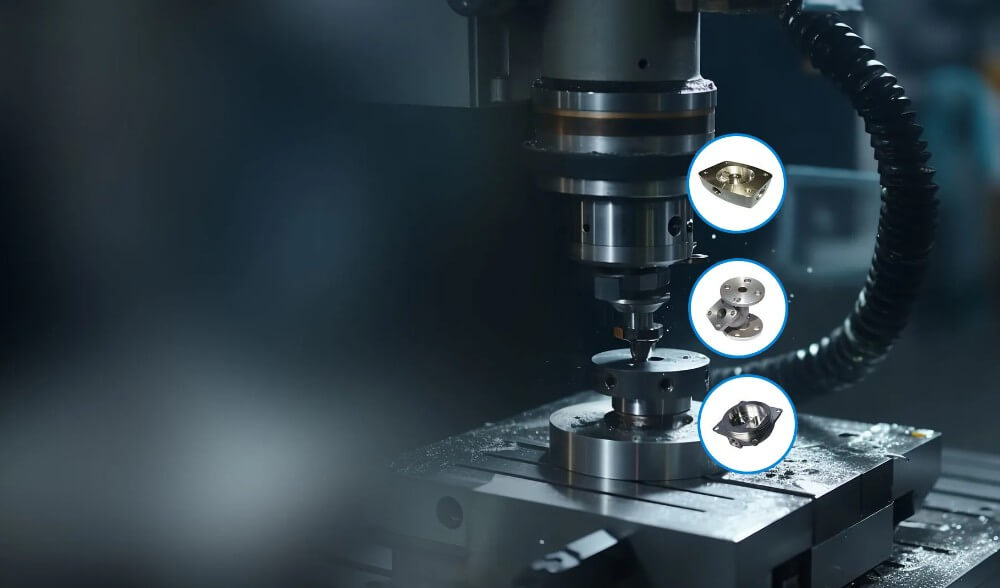
(2) Injection molding:
For plastic parts, such as housings, seals, etc., injection molding is used for production, which is efficient and low-cost.
(3) Surface treatment:
In order to improve the corrosion resistance and aesthetics of parts, surface treatment such as nickel plating, chrome plating, anodizing, etc. is often performed.
5.Detailed Overview of Mass Air Flow Sensor Parts Processing Technology
(1) Precision machining:
Including turning, milling, drilling, grinding and other processes, used to process metal and ceramic parts in sensors. Precision machining requires high-precision processing equipment and advanced processing technology to ensure processing accuracy and surface quality.
1) Turning:
It is mainly used to process rotating parts such as shafts and discs in sensors. Turning requires the use of high-precision lathes and tools, and strict control of cutting parameters to ensure processing accuracy and surface quality.
2) Milling:
It is mainly used to process planes, grooves, holes and other structures in sensors. Milling requires the use of high-precision milling machines and tools, and the use of reasonable processing routes and cutting parameters to ensure processing accuracy and surface quality.
3) Drilling:
It is mainly used to process various holes in sensors. Drilling requires the use of appropriate drill bits and controlled drilling depth to ensure the dimensional accuracy and positional accuracy of the holes.
4) Grinding:
It is mainly used to finish high-precision surfaces in sensors. Grinding requires the use of appropriate grinding wheels and grinding parameters to ensure surface roughness and dimensional accuracy.
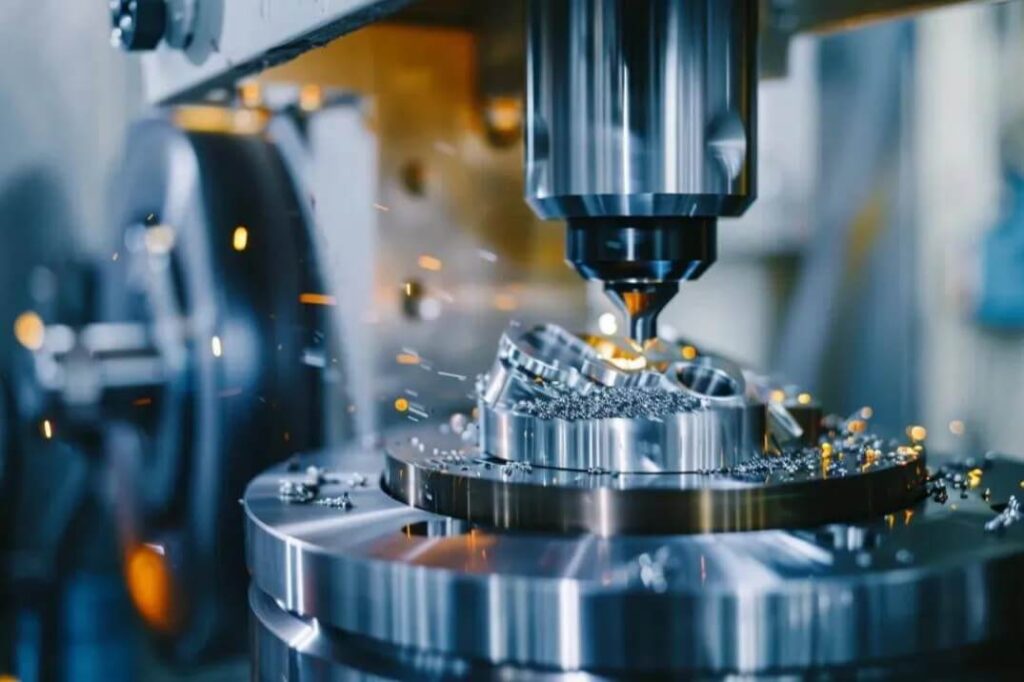
(2) Injection molding
Injection molding is the main manufacturing method for mass air flow sensor housings and some internal structural parts. It has the advantages of high production efficiency, low cost and good product consistency.
1) Material selection
The commonly used materials for injection molding are engineering plastics, such as polyamide (PA) and polycarbonate (PC). These materials have good mechanical strength, heat resistance and chemical corrosion resistance.
2) Mold design and manufacturing
The mold is the key to injection molding. The design of the mold needs to take into account factors such as the product’s structure, dimensional accuracy, surface quality, and production efficiency. The manufacture of high-precision molds is usually completed using CNC machining technology to ensure the accuracy and life of the mold.
3) Injection molding process parameter control
During the injection molding process, process parameters such as temperature, pressure, injection speed, and holding time need to be precisely controlled. Temperature control directly affects the melting and flow properties of the plastic, while pressure and injection speed determine the filling speed and density of the product. By optimizing these process parameters, products with stable dimensions and excellent surface quality can be obtained.
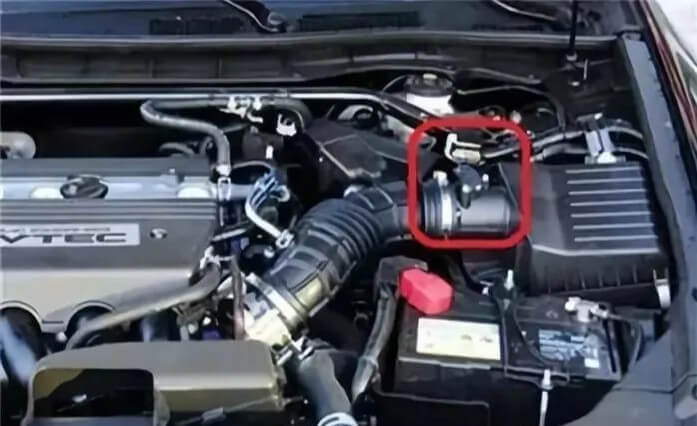
(3) Surface treatment:
Including nickel plating, chrome plating, anodizing and other processes, used to improve the wear resistance, corrosion resistance and aesthetics of sensor components. Surface treatment can not only extend the service life of the sensor, but also improve its working performance.
1) Nickel plating:
It can improve the wear resistance and corrosion resistance of sensor components and is widely used in the surface treatment of metal parts.
2) Chrome plating:
It can improve the hardness and wear resistance of sensor components and is suitable for surface treatment of parts requiring high wear resistance.
3) Anodizing:
It can improve the corrosion resistance and aesthetics of sensor components and is widely used for surface treatment of aluminum alloy parts.
6.Importance of precision machining technology
The precision machining technology of mass air flow sensor is directly related to the measurement accuracy, reliability and service life of the sensor. Precision machining technology not only needs to ensure the dimensional accuracy and surface quality of each component of the sensor, but also needs to ensure the stability and consistency of the sensor in the working environment.
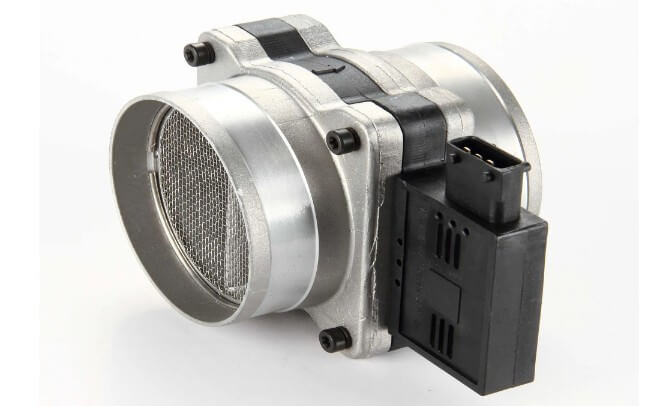
(1) Measurement accuracy:
The measurement accuracy of the sensor directly affects the working state of the engine. Precision machining technology can effectively control the size and shape and position tolerances of key components of the sensor, thereby improving the measurement accuracy.
(2) Reliability:
The sensor needs to withstand high temperature, high pressure, vibration and other harsh conditions during the operation of the car. Precision machining technology can improve the strength and wear resistance of sensor components and ensure their long-term stable operation.
(3) Service life:
Precision machining technology can reduce the wear and fatigue of sensor components, extend the service life of the sensor and reduce maintenance costs.
7.Summary
As a key component in the automotive electronic fuel injection system, the mass air flow sensor has an important impact on the performance and emissions of the engine. Therefore, the production of its components needs to rely on precision machining technology. This article has detailed the relevant issues on how to process its different components. If you need, please contact us.