The best guide to mechanical parts production, must read
The Mechanical Parts Production is vital in the fields of engineering and manufacturing. A deep understanding of the complexity of mechanical part production is essential to ensure high-quality products and efficient processes. This article will delve into various aspects of mechanical part production, including an overview of production, process preparation procedures, and the equipment involved.
1、Overview of Mechanical Parts Production
1.Pre-production preparation
Carry out process preparation, confirm that the design drawings and process documents are complete, determine the processing procedures, process parameters, equipment, prepare and inspect raw materials and process auxiliary materials, formulate detailed process plans and schedules, including determining the processing sequence and time schedule, and assigning production tasks. This link is crucial for the smooth progress of subsequent mechanical parts production.
2.Parts processing
Carry out cutting processing according to the design drawings, such as drilling, milling, turning, etc., determine the size and shape layer by layer, and finally check and grind to ensure that the size and surface quality meet the requirements.
3.Parts assembly
Determine the assembly sequence and method according to the design drawings and process documents, and debug and test the functional performance after assembly.
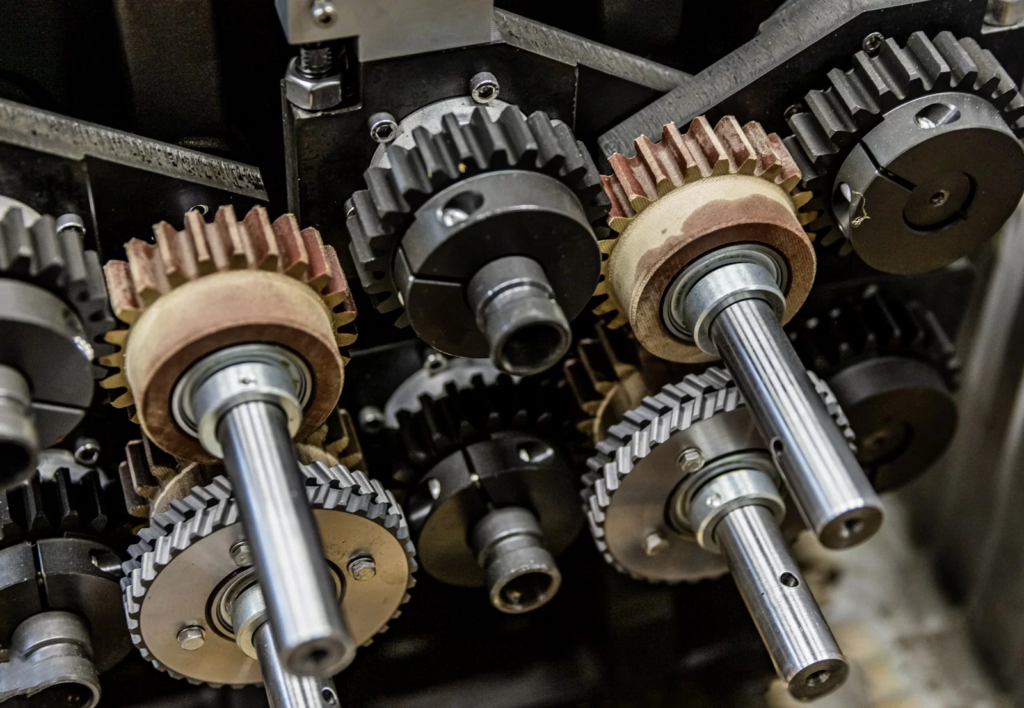
4.Factory inspection
Factory inspection is the last checkpoint to ensure the production quality of mechanical parts. Before the product leaves the factory, a comprehensive inspection of key dimensions, assembly clearances, surface quality, etc. is carried out, functional performance and reliability tests are carried out, and product packaging, quality records and document sorting are completed.
2、Mechanical parts production preparation process
1.Document confirmation
Document confirmation is the basic link in the Mechanical Parts Production, ensuring the accuracy and standardization of production.
Before production begins, confirm whether the design drawings and related process documents are complete. Interpret the drawings in detail, clarify key information such as part shape, size, material, and understand the processing requirements and technical standards in the process documents.
2.Determine processing details
Determine the processing procedures, process parameters and equipment based on the design drawings and process documents. Determine the complexity of the part structure, select the appropriate processing technology, such as turning, milling or grinding, and determine the process parameters such as cutting speed, feed rate, cutting depth, etc. to ensure processing accuracy and efficiency.
3.Material preparation and inspection
Prepare raw materials and process auxiliary materials, and conduct incoming inspection. Strictly control the quality of raw materials, check whether the chemical composition and physical properties meet the requirements, and ensure that the specifications and performance of process auxiliary materials meet production needs.
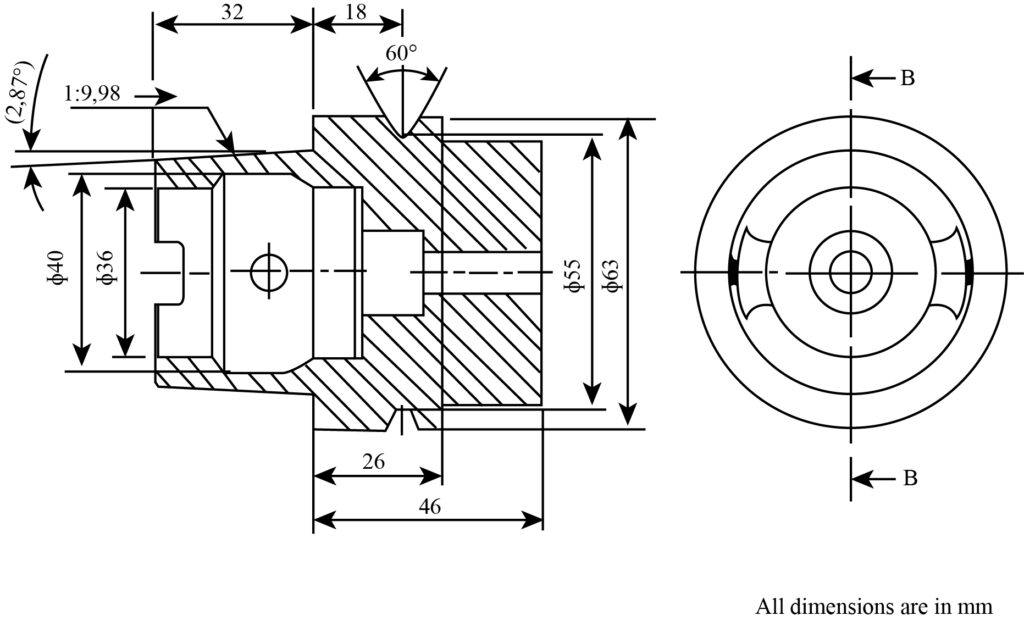
4.Pretreatment work
Prepare parts for subsequent processing procedures such as deburring, flash removal, cleaning, cleaning and measurement. The quality of pretreatment work directly affects the efficiency and quality of subsequent processing.
3、Common Mechanical parts production technology
There are many processing technologies and methods for the production of mechanical parts. Common processing technologies are as follows:
1.Other processing methods
In addition, there are also processing methods such as boring, honing, and polishing to meet the special processing needs of different parts. These processing methods enrich the processing methods of mechanical parts production.
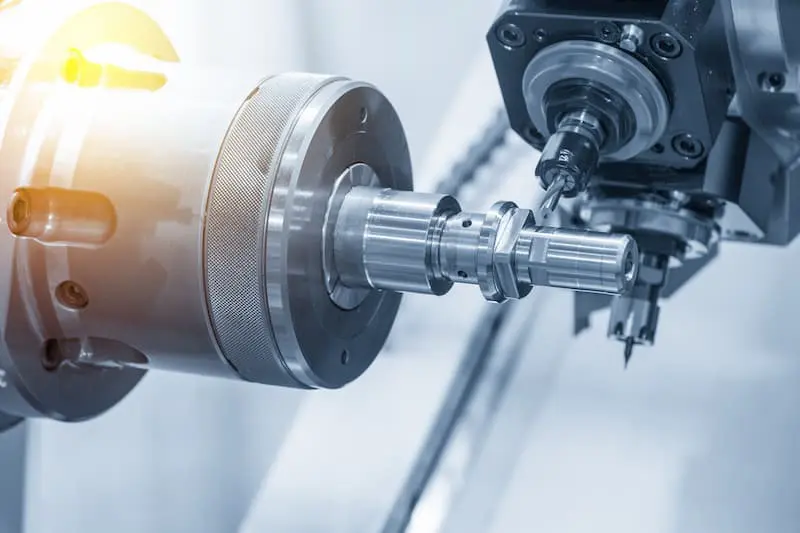
2.Turning
Turning is usually used to process parts with rotating surfaces such as cylinders and cones, such as shaft parts and disc parts. By cutting with a turning tool on a rotating workpiece, high-precision processing of surfaces such as outer circles, inner circles, and threads can be achieved. Turning is one of the common processing methods for the Mechanical Parts Production.
3.Milling
Milling is suitable for processing parts such as planes, grooves, and gears. The milling machine uses a rotating milling cutter to cut workpieces, which can achieve the processing of complex shapes. For example, in the production of mechanical molds, the milling process can process cavities and punches of various shapes.
4.Drilling
Drilling is mainly used to drill holes on workpieces. Its accuracy and surface quality requirements are relatively high, and it is often used to prepare for subsequent processing procedures.
5.Grinding
Grinding is used to improve the surface quality and accuracy of parts, such as further polishing parts that have been turned or milled to achieve higher surface roughness requirements.
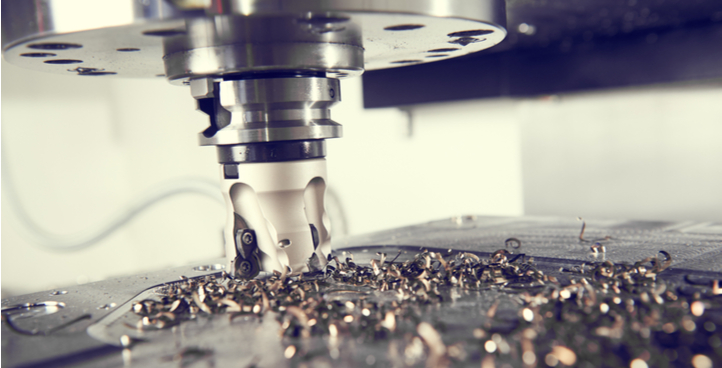
4、Quality inspection in the Mechanical Parts Production
1.Preparation before testing
Before testing, you should make adequate preparations, including preparing relevant testing equipment and tools, such as measuring instruments, test equipment, and testing tools. At the same time, clarify the purpose and standards of the test so that you can make accurate test judgments.
2.Appearance inspection
During the appearance inspection, the inspector needs to check the appearance factors such as the dimensions, surface finish, wear, deformation, and color difference according to the product design drawings to determine whether the product meets the requirements. For example, when inspecting the surface of mechanical parts, it is necessary to check whether there are defects such as scratches, depressions, and protrusions, and whether the surface roughness meets the specified standards.
3.Dimension inspection
Dimension inspection is one of the important links in the inspection of mechanical parts. Use measuring tools such as calipers, vernier calipers, and micrometers to measure the length, diameter, depth, angle, flatness and other parameters of the parts to assess whether their dimensions meet the design requirements. Dimension inspection is a key link in ensuring the production accuracy of mechanical parts.
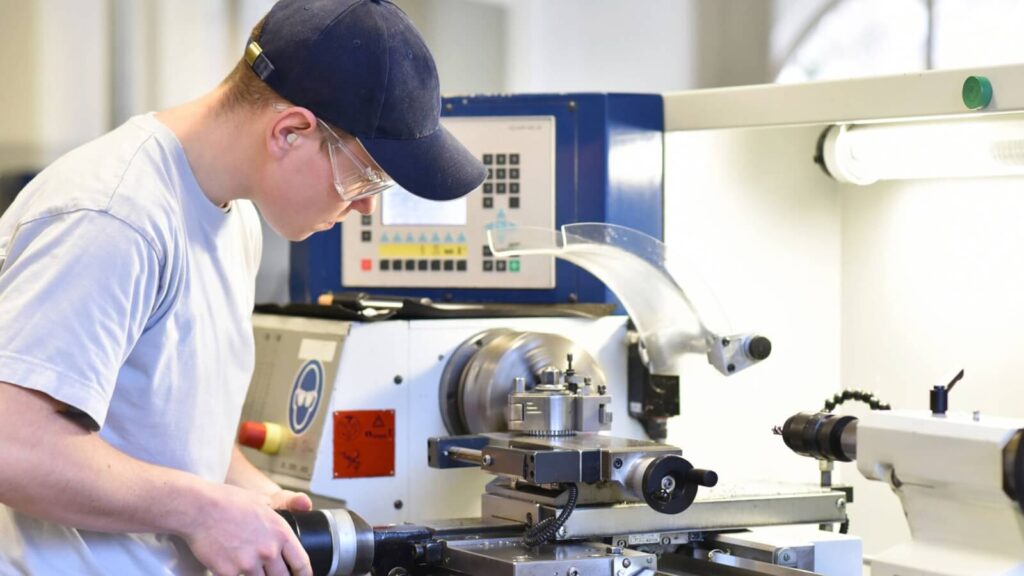
4.Material inspection
Material inspection is also an important part of quality inspection. Through various testing methods such as chemical analysis, tension, compression, and hardness testing, the performance of the material is tested to ensure that it meets the product requirements. For example, for materials used to manufacture high-strength components, tensile tests are required to determine whether their strength meets the standards.
5.Mechanical performance testing
Mechanical performance testing is an important means to ensure the performance of mechanical parts production products.
Mechanical performance testing is used to evaluate the product’s bearing capacity, stability, toughness and other properties. Through tensile tests, pressure tests, bending tests and other methods, ensure that product quality meets the requirements.
5、What should you consider when choosing machinery parts production equipment?
1.Processing requirements
First, we need to clarify the processing requirements, and determine the type, size, precision level and other requirements of the processed parts according to the product specifications and production plans. For example, for small parts with high processing precision, CNC machining centers are a more appropriate choice; for rough processing of large parts, gantry milling machines are more suitable.
2.Equipment functions
Then understand the functions of different types of machining equipment, including processing range, precision capability, processing efficiency, etc. For example, lathes are mainly used to process rotating parts, milling machines are suitable for processing planes and curved surfaces, and grinders are used to improve the surface accuracy of parts. Equipment function is one of the key factors in selecting mechanical parts production equipment.
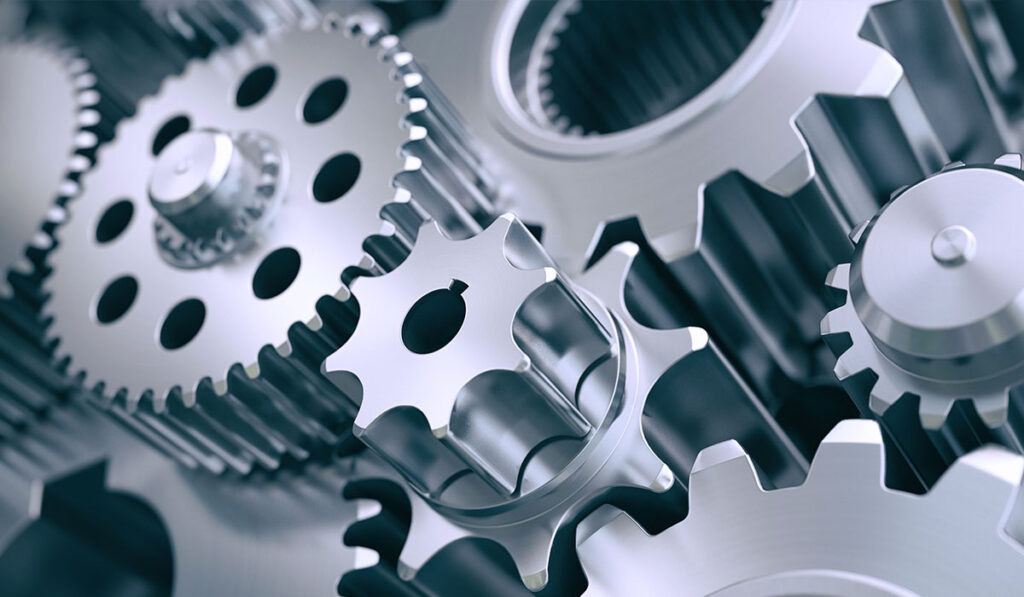
3.Equipment selection
When selecting equipment, appropriate processing equipment should be selected according to processing requirements and equipment functions to ensure processing quality and efficiency. At the same time, factors such as equipment performance, precision requirements, reliability, and stability should also be considered. For example, for production lines that need to run continuously for a long time, the reliability and stability of the equipment are particularly important.
4.Price and cost performance
On the premise of meeting the processing requirements, choose equipment with reasonable price, stable performance and convenient maintenance, and also consider the long-term benefits of the equipment such as the service life of the equipment, the replacement cycle of wearing parts, and the maintenance cost. Price and cost-effectiveness are important considerations when choosing equipment for the Mechanical Parts Production.
6、Processing characteristics of different types of mechanical parts
1.Shaft parts
Shaft parts usually have a rotating surface. During the processing, it is necessary to ensure the precision indicators such as cylindricity, coaxiality, and surface roughness. During the turning process, the tool and cutting amount should be reasonably selected to improve the processing efficiency and quality. Shaft parts are a common type in the Mechanical Parts Production.
2.Box parts
Box parts have complex structures and usually require multi-surface processing and hole system processing. During the processing, the parallelism, verticality and position accuracy of each surface must be ensured.
3.Mold parts
Mold parts are often of special shapes, and special processing methods such as EDM and wire cutting are required to meet their complex shapes and high precision requirements.
4.Thin-walled parts
Thin-walled parts are prone to deformation during processing, and special clamping methods and cutting processes are required to reduce deformation. The processing of thin-walled parts is one of the challenges in the Mechanical Parts Production.
5.High-precision parts
The processing of high-precision parts is a high-end field in the Mechanical Parts Production.
High-precision parts need to be processed in a constant temperature environment to reduce the impact of temperature changes on part accuracy. At the same time, high-precision measuring equipment is used for testing to ensure that the dimensional accuracy and shape and position accuracy of the parts meet the requirements.
7、Final
Mechanical parts production is a key link in the field of engineering and manufacturing, covering many aspects from pre-production preparation to processing procedures, quality inspection and equipment selection. Understanding and mastering these links is crucial to ensure the Mechanical Parts Production.