mechanical turned parts for the medical sector |
Mechanical Turned Parts for the Medical Sector: Optimization of Manufacturing Processes and Challenges
As an indispensable part of modern medical equipment manufacturing, the precision and quality of mechanical turned parts for the medical sector are directly related to the safety and effectiveness of medical equipment. With the continuous progress of medical technology, the requirements for mechanically turned parts are becoming more and more stringent, and how to improve their precision while ensuring efficiency has become a major challenge in front of manufacturers. In this paper, we will discuss in depth the challenges, technical requirements, manufacturing process, key components and other related contents of mechanical turned parts for the medical sector.
1.Overview of the basics of mechanical turned parts for the medical sector
(1) Overview of medical device industry
The medical device industry is a highly specialized and strictly regulated industry involving the intersection of many disciplines and technical fields. The development of this industry plays a vital role in improving the quality of human life and health. With the aging of the global population and rising health awareness, the demand for medical devices continues to grow, driving continuous technological advancement and innovation.
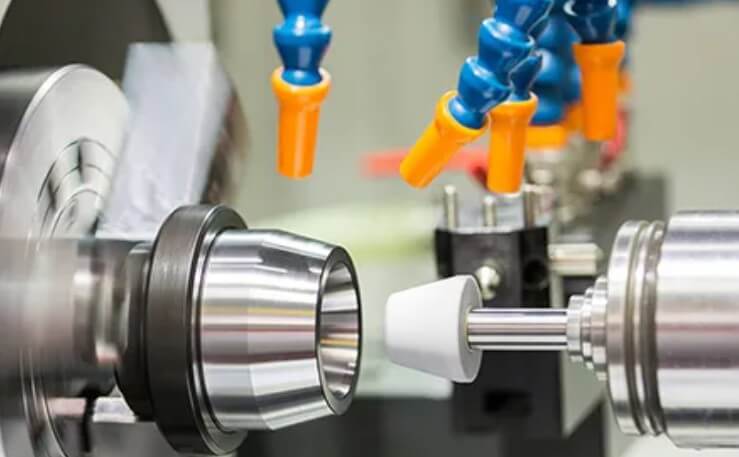
(2) Application related to mechanical turned parts in medical sector
The application of mechanically turned parts in medical devices is extremely wide, covering a wide range of aspects from basic medical tools to complex implants and high-end medical devices. For example, the manufacturing of key medical devices such as orthopedic implants, dental implants, pacemakers, etc. cannot be separated from high-precision mechanical turning technology. These turned parts not only require extremely high manufacturing precision, but also must ensure biocompatibility and stability in the human environment, so the choice of materials and processing technology requirements are very strict.
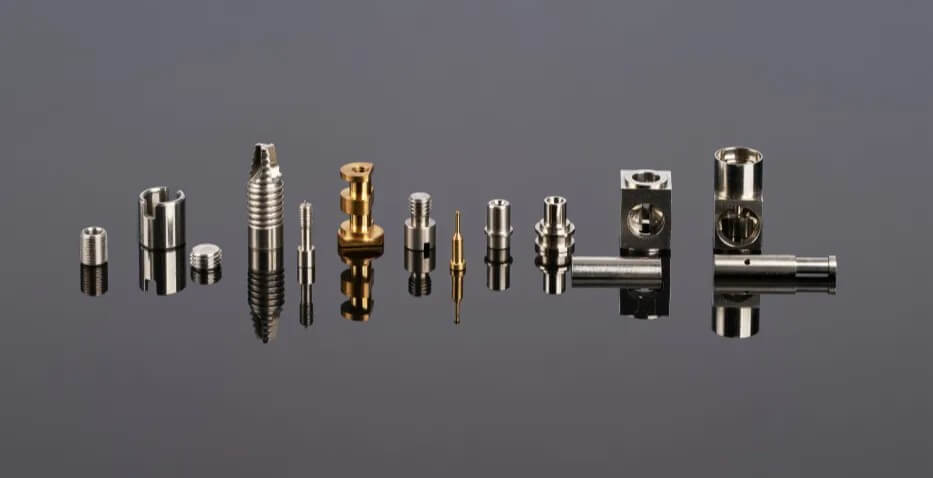
2.Technical requirements and challenges of mechanical turned parts for the medical sector
(1) Material requirements
Materials used for mechanical turned parts for the medical sector usually need to have excellent biocompatibility, corrosion resistance and mechanical properties. Commonly used materials include stainless steel, titanium alloys, cobalt-chromium alloys, and so on. These materials not only need to remain stable in the human environment, but also need to be able to withstand a variety of physiological conditions, such as corrosion of body fluids, mechanical stress and so on. In addition, the research and application of new materials are advancing to meet more complex and changing medical needs.
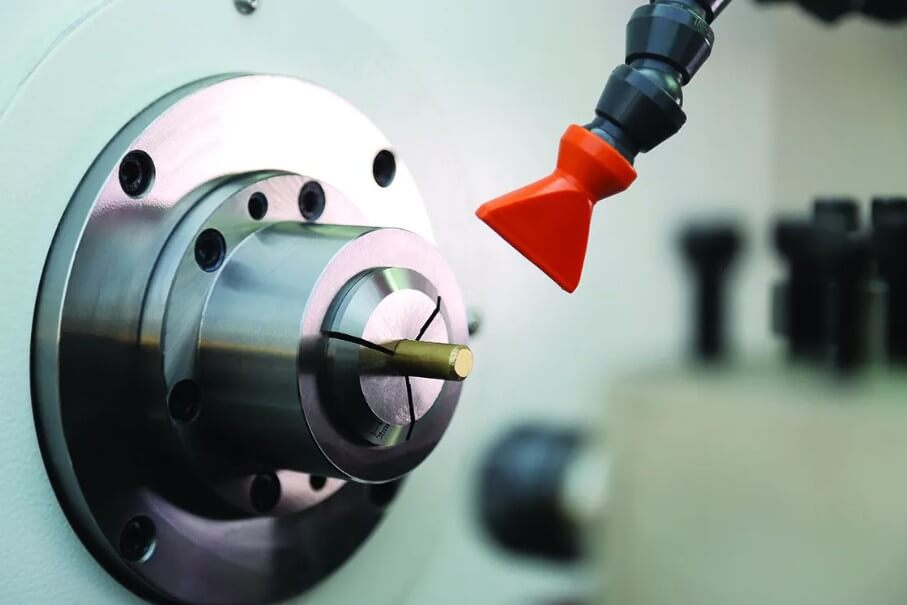
(2) Precision and surface finish requirements
Mechanical turned parts for the medical sector have extremely high requirements for precision and surface finish. For example, the surface treatment of orthopedic implants needs to ensure that they combine well with human bones and reduce the risk of rejection and infection. Therefore, every detail of the turning process must be precisely controlled to ensure the quality and performance of the final product. High-precision turning process can not only improve the service life of the product, but also enhance its safety and reliability in the human body.
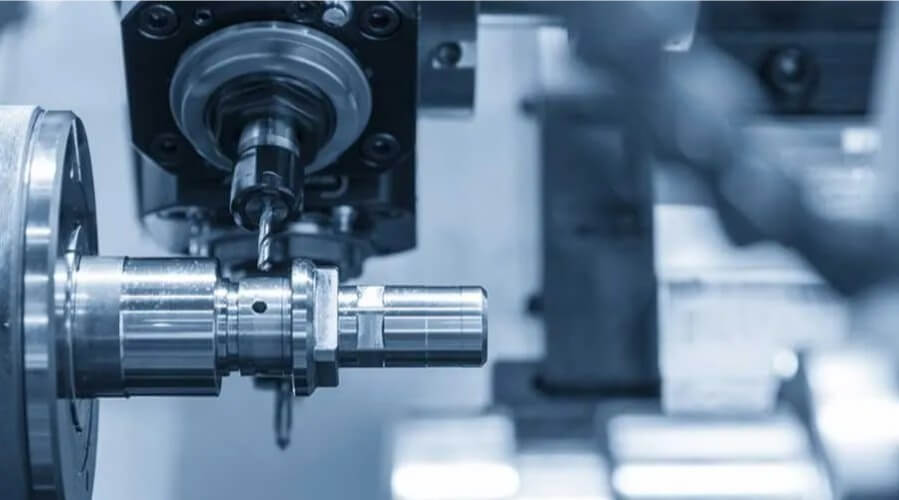
(3) Quality control in the production process
In the production process of mechanical turned parts for the medical sector, quality control is crucial. It is necessary to use advanced quality inspection technology and strict production management process to ensure that every turned part meets the standard. For example, the use of high-precision inspection equipment for dimensional and surface quality inspection, as well as the monitoring of the production process through statistical process control (SPC) methods to prevent defective products. It is also important to control the cleanliness of the production environment to prevent any possible contamination.
3.Manufacturing process for mechanical turned parts for the medical sector
(1) Overview of the turning process
The manufacturing of mechanically turned parts for the medical industry usually involves a variety of turning techniques, including conventional turning and CNC turning. CNC turning is more and more widely used in medical machinery manufacturing due to its high precision and high efficiency. CNC turning technology is a complex process that requires multiple procedures such as rough turning, semi-finish turning and finish turning, which can realize high-precision processing of complex shapes and ensure that the size and shape of each turned part meets the design requirements. In addition, CNC turning can also improve production efficiency and product quality through automation and intelligent means.
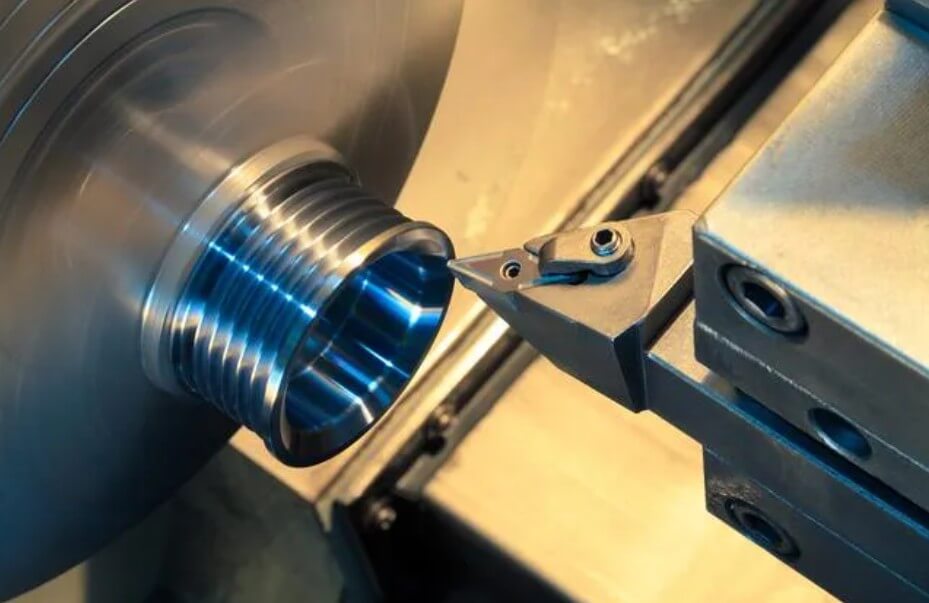
(2) The application of multi-axis linkage CNC machine tools
Multi-axis linkage CNC machine tools can complete the machining of multiple surfaces in a single clamping, which greatly improves the production efficiency and machining accuracy. In the manufacture of mechanical turned parts in the medical industry, it is widely used in the turning processing of high difficulty and high precision. For example, in the processing of artificial joints, orthopedic implants and other complex surfaces, five-axis linkage CNC machine tools can realize all-round, dead-angle-free machining, to ensure the accuracy and quality of the product.
(3) Tool selection and cutting parameter optimization
In the manufacturing process of mechanical turned parts for the medical sector, the selection of tools and optimization of cutting parameters have a direct impact on processing efficiency and quality. It is necessary to select the appropriate tool material and geometry according to the specific material and processing requirements. For example, for the high hardness thermal spray material layer, the better tool materials for cutting and machining are added lithium carbide, niobium carbide ultra-fine grain carbide and cubic boron nitride (CBN).
In addition, the optimization of parameters such as cutting speed, feed and depth of cut is also very critical, and the best combination of cutting parameters needs to be determined through practice to ensure the stability and efficiency of the machining process.
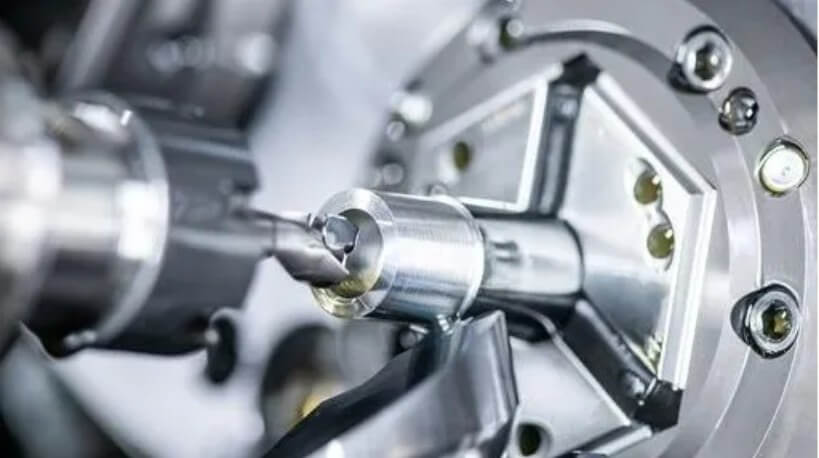
(4) Heat treatment and surface treatment requirements
Due to their special application environment, mechanical turned parts for the medical sector need to undergo strict heat treatment and surface treatment to ensure their performance and safety. In terms of heat treatment, turned parts usually need to be quenched and tempered to improve hardness and wear resistance and eliminate internal stress. Surface treatment includes polishing and coating, etc. Polishing reduces surface roughness and lowers the risk of bacterial adhesion; coating technologies such as titanium nitride and physical vapor deposition enhance corrosion resistance and biocompatibility.
In addition, the surface treatment of mechanical turned parts for the medical sector also needs to consider environmental protection and sterility requirements, using non-toxic and non-hazardous process materials, as well as strict cleaning and sterilization. Precise control and testing is carried out throughout the process to ensure that each product meets the stringent standards of the medical industry.
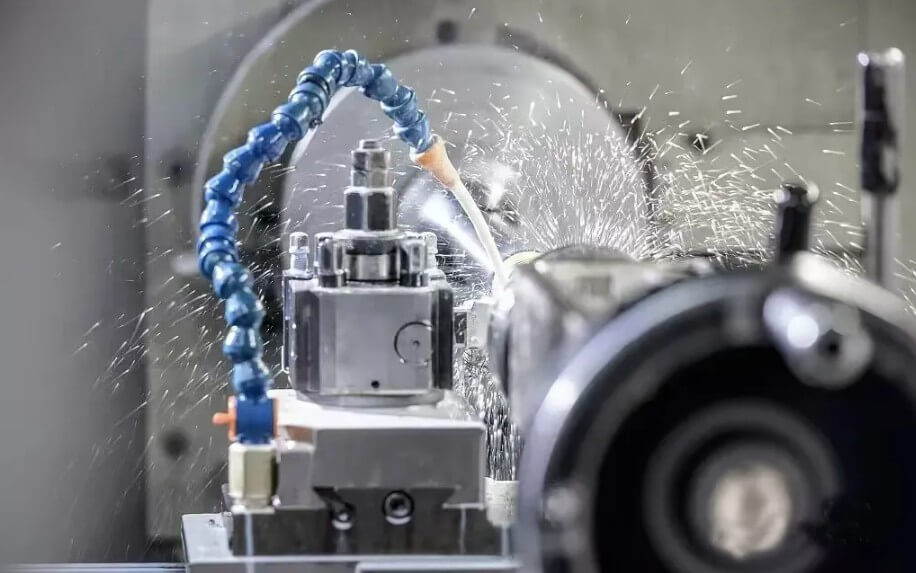
4.Analysis of key mechanical turned parts for the medical sector
(1) Orthopedic implants
Orthopedic implants, such as joint substitutes, bone spikes and bone plates, require extremely high material strength and biocompatibility. These implants are usually manufactured using titanium alloys or cobalt chromium alloys, and their dimensional accuracy and surface quality are ensured through precise turning processes. Titanium alloys are the material of choice for orthopedic implants due to their light weight, high strength and excellent biocompatibility. During the turning process, special attention needs to be paid to tool selection and optimization of cutting parameters to ensure surface finish and overall performance of the implant.
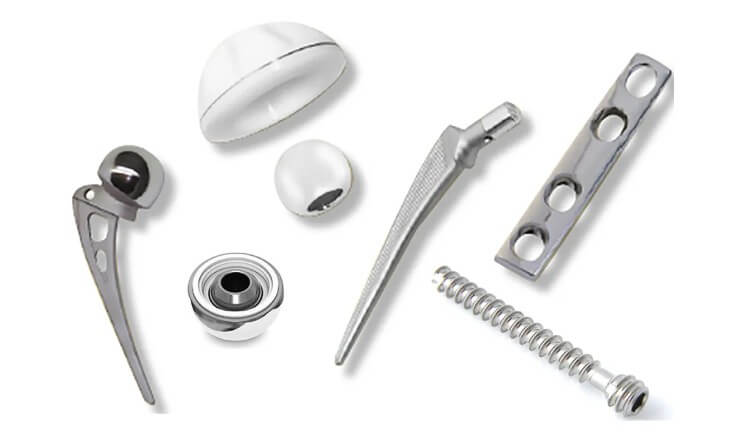
(2) Dental implants
Dental implants are mainly used for tooth restoration and replacement, and the biocompatibility and precision of the materials are also highly required. Commonly used materials include titanium alloys and ceramics. Turning processes are required to ensure that implants are precisely shaped and dimensioned to suit the specific needs of the patient. Additionally, the surface finish of dental implants is critical, requiring specific processes to enhance their surface finish and bioactivity to facilitate integration with surrounding tissues.
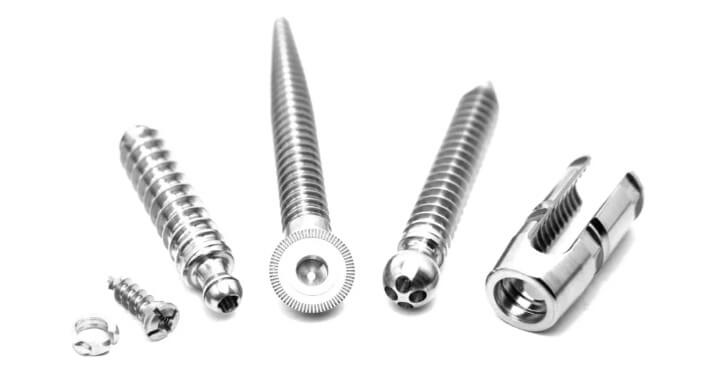
(3) Pacemaker Components
Cardiac pacemakers are high-precision medical devices, and their internal components need to be manufactured with extreme precision and reliability. Commonly used materials include stainless steel and titanium alloys. The turning process plays a crucial role in manufacturing these tiny but complex components, ensuring that the size and shape of each part is precise. Additionally, the surface finish of pacemaker components is critical, requiring specific processes to improve their corrosion resistance and biocompatibility.
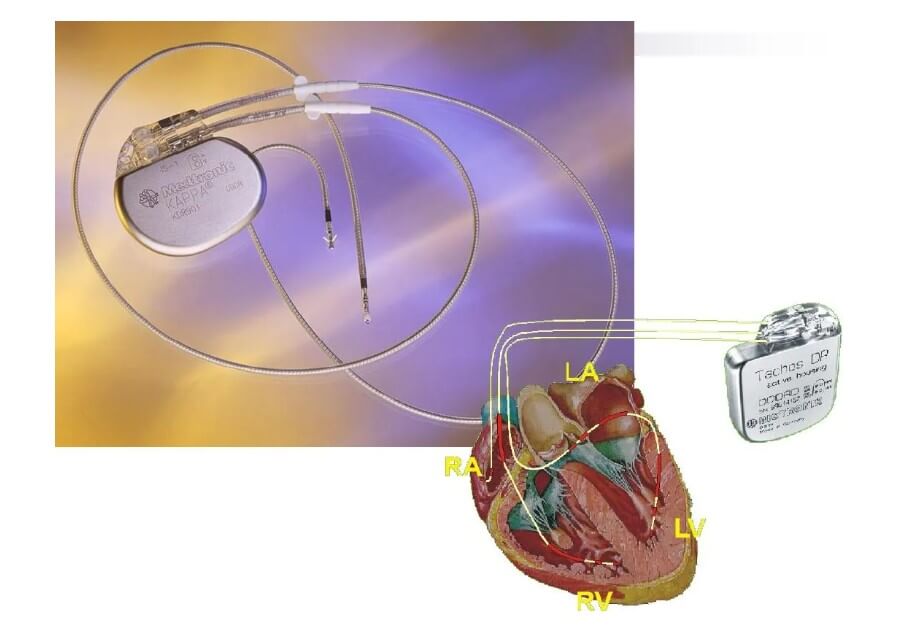
5.Summary
To sum up, the development of mechanical turned parts for the medical sector requires not only technological innovation, but also strict quality control and continuous optimization and upgrading. Only in this way can we ensure the efficient and stable operation of medical equipment and escort the cause of human health.