Importance of Medical Prototyping
Prototyping plays a key role in developing and perfecting cutting-edge medical solutions. Medical prototyping is the core link in transforming advanced ideas into practical medical solutions, and plays a vital role in promoting the progress of the medical industry. From the initial idea to the final product realization, medical prototyping runs through the entire process of medical device development, bringing endless possibilities to the medical field. This guide will introduce medical prototyping in depth to help users better understand it.
1.Basic Introduction to Medical Prototyping Design
Medical device prototyping is a critical step in the development of medical devices to carefully create preliminary versions or models. It is an important stage for rigorous testing, comprehensive evaluation and continuous improvement of medical devices before full production.
In the medical field, a prototype can be an early version of a medical device, tool or technology that vividly demonstrates the unique concepts and powerful functions of a new treatment method, diagnostic tool or medical device. Through medical prototyping, potential problems can be discovered in advance, costs can be effectively saved, and more innovative and practical medical devices can be created, greatly improving patient treatment and safety.
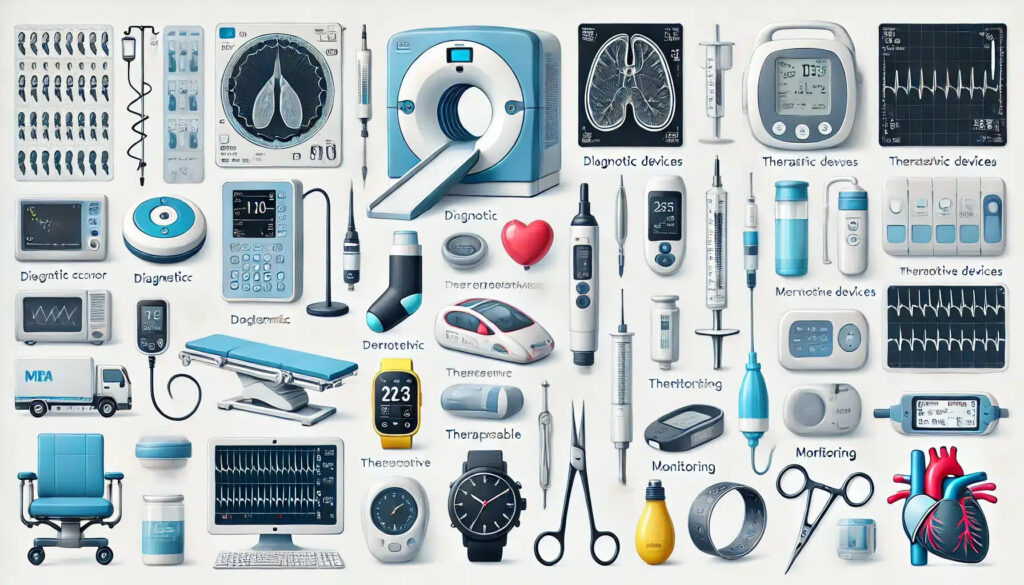
2.Detailed explanation of the medical prototype design process
1.Demand analysis
Comprehensively analyze the needs of medical equipment, clarify the required functions, performance and design features, and lay the foundation for subsequent design.
2.Concept design
Use CAD software and other conceptual design tools to make preliminary design drawings, covering appearance and structure, and show the design concept.
3.3D printed prototype
Use 3D printing technology to convert the designed virtual model into a physical prototype, conduct design verification and feasibility testing, and provide a basis for further optimization.
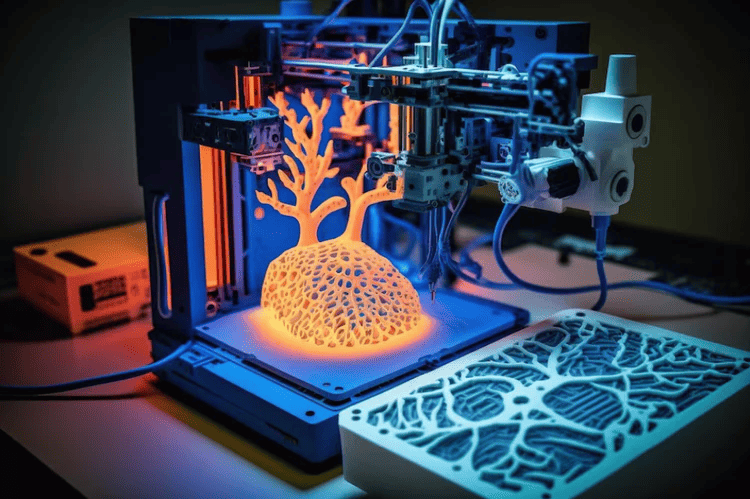
4.Functional testing
Perform actual functional testing on the prototype, including the operating performance, accuracy, stability and other aspects of the equipment to ensure product quality.
5.Pay attention to user feedback
Solicit feedback from healthcare professionals and patients, and make necessary improvements to the prototype based on the feedback to improve the practicality of the product.
6.Compliance assessment
Perform compliance assessment on the prototype to ensure that it complies with relevant regulatory standards for medical devices and ensure the legality and safety of the product.
7.Final verification
Perform final verification on the prototype to ensure that it meets the design requirements and works properly, and prepare for the official launch of the product.
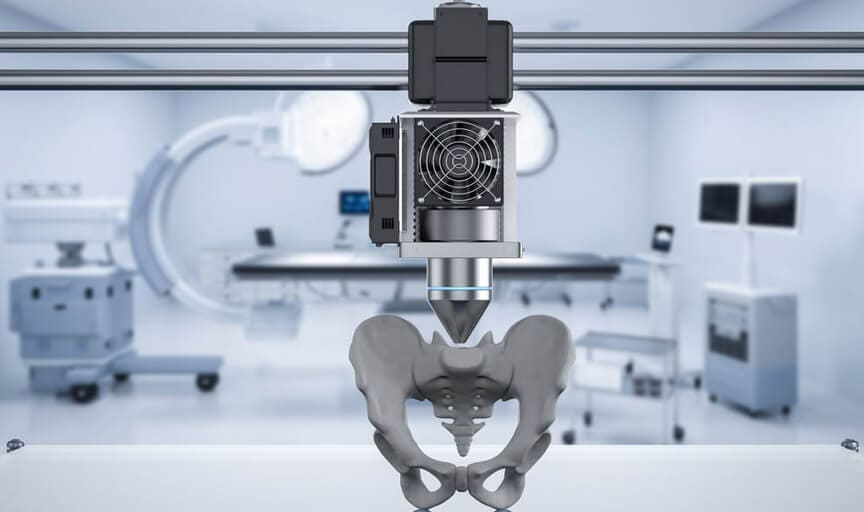
3.Benefits of Medical Prototyping
1.Low cost
Careful modifications during the prototype stage can significantly reduce the cost of the final product by avoiding problems discovered after mass production.
2.Product design optimization
Test product designs through actual operations, discover and correct potential problems in a timely manner, and comprehensively improve the functionality and performance of the final product.
3.Ensure regulatory compliance
Medical prototyping helps ensure that the design and manufacturing processes comply with industry specifications and regulatory requirements, ensuring product safety.
4.Rapid prototyping
With the help of 3D printing technology, the virtual model of CAD design can be quickly transformed into a physical prototype to verify the design concept and feasibility, further improve the design, and accelerate the process of medical innovation.
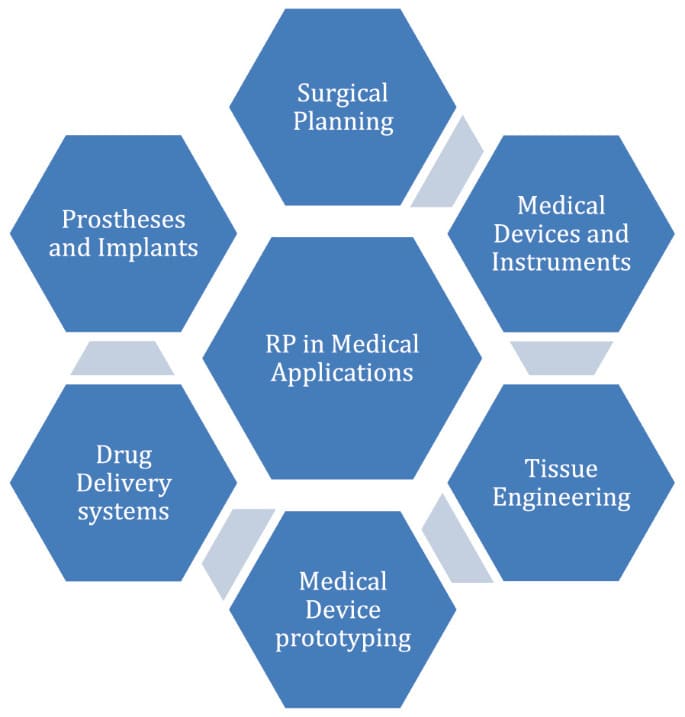
4.Medical Prototyping design application
1.Monitoring and diagnostic fields
Smart wearable health monitor: uses advanced sensor technology to accurately monitor various physiological parameters of patients in real time.
Telemedicine platform: enables remote diagnosis and treatment, greatly improving the accessibility of medical services.
Medical imaging enhancement function: significantly improve the clarity and accuracy of medical images.
Patient monitoring system: Monitor the patient’s vital signs at all times and make every effort to ensure the patient’s safety.
Wearable monitoring equipment: It facilitates patients to self-monitor anytime and anywhere and keep track of their health status.
2.Treatment and therapy
Drug delivery device: Precisely control the dose and time of drug delivery to improve treatment effects.
Virtual reality rehabilitation tools: provide patients with more personalized rehabilitation treatment plans.
Personalized medical platform: Develop exclusive treatment plans based on patients’ specific needs.
Minimally invasive surgical equipment: Reduce surgical trauma and improve the safety and effectiveness of surgery.
Implantable devices: long-term monitoring of the patient’s physiological status, or providing specific therapeutic functions.
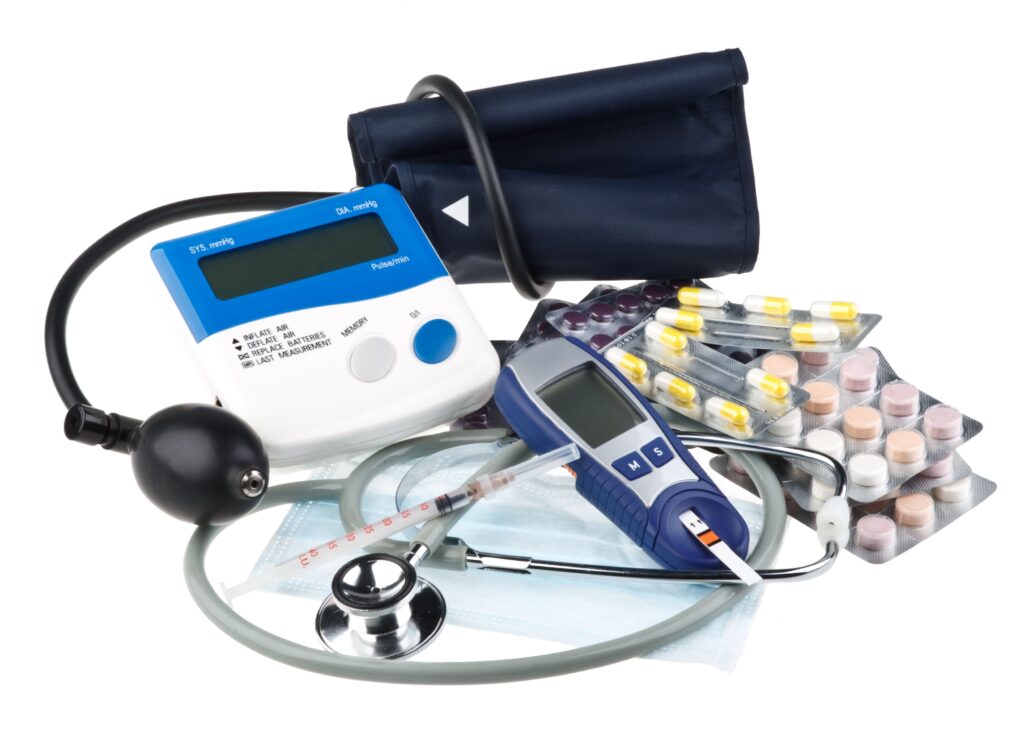
3.Medical auxiliary equipment
Patient-specific surgical instruments: Improve the accuracy and safety of surgery and bring a better treatment experience to patients.
Assistive devices for people with disabilities: Greatly improve the quality of life of people with disabilities and allow them to better integrate into society.
5.Best materials for medical prototype design
1.Corrosion-resistant materials
Stainless steel: It has the advantages of corrosion resistance and wear resistance and is widely used in surgical instruments.
High temperature resistant plastics: It is resistant to high temperatures and creep, and is suitable for medical devices that require high temperature sterilization.
2.Transparent and impact-resistant materials
Polycarbonate: It is light in weight, highly transparent, and highly impact-resistant, and is often used in medical device housings.
3.Chemically stable and biocompatible materials
Polyethylene: It is chemically stable and durable, and can be used in disposable medical products such as intravenous bags and surgical gowns.
Medical grade silicone rubber: It has good biocompatibility, heat resistance, chemical resistance, and electrical resistance, and is suitable for medical products that come into contact with the skin, such as prosthetic skin, medical tape, and wearable medical devices.
4.High-strength materials
Ceramics: It has high biocompatibility and high strength, and can be used in prosthetic joints and dental implants.
Carbon-based materials: It has high strength, light weight, and fatigue resistance, and is suitable for structural components of medical devices, such as parts of diagnostic equipment, treatment machines, and orthopedic equipment.
6.Medical Device Injection Molding
Medical device injection molding is an advanced method of producing medical devices and instruments through the injection molding process. This manufacturing method injects molten plastic into a mold to form the desired shape of the device or component.
Advantages of injection molding services
Precision manufacturing: The size and shape of the device can be accurately controlled to ensure that the product meets medical standards.
Cost-effectiveness: The production cost is low, suitable for large-scale production, and conducive to the mass production of medical devices.
Material diversity: Different types of plastic materials can be selected according to needs to meet the needs of different instruments.
High efficiency: Fast production speed, able to quickly meet market demand.
Finally
Medical prototyping plays an irreplaceable and important role in the development of medical equipment. Medical prototyping covers many fields such as monitoring and diagnosis, treatment and therapy, auxiliary and supporting technologies, and has many advantages. With the continuous advancement of medical technology, medical prototyping will continue to play a key role in promoting the development of the medical industry.