Lubrication and cooling mechanism of metal cutting fluid and its role in machining
Metal cutting fluid, as an indispensable auxiliary material in mechanical machining, plays a vital role in metal cutting and grinding. Its lubrication and cooling mechanism not only affects machining efficiency, but is also directly related to product quality, tool life and production cost.
This article will discuss in detail the lubrication and cooling mechanism of metal cutting fluid and analyze its various roles in metal machining.
1.Lubrication mechanism of metal cutting fluid
The lubrication effect of metal cutting fluid is mainly achieved through the following aspects:
(1) Reducing friction:
During the metal cutting process, there is intense friction between the tool and the workpiece, and between the tool and the chips. The lubricating components in the cutting fluid, such as oiliness, extreme pressure additives, etc., can form a lubricating film between the tool and the workpiece, and between the chips, effectively reducing friction. This lubricating film can penetrate between the tool and the workpiece and its chips, reducing cutting resistance, thereby reducing energy consumption and improving cutting efficiency.
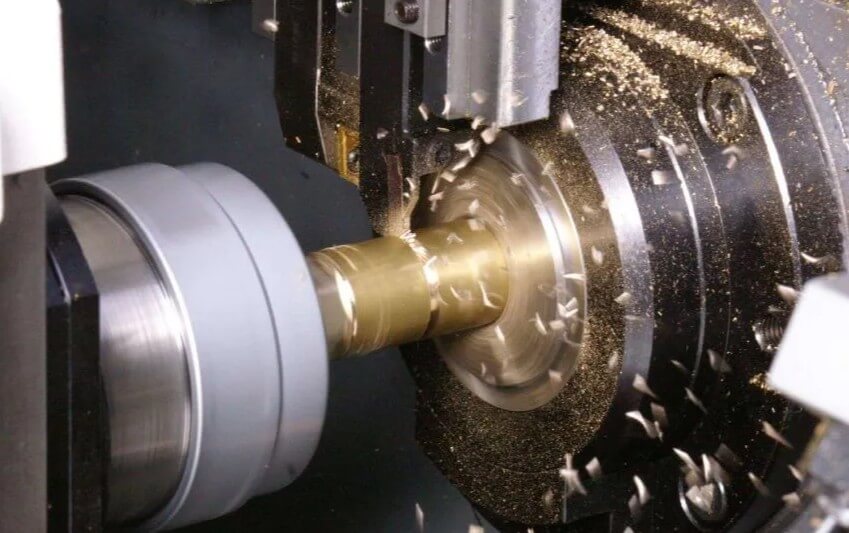
(2) Reducing cutting force:
The formation of the lubricating film not only reduces friction, but also changes the contact state between the tool and the workpiece. The presence of lubricating film reduces the direct contact between the tool and the workpiece, thereby reducing the cutting force. This is particularly important for high-precision machining, because lower cutting force can reduce workpiece deformation and improve machining accuracy.
(3) Extend tool life:
Lubrication reduces friction and wear between the tool and the workpiece and chips, reduces the temperature of the tool surface, and thus extends the tool life. Especially in high-speed cutting and heavy-load cutting, the lubrication effect is particularly effective in protecting the tool.
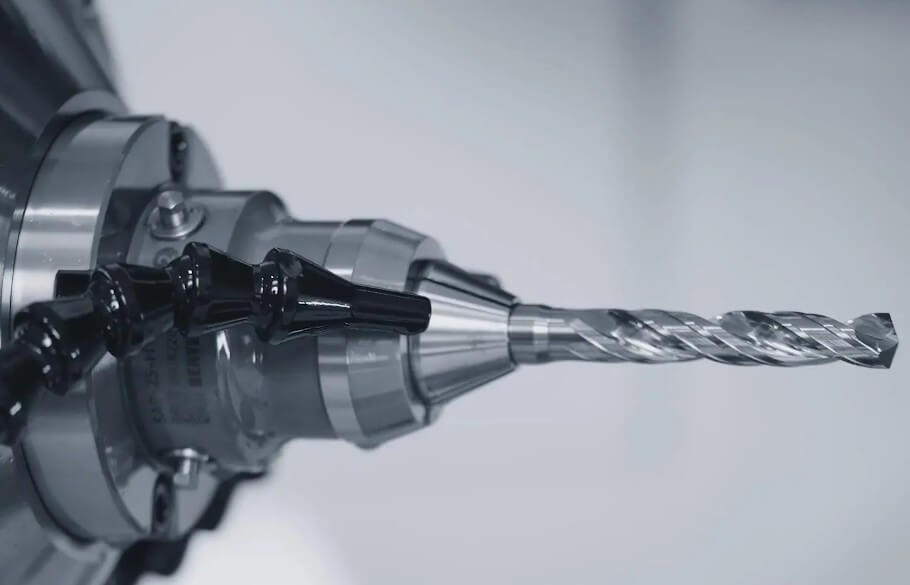
(4) Prevent adhesion:
During the metal cutting process, chips easily adhere to the tool surface, forming built-up edge, which affects the quality of the machining surface. The lubricating components in the cutting fluid can prevent the chips from adhering to the tool surface, keep the tool surface clean, and thus improve the machining quality.
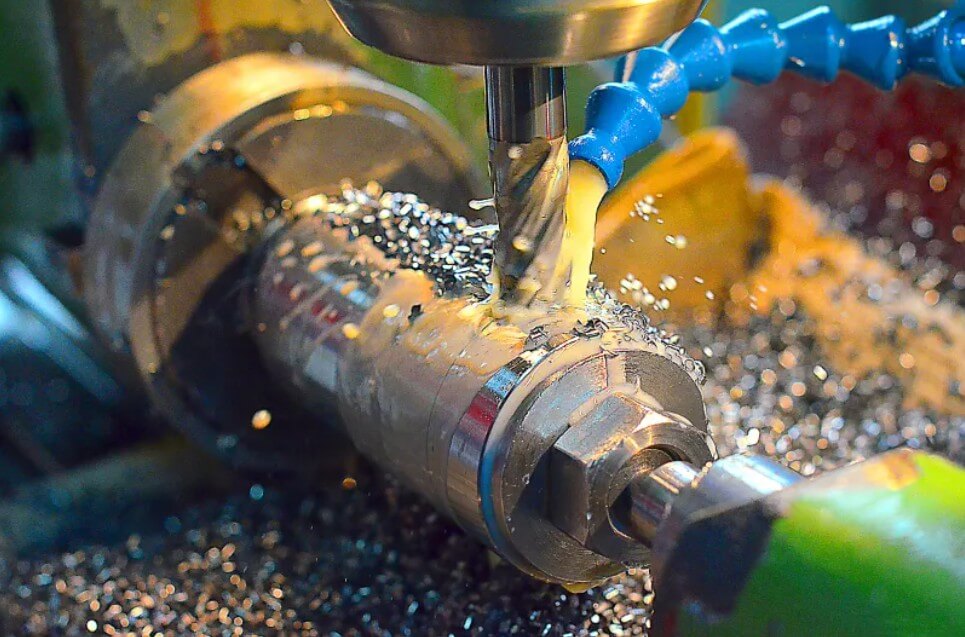
2.Cooling mechanism of metal cutting fluid
The cooling effect of metal cutting fluid is mainly achieved in the following ways:
(1) Heat conduction:
The cutting fluid has good thermal conductivity and can quickly conduct the heat generated during the cutting process away from the cutting area. The cutting fluid has a large thermal conductivity coefficient and can effectively absorb heat from the tool, workpiece and chips, reducing the temperature of the cutting area.
(2) Convection:
The cutting fluid circulates continuously during the cutting process, forming convection and taking away heat from the cutting area. Convection enhances the cooling effect of the cutting fluid, so that the temperature of the cutting area is effectively controlled.
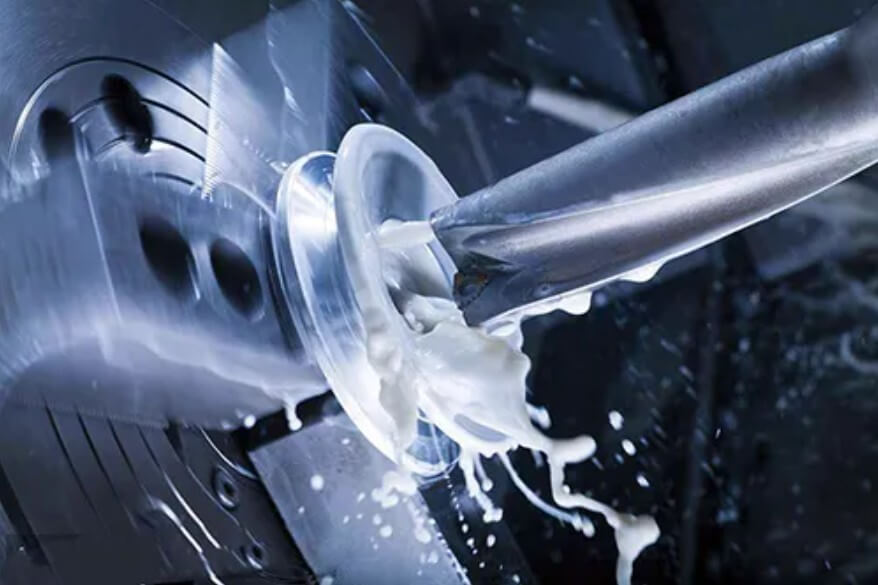
(3) Vaporization:
The cutting fluid will partially vaporize during the cutting process, absorbing a large amount of heat, thereby further reducing the temperature of the cutting area. Vaporization not only directly reduces the cutting temperature, but also takes away part of the heat in the cutting fluid, which helps to maintain the stability of the cutting fluid.
(4) Improve heat dissipation conditions:
The use of cutting fluid improves the heat dissipation conditions of the cutting area. The cutting fluid can flush away chips and dust from the cutting area, preventing them from sticking to each other and adhering to the workpiece, tool and machine tool, thereby maintaining a good heat dissipation environment.
3.The role of metal cutting fluid in processing
The role of metal cutting fluid in metal processing is multifaceted, mainly including the following aspects:
(1) Improve cutting efficiency:
The lubrication and cooling effects of the cutting fluid can reduce cutting resistance, reduce energy consumption and increase cutting speed. Studies have shown that the use of appropriate metal cutting fluids can increase cutting speed by 30% to 40%. This not only improves production efficiency, but also reduces production costs.
(2) Reduce surface roughness:
The lubricating effect of the cutting fluid reduces the friction between the tool and the workpiece, reduces the cutting force, thereby reducing scratches and burrs on the workpiece surface and reducing surface roughness. The use of appropriate cutting fluids can reduce surface roughness by 1 to 2 levels and improve the processing accuracy of the product.
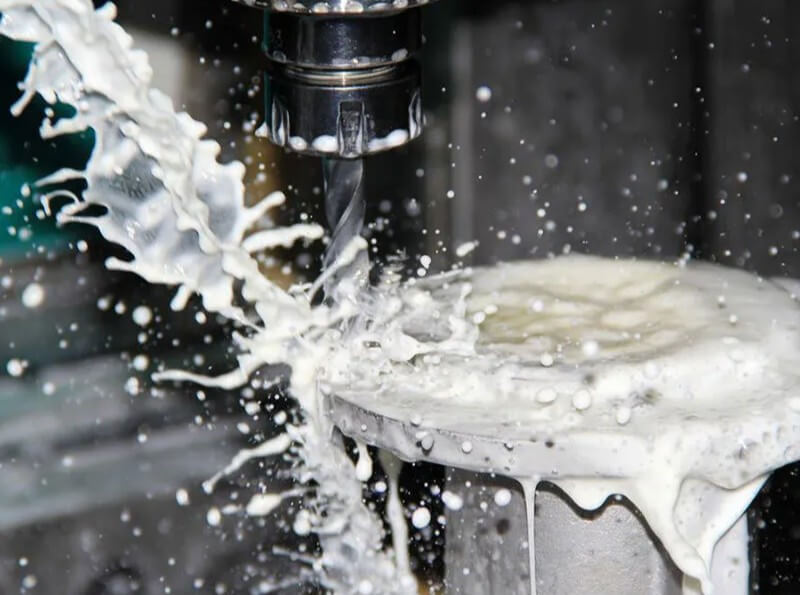
(3) Extend tool life:
The lubricating and cooling effects of metal cutting fluids reduce tool wear and heat accumulation, extending the tool life. Especially in high-speed cutting and heavy-load cutting, the protective effect of cutting fluids on tools is particularly significant, which can double the service life of tools and grinding wheels.
(4) Improve product quality:
The cooling effect of cutting fluids effectively controls the temperature of the cutting area, reduces the thermal deformation of the workpiece, and improves the processing accuracy of the product. At the same time, the washing effect of the cutting fluid washes away chips and dust from the cutting area, preventing them from sticking to each other and adhering to the workpiece, tool and machine tool, thereby ensuring the surface quality and accuracy of the product.
(5) Anti-rust effect:
Metal cutting fluid has certain anti-rust properties, which can prevent workpieces and machine tools from rusting during processing. This not only protects the surface quality of workpieces and machine tools, but also extends their service life.
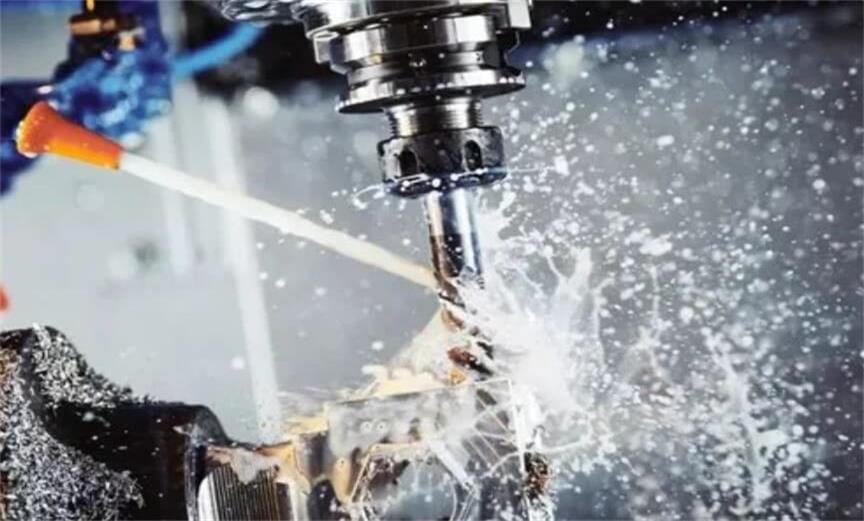
(6) Reduce environmental pollution:
Modern metal cutting fluids pay more and more attention to environmental protection performance in the design and production process. Many cutting fluids use non-toxic, odorless, and harmless ingredients to reduce the harm to operators and pollution to the environment during use. At the same time, the waste liquid treatment technology of cutting fluids is also constantly improving to reduce the negative impact on the environment.
4.Principles for the selection of metal cutting fluids
In efficient processing, the correct selection of metal cutting fluids is crucial, and three aspects need to be considered: process applicability, operating cost and safety.
(1) Process applicability
1) Cutting type:
For high-speed cutting and precision cutting, water-based cutting fluids with better cooling performance are generally selected; for heavy-load cutting and cutting of difficult-to-process materials, oil-based cutting fluids with better lubrication performance are selected.
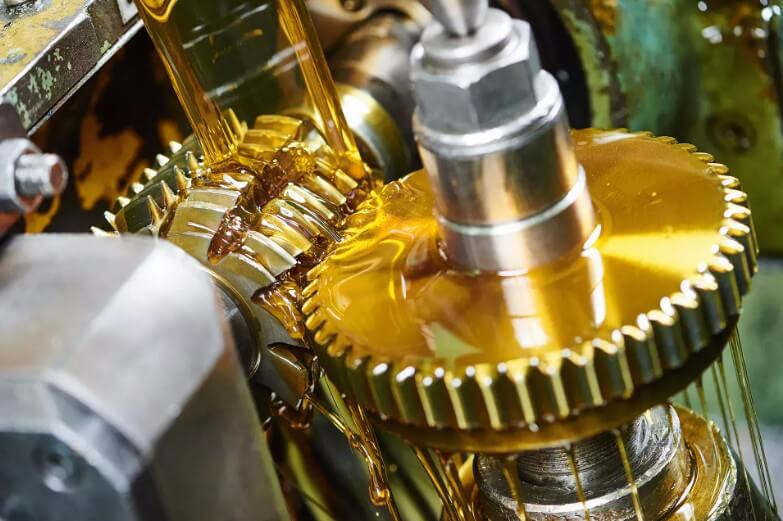
2) Workpiece material:
The processing performance of different materials varies greatly. For example, water-based cutting fluids can be selected for easy-to-process materials such as aluminum alloys and copper alloys, while oil-based cutting fluids are more suitable for difficult-to-process materials such as titanium alloys and stainless steel.
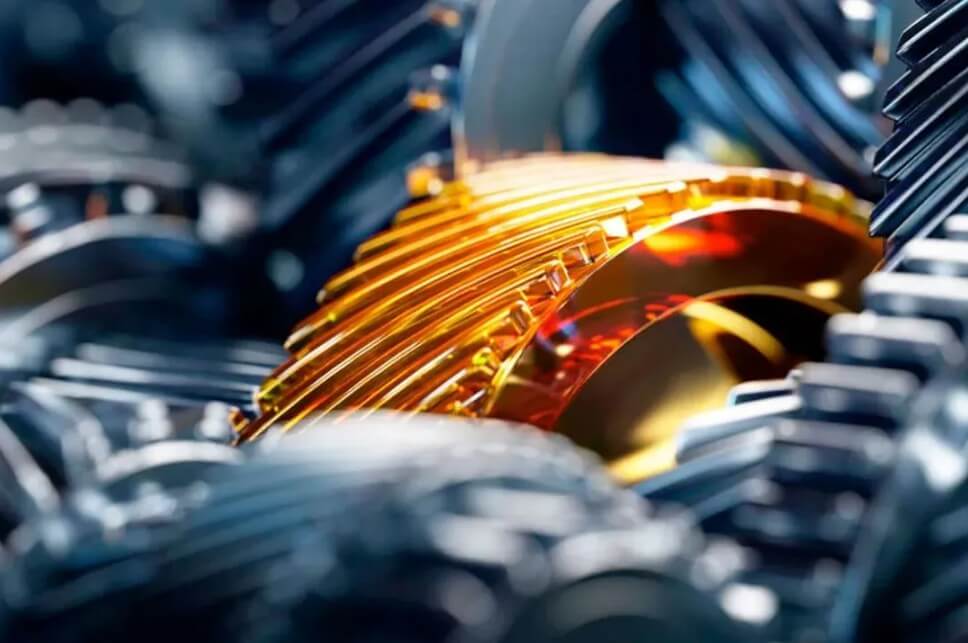
3) Tool material:
Different tool materials have different heat resistance and wear resistance. Choosing the right cutting fluid can increase tool life. For example, carbide tools generally use water-based cutting fluids, while high-speed steel tools are more suitable for oil-based cutting fluids.
(2) Operating cost
1) Cutting fluid cost:
The operating cost of water-based cutting fluids is relatively low, but oil-based cutting fluids have better lubrication and anti-rust properties. In some cases, they can reduce tool wear and workpiece scrapping rates, thereby reducing overall costs.
2) Machine tool maintenance cost:
Different types of metal cutting fluids have different maintenance requirements for machine tools. For example, water-based cutting fluids are prone to breeding bacteria and require regular replacement and cleaning of machine tools, while oil-based cutting fluids are relatively stable.
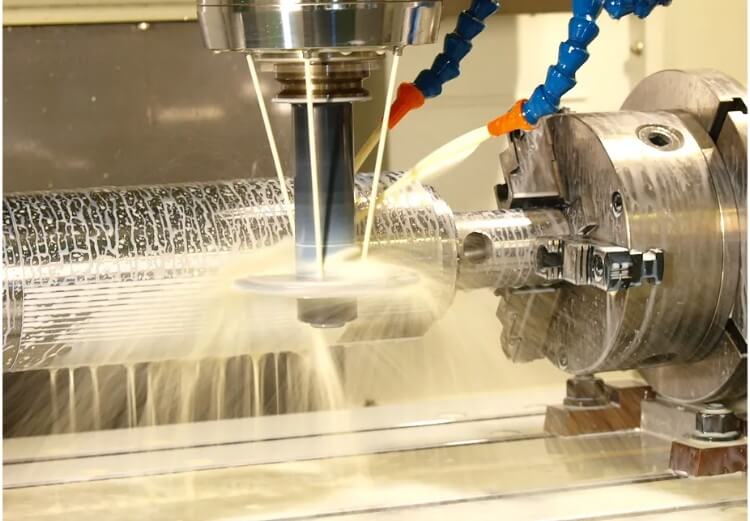
(3) Safety
1) Operator health:
Some cutting fluids contain harmful substances, which may cause harm to the health of operators. Therefore, when selecting cutting fluids, their safety and environmental protection should be considered, and low-toxic and environmentally friendly products should be selected as much as possible.
2) Fire and explosion prevention:
Oil-based cutting fluids have certain fire risks, and corresponding fire prevention measures need to be taken during use and storage.
5.Summary
In summary, the lubrication and cooling mechanism of metal cutting fluids and their role in processing are multifaceted. Reasonable selection of metal cutting fluids can not only improve cutting efficiency and reduce production costs, but also ensure product quality and extend tool life, which is of great significance to the development of the mechanical processing industry.
3 Comments