Metal cutting tools: micro-tool technology in precision machining
Metal cutting tools play a vital role in modern manufacturing. With the continuous advancement of industrial technology and the diversification of manufacturing needs, the types and functions of metal cutting tools are also constantly developing. From traditional turning and milling to modern high-speed cutting and high-precision machining, the performance of the tool directly affects the processing efficiency, product quality and production cost.
Therefore, in-depth understanding and mastering of the basic knowledge, selection methods, application skills and development trends of metal cutting tools is of great significance to improving the level of manufacturing. This article aims to comprehensively analyze metal cutting tools and explore their production, selection, use and optimization as well as development trends.
1.Basic knowledge of metal cutting tools
(1) Definition
Metal cutting tools are an indispensable and important tool in the manufacturing industry. Their quality and performance directly affect the efficiency, accuracy and cost of machining. Tools perform cutting, drilling, milling and other operations on metal workpieces through their specific geometric shapes and material properties, and are the key to achieving material removal and forming.
(2) Importance
Its importance lies in improving production efficiency, ensuring machining accuracy and reducing production costs. High-quality cutting tools can extend their service life and reduce the frequency of replacement, thereby reducing downtime and improving production efficiency. At the same time, precise cutting can reduce the workload of subsequent processing and improve the quality of workpieces. Reasonable selection and use of cutting tools can also reduce material loss and production costs. In modern manufacturing, metal cutting tools play an indispensable role and are one of the important tools to promote industrial development.
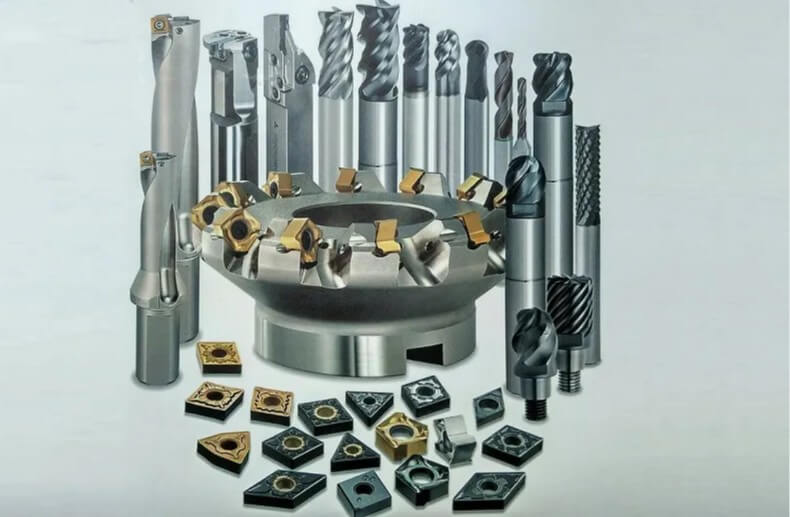
(3) Structural composition of cutting tools
Metal cutting tools usually consist of three parts: the cutter head, the cutter body and the cutter handle. The cutter head is the part directly involved in cutting, and its material and geometry have a decisive influence on the cutting performance; the cutter body provides the necessary strength and rigidity to support the cutting action of the cutter head; the cutter handle is used to connect with the machine tool to ensure the stability and accuracy of the tool during processing.
2.Classification of metal cutting tools
Metal cutting tools, as an indispensable tool in modern industrial manufacturing, have a wide variety of types and different functions. In order to better understand and use these tools, we can classify them from two dimensions: purpose and material.
(1) Classification by purpose
Metal cutting tools can be roughly divided into the following categories according to their purpose:
1) Turning tool:
Mainly used for lathe processing, suitable for rotating surface cutting of various metal materials. Turning tools can be divided into external turning tools, internal hole turning tools, etc. according to different processing requirements.
2) Milling cutter:
Used on milling machines, used for processing planes, grooves, forming surfaces, etc. Common milling cutters include face milling cutters and end milling cutters.
3) Drill bit:
Used for drilling holes in metal. According to the different diameters and depths of the holes, different types of drill bits can be selected, such as twist drills, deep hole drills, etc.
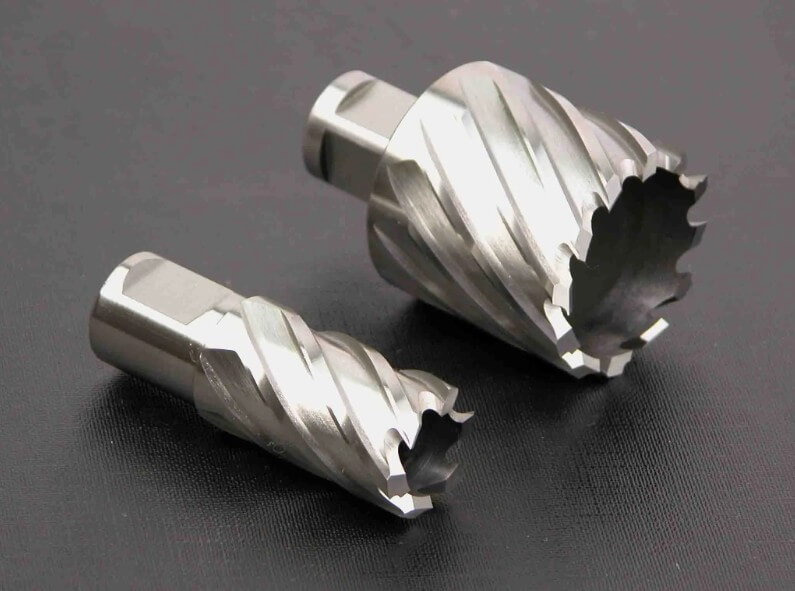
4) Boring tool:
Suitable for enlarging and finishing existing holes, often used for high-precision hole processing.
5) Tap:
Specially used for processing internal threads, forming threads by cutting metal.
(2) Classification by material
The performance of the tool material directly affects its cutting efficiency and durability. Common tool materials include:
1) High-speed steel:
It has good strength and toughness and is widely used in the production of various cutting tools. However, its hardness is relatively low and its wear resistance is not as good as other advanced materials.
2) Cemented carbide:
It is composed of high-hardness metal carbides and binders, has extremely high hardness and wear resistance, and is suitable for processing a variety of metal materials.
3) Ceramic tools:
With alumina or silicon nitride as the main component, it has extremely high hardness and high temperature resistance, but its strength and toughness are relatively poor.
4) Superhard tool materials:
Such as diamond and cubic boron nitride, it has the highest hardness and wear resistance, and is suitable for processing high-hardness materials such as hardened steel and cemented carbide.
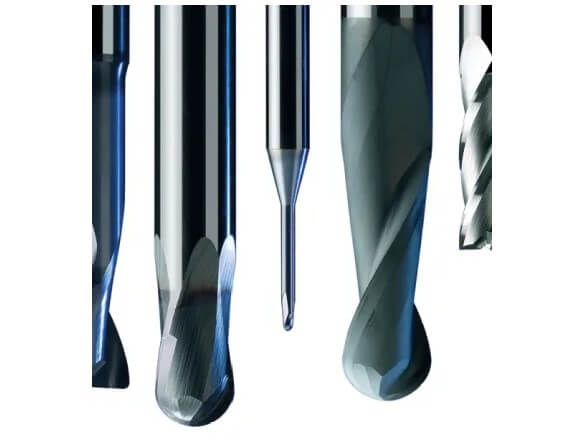
Through the above classification, we can better select the appropriate metal cutting tool according to the specific processing requirements and material properties, thereby improving processing efficiency and quality.
3.Tool selection and cutting parameter optimization
(1) Select the appropriate type of metal cutting tool
Selecting the appropriate type of tool is the key to ensuring processing efficiency and product quality. The selection of metal cutting tools should be based on the characteristics of the material being processed, the type of machine tool, and the specific processing requirements. For example, when processing high-hardness materials such as titanium alloy, carbide tools or ceramic tools should be used; while for softer materials such as aluminum alloy, high-speed steel tools may be more suitable.
(2) Determination of cutting parameters
Cutting parameters include cutting speed, feed rate and cutting depth. The reasonable setting of these parameters is crucial to improving processing efficiency and tool life. The selection of cutting speed should take into account the heat resistance of the tool material and the hardness of the workpiece; the feed rate needs to be determined based on the strength of the tool and the processing accuracy of the workpiece; the selection of cutting depth should balance the requirements of processing efficiency and surface quality.
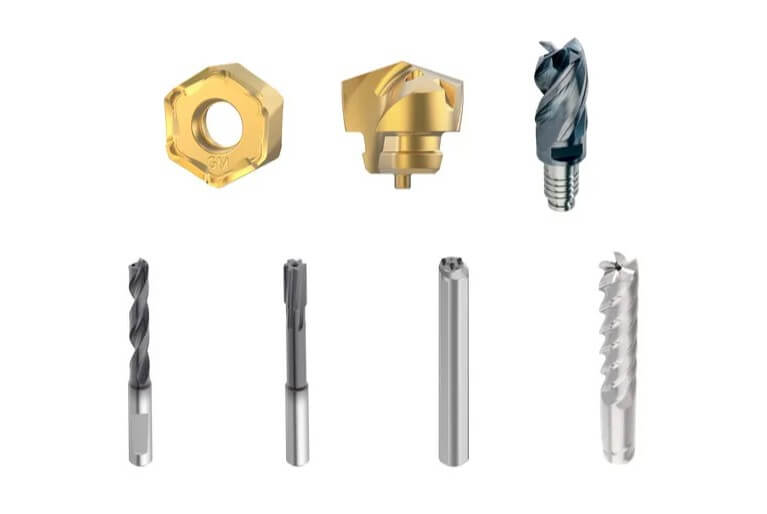
4.Selection and optimization of geometric angles of metal cutting tools
(1) Importance and basic concepts of tool angles
The geometric angle of the tool has a decisive influence on its cutting performance. The main tool angles include rake angle, back angle, main rake angle and secondary rake angle.
1) Rake angle:
affects the size of cutting force and chip formation. The larger the rake angle, the smaller the cutting force and the lighter the cutting, but the strength of the tool will be reduced.
2) Back angle:
reduces the friction between the back face of the tool and the workpiece, and improves the quality of the processed surface.
3) Main rake angle and secondary rake angle:
affect the cutting width and depth, as well as the durability and cutting stability of the tool.
(2) How to select the tool angle according to the processing material and process
Selecting the correct tool angle can significantly improve cutting efficiency and workpiece surface quality. For example, when processing plastic materials, a larger rake angle should be selected to reduce cutting force; while when processing hard and brittle materials, a smaller rake angle should be selected to increase tool strength. In addition, when processing high-hardness materials, a larger back angle should be selected to reduce friction and tool wear.
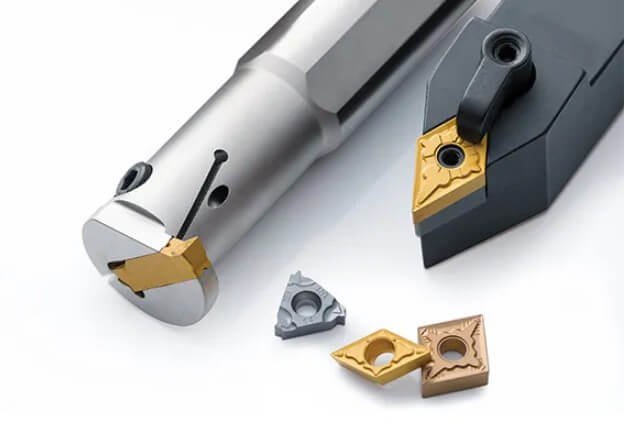
(3) Optimization design of tool angle
Modern metal cutting tool design can accurately optimize tool angles, improve cutting efficiency, reduce wear, and extend tool life through technologies such as computer-aided design (CAD) and finite element analysis (FEA). For example, the use of multi-axis linkage CNC machine tools can realize the processing of complex tool paths, thereby improving processing accuracy and efficiency.
5.Application of metal cutting tools in modern manufacturing industry
(1) Tool selection and use in CNC machining
The widespread application of CNC machining technology has put forward higher requirements for the selection and use of tools. CNC tools need to be selected according to the specific processing materials, machine tool performance and processing requirements to ensure processing accuracy and efficiency.
1) Characteristics and requirements of CNC tools:
CNC tools usually need to have high accuracy and durability to meet the needs of high-speed and high-precision processing. In addition, the structure and material of CNC tools should be suitable for automated production to reduce the time of tool change and adjustment.
2) Optimization of tool paths in CNC machining:
Reasonable tool path planning can reduce idle time and improve machining efficiency. Using CAM software to optimize tool paths can ensure the stability and efficiency of tools during machining.
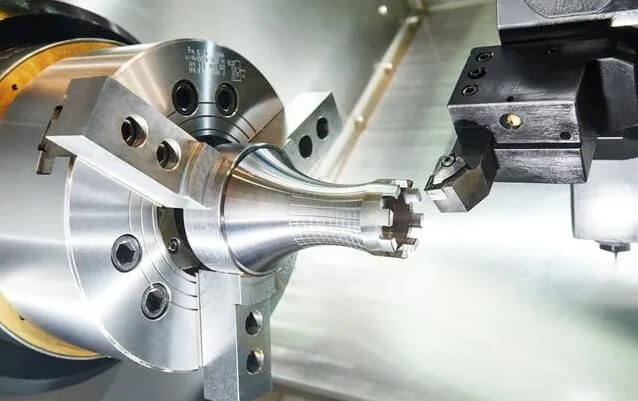
(2) Tool solutions for difficult-to-machine materials
With the development of aviation, aerospace and energy fields, the use of difficult-to-machine materials such as high-temperature alloys and titanium alloys is increasing. The cutting of these materials puts higher requirements on tools.
Processing strategies for high-temperature alloys, titanium alloys, etc.:
For these difficult-to-machine materials, tool materials with high hardness and high wear resistance, such as CBN and PCD, are usually selected. In addition, the use of special tool geometry design and coating technology can effectively reduce tool wear and improve machining efficiency.
(3) Application of tools in automated production lines
In modern automated production lines, the management and use of tools directly affect production efficiency and cost. Flexible manufacturing systems and automated tool management systems can realize automatic selection and replacement of tools, improving the flexibility and automation level of production lines.
Flexible manufacturing systems and tool management:
Flexible manufacturing systems (FMS) integrate functions such as tool presetting, tool monitoring and tool life management, and can monitor the status of tools in real time to ensure the continuity and stability of production.
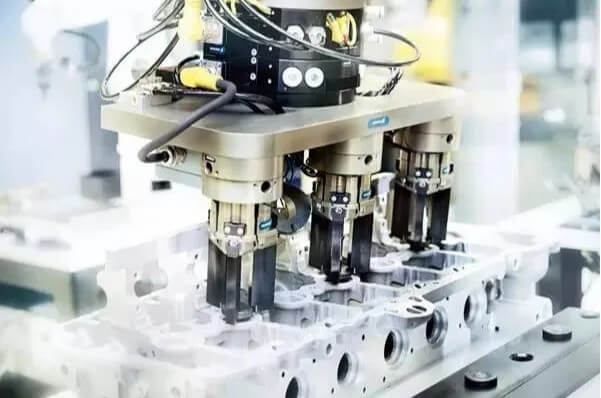
6.Wear and life management of metal cutting tools
(1) Types of metal cutting tool wear
Metal cutting tools will gradually wear out during the cutting process. The main types include mechanical wear, thermal wear and chemical wear. Mechanical wear is caused by friction between the tool and the workpiece; thermal wear is caused by softening of the tool material due to high temperature; and chemical wear is the result of a chemical reaction between the tool material and the workpiece material.
(2) Factors affecting the life of metal cutting tools
The life of metal cutting tools is affected by various factors, including tool material, cutting parameters, and the use of coolant. Selecting appropriate tool materials and optimizing cutting parameters are the key to extending tool life. In addition, appropriate coolant can reduce cutting temperature and thermal wear, thereby extending the service life of the tool.
(3) Strategies to extend the life of metal cutting tools
In order to extend the service life of metal cutting tools, reasonable use and maintenance strategies can be adopted, such as regular sharpening and the use of tool coating technology. Tool coating can significantly improve the wear resistance and thermal hardness of the tool, thereby extending the service life of the tool. In addition, reasonable tool storage and maintenance are also important measures to ensure tool performance.
The production of cutting tools involves a variety of precision processing methods, each of which has its own unique advantages and scope of application. The following are several common methods for making cutting tools:
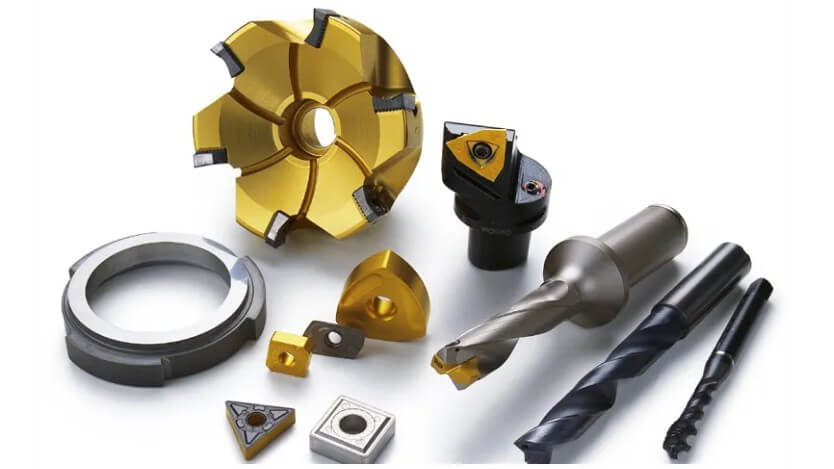
7.Methods for making metal cutting tools
(1) Machining method:
The metal blank is cut by lathes, milling machines and other machine tools to obtain precise tool shapes and sizes. Machining methods are suitable for the production of various types of tools, especially tools with high precision requirements, such as drills, milling cutters, etc.
(2) Electrospark machining:
Electrospark machining (EDM) is a method of machining tools by discharging and corroding materials. This method is particularly suitable for machining tools with high hardness and complex shapes. Electrospark machining can be performed without contacting the tool material, thus avoiding mechanical damage to the tool surface.
(3) Laser machining:
Laser machining is a method of cutting, drilling or surface treatment of materials using a high-energy laser beam. In tool manufacturing, laser machining can be used for precise cutting and etching, as well as texturing or coating on the tool surface to improve tool performance.
(4) Chemical vapor deposition:
Chemical vapor deposition (CVD) is a method of depositing a hardened coating on the surface of a tool. By converting a gas precursor into a solid coating at high temperature, CVD can significantly improve the wear resistance and corrosion resistance of the tool. This method is often used to make high-performance metal cutting tools.
(5) Powder metallurgy:
Powder metallurgy is a method of manufacturing tools by pressing metal powder into a shape and sintering it. This method can achieve material uniformity and high hardness, and is particularly suitable for manufacturing metal cutting tools with complex alloy components. Powder metallurgy tools generally have excellent mechanical properties and thermal stability.
(6) Precision grinding:
Precision grinding is a method of high-precision machining of tools using grinders and abrasives. This method can achieve micron-level precision of the tool, ensuring that the tool has extremely high sharpness and durability. Precision grinding is often used to make high-precision metal cutting tools, such as cutting knives, milling cutters, etc.

(7) 3D printing:
3D printing technology, also known as additive manufacturing, is a method of rapid prototyping and direct manufacturing. In tool manufacturing, 3D printing can be used to make tools with complex geometries, especially those that are difficult to process by traditional methods. By stacking materials layer by layer, 3D printing can achieve highly customized and complex tool manufacturing.
8.Modern metal cutting tool technology and development trends
(1) Research and development of new tool materials
With the advancement of materials science, new tool materials are constantly emerging, such as superhard materials and high-performance coatings. These new materials have higher hardness, wear resistance and thermal stability, and can meet the needs of high-speed and high-precision cutting. For example, polycrystalline diamond (PCD) and cubic boron nitride (CBN) tools perform well when processing hard materials.
(2) Advances in metal cutting tool manufacturing technology
The application of modern manufacturing technologies such as precision grinding and 3D printing technology has significantly improved the manufacturing accuracy and efficiency of metal cutting tools. These technologies can produce tools with complex geometric shapes to meet various special processing requirements.
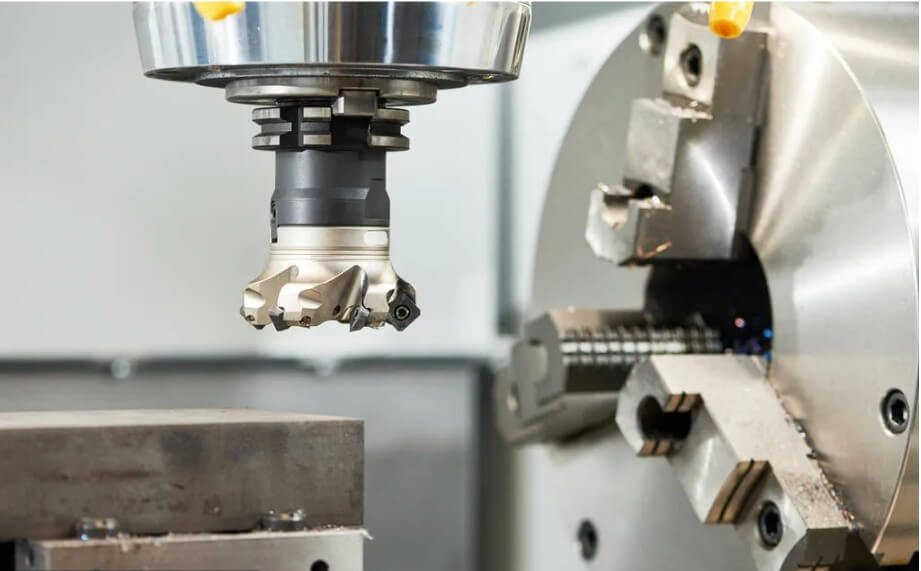
(3) Application of intelligent tools
With the development of intelligent manufacturing, the application of intelligent tools is becoming more and more extensive. These tools are equipped with sensors and monitoring systems, which can monitor the cutting status in real time and automatically adjust the cutting parameters, thereby optimizing the cutting process and improving processing efficiency and tool life.
9.Summary
Through an in-depth analysis of the classification, material properties, optimization of cutting parameters and geometric angles, and manufacturing processes of metal cutting tools, we understand that the rational selection and use of metal cutting tools is of great significance to improving production efficiency and product quality. In addition, the application of new tool materials and manufacturing technologies, as well as the development of intelligent tools, will further promote the advancement of metal cutting tool technology.
3 Comments