Introduction to Custom Metal Parts Manufacturing
Custom metal parts manufacturing is a complex and intricate process that involves the creation of metal components tailored to specific requirements. These parts are used in a wide range of industries, including automotive, aerospace, electronics, and construction. In this article, we will explore the various steps involved in the manufacturing of custom metal parts and the importance of precision and quality in this process.
Steps in Custom Metal Parts manufacturing
The first step in custom metal parts manufacturing is the design phase. This is where engineers and designers work closely with clients to understand their needs and specifications. The design phase involves creating detailed drawings and 3D models of the desired metal parts. This step is crucial as it lays the foundation for the entire manufacturing process.
Once the design is finalized, the next step is material selection. The choice of material depends on factors such as the intended use of the metal part, its required strength and durability, and the client’s budget. Common materials used in custom metal parts manufacturing include steel, aluminum, brass, and titanium. Each material has its own unique properties and characteristics, which must be carefully considered to ensure the final product meets the desired specifications.
After material selection, the manufacturing process begins with cutting and shaping the metal. This is typically done using advanced machinery such as CNC (Computer Numerical Control) machines. These machines use computer-aided design (CAD) software to precisely cut and shape the metal according to the design specifications. This step requires skilled operators who can program and operate the machines with precision.
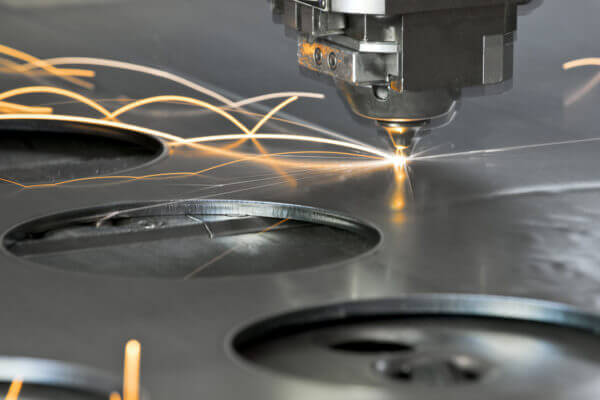
Once the metal is cut and shaped, the next step is to join the different pieces together. This step can be accomplished by various methods, such as welding, soldering or fastening with screws or bolts. The choice of joining method depends on factors such as the type of metal used, the strength requirements of the part, and customer preference. The most important thing is to make sure the joints are strong and secure to prevent any potential malfunctions or accidents.
After the metal parts are joined together, they undergo a series of finishing processes. These processes include grinding, polishing and coating to enhance the appearance and protect the metal from corrosion. At the same time, the finishing process also helps improve the overall quality and durability of custom metal parts.
Quality control is a critical aspect of custom metal parts manufacturing. Throughout the entire manufacturing process, strict quality control measures are implemented to ensure that the final product meets the required specifications. This includes regular inspections, testing, and documentation of all manufacturing processes. Any deviations or defects are identified and rectified to ensure that only high-quality metal parts are delivered to the clients.
In conclusion, custom metal parts manufacturing is a complex process that requires careful planning, precision, and attention to detail. From the initial design phase to the final finishing processes, every step is crucial in creating custom metal parts that meet the specific requirements of clients. By following strict quality control measures and utilizing advanced manufacturing techniques, manufacturers can ensure the production of high-quality metal parts that are durable, reliable, and tailored to the needs of various industries.