Differences Between Milling and Turning
In subtractive manufacturing, unique processes produce unique shapes, finishes, and tolerances as excess material is removed from a preformed blank to create the desired part. Each process has its own strengths and limitations and is suited to specific jobs.
As machining technology advances, the lines between processes are blurring, so in this blog, we will keep it simple and consider the two processes, milling and turning, as distinct principles.
Before we discuss the differences, let’s look at the similarities between milling and turning. Both are subtractive manufacturing: layers of a solid block are removed to form the intended product, while additive manufacturing is where layers are added to the block.
Both turning and milling are traditional machining processes that use a specially designed cutting tool to compress a layer of workpiece material and shear it off the workpiece. Both generally produce a fairly good finish, and both use cutting fluids to offset the heat generated by both processes.
What is the difference between milling and turning?
Well, everything else is pretty much the same. Traditionally, turning is used to make cylindrical or tapered parts from bar stock, while milling makes parts from block stock on a flat surface. Considering all the machining innovations of the past three decades, including but not limited to live tooling, rotary tables, 5-axis capabilities, and more, here is a basic overview of the differences between milling and turning.
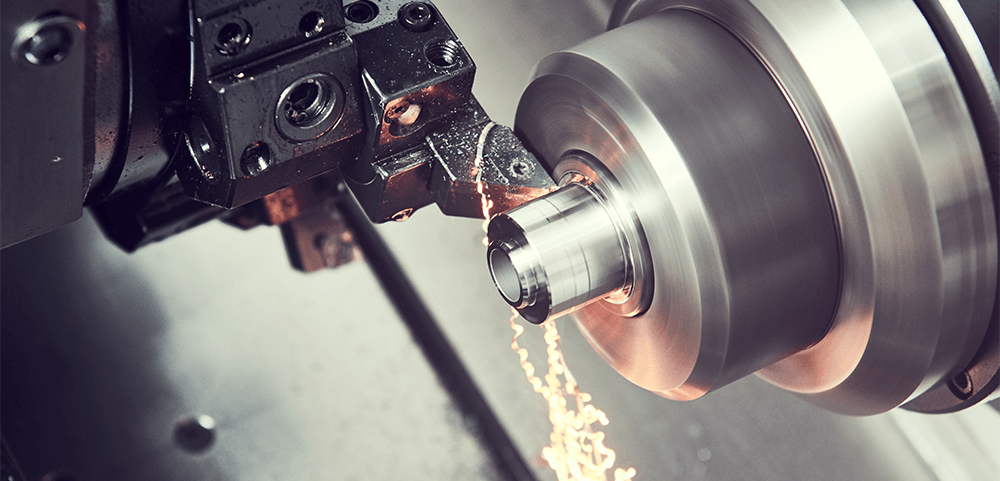
During turning, the cutting tool is fixed in place while the workpiece moves and rotates (literally “turns”) at a fixed RPM on a rotating axis called a lathe; the rotation of the workpiece (not the cutting tool) provides the speed required for forming.
Typically, if the workpiece is round, turning is required. Therefore, the process is used to make washers, bolts, ball bearings, etc.
The turning process is well suited for parts that need to be symmetrical about their central axis, and turned parts can generally be produced faster and at a lower cost than milled parts, making turning ideal for producing large quantities of parts.
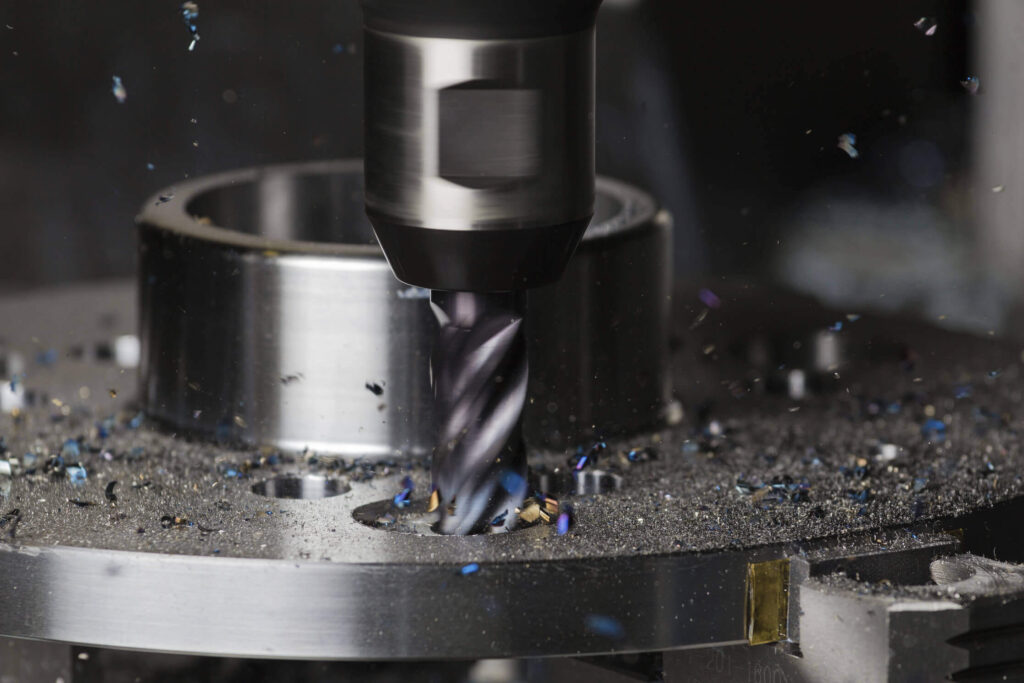
Milling uses a multi-point cutting tool (called a milling cutter) that spins at the necessary RPM to cut the workpiece. Notice the difference? The milling cutter spins, not the workpiece.
In fact, this is the main difference between milling and turning. The milling process keeps the workpiece stationary while the tool moves around the workpiece’s X, Y, and Z axes.
Machinists use milling not just as a secondary operation on an already manufactured part to add slots, threads, and holes to create a workpiece from scratch, but they are also used to make short-run production parts, precision assemblies, and prototype parts.
We often think of milling and turning as mutually exclusive, but they can be used together, even simultaneously!
At Xavier, we’re investing in the machining technology of the future, like 5-axis milling machines, a machine that works on 5 axes to make the exact parts you need in one powerful (and smart) machine.
Whether you need turning, milling, or a combination of both, Xavier has the equipment and experience to make the parts (and quantities) you need.