Milling vs. Turning of Plastic Parts: Which Option Is Best for Your Part?
Understanding the differences between milling of plastic parts and turning of plastic parts will help you decide which option is best for your project. Because CNC machining is a common method for molding plastic parts because it ensures dimensional accuracy, which is critical for functional plastic parts. Tolerances can be tightly controlled, ensuring consistent part quality.
Whereas milling and turning are two common methods for machining plastics. While both fall under the umbrella of CNC machining, they do and process differently.
1.Understanding CNC Machining
While CNC has become a common term, it is an abbreviation for computer numerical control. The machine produces high-precision parts directly from a CAD or CAM file.
G-codes and M-codes are part of CNC programming and instruct the machine to perform actions (e.g., move to a location, adjust spindle speed) and manage machine functions (e.g., start, stop, change tooling), respectively. These codes are essentially sequences of numbers that control the behavior of a CNC machine, hence the term numerical control.
The ability to CNC machine plastics is a boon to many industries. Plastics are increasingly replacing metals in a variety of applications because they are lightweight and many have comparable mechanical properties and chemical resistance.
While plastics and metals are machined the same way, properties such as thermal expansion, softening temperature, and elasticity make parts more challenging to produce. Part manufacturers must consider polymer selection, tooling, feed rates, stabilization methods, and more to achieve quality results.
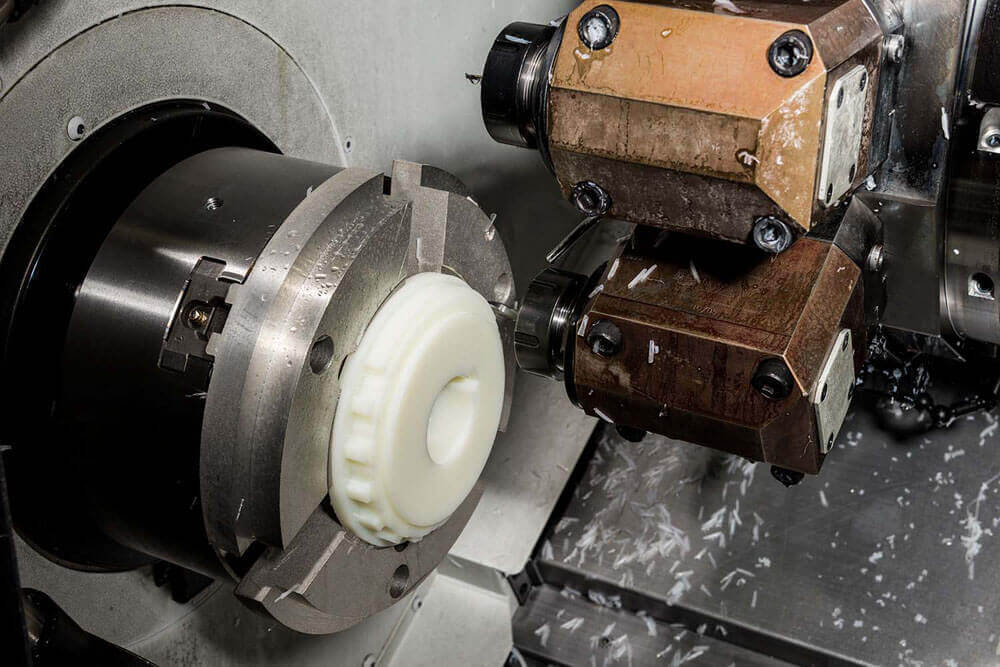
2.Milling of plastic parts vs. turning of plastic parts: Choosing the right method
Consider the following factors when deciding whether to machine plastic parts by milling or turning:
- Design requirements: Does your design require flat surfaces, complex shapes, cylindrical or symmetrical features?
- Material properties: Different plastics have unique properties—some can bend or break if not handled properly.
- Precision: What level of precision does your project require?
Remember that every project is unique, and the choice between milling of plastic parts and turning of plastic parts depends on your specific requirements.
Understanding these methods will allow you to work with your machining partner to make the right decision for your plastic parts. Since plastics behave differently than metals when machined, always work with a supplier that has experience machining plastics.
Below, we discuss the differences between milling and turning plastics.
3.What is milling?
CNC milling involves the high-speed rotation of a cylindrical cutting tool to remove plastic chips from a stationary workpiece. When milling, the workpiece usually remains stationary. The cutting tool performs work in a linear manner but can operate on multiple axes, giving it the flexibility to handle complex parts. Such machines are called CNC milling machines.
There are two different processes for milling plastics: climb milling (also known as climb milling) and reverse milling (also known as up-cut milling). The difference between them is the direction in which the tool rotates and the direction in which it is fed.
In climb milling, the tool rotates and is fed in the same direction. The cutting edge initially contacts the workpiece at its thinnest point, and as the cutting edge advances, the material thickness gradually increases. The chips move downward in the same direction as the tool is rotating. Climb milling is generally preferred when milling plastics.
In reverse milling, the tool rotates in the opposite direction of the feed direction. As the cutting edge contacts the material and shears it off the workpiece, the chips travel upward against the feed direction. In contrast to down milling, up milling produces thick initial chips that become thinner and less numerous as the cut progresses.
The challenge with up milling is that the chips are thick and hot. The heat generated melts the plastic, causing it to stick to the tool and potentially degrade the cut quality.
Whether up or down milling, the three common milling techniques used are end milling, peripheral milling, and step milling.
End milling involves cutting with a tool that has teeth on the end and sides to create a slot, groove, or profile on the workpiece. Peripheral milling uses a tool with teeth on the circumference to remove material from the surface of the workpiece and is typically used to create a flat surface or precise shape. Step milling involves making continuous step cuts to achieve a specific profile or feature on the workpiece and is typically used to create shoulders, grooves, or steps.
CNC milling excels at creating flat or complex shapes on plastic parts. However, the process generates heat that can negatively affect plastic parts if not controlled.
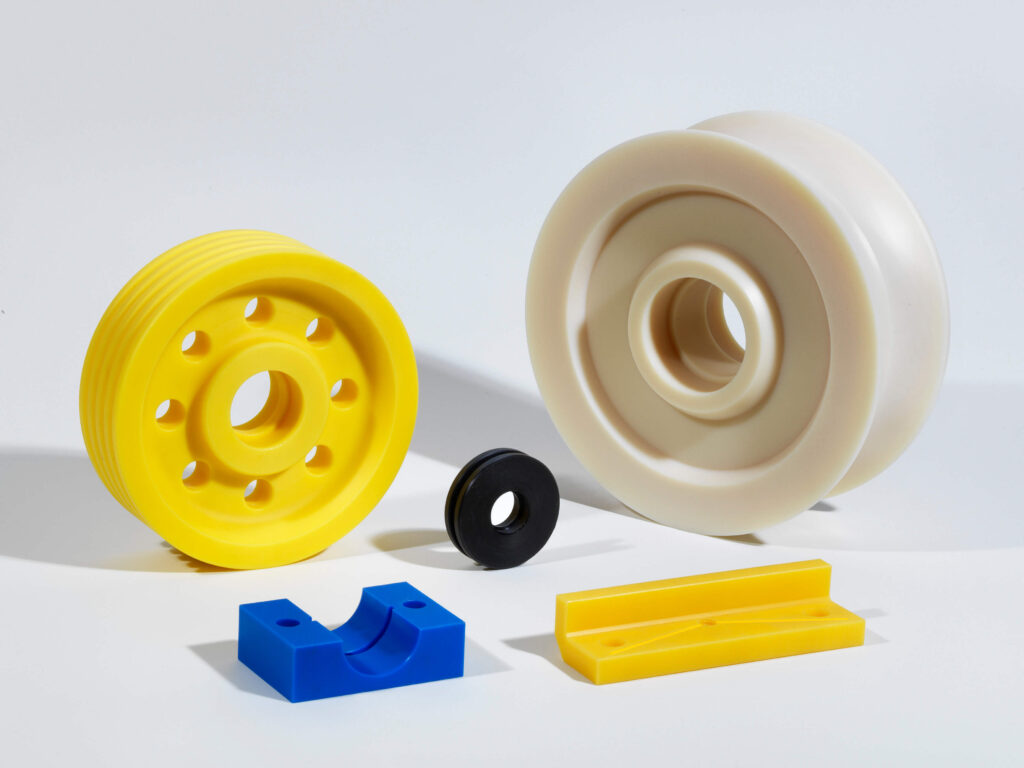
4.Understanding Turning
CNC turning is performed on a lathe. One difference from milling is that the plastic workpiece rotates about its axis, while the cutting tool is stationary as it is formed.
Manufacturers of turning of plastic parts must use the proper cutting tools, cutting speeds, and stabilization and cooling methods to achieve the best results.
Turning excels at making turning of plastic parts with cylindrical or symmetrical features. It is ideal for making rods, tubes, bushings, and other parts with a central axis.
Unlike the multi-axis tool motion of milling, turning relies primarily on the rotation of the workpiece and the linear motion of the cutting tool. This simplicity means that these rotationally symmetrical parts can be produced efficiently.
Like milling, plastic turning has some considerations. The choice of cutting tool is critical. Sharp, high-quality carbide inserts are preferred because they cut cleanly and minimize friction, which can generate unnecessary heat.
Maintaining proper speeds and feed rates is also important. Certain plastics often require lower speeds to prevent melting or burning at the cutting point.
Milling has a distinct advantage over turning – the production of continuous chips. This eliminates chip re-cutting, a potential problem in milling that can lead to a poor surface finish.
In addition, turning generally produces a smoother surface finish on the final part due to the continuous contact between the cutting tool and the rotating workpiece.
However, turning also has limitations. It is not suitable for creating complex geometries with intricate features on multiple planes. For these cases, the multi-axis capabilities of milling are a better fit.
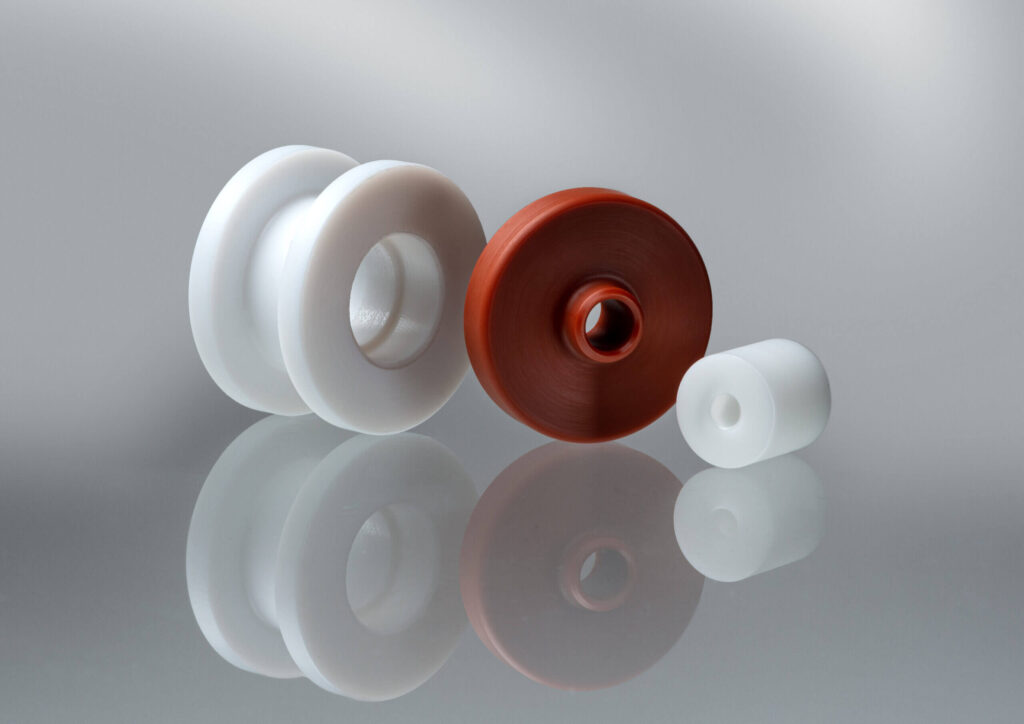
5.Choose an Experienced Partner
Plastics require different machining techniques than metals, so it is critical to work with an experienced plastics machining partner.
They understand the nuances and can machine your parts with the right speeds, feeds and tools to avoid warping, melting or cracking the material.
There are many different types of plastics, each with its own properties. An experienced plastics partner can help you select the right material for your application, considering factors such as strength, flexibility, heat resistance and chemical resistance.