Basic Overview of Nickel Plating and Chrome Plating
In the modern industrial field, surface treatment technology plays a vital role in improving product performance and appearance. Among them, nickel plating and chrome plating are two common electroplating methods, which are widely used in various industries. They each have unique characteristics and advantages, and there are obvious differences in physical and mechanical properties, appearance, durability, maintenance and cost. Next, we will delve into the basic overview of nickel plating and chrome plating, the main differences, and their uses in different fields.
1.What is nickel plating?
It is the process of forming a nickel layer on the surface of a part or product. The coating method can be either electrolytic or chemical. Moreover, it is not limited to metal surfaces. Nickel can also be plated on certain plastics. Moreover, nickel plating produces a more uniform coating. It can easily coat complex shapes and geometries. Therefore, a wide range of layer thicknesses can be achieved. Chemical nickel coating can deposit thick layers.
Characteristics of nickel plated parts
- Excellent corrosion resistance, thermal and electrical conductivity
- Silvery white with a slight golden hue
- Coating hardness up to Rockwell 63 (chemical plating)
- Minimal fading over time
- Adds magnetism to non-magnetic substrates
- Excellent adhesion
2.What is chrome plating?
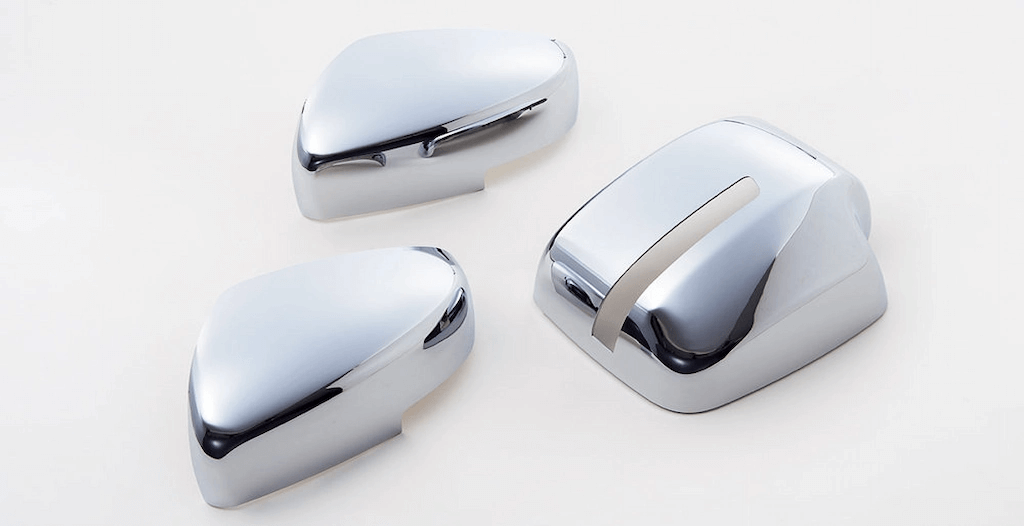
Chrome or chromium is a steel grey hard metal. It has excellent hardness, wear resistance, and corrosion resistance. Subsequently, these properties make it a suitable electroplated metal for a variety of applications. The hardness of chrome plating is higher if we compare nickel with chrome plating.
3.What are the main differences between nickel plating and chrome plating?
Now that we know the basics of both plating methods, let’s compare them from different aspects. How do they look? Their characteristics, cost, and more factors.
①Physical and Mechanical Properties
Chrome-plated parts are generally tougher and more durable, especially with hard chrome surfaces. On the other hand, chrome has a lower ductility and a higher risk of cracking under stress. Therefore, the coefficient of friction of nickel-plated surfaces is slightly lower. It is 0.40 for nickel surfaces and 0.50 for chrome surfaces.
②Appearance
Nickel’s appearance varies from matte to bright and from yellow to white. Chrome plating, on the other hand, looks bright bluish-white and is also highly reflective. That’s why it can achieve a mirror-like effect”. Next, nickel coatings come in various forms of finishes, from shiny polished nickel to brushed or satin nickel.
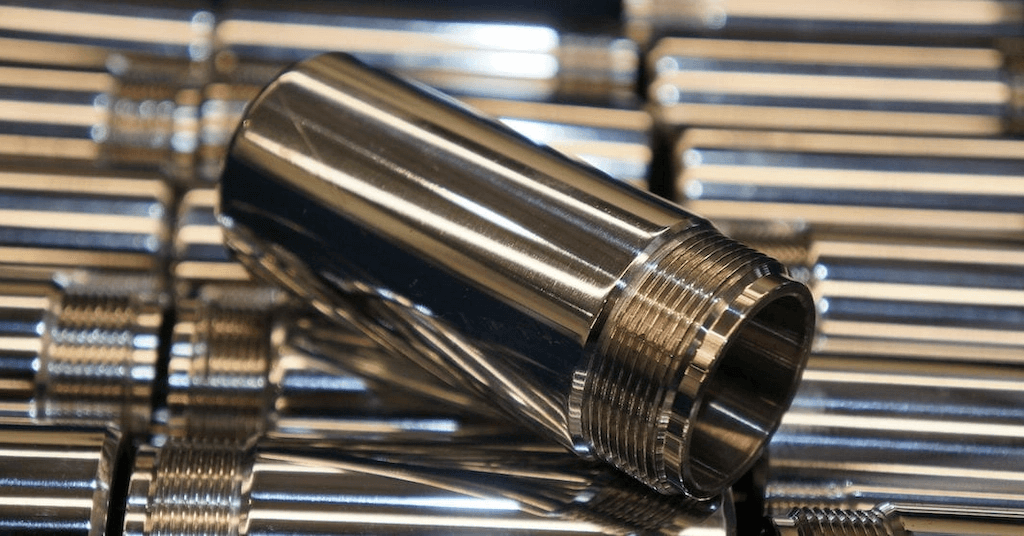
③Durability and Corrosion Resistance
Chrome plating is more scratch-resistant and holds up well against daily wear and tear. Its superior corrosion resistance makes it a great choice for fixtures that are exposed to wet environments. On the other hand, nickel-plated parts still offer reasonable durability. It resists rust and corrosion. For durability, chemical plating can be done at a lower price.
④Care and Maintenance of Finishes
Chrome finishes are relatively easy to clean and maintain due to their highly reflective finish. On the other hand, nickel (brushed or satin finishes) are more prone to spotting. However, both finishes can hide minor scratches and dents better.
⑤Cost Impact
The cost of both finishes can vary depending on the specific project and the quality of the finish. Generally speaking, nickel finishes tend to be slightly more expensive than chrome plating vs. nickel plating due to the cost of the raw materials. Zinc is another major electroplated metal.
4.What are nickel and chrome plating used for?
From automotive to medical and electronics, many industries rely on chrome and nickel plating to provide surface treatments for industrial parts. For example, nickel is used to plate electronic components such as connectors. Meanwhile, chrome provides aesthetics and protective properties to many items.