Material Selection
Custom aluminum parts are widely used in various industries due to their excellent properties, such as lightweight, high strength, and corrosion resistance. When it comes to manufacturing these parts, one of the key factors that determine their cost is the material selection. The choice of aluminum alloy plays a crucial role in determining the overall cost of custom aluminum parts.
There are a variety of aluminum alloys on the market, and each has its own unique properties and characteristics. The selection of the right alloy depends on the specific requirements of the part, including its intended application, required strength and the environmental conditions to which it will be exposed. At the same time, different alloys also have different associated costs, which can significantly affect the overall cost of custom aluminum parts.
When custom aluminum parts, the main factors affecting the cost of aluminum alloy
One of the main factors affecting the cost of aluminum alloys is their composition. Because aluminum alloys usually consist of aluminum as the base metal and various alloying elements such as copper, magnesium, zinc and silicon. The cost of these alloying elements can vary widely depending on their availability and market demand. For example, copper is generally more expensive than magnesium, which means that aluminum alloys with higher copper content cost more than alloys with higher magnesium content.
Another factor that affects the cost of aluminum alloys is their manufacturing process. Different alloys require different manufacturing techniques, such as casting, extrusion or forging. Each process has its own associated costs, including the cost of raw materials, equipment and labor. For example, casting aluminum alloys may require the use of molds and specialized equipment, which increases the overall cost of the part.
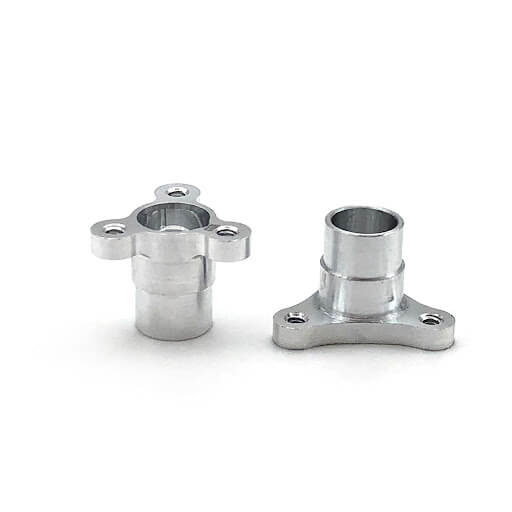
Furthermore, the level of customization required for the aluminum parts can also impact their cost. Custom aluminum parts often require additional processing steps, such as machining, surface finishing, or heat treatment, to achieve the desired specifications. These additional processes add to the overall cost of the parts, as they require additional time, labor, and resources.
In addition to material selection, other factors can also influence the cost of custom aluminum parts. These include the complexity of the part’s design, the quantity of parts required, and the lead time for production. Complex designs may require more intricate machining or tooling, which can increase the cost. Similarly, producing a large quantity of parts can lead to economies of scale, reducing the cost per part. Additionally, shorter lead times may require expedited production, which can result in higher costs.
In conclusion, the cost of custom aluminum parts is determined by various factors, with material selection being one of the most significant. The choice of aluminum alloy, its composition, manufacturing process, and level of customization all contribute to the overall cost. It is essential for manufacturers and customers to carefully consider these factors to ensure that the selected materials and processes align with the desired specifications and budget. By understanding the factors that determine the cost of custom aluminum parts, manufacturers can make informed decisions and optimize their production processes.