Overview of Optic Mounts: Principles, Manufacturing and Applications
Optic mounts are key components in optical systems for fixing, adjusting and supporting optical elements (such as lenses, mirrors, prisms, etc.). They play an important role in fields such as scientific research experiments, precision instruments, industrial testing and medical equipment.
As optical systems require high precision, the stability, adjustability and material properties of optic mounts have a direct impact on the performance of the whole system. In this paper, we will introduce the basic concept, structure type, manufacturing process and its application areas of optic mounts in detail.
1.Definition and role of optic mount
(1) Basic concept
Optic mounts are mechanical devices used to support and fix optical components. They can provide precise displacement, angle adjustment, and anti-vibration functions to ensure that the optical components are in ideal working condition.
In many high-precision optical systems, such as laser measurement equipment, microscopes and astronomical telescopes, the performance of the optical mount directly determines the overall accuracy of the system.
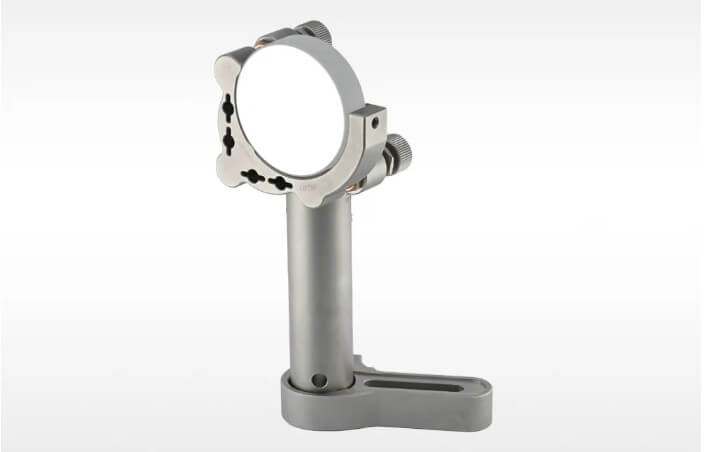
(2) The role of the optic mount
1) Fixed optical components:
Ensure that the lens, reflector and other components are in a stable position to prevent shaking or displacement.
2) Provide precision adjustment:
Some of the optic mounts are equipped with fine-tuning functions to adjust the angle, position and height to meet experimental or application requirements.
3) Reduce vibration effects:
High-precision experimental environments require optical systems that are insensitive to external vibration, and optic mounts can be designed with damping to reduce the impact of vibration.
4) Modular design:
Optic mounts often use standardized interfaces, can be used in combination to form a more complex optical system.
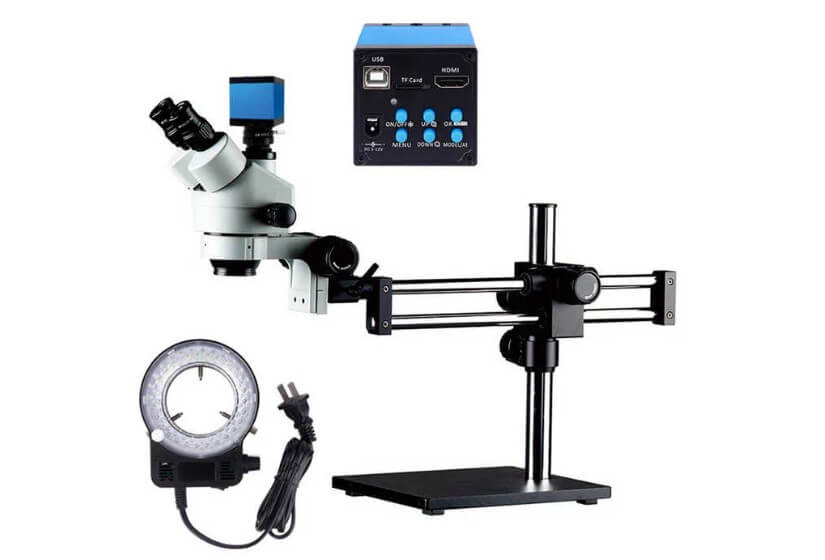
2.The basic structure and types of optic mounts
According to the needs of use, optic mounts can be divided into the following three categories:
(1) Fixed mounts
Fixed mounts are used to securely place optical components, usually without adjustment. These types of mounts are usually used in scenarios where no adjustment is required or where the frequency of adjustment is low, for example:
1) Lens holder: Used to fix a single lens or lens group.
2) Reflector bracket: Used to support a fixed reflector to keep it at a fixed angle.
3) Beam Splitter Bracket: Used to fix the beam splitter prism and other components.
(2) Adjustable Holder
Adjustable mounts allow the user to fine-tune the optical components to achieve precise optical alignment. These mounts usually have precision threads or mechanically displaced platforms, for example:
1) Tilt Adjustable Mounts: Allows the tilt angle of the optics to be adjusted for precision alignment.
2) Rotary mounts: allow 360 degree rotation for polarized optics systems.
3) XYZ moving platform: allows precision movement in the forward and backward, left and right, and up and down directions, commonly used in laser experiments.
(3) Combined Optical Stands
Combined optical bracket is a modular design of optical bracket, able to connect different types of bracket units, to build more complex optical systems. For example:
1) Multi-element combined mounts for interferometers.
2) Optical stages for laser alignment.
3) A movable precision measurement system.
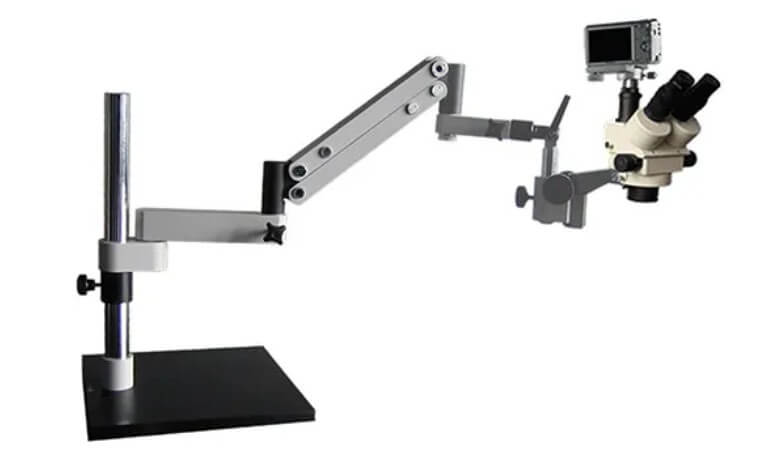
3.Manufacturing process of optic mounts
The manufacturing precision of optic mounts requires high precision, mainly involving material selection, processing technology and surface treatment and other aspects.
(1) Material selection
Optic mounts usually use the following materials:
1) aluminum alloy: lightweight and high rigidity, widely used in laboratory and industrial optical systems.
2) Stainless steel: corrosion resistance, suitable for high temperature and high humidity environment.
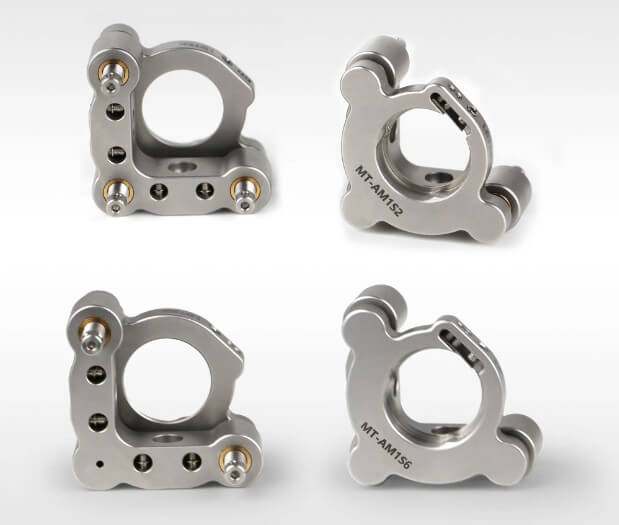
3) Carbon fiber: lightweight and highly rigid, suitable for aerospace optical systems.
4) Ceramic materials: with a very low coefficient of thermal expansion, suitable for high-precision measurement systems.
(2) Processing technology
1) CNC precision machining
The CNC machining process usually includes the following steps:
● Design and programming: Use CAD software to create a three-dimensional model of the optical mount, and use CAM software to generate an executable G-code for the CNC machine.
● Material Preparation: Select suitable metal materials, such as aluminum alloy or stainless steel, and make preliminary cuts to the material.
●Machine setup: install suitable cutting tools and adjust machining parameters, such as cutting speed and feed rate.
●Cutting: The machine tool carries out cutting, drilling, tapping and other operations according to the preset program to ensure that the parts meet the high precision requirements.
● Quality Inspection: Use measuring tools (e.g. micrometer, laser interferometer) to inspect the dimensional accuracy of the processed parts and make adjustments or corrections.
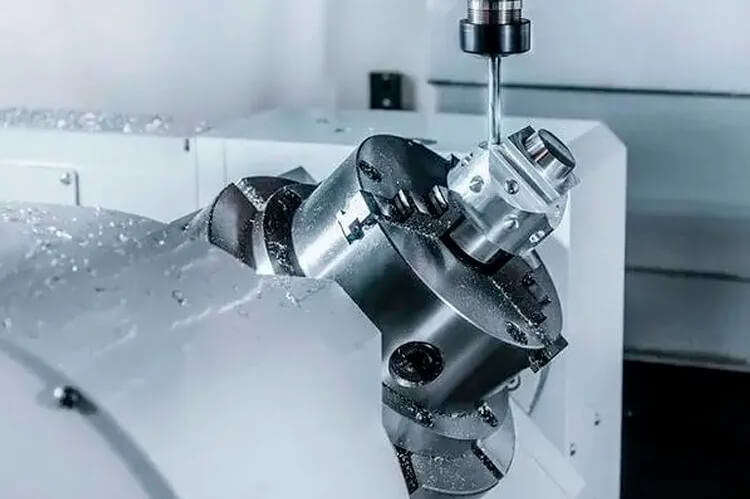
2) 3D Printing Technology
The 3D printing process generally includes the following steps:
● Model design: use CAD software to design a 3D model of the optical mount.
● Slicing: Use slicing software to layer the model and generate the print path.
● Material Selection: Select metal powder or other printing materials according to requirements.
●Printing process: Build up the material layer by layer, and use laser or nozzle for curing or sintering.
●Post-processing: Remove the support material and perform surface polishing, heat treatment, or plating.
(3) Surface treatment
Anodizing: Applied to aluminum alloy supports, it improves corrosion resistance and surface hardness.
Plating treatment: Stainless steel supports are nickel-plated or chromium-plated to enhance oxidation resistance.
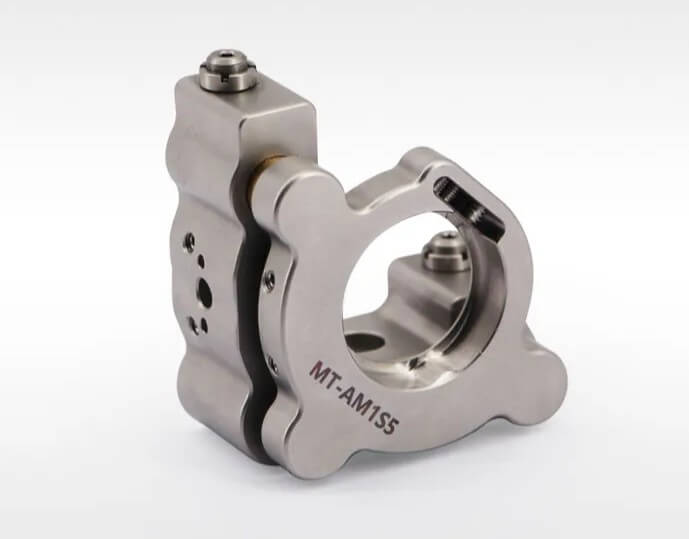
5.Application areas of optic mounts
Due to the high precision and stability of optic mounts, they are widely used in many fields.
(1) Scientific research experiment
In the field of scientific research, optic mounts are an important part of optical experimental equipment. For example:
1) Optical laboratory: used to build interferometers, spectrometers and other precision optical systems.
2) Laser system: used to fix lasers, mirrors and beam separators.
3) Physical optics experiments: for measuring the interference, diffraction and polarization properties of light.
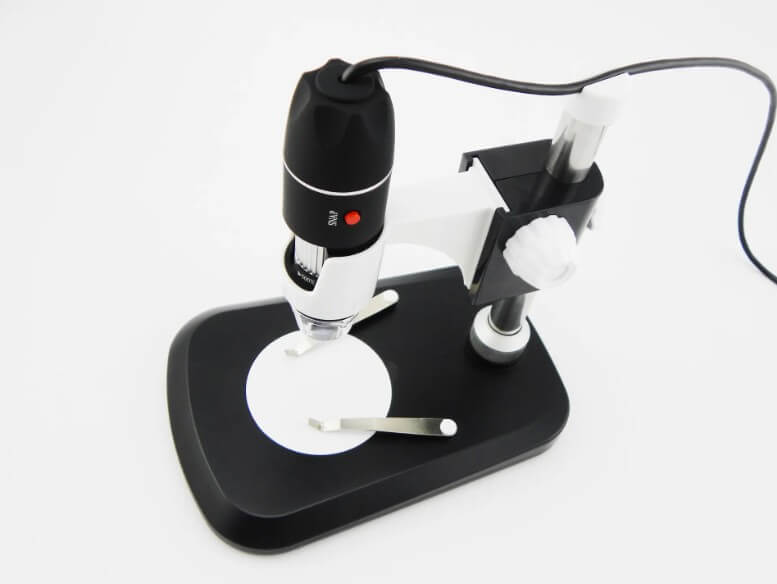
(2) Precision instruments
Optical supports play a vital role in precision instruments, such as:
1) Microscope: used to support and adjust the objective lens, eyepiece and illumination system.
2) Telescope: used to fix the optical components and ensure the stability of the optical path.
3) Spectrum analyzers: for adjusting and fixing optical components such as gratings and prisms.
(3) Industry and Manufacturing
In industrial production and manufacturing process, optic mounts are widely used in automated inspection equipment, such as:
1) Machine vision systems: used to support industrial cameras, lenses and lighting systems.
2) Laser processing equipment: to fix optical lenses and scanning mirrors to ensure the stability of the laser light path.
3) Automatic Optical Inspection (AOI) equipment: for precision inspection in electronics manufacturing.
4) Semiconductor manufacturing: used to support and adjust high-precision optical components in lithography, wafer inspection equipment and laser alignment systems.
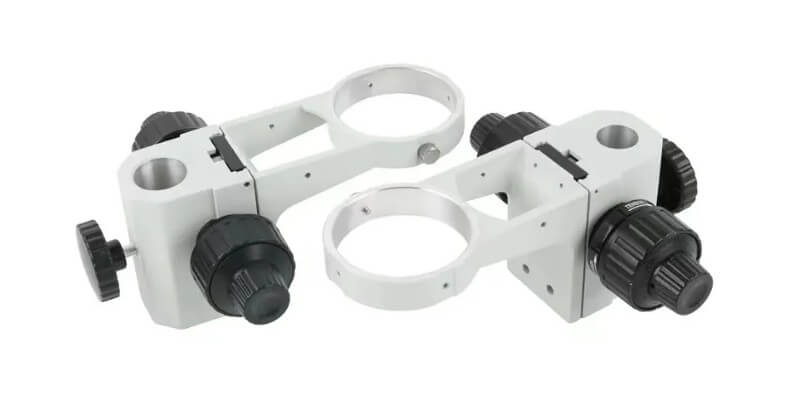
(4) Medical and Biological Imaging
In the field of medical and biological imaging, the ability to accurately position optical supports is particularly important, for example:
1) Optical microscopes: for high magnification observation of biological samples.
2) Surgical navigation systems: for supporting and adjusting medical imaging equipment.
3) Laser therapy equipment: to ensure stable focusing of the beam during the treatment process.
6.Summary
Optic mount is an indispensable key component in optical system, which plays an important role in scientific research, industry, medical and other fields. In the future, optic mounts will also develop in the direction of higher precision, higher stability, miniaturization, lightweight, intelligence and automation.