Understanding Dynamic Toolpaths for Optimized CNC Machining
CNC machining has revolutionized the manufacturing industry, making the production of complex parts precise and efficient. A key aspect of CNC machining is the toolpath, which determines the path the cutting tool follows as it moves through the material. Dynamic machining is one such newer machining strategy. It can handle even the most complex parts such as hotpoint washing machine parts diagram and sewing machine parts diagram.
Traditional toolpaths are static, meaning they are predetermined and do not change based on changes in the material or cutting conditions. However, dynamic toolpaths have changed the CNC machining landscape, increasing efficiency and improving surface finish on many parts such as hotpoint washing machine parts diagram and sewing machine parts diagram.
Dynamic tool paths, as the name suggests, are tool paths that adapt to changes in materials and cutting conditions in real time. This adaptability is achieved through the use of advanced algorithms and sensors that also monitor various parameters during machining. Finally, dynamic toolpaths optimize the cutting process by continuously adjusting the toolpath, thereby reducing machining time and improving part quality.
Key Benefits of Dynamic Toolpaths in CNC Machining
One of the main advantages of dynamic toolpaths is their ability to adapt to changes in material properties. Traditional tool paths are designed based on assumptions about the material being machined, such as its hardness and density. However, these assumptions may not always hold true, especially when using materials with varying properties. Dynamic toolpaths, on the other hand, can detect changes in material properties and adjust cutting parameters accordingly. This ensures that cutting tools are always operating under optimal conditions, minimizing tool wear and maximizing material removal rates.
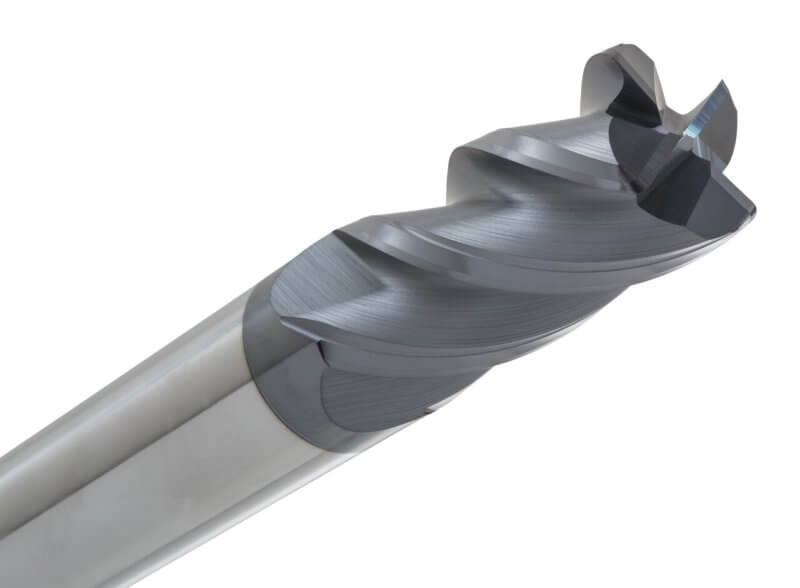
Another benefit of dynamic toolpaths is their ability to adapt to changes in cutting conditions. Traditional toolpaths are designed based on a set of predefined cutting parameters, such as cutting speed and feed rate. However, these parameters may not be optimal for all cutting conditions. For example, when machining a part with varying depths of cut, a static toolpath would use the same cutting parameters throughout the entire operation. This can result in inefficient cutting and poor surface finish. Dynamic toolpaths, on the other hand, can adjust the cutting parameters based on the actual cutting conditions, ensuring that the tool is always operating at the optimal parameters.
Dynamic toolpaths also improve surface finish compared to traditional toolpaths. Because traditional tool paths often produce visible tool marks on the machined surface, additional finishing operations are required. Dynamic toolpaths, on the other hand, can also minimize tool marks by continuously adjusting the toolpath to distribute cutting forces more evenly. This advantage not only results in a smoother surface finish, but also reduces the need for additional finishing operations, saving time and money.
In conclusion, dynamic toolpaths have revolutionized CNC machining by offering increased efficiency and improved part quality. By adapting in real-time to changes in material properties and cutting conditions, dynamic toolpaths optimize the cutting process, resulting in reduced machining time and improved surface finish. With the advancements in algorithms and sensors, dynamic toolpaths are becoming increasingly popular in the manufacturing industry. Manufacturers who adopt dynamic toolpaths can benefit from increased productivity, reduced costs, and improved customer satisfaction. As CNC machining continues to evolve, dynamic toolpaths will undoubtedly play a crucial role in shaping the future of manufacturing.