Application of photochemical etching in the manufacture of electric vehicle parts
As the world pays more attention to environmental protection, the electric vehicle (EV) industry is rapidly rising and becoming a pioneer in reducing carbon emissions. In this context, photochemical etching technology, with its unique advantages, has become a key process in the manufacture of precision metal parts for electric vehicles. This article will discuss in detail the importance and advantages of etching technology in the manufacture of electric vehicle parts and its far-reaching impact on the future development of the industry.
1.What is photochemical etching?
Photochemical etching, also known as precision chemical machining or chemical milling, is a subtractive manufacturing process that uses photosensitive materials and chemical solutions to create complex metal parts. This non-contact method can achieve precise, clean edges while avoiding material stress or deformation, making it ideal for producing high-precision metal parts.
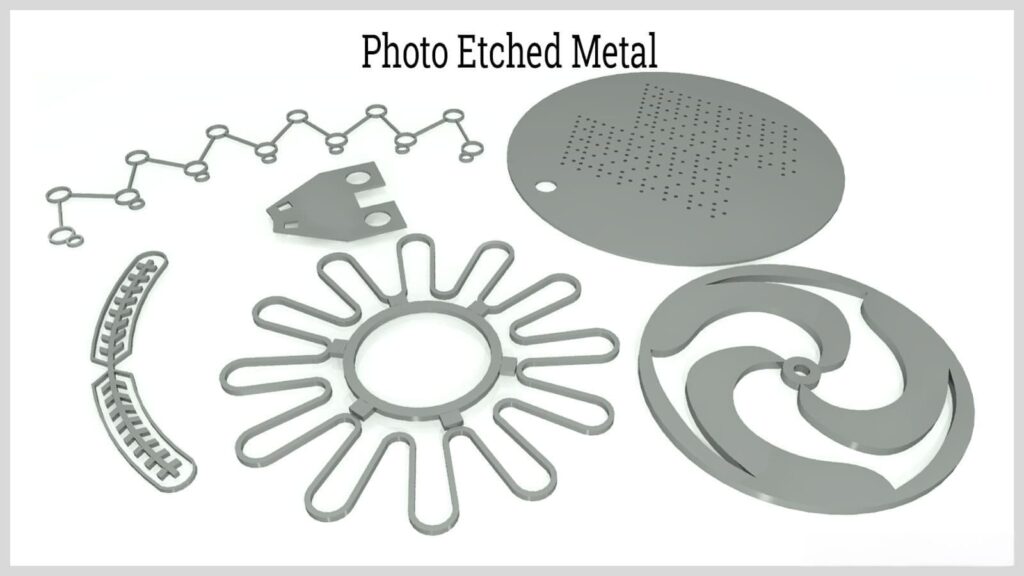
2.Advantages of photochemical etching
1)High precision and complexity
It is possible to produce complex designs with tight tolerances, which is difficult to achieve with traditional stamping or machining.
2)Integrity
As a non-contact process, photochemical etching avoids mechanical stress and deformation, maintaining the integrity of metal parts.
3)Cost-effective
Compared with traditional stamping or CNC machining tools, etching tools are low-cost, faster to produce, and less expensive.
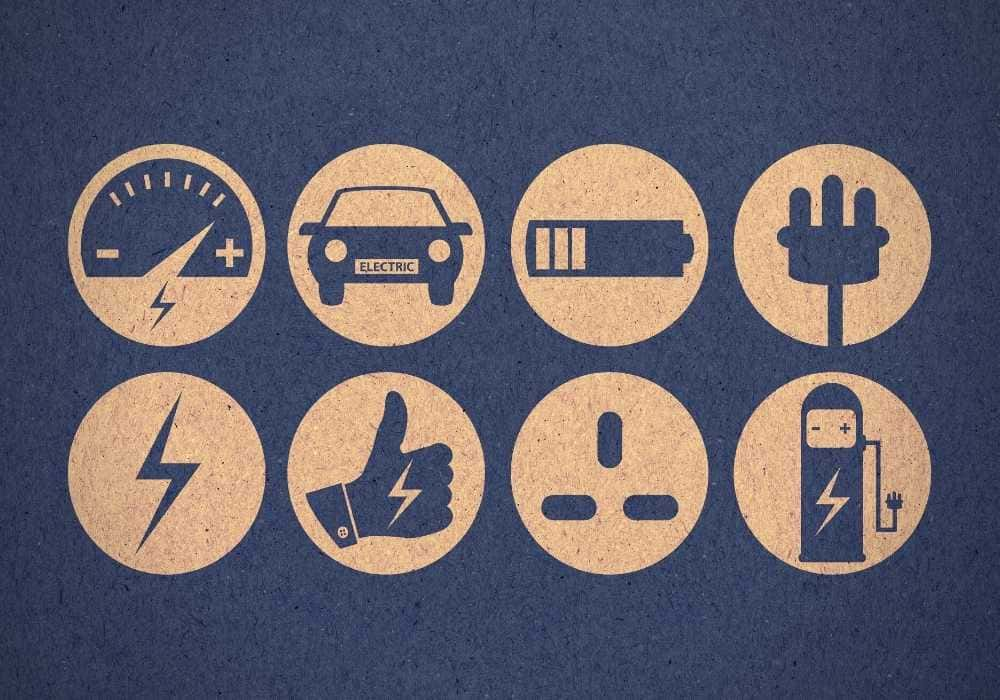
4)Flexibility of thin materials
Photochemical etching is particularly suitable for processing thin metal sheets, avoiding deformation or breakage.
5)Quick adjustment
The photomask of photochemical etching can be adjusted quickly, enabling rapid prototyping and shortening delivery time.
6)Material versatility
Applicable to a variety of metals, including stainless steel, aluminum, copper alloys and even titanium, to meet different material needs.
7)No heat-affected zone
Unlike laser cutting, photochemical etching does not generate heat that affects the properties of metals.
8)Low environmental impact
The process is efficient, has less waste, and is more environmentally friendly.
9)Scalability
Photochemical etching is easy to scale to large-scale production while maintaining consistency and precision.
3.Automotive parts produced by photochemical etching
1.Battery collectors
Thin, lightweight copper or aluminum plates responsible for conducting electricity within the battery.
2.Busbars
Conductive metal strips that distribute electricity throughout the electrical system, ensuring efficient energy flow.
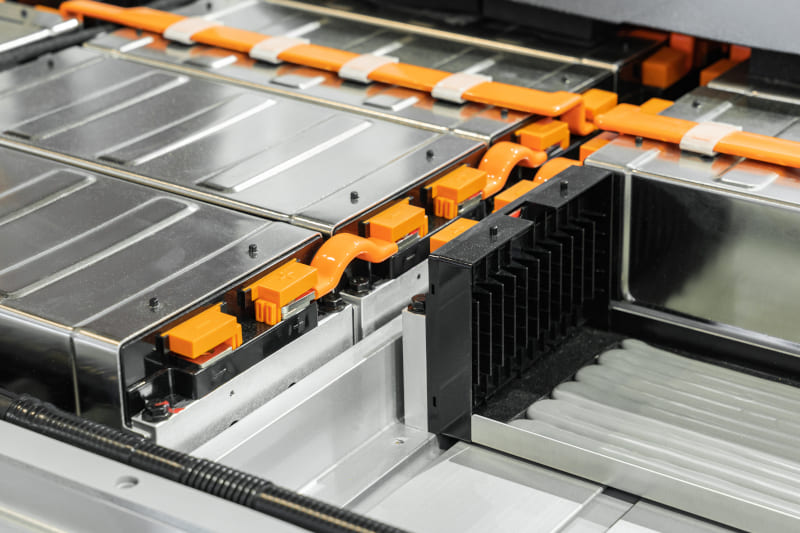
3.Heat shields
Protect sensitive components from the heat generated by the battery or motor.
4.Battery Management System (BMS)
Monitors and controls the performance, safety, and efficiency of the battery pack.
5.EMI/RFI shielding components
Prevents electromagnetic and radio frequency interference, essential for the proper operation of vehicle electronics.
6.Cooling plates
Manages battery system temperature to prevent overheating and ensure service life.
6.Sensor components
Small precision metal parts that detect temperature, pressure, and position of the vehicle.
7.Fuel cell boards
Efficient operation of fuel cells in hydrogen-powered electric vehicles is essential.
8.Connector pins and terminals
Essential for safe electrical connections throughout the electric vehicle.