The Importance of Color in Plastic Injection Molding
Color uniformity in plastic injection molding is more than just an aesthetic issue, it is an important component of product quality. In this article, we will uncover the complexity of different color systems used in injection molding and the importance of specifying hues with numbers. Whether you are a designer, manufacturer, or just curious about the world of plastic parts, these insights will provide you with the knowledge to ensure color consistency in your projects.
1.Color Systems in Plastic Injection Molding
In plastic injection molding (IM), the application of color is more than just appearance. It represents brand identity, function, and quality. There are a variety of color systems to help manufacturers achieve precise and consistent coloring.
- Pantone Matching System (PMS)
PMS is widely used in brand strategy and marketing to achieve precise color matching between various materials. - CIE Lab System
A color opposition space that quantifies color perception, allowing precise color communication and control. - RAL Color System
This is a European color standard used primarily in architecture, construction, and industry, known for its comprehensive and accurate color representation. - HSB (Hue, Saturation, Brightness)
A cylindrical coordinate system that represents color in the way humans perceive it. - RGB and CMYK
These systems are commonly used in digital printing and display and focus on red, green, blue, and combinations of cyan, magenta, yellow, and black.
2.Lab Color System in Plastic Injection Molding
The Lab color system, also known as CIE Lab, is the system with the highest accuracy in color representation. The system operates in three dimensions: L* for lightness, a* for green to red, and b* for blue to yellow.
By quantifying color perception, the Lab system creates a standardized color adversarial space, making it indispensable for industries that require accurate color matching. An important advantage of the Lab system is its device-independent nature, meaning that colors remain consistent across different devices or displays. Its mathematical basis ensures that any color within human vision can be described, which is a crucial aspect in plastic injection molding where color accuracy is critical. Various online tools, such as this fixed sensor, can be used to convert color values to the Lab system.
2.RAL Color Standard in Injection Molding
Derived from the German Ministry of Industrial Relations, the RAL color system is a recognized European color standard with more than 2,300 colors and is widely used in the architecture, construction, and injection molding industries. Unlike the Lab system, RAL focuses on categorizing colors into series such as classic, effect, and design. It is known for accurate color representation, especially in industrial applications.
3.Comparative Analysis: Lab vs. RAL
While both systems have their unique advantages, comparing them reveals clear differences:
- Versatility
Lab’s mathematical approach makes it more versatile, while RAL’s categorized series cater to specific industries - Accuracy
Lab offers equipment-independent accuracy, while RAL’s physical color representation may vary from device to device - Application
Lab is more widespread, while RAL is more favored in European industrial environments
The choice between Lab and RAL depends on the specific requirements of your plastic injection molding project. Understanding their intricacies will help select a system that ensures color uniformity and meets technical requirements and aesthetic preferences.
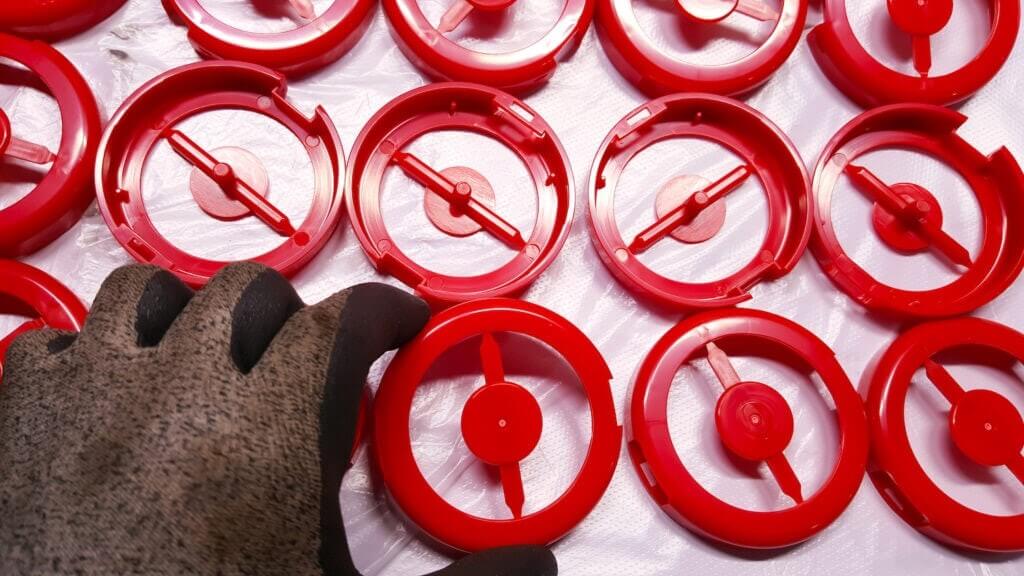
4.Achieving Color Uniformity in Plastic Injection Molding
1) Design Tips for Color Consistency
The design phase plays a vital role in maintaining color uniformity in plastic injection molding. Here’s how to do it:
- Material Considerations: Understanding the properties of the material is critical because different engineering plastics react differently to colorants
- Colorant Selection: Using high-quality colorants that match the polymer being used helps achieve consistent hues
- Simulation and Prototyping: Testing color through simulations and prototypes ensures that the final product matches the desired hue
- Consider Environmental Impacts: Different lighting conditions and environments can affect color appearance. Design with the end-use environment in mind
2) Uniform Color Selection Guidelines
Choosing the right materials and methods is critical for color uniformity in injection molding. Here are the guidelines:
- Understand the project requirements: Determine the exact color specifications and intended use of the part
- Choose the right color system: Choose between systems such as Lab or RAL based on project needs and industry standards
- Choose the right colorant: Work with a supplier that offers industry-certified colorants to ensure quality and consistency
- Consult a professional: Speak with an experienced engineer or color expert who can guide you to achieve the exact hue
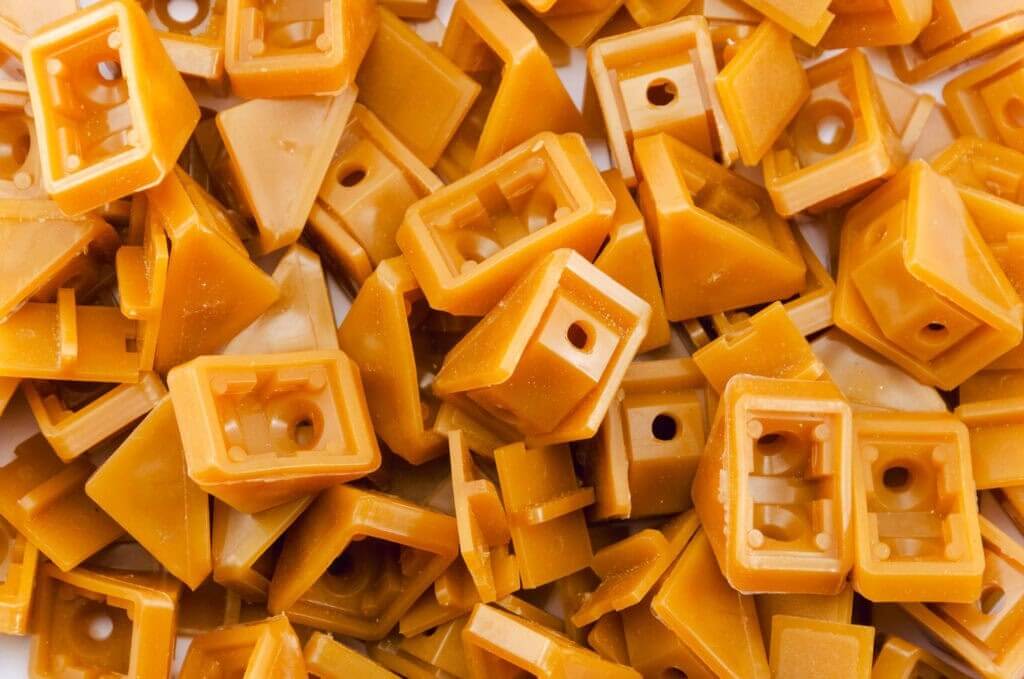
5.Sending a sample to the manufacturer: a must-do step
A practical and often overlooked solution to ensure color uniformity is to send a sample to the manufacturer. The sample is a 50 x 50 mm flat piece that can be either material cut from the target color or a part you want to match with a newly manufactured part. This practice of sending a sample to Xavier or the relevant manufacturer allows for an exact color match. It eliminates guesswork, reduces the risk of inconsistencies, and ensures that the final product is exactly what the customer expects.
6.Conclusion
In the multifaceted world of plastic injection molding, color uniformity is more than just a visual aspect; it symbolizes quality, brand image, and customer satisfaction. Achieving precise hues becomes an achievable goal through detailed understanding of color systems such as Lab and RAL, careful design planning, strategic selection, and sending samples to manufacturers.
These principles, rooted in technical expertise and collaboration, ensure that the final product resonates with the desired vision, paving the way for success in any plastic molding venture. Xavier offers a wide range of manufacturing capabilities, including plastic injection molding and other value-added services, to meet all your prototyping and production needs.