Detailed explanation of polished brass: the transformation from traditional to modern
Brass, an ancient and charming material, is widely used in decoration, artworks and industrial parts for its unique color and excellent mechanical properties. Polished brass is the key step to give brass products a brilliant shine and delicate touch. This article will explore in depth the various processes of polishing brass, from traditional to modern, and analyze its processes, techniques and precautions one by one.
1.The importance of polishing brass
Brass is an alloy composed of copper and zinc. Its surface is easily oxidized in the air, forming a dull oxide film that affects its appearance. Through polishing, not only can the oxide layer, scratches and impurities on the surface be removed, but the gloss and texture of brass can also be significantly improved, making it show a magnificent effect. In addition, polishing brass can also enhance the corrosion resistance of its material to a certain extent and extend its service life.
(1) Improve aesthetics
The surface of polished brass is as smooth as a mirror, which can reflect dazzling light and is highly decorative. It is widely used in home decoration, lamps, accessories and other fields.
(2) Enhanced durability
During the polishing process, the fine scratches and flaws on the brass surface are removed, forming a dense protective film that can effectively resist the erosion of external corrosive media and improve the durability of brass products.
(3) Meeting special needs
In some fields such as precision instruments and optical components, polished brass needs to achieve extremely high surface roughness to meet specific usage requirements.
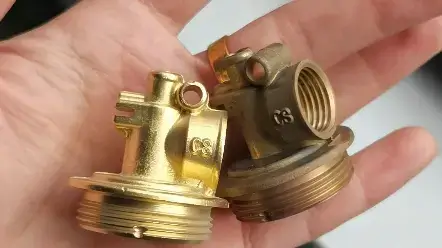
2.Traditional brass polishing process
The traditional brass polishing process mainly relies on manual operation, with simple tools, but it is time-consuming and labor-intensive, and has low efficiency. However, its unique craftsmanship and delicate feel are still favored by many people.
(1) Mechanical polishing
1) Tools:
Sandpaper, grinding wheel, polishing wheel, etc.
2) Process:
First, use coarse sandpaper or grinding wheel to remove obvious flaws and oxide layers on the brass surface, and then gradually replace with finer sandpaper for polishing until the surface is smooth. Finally, use a polishing wheel and polishing paste to polish the surface to make it shiny.
3) Precautions:
During mechanical polishing, pay attention to the control of force and speed to avoid excessive polishing that may cause the brass surface to heat up and deform or leave polishing marks.
(2) Chemical polishing
1) Principle:
Use chemical reagents to corrode the brass surface so that the microscopic concave and convex parts of the surface are evenly corroded, thus forming a smooth surface.
2) Process:
Soak the brass product in a specific chemical polishing liquid, take it out after a period of time, rinse it with clean water, and perform necessary post-treatment.
3) Precautions:
The formula and immersion time of the chemical polishing liquid need to be strictly controlled to avoid excessive corrosion that may damage the brass product. At the same time, the chemical polishing liquid has certain toxicity and corrosiveness, so protective measures need to be taken during operation.
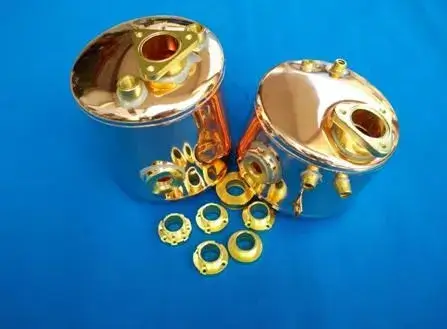
(3) Electrolytic polishing
1) Principle:
Use electrolysis to polish the brass surface. In the electrolyte, the brass product acts as an anode. After power is applied, an electrochemical reaction occurs on the surface, and the microscopic concave and convex parts are selectively dissolved, thus forming a smooth surface.
2) Process:
Put the brass product as the anode into the electrolyte and turn on the power for electrolytic polishing. During the electrolytic polishing process, it is necessary to control the current density, electrolyte temperature and time and other parameters to achieve the ideal brass polishing effect.
3) Precautions:
Electrolytic polishing requires professional equipment and operating skills. Pay attention to safety during operation to avoid dangers such as electric shock and electrolyte leakage.
3.Modern brass polishing process
With the development of science and technology, the modern brass polishing process has been significantly improved in efficiency and effect, and is more suitable for the needs of large-scale industrial production.
(1) Ultrasonic polishing
1) Principle:
Use ultrasonic vibration energy to polish the brass surface. In the polishing liquid, ultrasonic vibration will generate a large number of tiny bubbles. These bubbles will generate huge impact force when they burst, which can effectively remove dirt and oxide layer on the brass surface.
2) Process:
Put the brass product into an ultrasonic cleaning machine containing polishing liquid and turn on the ultrasonic wave for polishing. During the polishing process, it is necessary to control the ultrasonic frequency, power and time and other parameters to achieve the ideal polishing effect.
3) Advantages:
Ultrasonic polishing is efficient and effective, and is suitable for polishing complex shapes and small parts. At the same time, ultrasonic polishing causes less damage to the brass surface and can maintain the original shape and dimensional accuracy of brass products.
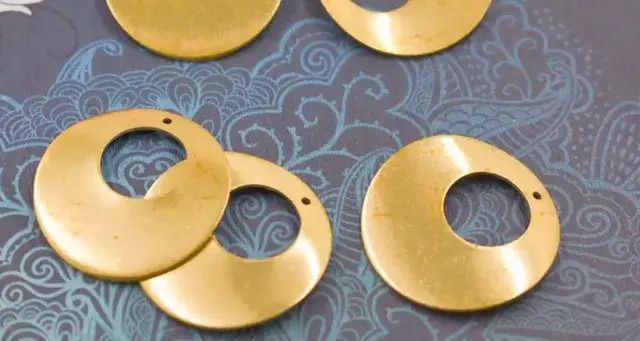
(2) Laser polishing
1) Principle:
The brass surface is scanned by a laser beam, and the microscopic concave and convex parts of the brass surface are quickly melted and re-solidified through the thermal effect of the laser to form a smooth surface.
2) Process:
The brass product is fixed on the workbench and the brass surface is scanned and polished by a laser. During the laser polishing process, parameters such as laser power, scanning speed and spot size need to be controlled to achieve the ideal polishing effect.
3) Advantages:
Laser polishing has high precision, good effect, and minimal damage to the brass surface. At the same time, laser polishing can be automated and controlled to improve production efficiency.
(3) Ion beam polishing
1) Principle:
Bombard the brass surface with an ion beam, and the microscopic concave and convex parts of the brass surface are selectively removed through the physical action of ions, thereby forming a smooth surface.
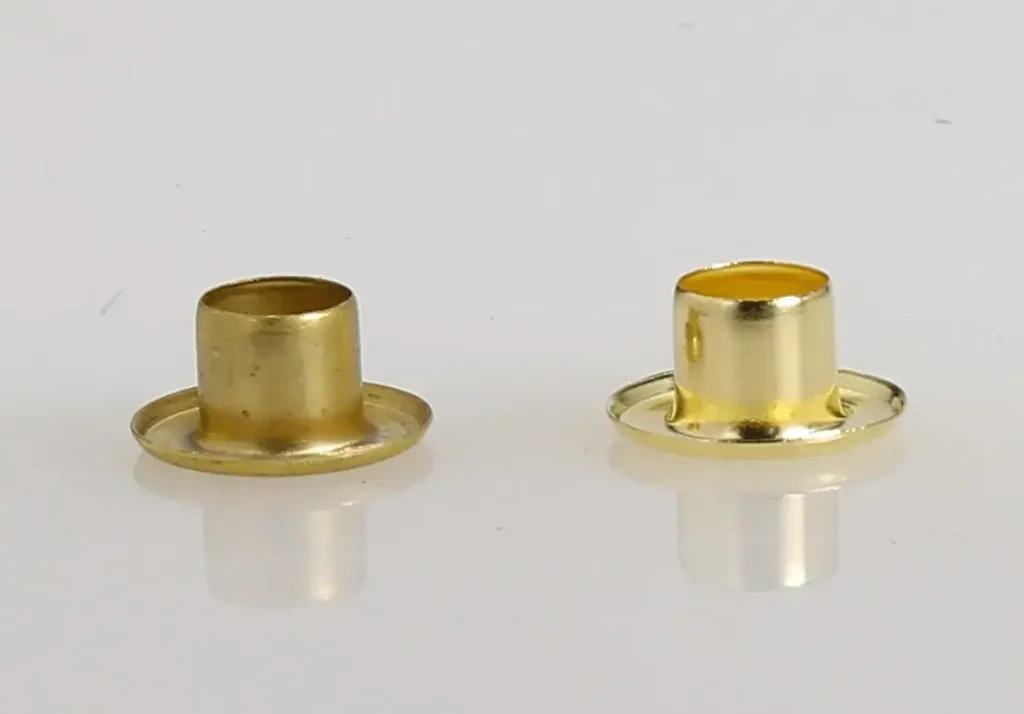
2) Process:
Put the brass product into the ion beam polishing equipment and turn on the ion beam for polishing. During the ion beam polishing process, it is necessary to control parameters such as ion beam energy, beam current density and time to achieve the ideal polishing effect.
3) Advantages:
Ion beam polishing has extremely high precision and excellent effect, and the damage to the brass surface is almost negligible. At the same time, ion beam polishing can achieve polishing of complex shapes and small parts.
4.Application cases of polished brass process
(1) Household appliances
In the field of household appliances, polished brass is often used to improve the appearance quality and market competitiveness of products. For example, polished brass decorative parts can be used in high-end refrigerators, washing machines and other household appliances, making the products look more upscale and beautiful.
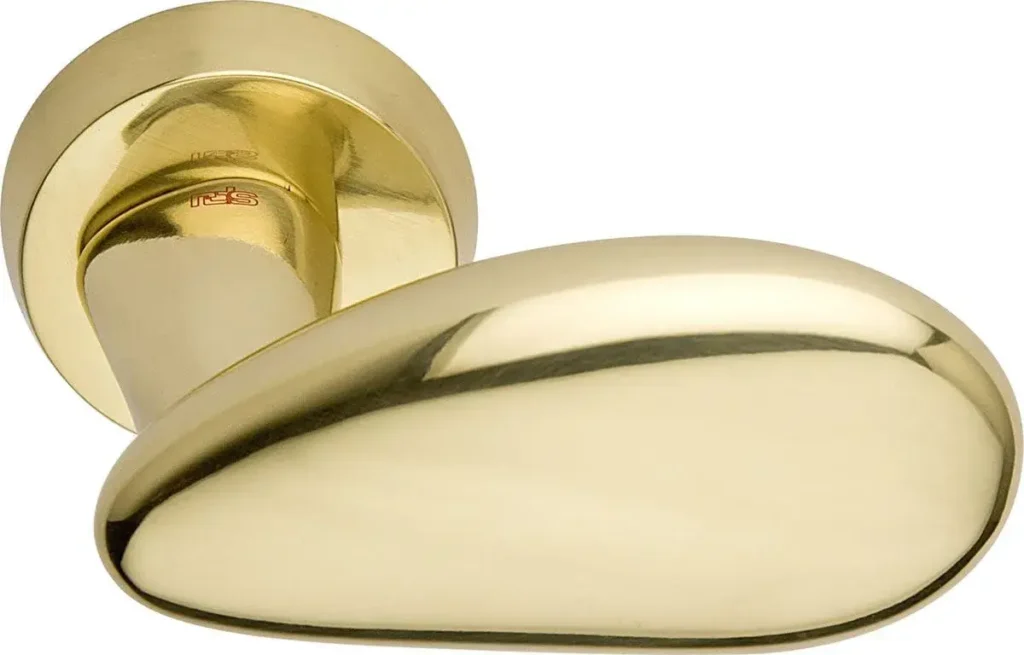
(2) Accessories and crafts
Polished brass plays an important role in the manufacture of accessories and crafts, and can significantly enhance the beauty and value of products. For example, polished brass pendants and jewelry show an elegant luster and are deeply loved by consumers.
(3) Musical instrument manufacturing
In the manufacture of musical instruments, the polished brass process is widely used in the production of brass instruments. Polishing not only makes the appearance of the instrument more beautiful, but also improves the sound quality and performance of the instrument. For example, the surface of the polished brass trumpet and trumpet is smooth and delicate, and the tone is purer and more pleasant.
5.Evaluation and post-processing of polished brass
(1) Effect evaluation standard
The evaluation of the effect of polished brass is usually based on the surface finish, gloss uniformity, and the presence of defects such as scratches and oxidation spots. The evaluation method can be visual inspection, tactile evaluation, and precise measurement using a surface roughness measuring instrument.
1) Visual inspection is to observe the gloss and uniformity of the brass surface with the naked eye to judge the polishing effect.
2) Tactile evaluation is to touch the brass surface with your hands to feel its smoothness and fineness.
3) The surface roughness measuring instrument can accurately measure the roughness value of the brass surface and provide a scientific basis for evaluation.

(2) Post-processing process
Polished brass needs to be cleaned and anti-oxidation treated to maintain its finish and extend its service life. Common post-processing processes include cleaning, drying, and coating with an anti-oxidation layer.
For example, the polished brass workpiece can be cleaned first to remove residual polishing agent and impurities on the surface, and then dried to prevent oxidation caused by residual moisture. Finally, an anti-oxidation layer such as varnish or wax can be applied to protect the brass surface from oxidation and corrosion.
6.Summary:
Polishing brass is an evolving technology. From traditional manual operations to modern high-tech means, each method has its unique advantages and scope of application. In practical applications, the appropriate polishing process can be selected according to the specific requirements and production conditions of brass products to achieve the best polishing effect.