The Importance of Precision Brass Components in Manufacturing Processes
The manufacturing industry relies heavily on precision brass components to ensure the smooth operation of various processes. These components play a crucial role in maintaining the quality and efficiency of manufacturing operations. In this article, we will explore the importance of precision brass components in manufacturing processes and provide a guide to choosing the best ones for your specific needs.
Important Benefits of Precision Brass Components in the Manufacturing Industry
Precision brass components are widely used in the manufacturing industry due to their excellent mechanical properties and corrosion resistance. Because brass is an alloy of copper and zinc, it has a unique combination of strength, durability, and ductility, making it an ideal material for a variety of applications. These components are often used in industries such as automotive, aerospace, electronics and piping, where even slight deviations can have irreparable consequences.
One of the key reasons why precision brass components are essential in manufacturing processes is their ability to provide accurate and reliable performance. These components are manufactured to very tight tolerances, ensuring that they fit perfectly into the intended application. Whether it is a valve, fitting, connector, or any other brass component, precision is of utmost importance to ensure proper functionality.
Another significant advantage of precision brass components is their resistance to corrosion. Brass has excellent resistance to both atmospheric and water corrosion, making it suitable for applications where exposure to moisture or harsh environments is expected. This corrosion resistance ensures the longevity and reliability of the components, reducing the need for frequent replacements and maintenance.
Furthermore, precision brass components offer excellent thermal conductivity. This property is particularly important in applications where heat transfer is required, such as heat exchangers or cooling systems. The high thermal conductivity of brass allows for efficient heat dissipation, ensuring optimal performance and preventing overheating.
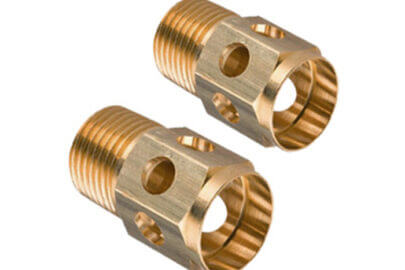
When it comes to choosing the best precision brass components for your manufacturing processes, several factors need to be considered. Firstly, it is essential to assess the specific requirements of your application. Consider factors such as the operating conditions, pressure, temperature, and compatibility with other materials. This evaluation will help you determine the appropriate brass alloy and component design for your needs.
Next, it is critical to choose a reputable supplier or manufacturer. Look for companies that have a proven track record of producing high-quality components. Consider their experience, certifications, and customer reviews. A reliable supplier will ensure that you receive precision brass parts that meet your specifications and quality standards.
Additionally, consider the cost-effectiveness of the precision brass components. While it is important to prioritize quality, it is also essential to find components that offer value for money. Compare prices from different suppliers and evaluate the overall cost of ownership, including factors such as durability, maintenance requirements, and potential downtime.
In conclusion, precision brass components play a vital role in manufacturing processes, offering accurate performance, corrosion resistance, and thermal conductivity. When choosing these components, it is crucial to assess your specific application requirements, select a reputable supplier, and consider the cost-effectiveness. By following this guide, you can ensure that you choose the best precision brass components for your manufacturing needs, ultimately enhancing the efficiency and reliability of your operations.