Precision CNC Machining:Astounding Tolerances
The role of precision CNC machining is to achieve this level of accuracy that cannot be achieved by standard machining methods. Automotive parts, medical implants, defense equipment parts, and many other applications require tight functional tolerances, often as low as ±0.001 inches. For those who are not familiar with the manufacturing industry, precision CNC machining is a manufacturing process that uses computer programs to manufacture any product to precise specifications.
In order to give you a comprehensive understanding of precision CNC machining, this article will provide a comprehensive introduction to the process, equipment, materials, advantages, and applications of precision CNC machining. If you are interested in learning more about precision CNC machining, please read to the end.
1.What is precision CNC machining?
Precision CNC machining involves shaping raw materials into finished products by cutting away excess parts specified by computer-aided design (CAD) or computer-aided manufacturing (CAM) blueprints. The automation of tool movement provides tighter tolerances than traditional machining methods, and precision machining typically involves tolerances of ±0.1 to 0.2 mm.
2.Common types of tolerances in precision CNC machining
(1) Standard tolerances
Machinists generally adhere to standard CNC tolerances for commonly manufactured parts. This includes specific accuracy for elements such as threads, pins, and pipes, and many milling services offer international standards of approximately +/-0.1mm. For a comprehensive understanding, refer to the detailed CNC machining chart.
(2) Bilateral tolerances
When bilateral tolerances are used, the deviation from a given dimension can be negative or positive, allowing the part to be slightly larger or smaller than specified. For example, +/- 0.06mm means that the machined part can be 0.06mm shorter or longer than the specified measurement. Such specifications usually apply to external dimensions.
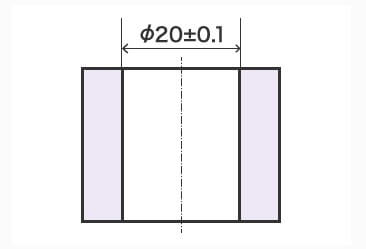
(3) Geometric dimensioning and tolerances
GD&T tolerances are more thorough than other machining tolerance systems. It highlights the measured value and the allowable deviation. It also outlines the specific geometric features of the machined part, such as its flatness, concentricity, and true position. GD&T tolerances are often used for parts with extremely precise dimensions.
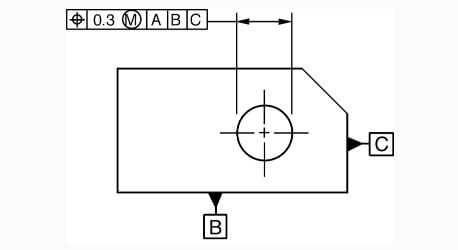
(4) Unilateral tolerance
Unilateral tolerance allows deviation in only one direction, either positive or negative. For example, a tolerance specified as +0.00/-0.06mm means that the finished part can be at most 0.06mm smaller than the specified measurement, but no larger. This tolerance is often used in designs where a part must be installed into another component, and it is critical to ensure that the part does not exceed the specified size.

(5) Limit tolerance
The limit tolerance is expressed as a range of values, and as long as the measurement falls within this range, the part is good. For example, 13 – 13.5mm is the limit tolerance for precision CNC machining, indicating that the size of the part must be between an upper and lower limit (13mm is the upper limit and 13.5mm is the lower limit).
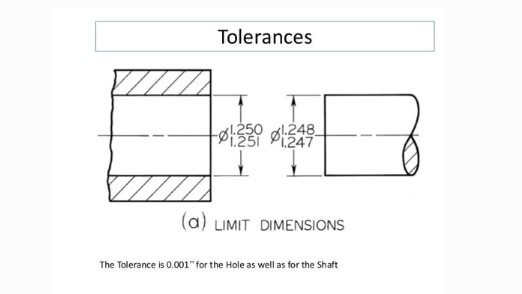
3.Precision CNC machining process guide
(1) Design and CAD modeling
CAD software is one of the most basic software in CNC machining, used to draw and design three-dimensional models or two-dimensional drawings of parts. After final requirements are determined, engineers or designers will create a detailed 3D engineering design that includes dimensions, tolerances, features, proportions, and other information. This provides a basis for subsequent processing and manufacturing.
(2) CAM and CNC programming
CAM software is another important software in CNC machining, which is used to convert CAD models into command codes (G codes) that machine tools can recognize and execute. CAM software generates cutting paths, tool paths, cutting parameters, and other information based on the geometric information of the part and the machining requirements. This process is also called CNC programming, and these codes can be read by CNC precision machines.
(3) CNC machine tool setup
Machine tool setup for precision CNC machining involves two main tasks: tool setup and workpiece clamping. First, the operator installs the tool in the chuck or tool holder and mounts the workpiece on the machine tool bed or chuck. At this stage, the correct tool selection (end mill, face mill, drill, etc.) and stable clamping of the workpiece and tool are critical to the final accuracy.
(4) Processing parts
The machine is connected to the control system to process operating instructions. This is the actual processing stage, where the operator can manually adjust parameters such as spindle speed, cutting speed, depth, feed speed, and set various processing instructions and process parameters. At the same time, fine-tuning parameters through testing can help produce precision CNC machined parts that meet precision requirements.
(5) Post-processing and finishing
This is the last and most important step in precision CNC machining. The post-processing process includes cleaning, deburring, polishing, surface treatment, etc., each of which directly affects the final quality and service life of the parts.
The selection of post-processing methods should be based on different metal materials, part shapes, and usage requirements. For example, for aluminum alloy parts, anodizing, sandblasting, spraying, etc. can be used for surface treatment to enhance their corrosion resistance and aesthetics; for stainless steel parts, electroplating, polishing, etc. can be selected to improve their surface finish and hardness. Different combinations of post-processing methods can achieve different effects and meet customers’ different requirements for part quality.
4.Types of precision CNC machining equipment
Due to the different processes involved in precision CNC machining, different equipment is required to make it work.
(1) CNC milling machines
Milling is a precise machining process that involves the use of a rotating tool to remove excess material from a workpiece. It involves several types of mills. Examples of such milling cutters include end mills, chamfer mills, and spiral mills. CNC-enabled milling machines also include manual milling machines, flat milling machines, universal milling machines, and universal milling machines.
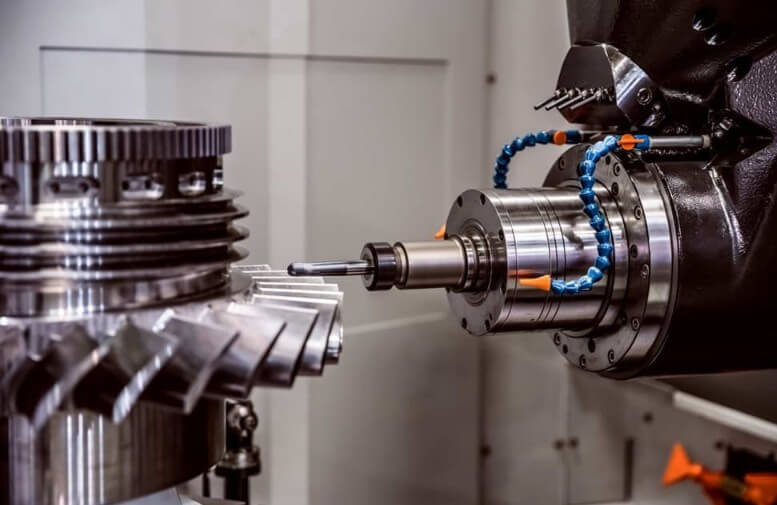
(2) CNC lathes
Turning is a precision CNC machining process that involves rotating a workpiece next to a rotating single-point cutting tool. The most popular tools used for turning are lathes such as turret lathes, engine lathes, and engine-specific lathes. Other turning equipment includes straight turning, taper turning, external grooving, threading, etc.
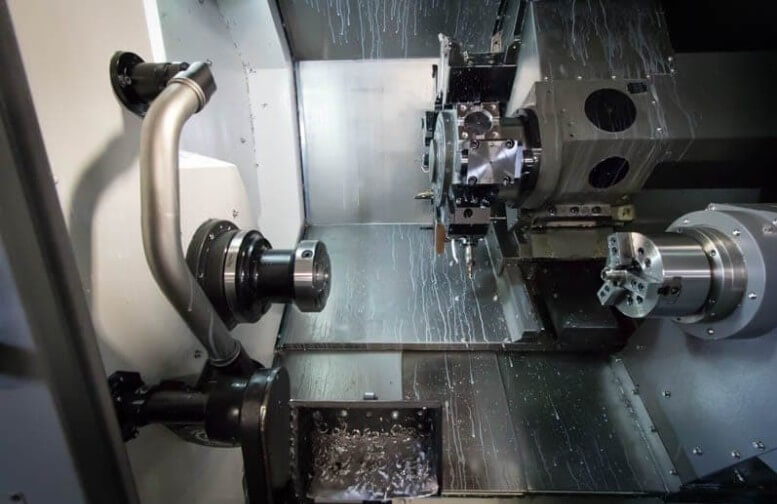
(3) CNC drilling equipment
Drilling is a precision CNC machining process that uses a rotating multi-point drill to form a cylindrical hole in the raw material/workpiece. In addition, the drill is designed to keep the chips off the workpiece, keeping the drilled hole clean.
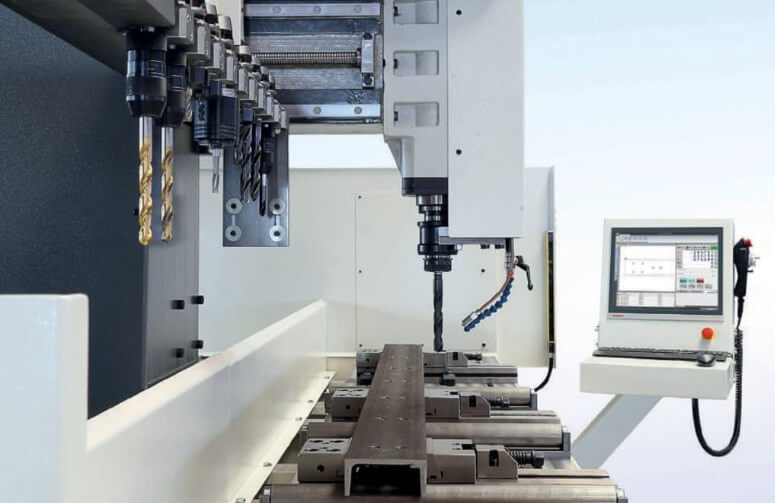
(4) CNC Discharge Mining Equipment
Discharge mining is a precision machining process that uses electrical discharge (sparks) to obtain a finished product.
The device consists of a tool electrode (tool) and a workpiece electrode (workpiece) separated by a dielectric fluid and subjected to a voltage. The process is also called spark machining, spark erosion, burning, die sinking or wire erosion.
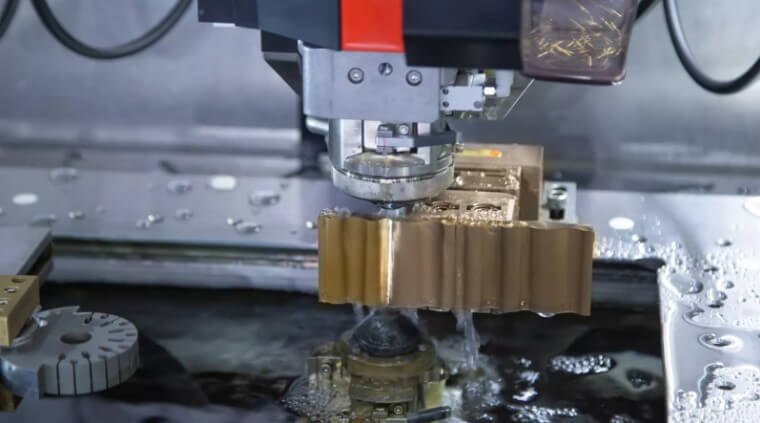
5.Main Applications and Industries of Precision CNC Machining Parts
Due to its versatility, cost and time-efficient process, precision CNC machining has gradually taken a dominant position in the manufacturing industry. Precision machining processes are used in the following industries:
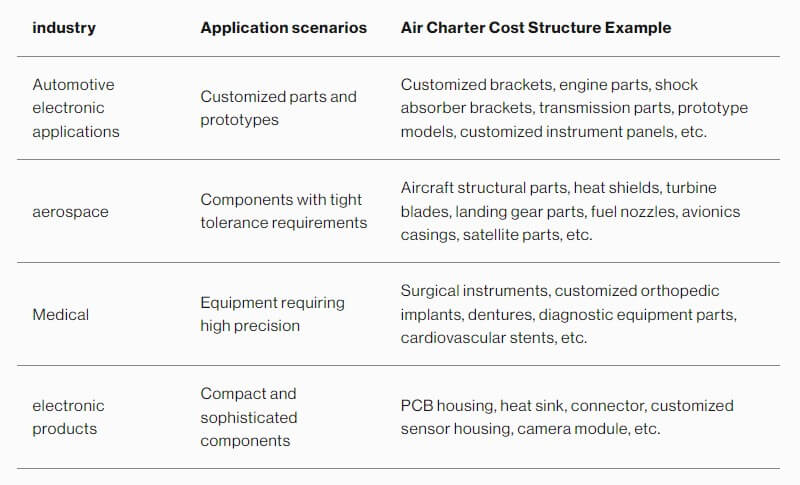
6.Conclusion
Precision CNC machining can be said to be the most effective way to manufacture customized parts. In addition to saving you money, it takes little time and allows little room for error.
If you are looking for an experienced Precision CNC Machining Manufacturer, Xavier is undoubtedly your ideal choice. If you are looking for an experienced precision CNC machining manufacturer, Xavier is undoubtedly your ideal choice. The Xavier team is well equipped to customize products online, and we will provide you with excellent tolerances and high-quality CNC machining solutions. For more information or to discuss your machining needs with us, please feel free to contact us.