Introduction to the Classification of Precision CNC Machining Methods
CNC machining is a general term used for a variety of machining applications. There are 5 different types of CNC equipment that perform 5 common CNC precision machining operations. These include milling, turning, laser machining, EDM and plasma cutters. D & N Machining Co can provide a variety of precision CNC machining services to the global aerospace, oil and gas and many other industries.
“CNC” stands for computer numerical control and refers to the programmable capabilities of a machine that enables it to perform many functions with minimal manual control.
CNC machining is the use of CNC controlled machines to make parts. The term describes a range of subtractive manufacturing processes that remove material from a bar or blank to produce a finished part.
CNC precision machining is widely used in industries such as medical, aerospace, industrial, oil and gas, hydraulics, etc. CNC machining can process a wide range of materials, including metals, plastics, glass, composites, and wood. And precision CNC machining has many advantages over machining without CNC programmability, which can significantly reduce machining cycle time, improve surface smoothness, and enhance quality and consistency.
Here are the 5 most common types of precision CNC machining:
1.CNC Machining:CNC turning
The characteristic of CNC lathes is the ability to rotate (turn) the material during the machining process. A lathe’s cutting tool is fed in a linear motion along a rotating bar; this removes material around the circumference until the desired diameter and features are achieved.
A subset of CNC lathes are CNC Swiss lathes (also known as automatic lathes). With a CNC Swiss lathe, the bar stock is rotated and axially slid into the automatic lathe via a guide bushing, which then automatically machines the cut part; generally speaking, CNC automatic lathes are good for machining small diameter parts.
Precision CNC turning can create internal and external features on a part: this includes drilling, broaching, reaming, slotting, tapping, and threading. CNC lathes and turning centers can manufacture parts including screws, bolts, shafts, fittings, and more.
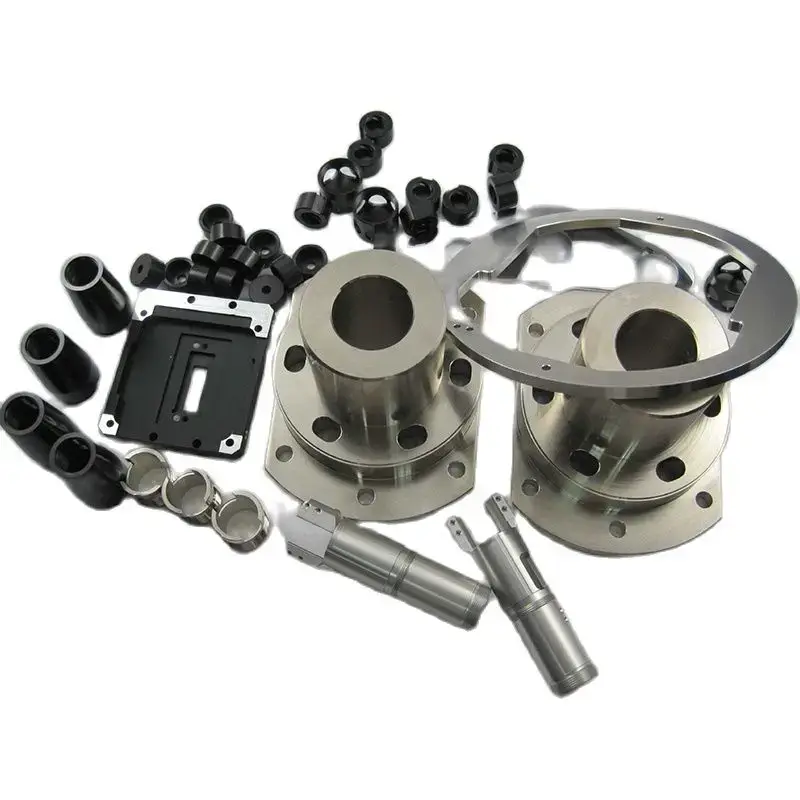
2.CNC Milling
CNC milling machines are characterized by their ability to rotate the cutting tool while holding the workpiece/block of material stationary. They can machine a variety of shapes, including face milling (shallow planes and cavities in the workpiece) and perimeter milling (deep cavities such as slots and threads). Parts suitable for production on CNC milling machines are typically square or rectangular with a variety of features.
3.CNC Laser Processing
CNC lasers have a pointed milling cutter that produces a highly focused laser beam that is used to precisely cut, slice, or engrave materials. The laser heats the material and melts or vaporizes it, creating a cut in the material. Typically, the material is in sheet form. The laser beam moves back and forth across the material to create the precise cut.
The process allows for a wider range of design freedoms than conventional cutting machines (lathes, turning centers, milling machines), and often produces cuts and/or edges that do not require additional finishing processes.
CNC laser engravers are often used to mark (and decorate) machined components. For example, logos and company names are difficult to machine using CNC turning or CNC milling processes. However, they are very easy to engrave using CNC laser engraving, and can be added to components even after the machining operation is complete.
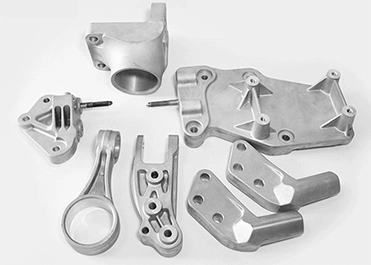
4.CNC Electrical Discharge Machining (EDM)
CNC Electrical Discharge Machining (EDM) uses highly controlled electrical sparks to machine materials into the desired shape. It may also be called spark etching, spark machining, or wire cutting. The part is placed under the electrode wire and the machine is programmed to discharge the electrode wire, generating high temperatures (up to 11,700 °C). The material is melted or washed away by the liquid to form the desired shape or feature.
EDM is most commonly used to create precise micro holes, slots, tapered or angled features, and a variety of other more complex features in a part or workpiece. It is often used to machine parts with difficult shapes and sizes, and is often used to machine very hard metals. For example, gears.
5.CNC Plasma Cutting Machines
CNC plasma cutting machines are also used to cut materials. However, they use a high-powered plasma (electron ionized gas) torch that is controlled by a computer to do this. The plasma torch functions similarly to a handheld pneumatic torch used for welding (up to 5500 °C), reaching temperatures up to 27,500 °C. The plasma torch melts the workpiece, creating the cut in the material. Whenever CNC plasma cutting is used, the material being cut must be conductive. Typical materials are conductive metals such as steel, stainless steel, aluminum, brass, and copper.
Precision machining offers a wide range of capabilities for part manufacturing and CNC finishing. Depending on the use environment, required materials, lead time, quantity, budget and required functionality, there is usually an optimal method that will provide the desired results.