Benefits of Precision Manufacturing
Precision manufacturing is one of the biggest advancements in the manufacturing industry in recent years. Machining companies near me are all about making progress.
Unlike other trends in the industry, precision manufacturing has the potential to revolutionize the way a range of industries operate, reducing costs, increasing efficiency, tightening tolerances, and providing a more reliable way to produce parts.
Precision manufacturing techniques have already impacted a wide range of industries, including automotive, aerospace, and medicine, and as more companies see the opportunity to use precision manufacturing techniques, precision manufacturing may become even more prominent than it is now.
But why is precision manufacturing so effective? How can it help you make better products? To answer these questions and better understand how to use the technology, let’s take a look at some of the biggest advantages it can offer when creating products.
1.Impeccable Precision
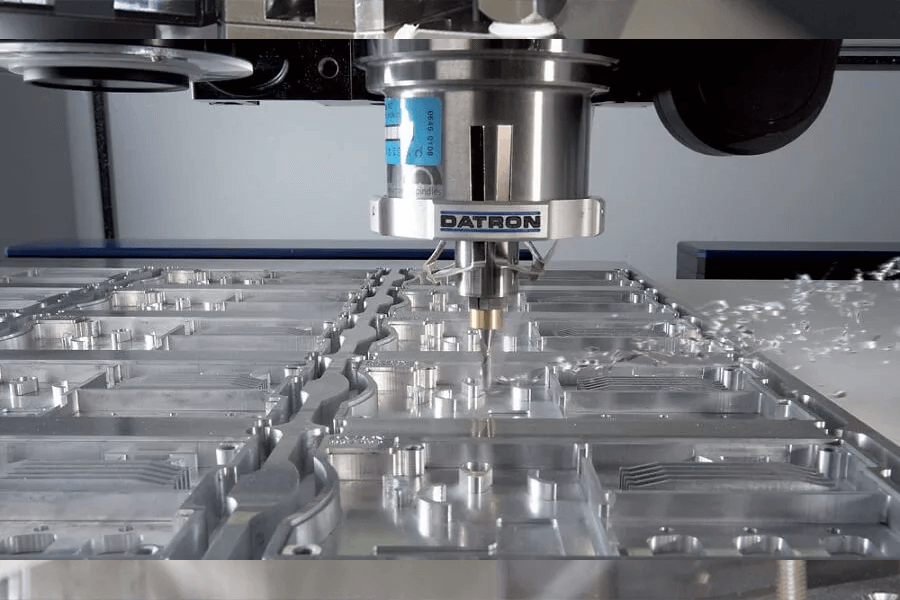
As the name suggests, precision manufacturing techniques can produce parts and products with precision that is difficult to match with most other methods. The entire industry has leapt forward as a result, as precision manufacturing allows companies to produce parts with very tight tolerances in areas where even the slightest deviation is not allowed. Even if the product industry you work in doesn’t require absolute precision, there is still a need for a reliable and affordable production method that can provide you with an identical copy of your design every time.
The technology also has excellent automation options, further increasing the precision and accuracy of the method by utilizing precision machining techniques to reduce the need for labor and minimize the possibility of human error.
In fact, it’s not impossible to CNC machine large parts, as savvy engineers can use the technology to produce larger products, further expanding the technology’s capabilities and applications.
2.Fast Turnaround
Thanks to the advanced software capabilities of modern precision manufacturing, turnaround times have been greatly reduced, as the combination of software and machining solutions makes the process from design to finished product much simpler and more manageable. Using advanced design and manufacturing tools can greatly reduce manual work. This means that design processes that used to take months to complete can now be completed in months or even weeks, completely changing the way companies produce and plan product release schedules.
Automated Processes Use CNC machining technology to perform repetitive tasks with perfect precision every time, producing parts with tight tolerances and ensuring that components remain consistent even when running larger batches. Once everything is set up, you can use precision manufacturing to quickly produce large quantities of products, as the machines require little supervision and can work automatically, repeating the same model around the clock.
3.Reduced Costs
Producing parts with tight tolerances is a costly process. This is especially true in certain demanding industries that require impeccable precision in every part produced. However, with advances in precision manufacturing, even tight tolerances have become more affordable, allowing companies to achieve better results for the same or even lower prices than they did ten or twenty years ago. Using CNC machining technology offers a range of advantages that can reduce costs at all stages of the development process.
Advanced software makes it easier to design parts and ensure their structural integrity, not only because of advances in the technology itself, but also because prototypes can now be quickly produced that can be tested and adjusted based on research findings. In addition, precision manufacturing requires less labor, which means fewer people involved in the project and many repetitive tasks can be automated on a large scale. This also allows precision manufacturing companies to offer more competitive prices and provide customers with greater flexibility, further increasing the popularity of this type of manufacturing.
Due to the same automation, the potential for human error is also reduced, which means fewer costly mistakes, thus avoiding additional expenses that inflate budgets.
Finally, the way CNC machining technology itself works can produce minimal waste. As a result, material requirements are reduced, passing on savings to customers and the opportunity to use a wider variety of expensive materials in the production process.
4.Easier Testing and Prototyping

Testing is an integral part of any successful product launch process. No matter how well-designed the initial design may be, in most cases at least some changes and adjustments will be required to ensure consistent performance and necessary durability.
Unfortunately, this can be cumbersome for some production methods, as prototype production takes a long time, the types of materials that can be used are limited, and the cost is too high to be practical.
Fortunately, these issues do not arise with precision manufacturing technology. It provides flexible product development opportunities, allowing companies to explore various markets and options for their products, quickly produce prototypes using a variety of materials, and allow for testing of their performance without any restrictions.
Rapid prototyping capabilities are one of the biggest selling points of CNC machining technology, as it not only provides greater flexibility with low tooling costs, but also significantly reduces waiting time. Prototypes are not just concepts, but can be produced into fully functional products using the necessary materials, including metal prototypes. Therefore, if testing proves that it is a viable product, full production can begin almost immediately, saving the company time and allowing it to take advantage of favorable conditions as soon as possible.
As you can imagine, having a fully functional prototype that can be used immediately can make a more convincing pitch to investors or stakeholders, making it much easier to sell the product than if you just had a placeholder concept.
5.Wide Range of Materials
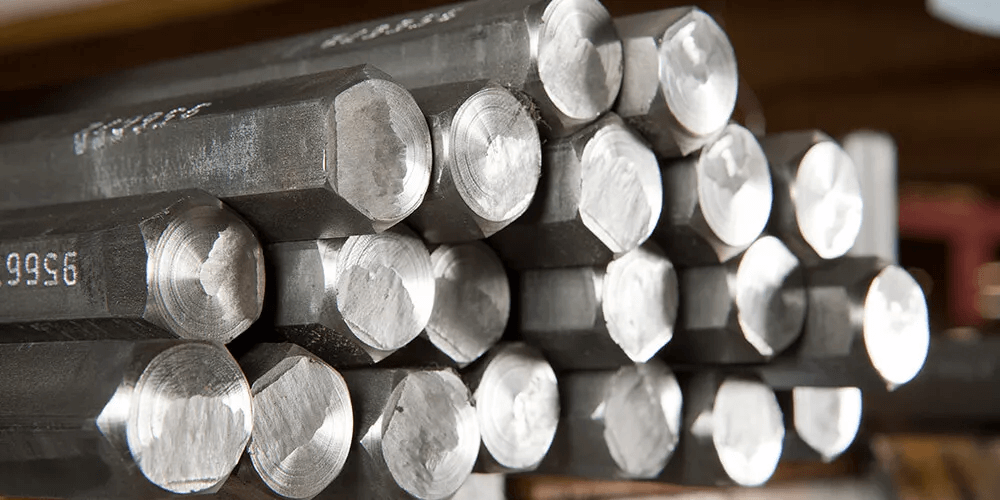
Precision manufacturing is used to produce both standalone parts and various components of machinery or products, so it’s no surprise that a wide range of materials are required depending on practical considerations such as industry, product requirements and budget. Fortunately, the technology is flexible enough to produce parts in a wide range of materials, which is why it is used in both high-tech industries and consumer-level product development.
Basic and engineered plastics are also useful because they are easy to modify and affordable, which is why it is widely used not only in consumer-grade parts production, but also in more high-tech fields such as medical devices or aerospace. With engineered plastics, you can get the same qualities as steel and other more expensive materials at a lower cost, which makes it an increasingly popular choice across industries.
Other materials that are popular when using precision manufacturing techniques include copper, brass, and steel, to name a few. Different variations of the above elements are not uncommon, though.
On top of that, with precision manufacturing, experienced service providers can take on nearly any project and make it a reality while meeting tight tolerances, managing customer budgets, and ensuring production deadlines are met.